What is Class Zero Compressed Air?
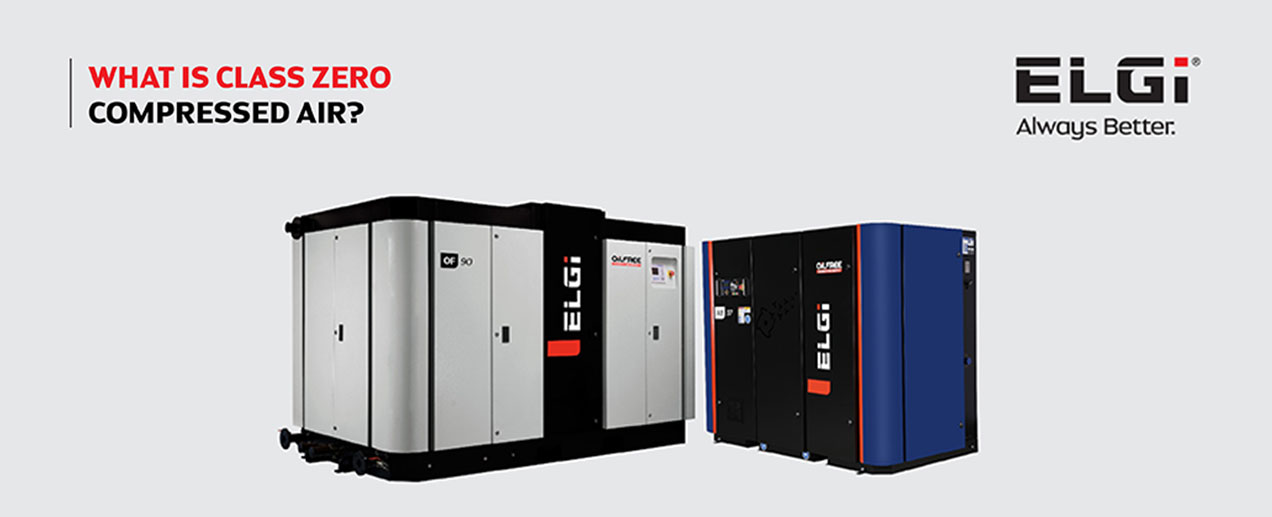
Conventionally, compressed air is specified in terms of flow (Cubic Foot per Minute, Cubic Meter per Minute) and pressure (psi g, bar g) required for the application. An important parameter that is often not specified is the quality of compressed air required for the application.
In this article, let us understand what we mean by air quality and then get into greater details about class zero compressed air and some of the common questions about class zero compressed air.
What are the typical impurities found in compressed air?
Below are the most commonly found impurities in compressed air
- Dust Particles
- Moisture
- Oil
Compressed air exiting an air compressor has dust particles. The typical sources of dust are rust particles from the compressed air piping, internal coating peel-off, weld spatters from the piping and aftercooler, and air oil separator filter media. Dust particles are also picked up from moisture traps, wet receiver tanks, and piping. The amount of dust in the compressed air is influenced by several parameters. A few are the build quality and material selection of the compressor's internals, compressor maintenance schedule adherence, piping material selection, and the wet tank’s internal coating.
When compressed air is cooled in the after cooler, moisture carried in the air changes state and becomes liquid water. While most of the water condensate is filtered out by the moisture separation filters in the compressor, traces of moisture still remain in the compressed air. The most common factors influencing the amount of moisture in the compressed air are relative humidity of air entering the compressor for compression, the effectiveness of the condensate removal system in the compressor, and the operating temperature of the air compressor.
Oil lubricated air compressors are the market's most popular source of compressed air. The compressed air output from these compressors carries traces of compressor lubrication oil. Some of the many factors influencing the amount of oil in compressed air include the air-oil separation system's efficiency, operating temperature, operating pressure, duty cycle of the compressor, effective functioning of the compressor valves, and velocity of compressed air exiting the compressor.
What are the impacts of these impurities?
When dust particles are not removed from the compressed air, it chokes up the downstream accessories such as dryers, making them lose their effectiveness and shorten their life. Dust particles also choke up appliances using compressed air, reducing their efficient operation or, in many cases causing irreparable damage to the appliances.
Moisture in compressed air causes compressed air pipes, fittings, and flow regulation valves to rust, thereby reducing their usable life. Moisture in compressed air also damages the appliances using compressed air by causing them to rust, choke and change properties.
Oil in compressed air affects the performance of all downstream accessories and ultimately results in reducing their usable life. Oil traces that reach the appliances using compressed air could completely damage them beyond repair. In many cases, oil traces reaching the end application might result in damaging the end product.
Which applications are sensitive to air quality?
A wide range of appliances uses compressed air to function. These appliances have varying tolerance levels to impurities found in compressed air. While some appliances can be more forgiving, others are extremely sensitive to any or all of these impurities. Based on how and where the compressed air is used, the compressed air application can be classified into contact and non-contact applications.
