Rotary Screw vs. Reciprocating Air Compressors
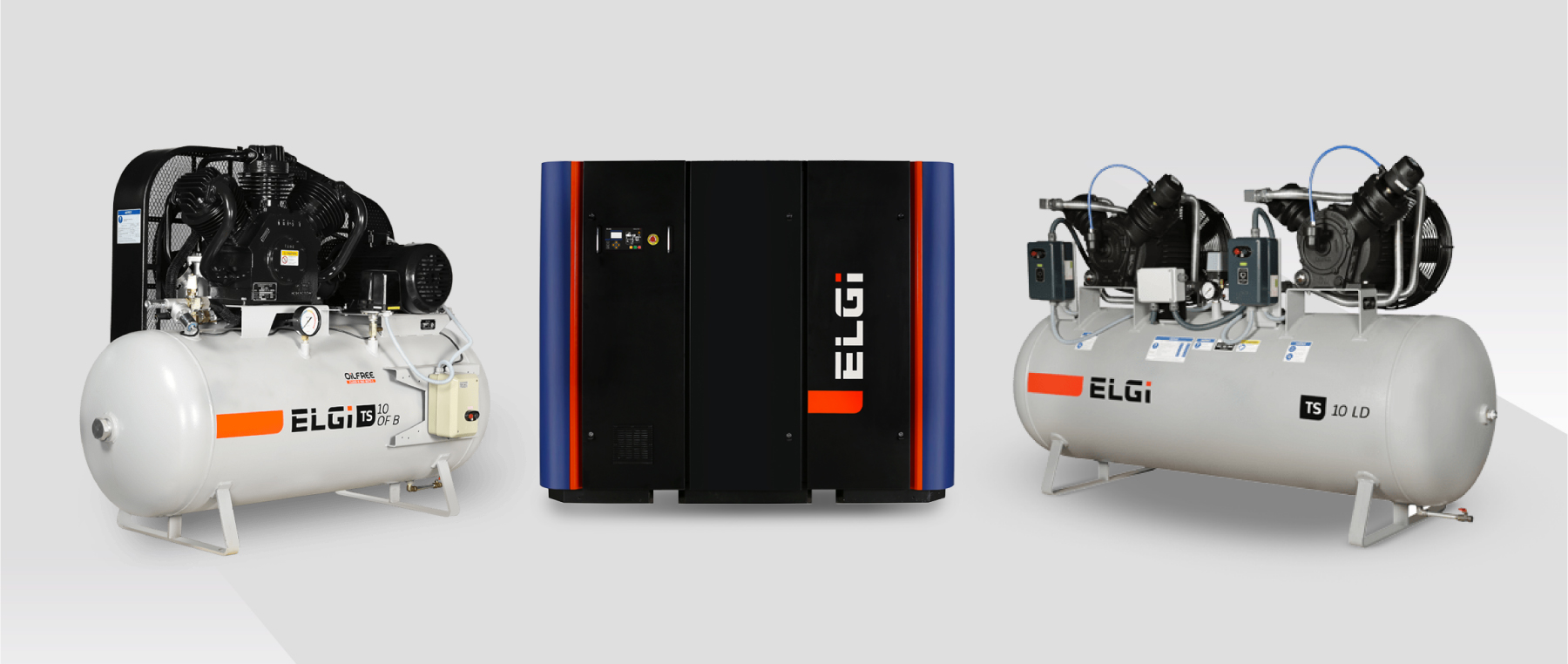
Rotary screw compressors and reciprocating compressors are the two most commonly used types of air compressors. It is important to understand their differences to make the right choice for specific applications.
Comparison of Rotary Screw and Reciprocating Air Compressors
When evaluating rotary screw and reciprocating air compressors, multiple factors come into consideration, such as design, operation, maintenance needs, performance characteristics, and suitability for applications.
Design and Operation:
Reciprocating compressors employ a piston-cylinder mechanism with linear motion, while rotary screw compressors utilize interlocking helical screws with rotary motion. Reciprocating compressors have a higher number of moving parts, including valves, piston rings, and connecting rods, whereas rotary screw compressors have fewer moving parts, reducing wear and tear. Rotary screw compressors are engineered for continuous operation, whereas reciprocating compressors are more suitable for intermittent usage.
