The ELGi HLD Modular Desiccant Dryer is an energy-efficient dryer suitable for all applications that require a Class 2 air such as painting, powder coating, pharmaceutical, dental laboratory, glass, semiconductor, and food industry. The HLD series dryers are globally certified for CE and CRN standards.
Eliminate Moisture and Achieve Class 2 Quality of Air
The heatless twin tower design of the HLD desiccant dryer series operates by removing moisture from the air supply through absorption into a granular bed of desiccant. As compressed air flows through the packed desiccant bed of the first tower, the water vapor is absorbed; Meanwhile, tower 2 is rapidly depressurized and dry purge air from tower 1 is outlet through a purge valve, expanded to near atmospheric pressure, and counter-flowed down through tower 2 to induce desiccant bed regeneration. When desiccant in tower 1 becomes saturated, the air supply is switched back to tower 2 and the cycle continues.
Energy Saving Purge Optimizer
In practical situations, the airflow through the dryer is not maintained at the maximum flow value that the equipment is designed for. The moisture load may also vary. During these times, less purge-air may be required to remove the moisture from the desiccant in a tower. HLD dryers feature a purge economizing feature that can reduce the amount of purge air used by changing the regeneration.
Reduction of the percentage of air purge regeneration flow is based on a controller setting. It has 4 options - 40%, 60%, 80% & 100% purge optimization cycles respectively. The settings correspond to flow or moisture load through the dryer. There are separate LED indicators for Tower Status, Purge Optimizer & Condensate Drain
Dew Point Stretch Cycle (Optional Feature)
HLD dryers can be optionally operated under external dewpoint control. In this optional system, a dewpoint meter is installed at the outlet of the system. This feature stretches the moisture loading time of the desiccant bed by increasing the drying time. A dew point meter at the outlet with a required dew point setting provides the signal for the stretch cycle. This reduces the purge air in accordance to the air flow and dew point chosen. The purge occurs for the preprogrammed time during this time
High Performance Filters
ELGi HLD series compressed air dryers are equipped with high performance filters which are shipped in the dryer packing box. The filters are certified for regulations and performance and remove the wet particles down to 0.01 micron and oil aerosols down to 0.01 mg/m3.
Mixed Bed Desiccants
ELGi HLD modular desiccant compressed air dryer works with a mixed bed of desiccants - Activated Alumina and Molecular Sieves in 7:3 ratio, packed, bagged, separately and loaded in the towers. This combination is meticulously engineered to deliver high performance adsorption.
Air coming from any compressor is 100% saturated for that pressure and temperature combination. When air travels downstream, the temperature drops which results in the formation of condensation. This condensate water is detrimental to downstream equipment, and it may affect downstream critical processes or even cause corrosion. To avoid this compressed air dryers are used. There are different types of air dryers available based on the application. The most popular option is refrigerated air dryers. However, for applications that demand ultra dry compressed air - desiccant dryers needs to be used.
ELGi HLD modular desiccant compressed air dryers remove moisture and water vapor to as low as -40°F PDP to cater to the demanding applications downstream and ensure quality compressed air, meeting class 2 quality.
HLD Series
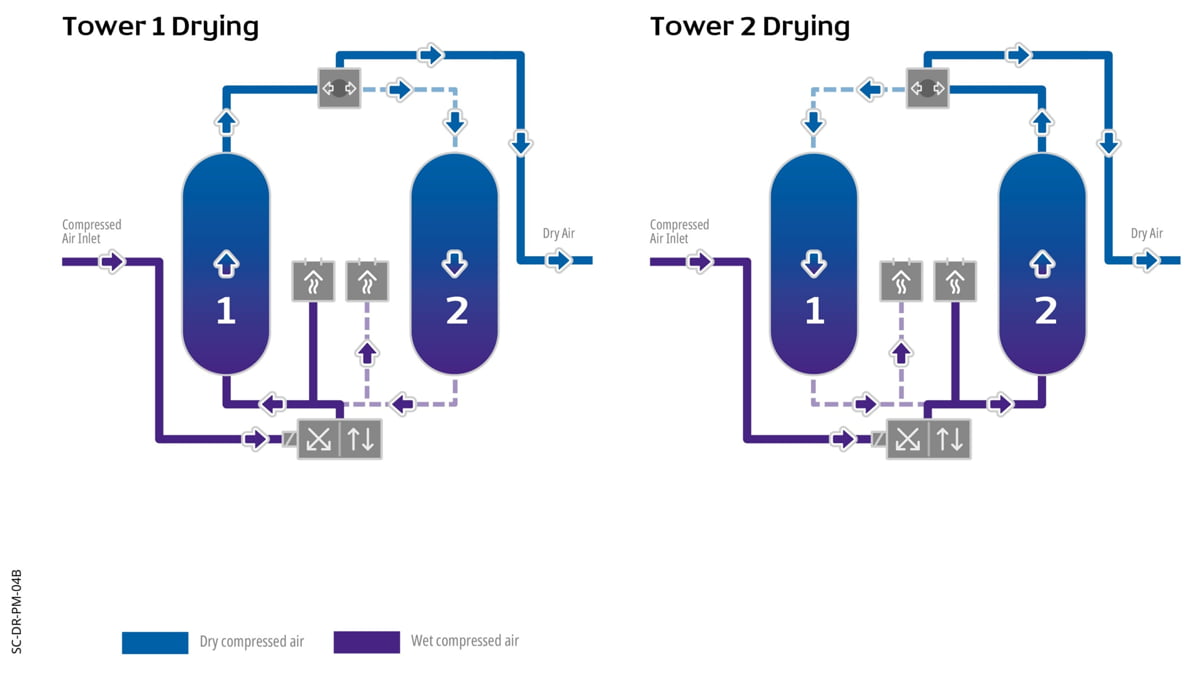
Working Principle
Stage 1 : Moist compressed air enters the desiccant-filled drying Tower 1 through the 3/2 Valve
Stage 2 : Up-flow drying enables the desiccant to strip the air stream of moisture. Clean, dry compressed air exits through NRV
Stage 3 : When in regeneration mode, Tower 2 depressurizes to atmosphere through the muffler when the exhaust valve opens
Stage 4 : Purge air (dry compressed air) is diverted before exiting through the bypass valve into Tower 2 and exits at exhaust valve to desorb the moisture from the desiccant. Once desorbed, exhaust valve closes, and Tower 2 is repressurized
Stage 5 : At tower shift-over Tower 2 will be placed on-line to dry the bed. Operations will switch and Tower 1 will be regenerate
From service plans, service networks to Genuine ELGi parts, explore our vast range of services and parts to find exactly what you need.
CONNECT WITH US