Contact applications are where compressed air directly interfaces with the end products that impact the consumer. Typical examples of contact applications can be found in industries such as food and beverage, electronics, chemical processing, pharmaceuticals, and medical.
Non-contact applications are typically actuation of a pneumatic circuit or appliance that in turn handles end products that impact the consumer. Typical examples of non-contact applications can be found in industries such as packaging, sheet metal working, manufacturing, and general applications involving any forms of pneumatic automation requiring high-quality compressed air.
How is air quality measured?
The International Standards Organization (ISO) is the world’s largest developer and publisher of international standards. The standard ISO8573-1: 2010 is the latest standard most commonly used in the industry to specify quality of compressed air. The first part of the ISO8573 standard specifies purity classes of compressed air with respect to particles, water, and oil independent of the location in the compressed air system at which the air is specified or measured. The purity level of each contaminant are shown separately in tabular form. However, for ease of use, the table below combines all three contaminants into one easy-to-use document.
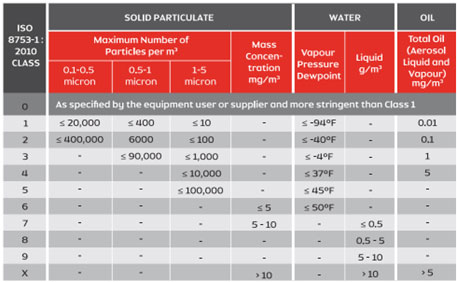
How is air quality specified in accordance with ISO8573-1:2010?
When specifying the air purity requirement in accordance to the standard, the quality class of particles, water, and oil are to be specified exactly in the same order.
Example air purity representation: ISO8573-1:2010 class 2.4.3
The above standard is to be read as follows:
-
Quality class of particles – Class 2: In each cubic meter of compressed air, the particle count must not exceed 20,000 in 0.1 to 0.5-micron size range, 400 particles in the 0.5 to 1.0-micron size range, and 10 particles in the 1 to 5-micron size range.
-
Quality class of water – Class 4: A pressure dew point of less than or equal to 37° F and no presence of liquid water.
-
Quality class of oil – Class 3: In each cubic meter of compressed air, the total oil contaminant should not be more than 5mg/m3.
What is class zero pure air?
Class 0 (zero) specifies to the purity class of oil in compressed air. As inferred from the ISO8573-1:2010 air quality standards table, it can be noted that class 0 does not mean that the air is free from any oil contamination. Any quality less than class 1 (0.01 mg/m3) is deemed as class 0, which can be mutually agreed between the user and the manufacturer.
Typically, applications that require class 0 purity of oil in compressed air also have stringent quality requirements for particles and moisture, and hence compressed air with class 0 quality is considered to be the highest degree of purity in the industry.
How NOT to design a class zero pure air system?
A general misconception in the industry is that oil-free compressed air can be achieved by using a series of downstream filters to filter out oil particles. The solution might seem to meet the requirement in theory and might be a less expensive option to install, but there are multiple drawbacks to this approach.
-
Filters do not have an efficiency of 100%, which means they will pass through a very small amount of oil.
-
Filters age and lose efficiency over a period of time which means more probability of oil to remain in the compressed air.
-
Filters have a tendency to rupture when choked which does not filter any oil in the compressed air. It is almost impossible to detect a ruptured filter, so the system is always at a risk.
-
There are no commercially feasible solutions to detect oil carry-over in a live compressed air system to warn the user so the problem is often detected after the damage is already done.
-
Installing a series of filters downstream increases the pressure drop of the total compressed air system that ultimately increases the operating cost of the compressed air system.
-
Frequent proactive replacement of filters increases the maintenance cost of the compressed air system.
-
Oil carried over from the air compressor is a function of several operational and maintenance parameters of the air compressor. Excessive oil carried out from the compressor will impact the life and efficiency of the downstream filters which is hard to predict.
The risk of having oil in the compressed air system varies based on the application. If there are regulatory norms demanding oil free air, the penalty ranges anywhere between a huge fine to legal law suites. If the sensitivity of downstream equipment handling compressed air does not permit oil in compressed air, then the penalty ranges anywhere between drop in operational efficiency to complete premature breakdown of the equipment.
How is class zero pure air achieved?
The only reliable way to consistently provide class 0 quality compressed air is to choose an air compressor that does not use oil in its compression chamber. These type of compressors are called oil-free compressors.
There are different oil-free compression technologies in the market. A few of the popular technologies are reciprocating oil-free piston compressors, oil-free scroll compressors, oil-free rotary tooth/lobe/screw compressors, water-injected screw compressors, and oil-free centrifugal/turbo compressors. The chart shows a general overview of when each technology is preferred.