Temperature:
Screw air compressors operate at controlled internal temperatures of 80 to 99 degrees Celsius due to the absence of friction between the screws. Heat dissipation is achieved through a fluid circuit, managed by a thermostat, where oil or lubricant forms a non-wearing seal between the rotors and casing.
In contrast, reciprocating air compressors encounter higher piston temperatures ranging from 150 to 200 degrees Celsius due to friction between the piston rings and cylinder walls.
Oil Filtration:
Oil-lubricated screw air compressors have a highly efficient three-stage oil filtration system that effectively eliminates the presence of oil in the compressed air, with oil particle concentration maintained below three particles per million (PPM).
In contrast, reciprocating air compressors lack an oil filtration system, resulting in higher air contamination. Deteriorated pistons and oil rings can allow oil to enter the compression side, elevating the oil content in the air.
Air-Receiver Tanks:
Choosing the appropriate size of an air-receiver tank can be challenging with rotary screw air compressors, as they are typically designed for continuous airflow without the need for a tank in most applications. In contrast, piston-based compressors use air-receiver tanks to store and smooth out the airflow before delivering it to connected applications. Once the tank reaches its maximum capacity, the equipment can operate effectively.
Maintenance:
Reciprocating compressors require regular maintenance due to their complex design and higher number of components. This includes lubrication of moving parts, inspection and replacement of valves, and monitoring of piston rings. Rotary screw compressors also require maintenance, such as regular oil changes, filter replacements, and monitoring of the air-end temperature.
Performance Characteristics:
Rotary screw compressors typically provide higher air output and can deliver a constant supply of compressed air. They are more efficient and consume less energy compared to reciprocating compressors.
In terms of pressure range, reciprocating compressors can achieve higher pressures, making them suitable for applications requiring greater pressure levels. Reciprocating compressors also have a quicker response time to changes in demand for compressed air, as they can start and stop more rapidly compared to rotary screw compressors.
Applications and Industries:
Reciprocating compressors are used in industries with intermittent compressed air needs, like automotive repair shops and home workshops. They power air tools, inflate tires, and assist in painting applications.
Rotary screw compressors are widely employed in commercial and industrial settings for continuous operation and high air output. They are commonly found in manufacturing, automotive, and construction industries, powering assembly lines, pneumatic machines, and heavy-duty machinery. Additionally, rotary screw compressors are utilized in pharmaceutical and food processing plants for clean and oil-free compressed air.
Reciprocating compressors are simple, cost-effective, and perfect for intermittent usage. Conversely, rotary screw compressors deliver continuous and efficient operation, making them ideal for heavy-duty applications with constant and high-demand airflow.
ELGi Equipments, a trusted manufacturer of reliable reciprocating and rotary compressors, offers a comprehensive range of air compressors, including rotary screw and piston-based reciprocating models. While reciprocating air compressors are suitable for low-capacity needs, your facility may require more energy-efficient units as the demand for associated applications grows. ELGi's rotary screw air compressors are known for their compact size, quiet operation, and reliability, ensuring a consistent airflow. They are ideal for a wide range of applications across various industries, providing a stable air supply.
To arrange a free consultation for selecting the suitable air compressor, contact us at communications@elgi.com.
