The food and beverage industry is crucial to our economy, on both a global and national scale, as it permeates every household, delivering products that are integral to daily life. Air compressors are essential to food and beverage companies as they provide solutions from food packaging to processing and everything in between.
COMPRESSED AIR APPLICATIONS IN THE FOOD AND BEVERAGE INDUSTRY
The food and beverage industry relies on clean and contaminant-free compressed air for its operations. In the fast-paced world of food processing and beverage production, ensuring a clean, reliable, and energy-efficient air supply is of utmost importance. The following are common compressed air applications in the food and beverage sector:
Bottling and Canning
Compressed air is used to control machinery for filling and sealing bottles and cans, ensuring a smooth and efficient packaging process.
Packaging Operations
Compressed air powers pneumatic tools for tasks like sealing, labeling, and packaging, contributing to the automation and efficiency of packaging processes.
Cleaning and Sanitation
Compressed air is employed for cleaning and sanitizing equipment, production lines, and storage facilities, maintaining high hygiene standards in food and beverage manufacturing.
Conveying Ingredients
Pneumatic conveyors use compressed air to transport raw ingredients such as flour, sugar, and grains within the production facility, facilitating efficient material handling.
Aeration and Agitation
Compressed air is utilized in tanks and vessels to aerate and agitate liquids, aiding in the mixing and blending of ingredients during various stages of production.
Food Freezing and Cooling
In cryogenic applications, compressed air assists in freezing or cooling food products, ensuring preservation and extending shelf life.
Pneumatic Control Systems
Compressed air is crucial for powering pneumatic valves and controls that regulate the flow of liquids and ingredients in food processing.
Dough Kneading
In bakeries, compressed air may be used in dough kneading machines to achieve the desired texture and consistency in the production of bread and other baked goods.
Sparging and Blanketing
Compressed air is employed for sparging (introducing gas into liquids) and blanketing (creating a protective atmosphere) in tanks to prevent oxidation or contamination of sensitive food products.
Air Knives for Drying
Compressed air is utilized in air knife systems to remove excess moisture from food products or packaging, ensuring the quality and appearance of the final goods.
Controlled Atmosphere Storage
Compressed air is used to control the atmosphere in storage facilities, preserving the freshness of fruits, vegetables, and other perishable items.
THE IMPORTANCE OF COMPRESSED AIR QUALITY IN THE FOOD AND BEVERAGE INDUSTRY
The food and beverage industry adheres to strict standards to ensure the production of safe and consumable products. Compressed air comes into direct contact with various stages of food and beverage production, including processing, packaging, and storage.
When exiting the air compressor, compressed air can carry contaminants such as oil, water vapor, and particles which can introduce unwanted microorganisms or impurities into products, compromising their safety and quality. That’s why it's essential to ensure high-quality, class 0 contaminant-free air to help preserve the integrity of flavors, textures, and quality. Maintaining high compressed air quality is essential in the food and beverage industry to not only adhere to regulatory requirements by the FDA (Food and Drug Administration) but to also ensure product safety and to protect both equipment and consumer trust.
What kind of impurities can be found in compressed air?
Dust Particles: Solid particles like dust, rust, and debris from the ambient air or air compressor system can become suspended in compressed air. These particles can cause equipment wear and compromise product quality. To help limit the solid particles within compressed air, proper construction, reliable material, and air compressor maintenance is essential.
Moisture:Moisture in the form of water vapor is often present in compressed air. Excessive moisture can lead to corrosion, affect product quality, and contribute to the growth of microorganisms. To help guard against moisture in compressed air systems, water-separator filters are essential.
Oil: Lubricants used in oil-lubricated compressors introduce oil droplets or vapors into compressed air. For many industries this isn’t a cause for concern, but in the food and beverage industry, oil contamination is a significant issue since the compressed air comes into direct contact with products.
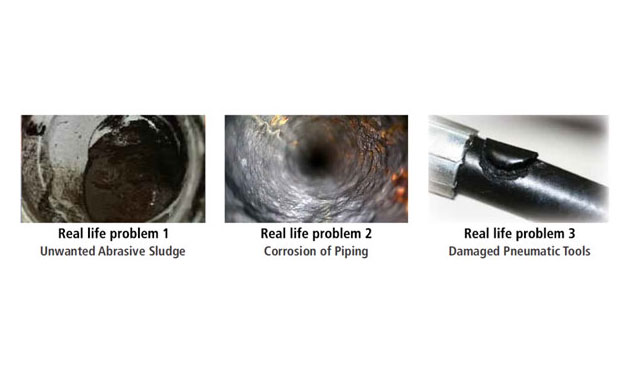
Dirt particles, moisture, and oil can lead to unwanted abrasive sludge,
corrosion of piping, and damage to pneumatic tools.