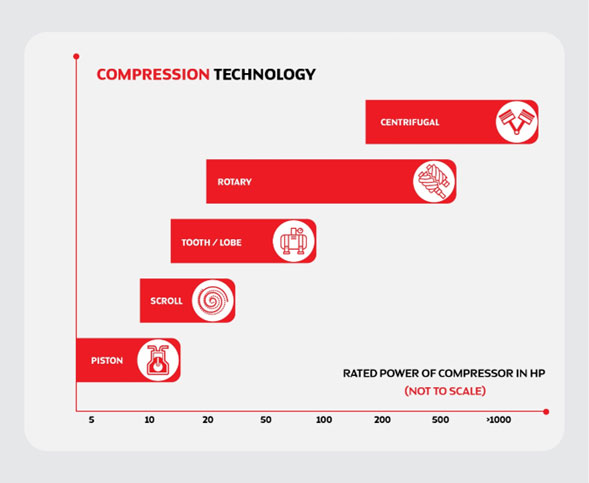
What are the advantages of using class zero pure air?
Following are some of the advantages of a class zero pure compressed air system:
-
The system meets the stringent air quality requirements of sensitive applications without running the risk of having oil contaminants mixed with the compressed air. This offers complete peace of mind.
-
Class zero pure air enhances the life of downstream equipment as there are no traces of oil in the compressed air system.
-
A class zero pure compressed air system does not require downstream oil filters, which reduces initial installation cost, cost of replacement of filters, and removes unnecessary pressure drops in the compressed air system. Since these unnecessary pressure drops are avoided, the compressed air system pressure can be maintained very close to the application pressure requirement, which results in additional savings in cost of energy.
-
The condensate that comes out of a compressed air system running class zero pure air is free of any oil and can be safely disposed according to the local practices without needing any additional treatment. This saves initial cost of installation, cost of maintenance of the condensate treatment, and disposal equipment.
-
In general, the oil-free compressor uses fewer consumables in comparison to an oil lubricated compressor which results in lower cost of consumables for a class zero compressed air system.
What are the disadvantages of using class zero pure compressed air?
Some of the disadvantages of having a class zero pure air compressor system are as follows:
-
Oil-free compressors are expensive to purchase when compared with the more conventional oil-lubricated compressors. This increases the overall initial cost of installation of the compressed air system.
-
When compared to oil-lubricated compressors, the oil-free compression technology is not very efficient. A comparable oil-free compressor delivers less flow for the same rated horsepower.
-
Conventional oil-free compressors usually have high operating temperatures with the exception of a few technologies, which result in less efficient operation and shorter life of parts which makes the cost of maintenance high in the long run.
-
Conventional oil-free compressors have very poor performance when operated under part load. Sizing the air compressor as close as possible to the application needs becomes
-
Oil-free compression technology is a bit more sophisticated than a conventional oil lubricated compression technology which requires a skilled technician to maintain and service the compressor, which results in increasing the cost of maintenance.
-
While these disadvantages prevail, it is important to note that the cost implications of risking oil contaminants in the compressed air system in an application that requires class zero pure compressed air is far greater and at times, catastrophic to deal with.
Is class zero compressed air demand growing in popularity?
The need for class zero pure air is growing year after year. The oil-free compression technology has been in the market for a few decades and its popularity continues to increase year over year as the awareness and need for class zero pure air grows. Below are some of the influencing factors driving awareness and popularity for class zero pure air.
-
Regulations on end products and their manufacturing processes in several industries are becoming more stringent that require class zero pure air.
-
Applications and the fundamental technologies driving them are becoming more sensitive to the presence of oil in compressed air, which affects longevity.
-
Increase in industrial automation and robotics has seen an organic increase in the need for class zero pure compressed air
-
Several air compressor manufacturers are invested and committed in making class zero pure air less expensive to own. Improvements and innovation in the design of a class zero pure compressed air system has lowered the total cost of ownership of these systems bringing them closer and closer to the conventional oil lubricated compressed air system. This results in more favorable return on investment (ROI) when using the class zero compressed air system.
-
Organizations are more committed to reducing the overall carbon footprint. Class zero pure compressed air system has the lowest carbon footprint in the industry.
In summary, class zero pure compressed air is the cleanest form of compressed air available in the industry as specified by ISO8573. This can only be achieved by installing an oil-free air compressor.
There is a growing popularity towards the use of class zero pure compressed air in the market and this market is estimated to grow rapidly in the future. The need for class zero pure compressed air is driven mainly by the application, which either has a regulatory need or a design or functional need. Class zero pure compressed air offers several advantages that outweigh some of the current drawbacks.
We understand that there are a lot of factors to consider when deciding to transition to oil-free compressors. Our team of compressed air experts is ready to help answer any questions you have and determine if oil-free is the right solution for your operations. Reach out to us to request more information!
CONTACT US EXPLORE ELGI’S OIL FREE PRODUCTS