The Thrill of Speed!
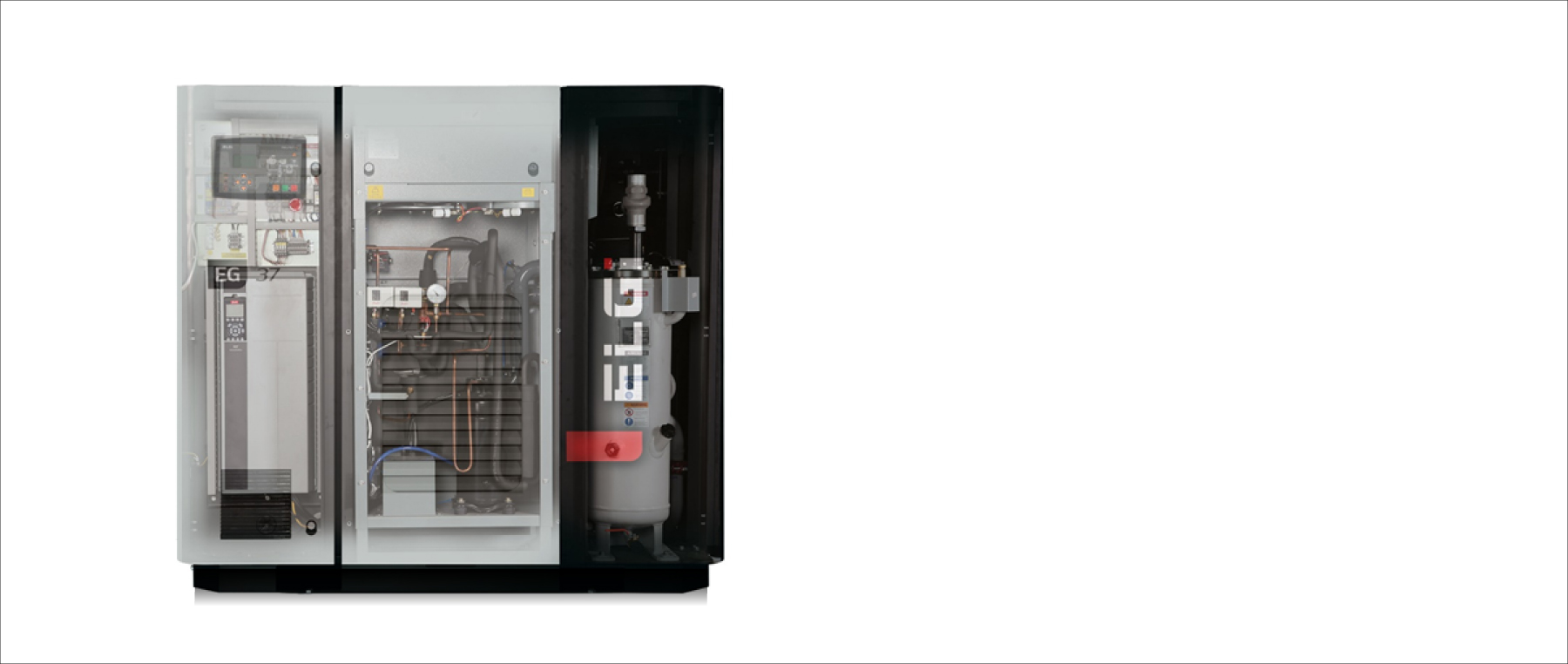
One of the important decisions to make while investing in an air compressor is to decide whether a production facility needs a fixed speed or a variable speed compressor.
Typically, energy costs contribute to more than 75% of the total life cycle costs of a compressor. Appropriate selection of compressors will result in optimal energy utilization, thereby reducing energy costs significantly for the user.