RELATED BLOGS
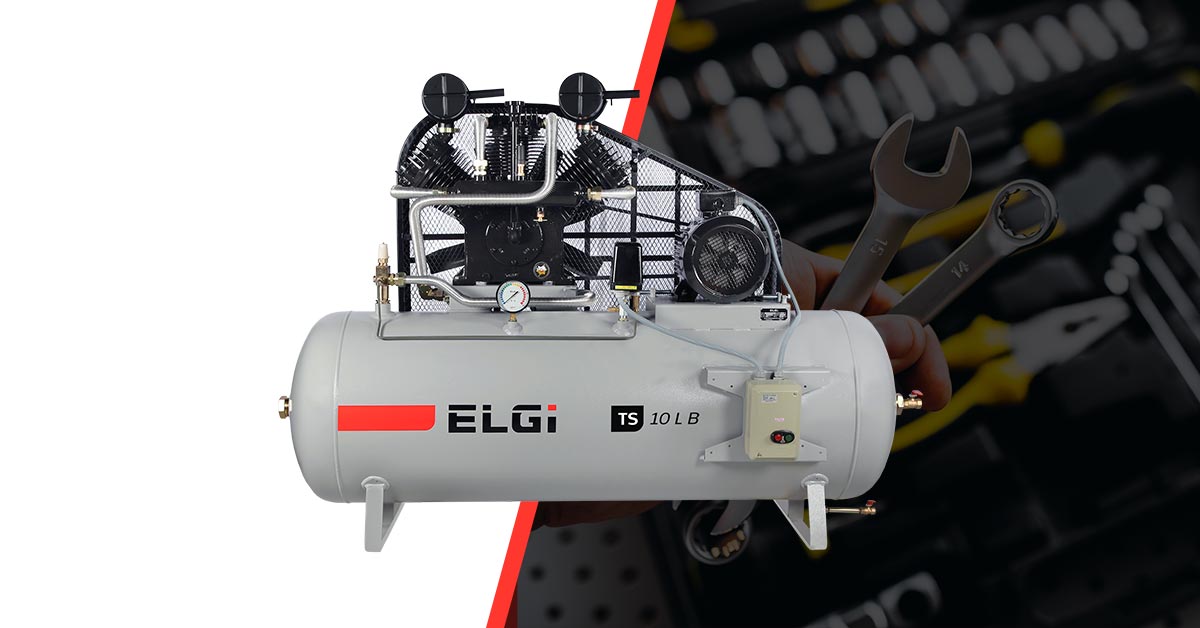
A reciprocating air compressor, also known as a piston compressor, is a positive di...
Read More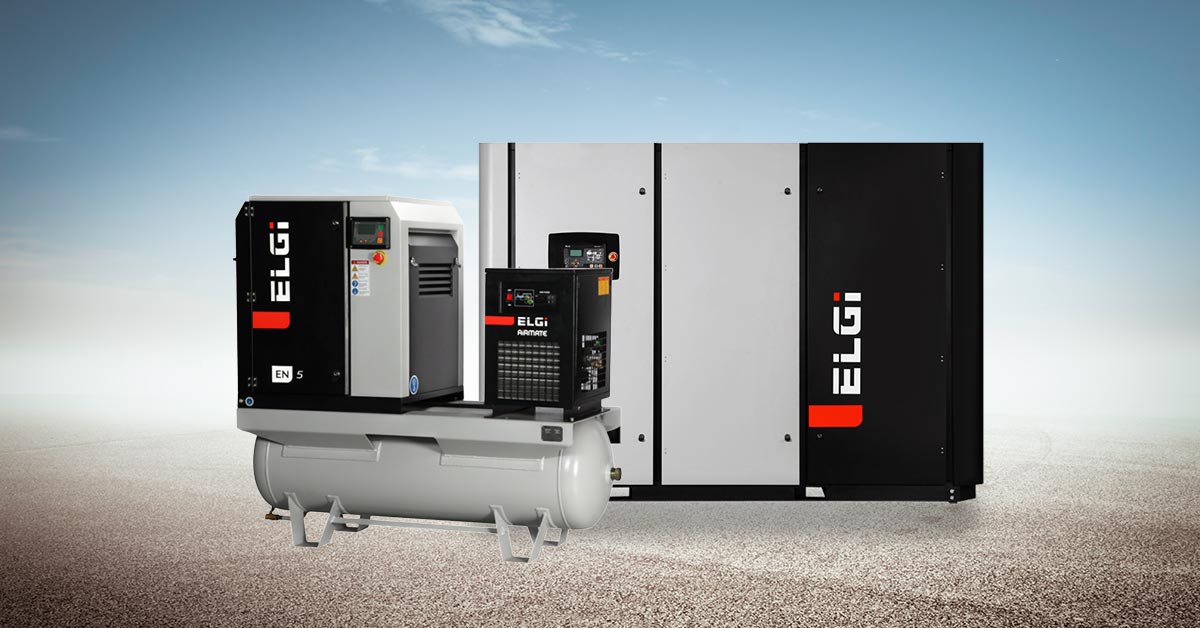
Rotary screw air compressors are a popular choice for industrial applications due t...
