Key Factors to Consider When Upgrading Your Air Compressor
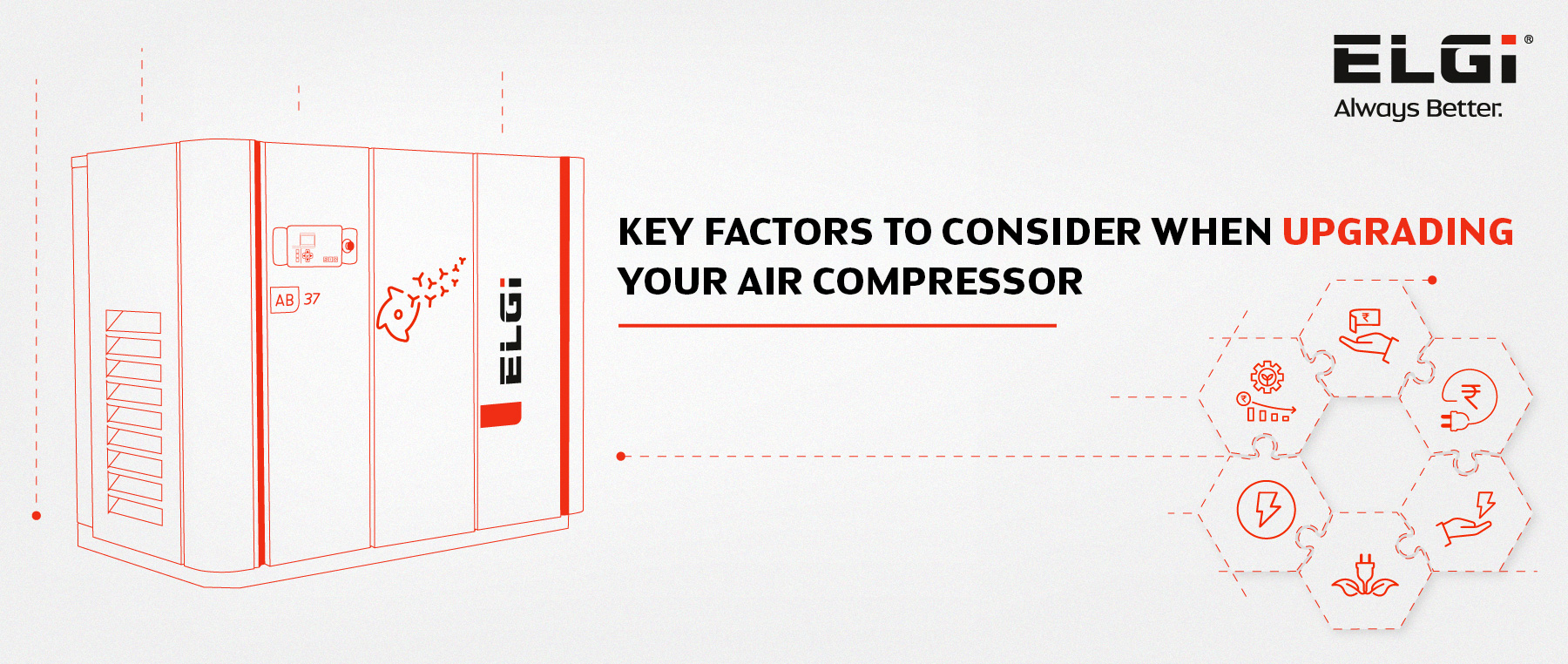
Upgrading your air compressor is a critical decision that can significantly impact your productivity, energy efficiency, and overall operational costs. Whether you're experiencing performance issues with your current compressor or looking to improve your system's capabilities, it's important to make an informed choice.
Here are the key factors to consider when upgrading your air compressors. By understanding these factors, you can ensure that your new compressor meets your specific requirements and delivers long-term benefits.
Assessing Your Current Air Compressor
Evaluate factors such as output capacity, power efficiency, maintenance costs, and reliability. If your compressor is struggling to meet your air demands, energy bills escalating due to inefficiency, breakdowns and repairs are becoming more frequent, then these may be signs that you need an upgrade. Identifying the limitations of your current compressor will help you understand areas that require improvement and guide you in selecting a suitable replacement.
Additionally, consider gathering data on your compressor's operational metrics, such as running hours, energy consumption, and maintenance history, to have a quantitative understanding of its performance.
Identifying Your Compressor Needs
It's crucial to determine your specific requirements before making any informed decision. Consider factors such as desired pressure levels, airflow demands, and duty cycle. Assess your current and future needs to ensure scalability. Evaluate the type of applications your compressor will support and the air quality requirements. By understanding these requirements, you can choose a compressor that meets your workload demands and avoid overspending on unnecessary features or under-sizing the equipment. Consult with process engineers, facility managers, and equipment suppliers to gather valuable insights into your air demand patterns and future growth projections.