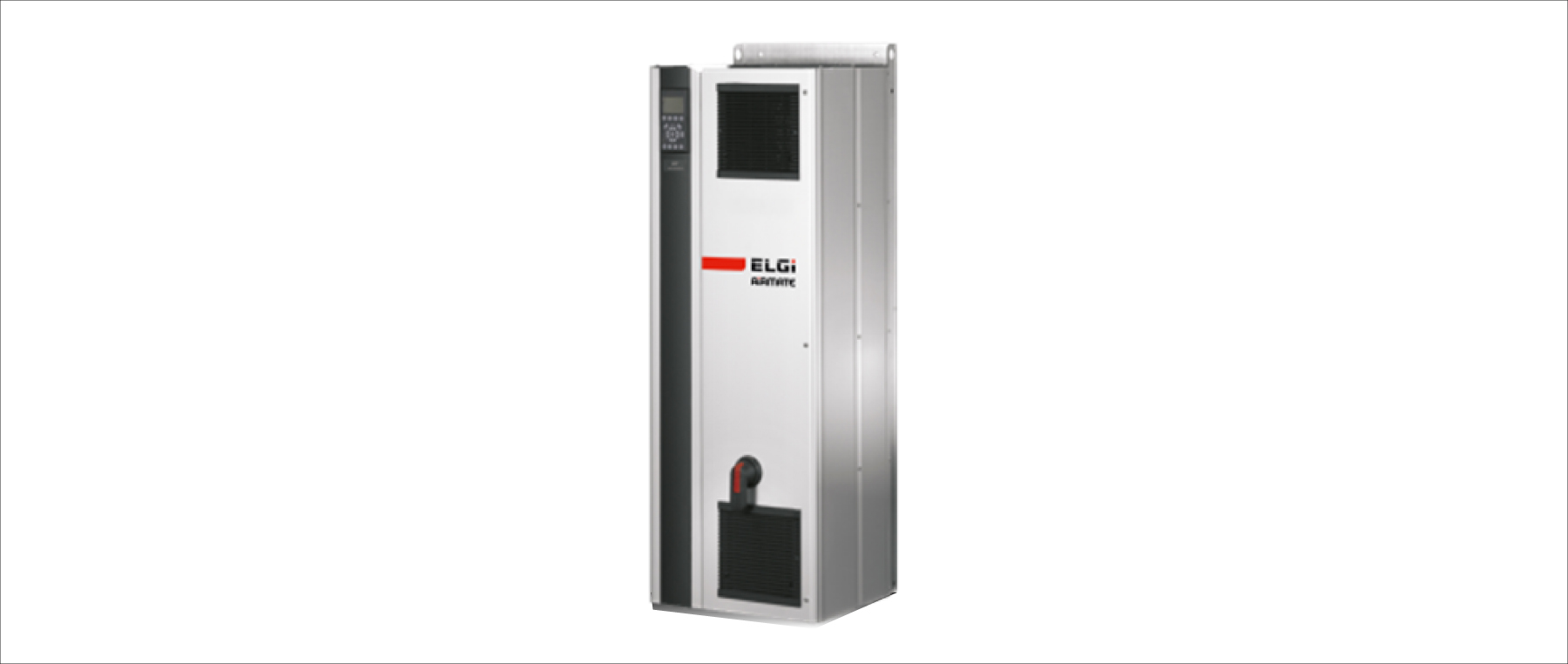
Fixed Speed Compressors
Fixed speed compressors are designed to deliver a fixed or constant flow (cfm or m3/min) of compressed air for a rated operating pressure. This is achieved by the electrical motor in a compressor running at a constant speed (rpm), which in turn drives the air end of a compressor.
Variable Speed Compressors
Variable speed compressors or compressors equipped with variable frequency drive (VFD) are designed to deliver varying flow of compressed air depending on the airflow demand by the applications in a production facility. This is achieved by varying the speed of the motor which in turn varies the speed of the air end of the compressor. The speed of the motor is proportional to the flow delivered by the compressor.
As the demand for airflow increases, the speed of the motor is increased up to the maximum rated speed, and when the demand for airflow decreases, the speed of the motor is decreased up to the minimum rated speed of the motor. The VFD also allows the motor to operate at frequencies between the maximum and minimum speeds.
To understand better on when to use a fixed speed compressor and when a VFD compressor will be beneficial, we will discuss further about, airflow demand.