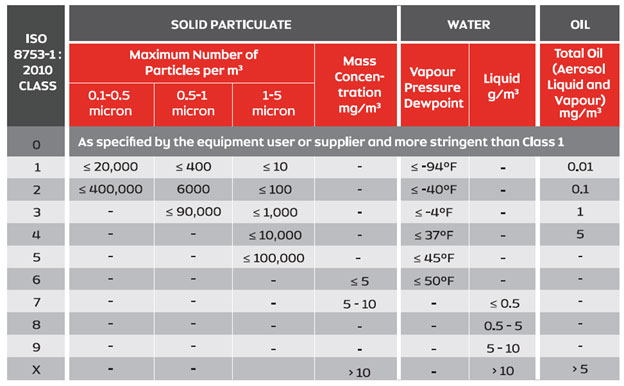
Easy-to-use chart that combines all three contaminants.
Classifying Compressed Air Based on Application: Compressed air is classified based on its application into various air quality classes to ensure it meets the specific requirements of different industries. The classification typically considers factors such as moisture content, oil content, and the presence of contaminants. Industries such as food and beverage, pharmaceuticals, electronics, and healthcare often require higher air quality standards to ensure product safety, process efficiency, and compliance with regulations.
International Standards for Air Quality: The most widely recognized standard for compressed air quality comes from the International Standards Organization (ISO), a key player in developing global standards. ISO 8573-1:2010 outlines the air quality by classes that are needed for different industry standards. The numbers within each class represent the maximum allowable concentration levels for various contaminants.
It's essential to understand the specific quality requirements for applications and choose compressed air systems and treatments accordingly. Regular testing and monitoring are also crucial to maintaining the desired air quality over time.
In the food and beverage industry, the classification of compressed air is a critical aspect, ensuring that the air used in various processes meets strict quality standards. Compressed air in this sector is often classified based on the specific application and potential impact on product safety and quality.
ELGi is proud to manufacture class 0 contaminant-free compressed air for applications in the food and beverage industry. What is class 0 contaminant-free air?
- Moisture Content: Extremely low moisture content.
- Oil Content: Absolutely no oil content.
- Contaminants: Ultra-pure air with no trace of oil or other contaminants.
Do you need assistance in identifying the air quality requirements for your industry? Reach out to our compressed air experts to find the best air compressor system for your facility!
Get Expert Guidance and Personalized Solutions
WHY CHOOSE ELGi AIR COMPRESSORS FOR THE FOOD AND BEVERAGE INDUSTRY?
Between oil-lubricated screw air compressors and oil-free air compressors, oil-free is the most used type in the food and beverage industry. If you’re looking to purchase an air compressor for your food or beverage business, it’s essential to choose food-grade compliant air compressors that use lubricants that are safe when used with food products to adhere to quality standards.
ELGi is your reliable partner for compressed air for the food and beverage industry. We've partnered with various facilities globally to ensure food-safe and efficient compressed air is supplied throughout food and beverage manufacturing processes. Why choose ELGi air compressors?
Highly Efficient and Reliable Air End
ELGi’s designs and manufactures its own air ends at its state-of-the-art foundry. ELGi’s unique air ends are designed with in-house developed eta-v profile rotors, with a 4/5 lobe combination. The ELGi air compressors’ air ends run at lower speeds offering high energy efficiency and reliability.
Best-In-Class Warranty
ELGi is proud to offer industry-leading warranty for all leading compressor models.
- EG Series Lubricated Rotary Screw Compressors: life time air end warranty, five-year compressor package
- EN Series Lubricated Rotary Screw Compressors: 6-year air end warranty, five -year compressor package warranty
- OF Series Oil-Free Rotary Screw Compressors: 4-year air end warranty, 1-year compressor package warranty
- AB Series Oil-Free Rotary Screw Compressors: 5-year air end warranty, 1-year compressor package warranty
Low Ownership Cost
ELGi air compressors provide you with the lowest cost of ownership on your compressed air system. With low parts and service costs and high-performing, energy-efficient products, choosing ELGi means choosing a cost-effective solution that optimizes your operational efficiency.
Ease of Maintenance
Maintenance isn’t a hassle with ELGi air compressors. Designed with the customer in mind, service components are easily accessible in all ELGi air compressors. Each compressor is equipped with an easy-to-use full function controller that provides at-a-glance compressor status.
Quality Assurance
ELGi is dedicated to quality and ensures each air compressor fulfills high requirements. With our stringent quality control techniques, we ensure that customers receive reliable and consistent products and services. ELGi is one of two air compressor manufacturers to have won the Deming Prize for Total Quality Management.
FOOD AND BEVERAGE INDUSTRY
INTERESTED IN OUR
SERVICES & PARTS?
From service plans, service networks to Genuine ELGi parts, explore our vast range of services and parts to find exactly what you need.
PLACE A REQUEST