Read MoreDiesel vs. Electric Portable Air Compressors. The power source affects the maintena...
Read More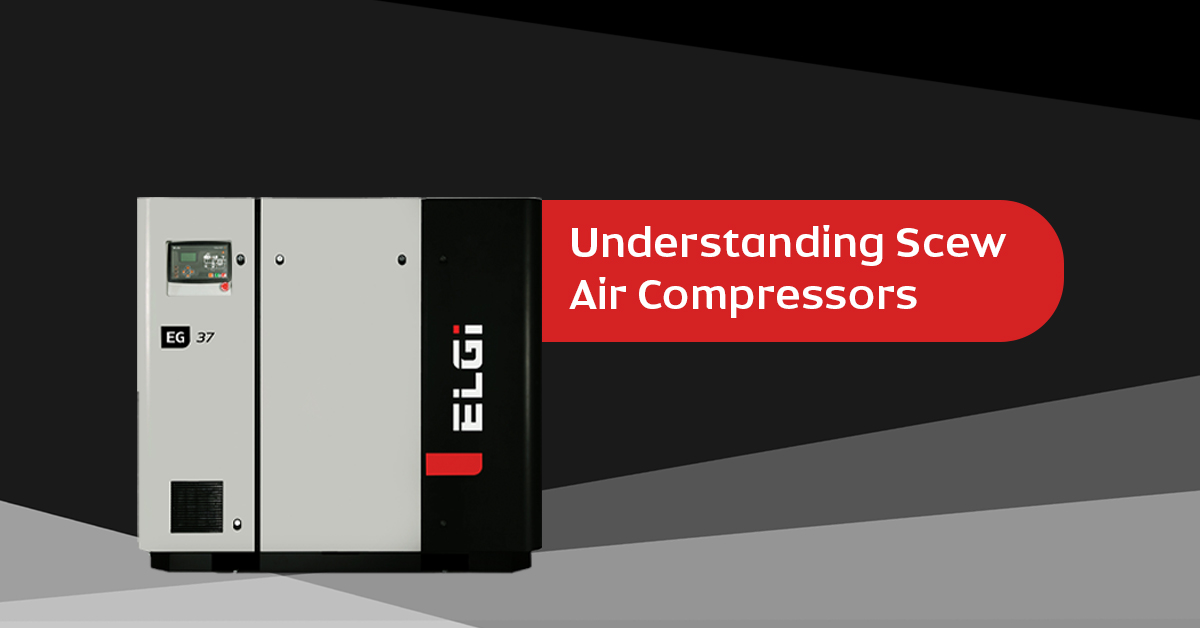
When selecting a suitable air compressor for your business, a few fac...