Energy Efficiency
Energy costs constitute more than 75% of a compressor's overall life cycle cost (LCC), making them the crucial determinant for considering an air compressor upgrade. By identifying the current compressor's energy cost via an air audit or total input power assessment, one can evaluate the advantages of a new compressor in relation to energy savings. When the compressor's duty cycle experiences a significant surge due to additional manufacturing activities, the cost savings become more pronounced, leading to a quicker return on investment. Moreover, if a facility requires a higher airflow to accommodate expansion, it provides an excellent opportunity to assess the need and consider an upgrade. The machine's size (in kW) should also be considered, as larger units offer greater potential for savings.
Compressor Types and Technologies
Common types of compressors include reciprocating compressors, rotary screw compressors, and centrifugal compressors. Reciprocating compressors are suitable for small-scale applications, while rotary screw compressors are ideal for continuous-duty applications with higher airflow demands. Centrifugal compressors are used in large-scale industrial applications.
Consider factors such as space requirements, noise levels, and maintenance needs when selecting the appropriate compressor type for your upgrade.
Capacity and Sizing
Selecting the right capacity for your air compressor is critical. Consider your airflow requirements, pressure demands, and duty cycle. An undersized compressor may struggle to meet your air demands, leading to decreased efficiency and increased wear and tear. Conversely, an oversized compressor can result in excessive energy consumption and higher upfront costs. Properly calculate the required capacity based on your specific needs to avoid these issues and optimize your compressor's performance. Factors such as future expansion plans, peak demand variations, and air quality considerations should also be considered during sizing the air compressor.
Lifecycle Costs and Return on Investment (ROI)
Evaluating the lifecycle costs and Return on Investment (ROI) is essential when upgrading your air compressor. Consider initial costs, energy savings, maintenance expenses, and equipment lifespan. While a more energy-efficient compressor may have a higher upfront cost, it can result in significant long-term savings through reduced energy consumption.
Factor in maintenance costs and the expected lifespan of the compressor to calculate the ROI accurately. By assessing the total cost of ownership, including installation, operation, maintenance, and disposal costs, you can make a financially sound decision and maximize your investment. Conduct a comprehensive cost analysis and compare different compressor models to determine the most cost-effective option.
Maintenance and Service Support
When air compressors age and require consistent maintenance to remain operational, the associated unplanned repair costs start to mount. If these repair expenses approach about 40-50% of the compressor's value, coupled with the declining energy efficiency characteristic of older models, it's an opportune moment to assess and consider upgrading your air compressor.
Breakthrough products
It is essential for Compressor users to look out for breakthrough products that will result in superior performance. AB Series, introduced by ELGi features a revolutionary oil-free technology that significantly reduces the life cycle cost of oil-free compressors. These breakthrough advancements present a valuable opportunity to enhance overall plant efficiency and performance, effectively meeting the diverse needs of users. As production demands in a plant continue to grow, the adoption of alternative compressor technologies becomes necessary, such as transitioning to centrifugal compressors to accommodate larger volumes of compressed air.
Technology innovations
There are several compelling reasons to consider an upgrade, including notable advancements in controller features, enhanced intelligence through additional sensors, and the evolution of IoT capability. These improvements yield various benefits, such as increased uptime, valuable insights for optimizing energy efficiency, and the ability to fine-tune operational settings based on real-time data. Moreover, the ability to remotely monitor the compressed air system 24x7 from any location in the world is a remarkable advantage, especially for industrial plants where system failures can lead to substantial productivity losses. Another crucial factor to consider is the improvement in the lifespan and reliability of consumables. For instance, ELGi has introduced oil filters with double the lifespan for their oil-lubricated rotary screw compressors across multiple models. These advancements not only enhance the efficiency of the compressors but also significantly enhance their reliability and overall sophistication.
Upgrading your air compressor requires careful consideration of various factors. You can make an informed decision by assessing your current compressor, determining your requirements, considering energy efficiency, evaluating compressor types and capacities, factoring in lifecycle costs and maintenance support.
An upgraded air compressor that aligns with your specific needs can significantly enhance your productivity, reduce operational costs, and improve overall system performance. It is advisable to research, consult with experts, and perform a comprehensive cost analysis to ensure a successful upgrade that meets your present and future requirements.
