Energy savings by reducing pressure drop in compressed air systems
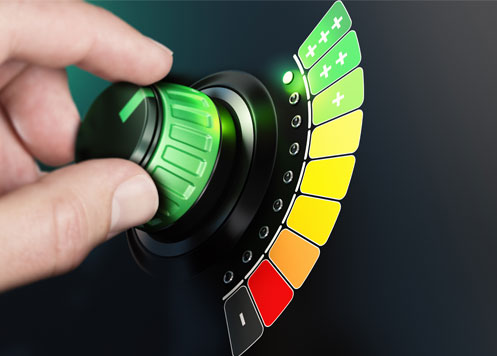
‘Pressure Drop’ is a term used to portray the reduction in air pressure from the compressor discharge point to the application point of usage. As the pressurised air travels through the pipes through the distribution system till the end application due to friction “pressure drop” occurs in the entire piping system and its downstream equipment. As a thumb rule, a well-designed compressed air piping system should not have a pressure drop not more than 0.5 per cent of the discharge pressure throughout the piping system network. This is calculated from the compressor discharge to the application point.
High pressure drop in the distribution system and the hoses, pipes, and joints results in lower operating pressure to the user and thus result in additional pressure generation and a significant increase in energy consumption. Pressure drop upstream of the compressors require higher compression pressures to achieve the control settings on the compressor and pressure drop in downstream will induce the system to generate more pressure. Air pressure optimisation, and minimising differentials in all parts of the system are important criteria for efficient operation and energy saving.
The most typical areas where “Pressure drop” occurs includes the pressure vessel, after cooler, air treatment equipment like dryers, filters and check valves, and the piping system itself. For every additional 1 bar increase in discharge pressure, there will be an additional energy consumption of approximately 7 per cent percent of the full load power. Additional generation of pressure will also lead to additional storage capacity and increase the cost of equipment.
Demand side pressure drop
On the demand side, pressure drop can occur due to resistance created to the airflow path because of blocks in the system. “Pressure drop” can also occur due to leaking of pipes, hoses, wrong selection of filters, undersize hoses /piping, and regulators.
Supply side pressure drop
On the supply side of the system, dryers, after coolers, moisture separators, and filters can be the main equipment’s causing significant “pressure drop”.
The maximum “pressure drop” from the supply side to the usage point will occur when the compressed air flow rate is highest. System components should be selected based upon these conditions. Filter elements should be changed when the pressure drop approaches the maximum recommended differential pressure by the manufacturer. In many cases, filter element change is directly proportional to higher pressure drop and energy losses.
Pressure drop in piping
Piping is always identified as having excess pressure drop because of improper sizing, several bends, and leakages in end usage application point of usage cannot retain the required pressure. The correct root cause analysis requires pressure measurements at different points in the piping system to identify the areas causing the excess pressure drop, a detailed Air-Audit will help in identifying the areas to minimize pressure drop.
Plant side
Many plant air compressors operate with a full- load discharge pressure of 7 bar and an unload discharge pressure typically 10 per cent higher than discharge pressure, typically many types of machinery and tools need air pressure less than 7 bar at the end point application. Selection of air compressor discharge pressure that meets the end application pressure requirements can be measured and if reduced will give significant savings in energy cost and also give a better life of operating equipment.
A typical pressure differential for downstream accessories like a filter, pressure regulators are normally set at 7 bar, only for not well maintained and poorly designed system the pressure requirement will be higher than 7 bar, this can be controlled by setting demand pressure to required end application need to save energy.
Selection of compressor
Compressor should be selected based on individual application needs. If an application requires higher pressure, it is advisable to use a separate compressed air system for that pressure rather than increasing the operating pressure of the compressor that supplies air to complete operating system in a factory. The RoI cost of a separate system will be economical compared to overall energy savings that plant would get by optimising pressure requirement.
Sample workout with a compressor pressure drop of 0.5 bar in a single 110 kW compressor | |
---|---|
Compressor power consumption | 110 kW |
Loss due to pressure drop of 0.5 bar g | 3.85 kW (3.5%) |
Energy lost/ year* | 18,480 kW.h/year |
Energy cost loss/year | 18,480* Rs 8 = Rs 1.5 lakh |
*at 16 hrs/day of operation for 300 days/year |
Finally setting compressor control setpoints to obtain more efficient operation by reducing constant loading and unloading patterns will further reduce energy consumption.
About the Author:
Raajeshwar M K is the VP & Head – Industrials of Elgi Equipments Limited.
READ MORE