Read More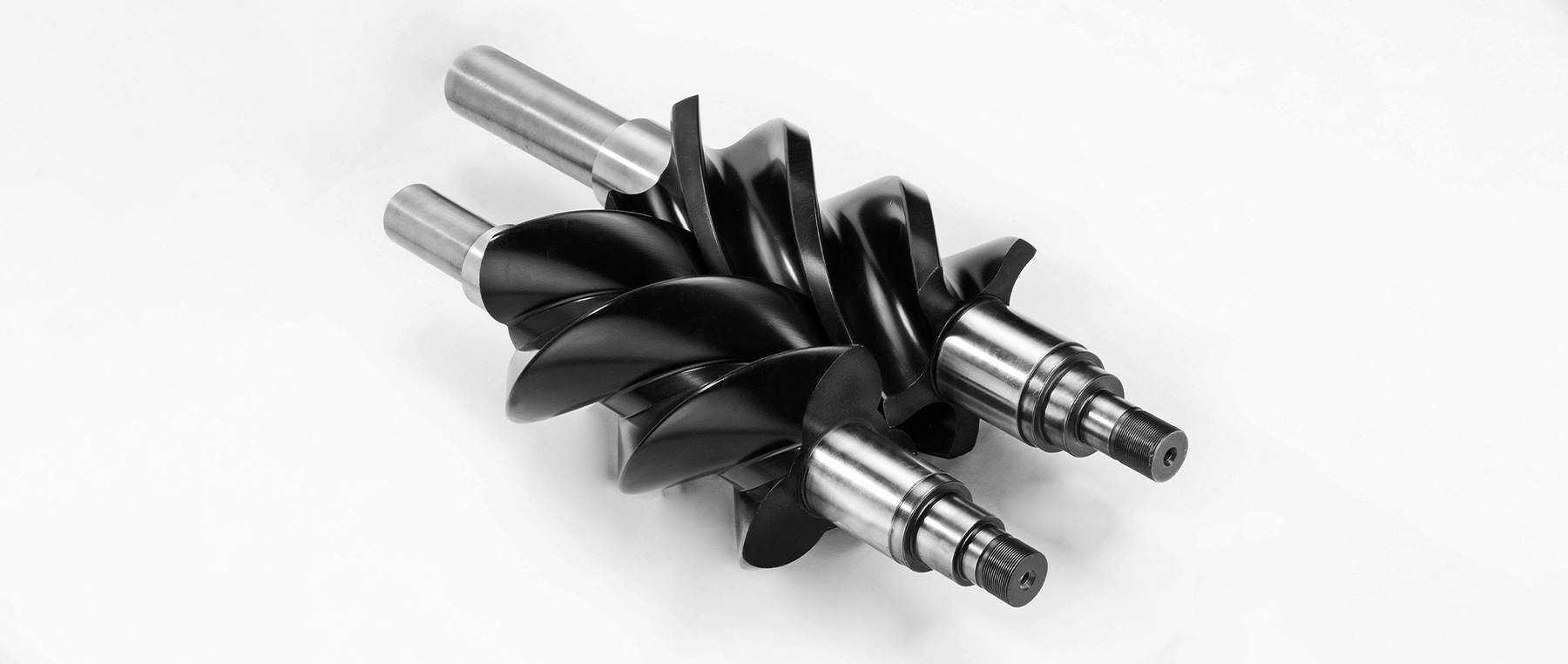
The concept of air compressors dates back thousands of years. The...
Read More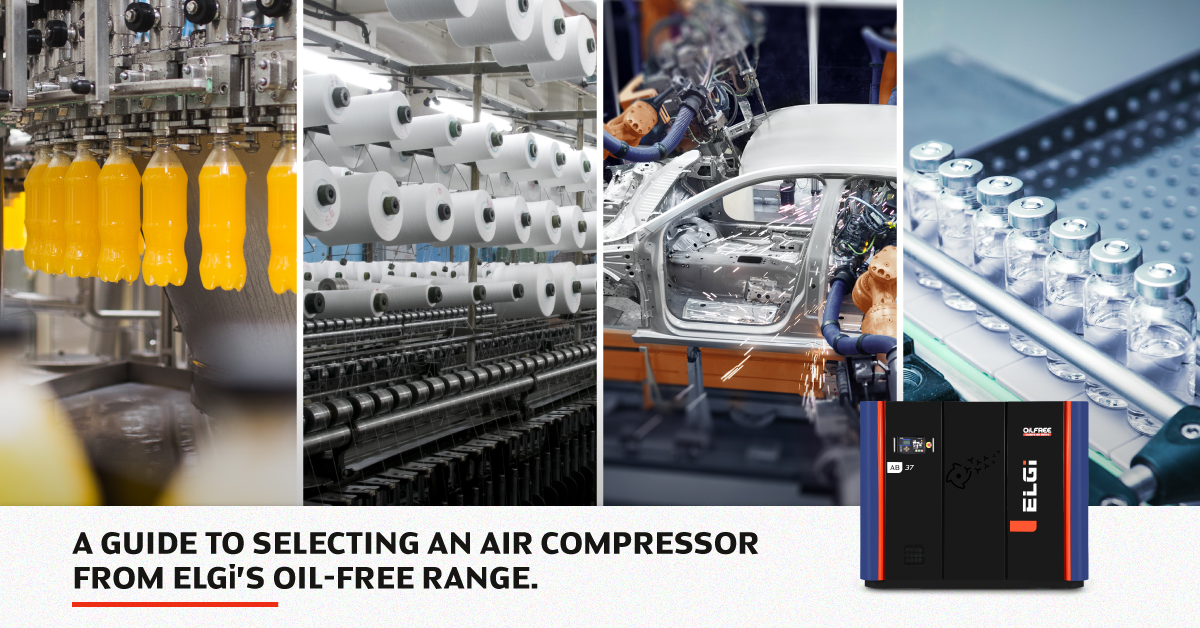
ELGi has been delivering an extensive range of compressed air s...