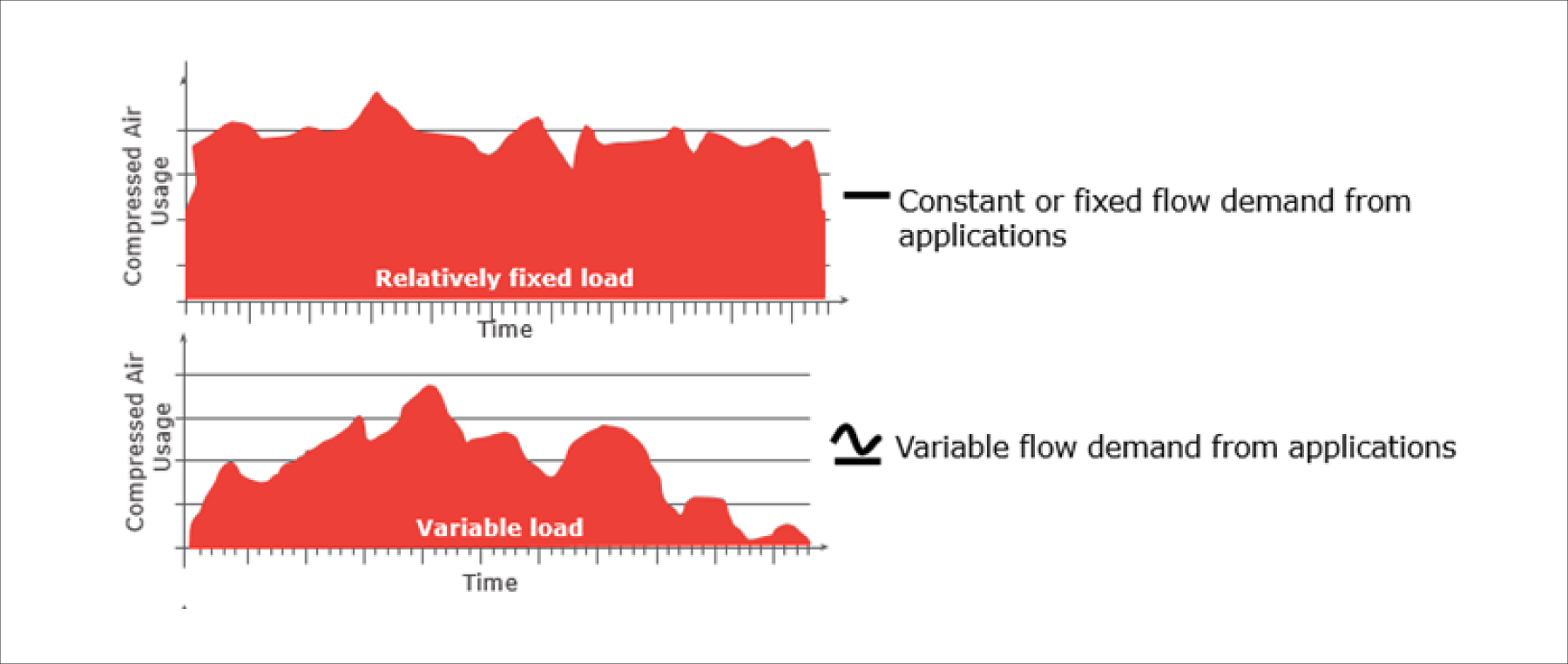
What is “airflow demand”?
Airflow demand is the rate of volume of compressed air (cfm or m3/min) required by applications in a production facility.
For example, a manufacturing facility with machining centers and a few pneumatic actuators need 100 cfm (2.8 m3/min) of compressed air at a rated pressure of 7 bar g. If these applications run continuously together in a shift, the flow demand is considered to be constant.
In the same example, if the machining centers and the pneumatic actuators are operated separately and for different durations during the shift, the airflow demand will fluctuate depending on the number of applications run at a given time.
An example of a relatively constant and variable airflow demand is shown in the graphs below.