Read More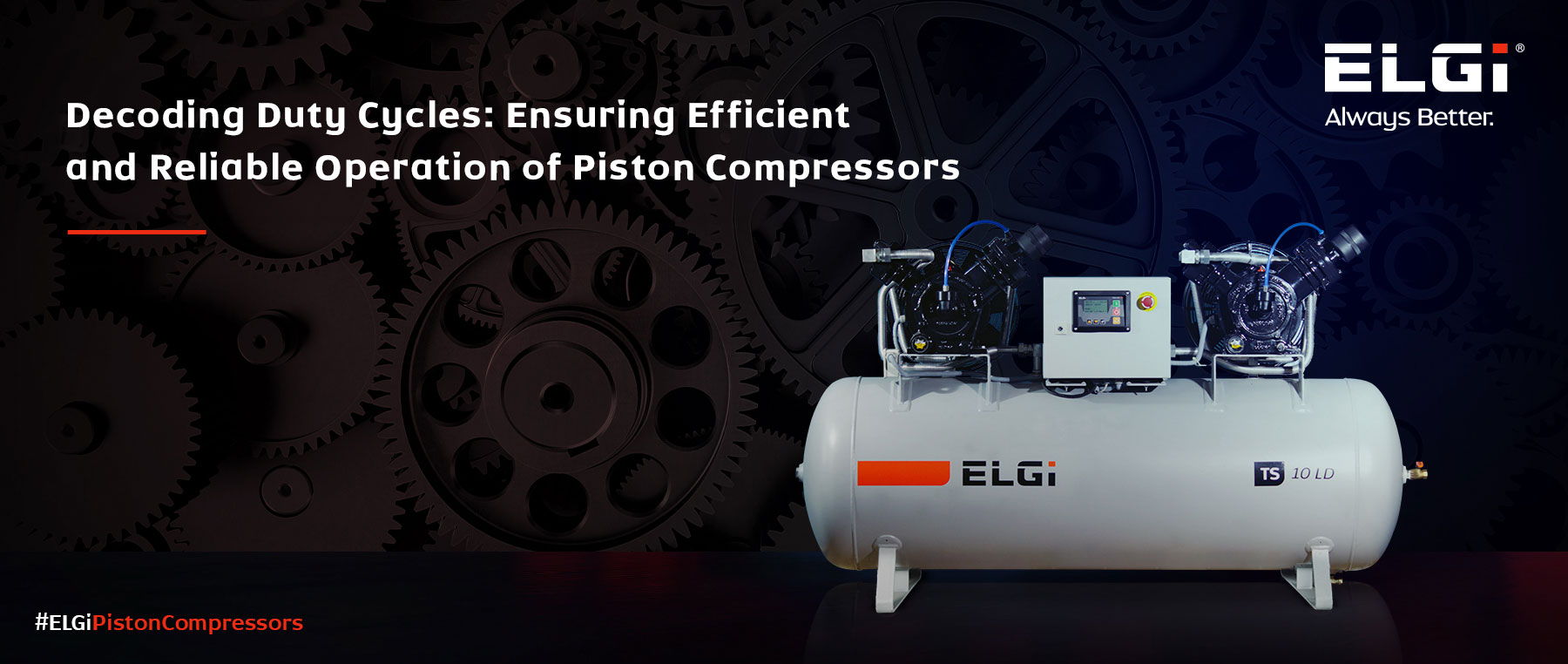
The duty cycle of piston compressors is a critical aspect to understand for an effi...