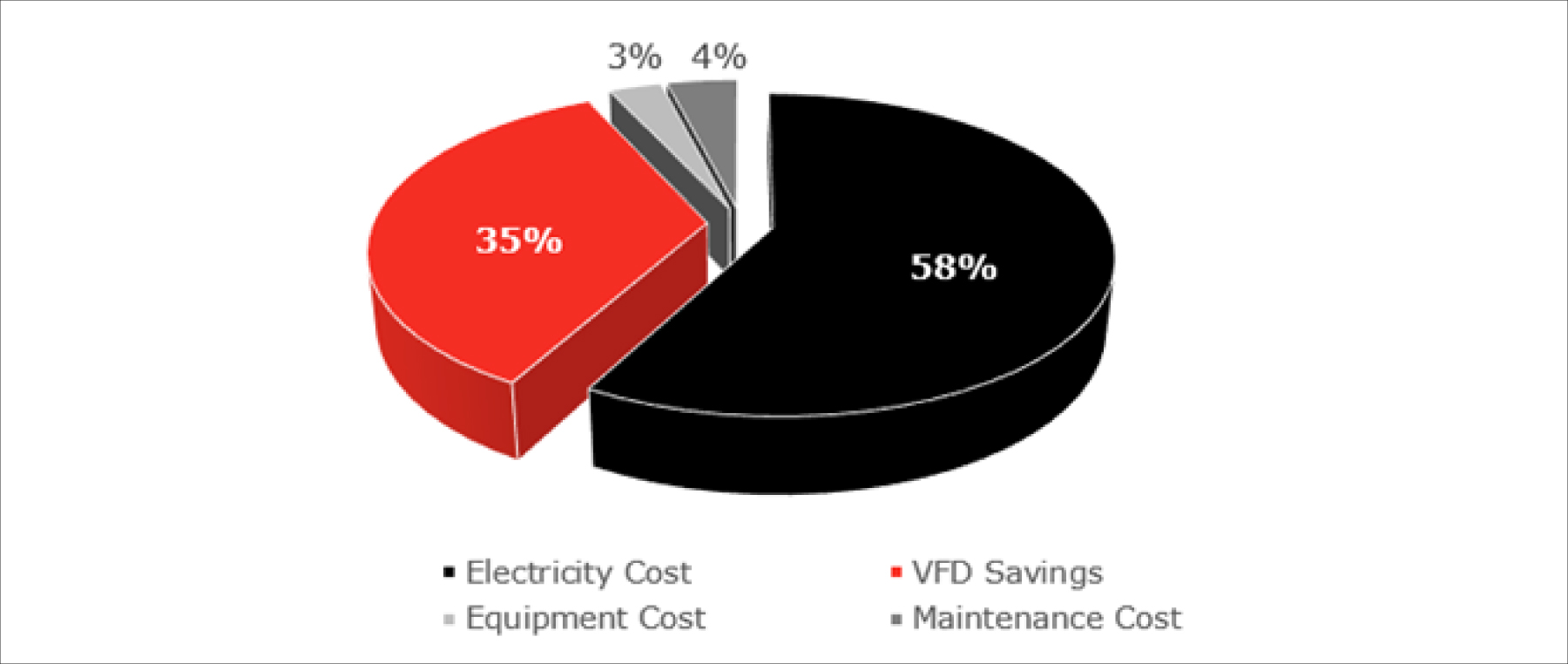
Fixed Speed or Variable Speed?
In addition to the airflow demand, another parameter to consider while choosing a fixed speed or VFD compressor is the duration of the airflow demand. If the airflow demand is relatively constant i.e if the flow demand does not fluctuate and remains relatively constant for a significant duration in a shift, the choice will be that of a fixed speed compressor. This is because fixed speed units deliver constant airflow and will meet the demands. The increased cost of a VFD unit is not justified in such a constant airflow demand scenario.
If the airflow demand is varying for a significant duration in a shift between the minimum and maximum flow capacity, then the choice will be compressors with VFD. The compressors equipped with VFD will vary the speed of the motor and ensure excess energy is not consumed by the compressor. Compressors with VFD can save up to 35% in energy costs compared to fixed speed compressors.
If a fixed speed compressor is chosen for a varying airflow demand, it will result in higher energy consumption. When the demand fluctuates significantly, fixed speed compressors will run on “un-load” mode where no compressed air is delivered but energy is consumed. The increase in the duration of unload mode of operation can result in significant loss of energy.
Our compressed air experts will help you understand the airflow demand and help you choose the most appropriate product solution to ensure optimal energy consumption at your production facility. ELGi offers both fixed and variable speed compressors with both oil-injected and oil free rotary screw compressors. Reach out to our experts today!