Read More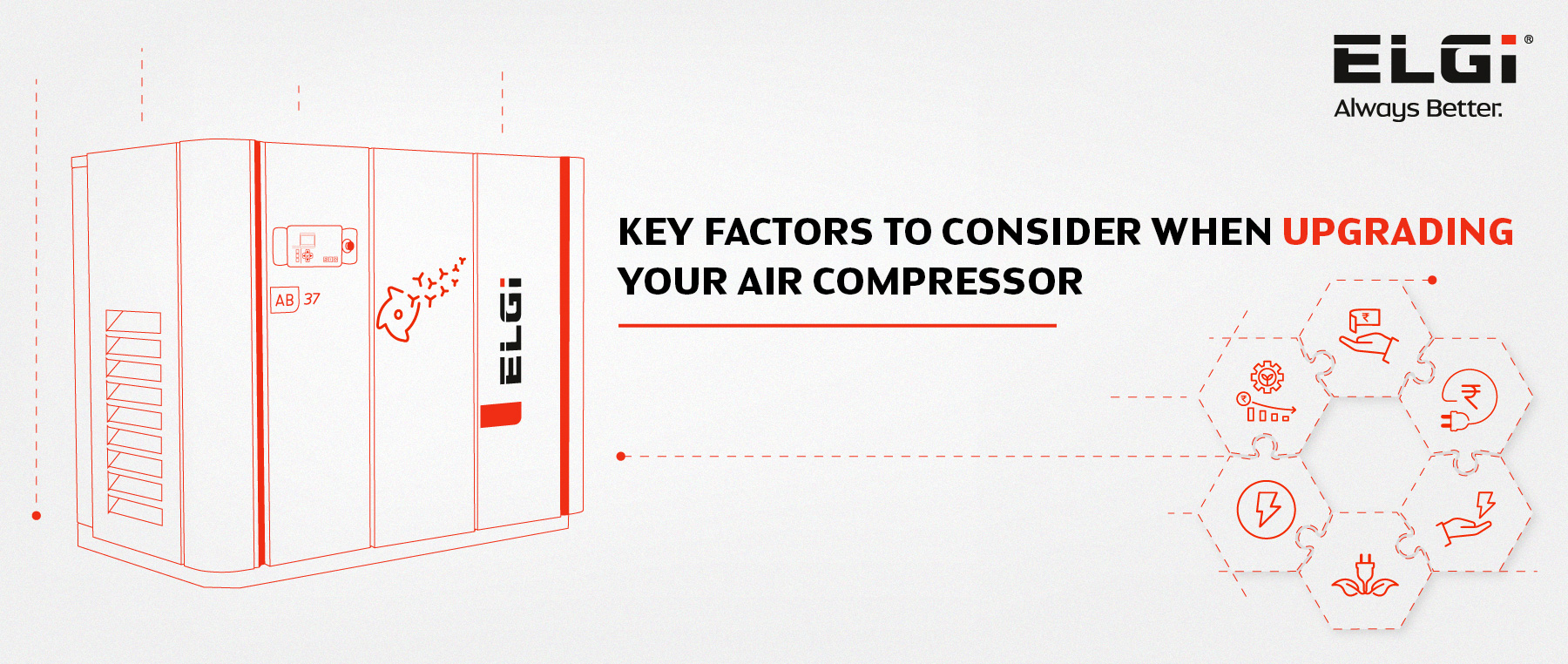
Upgrading your air compressor is a critical decision that can significantly impact ...
Read More