RELATED BLOGS
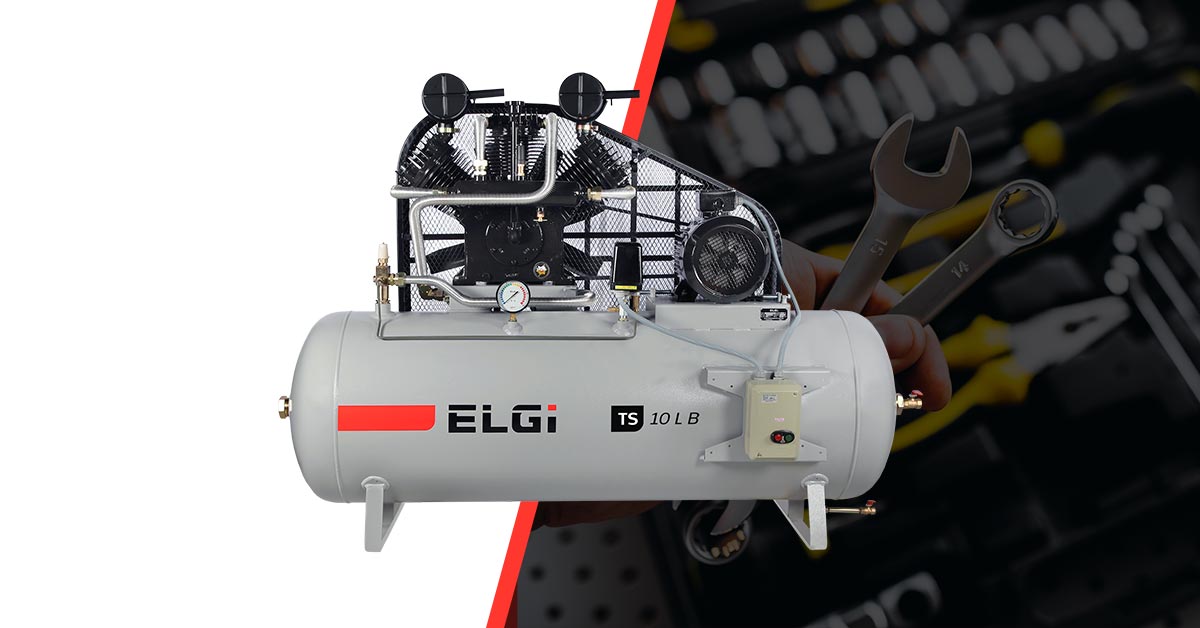
A reciprocating air compressor, also known as a piston compressor, is a positive di...
Read More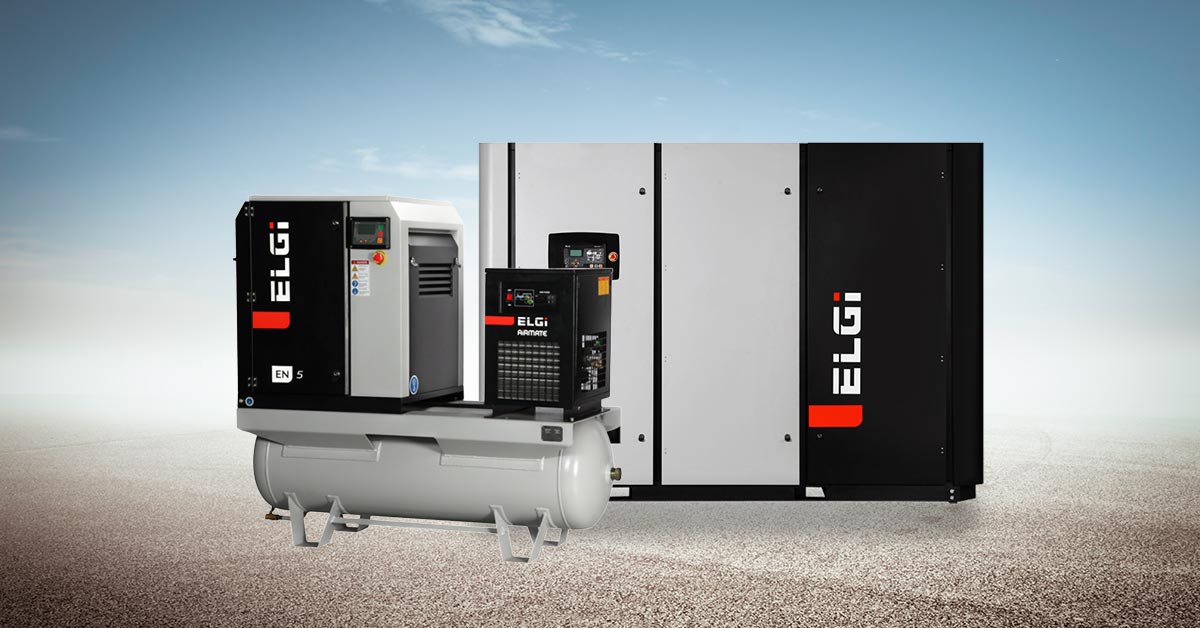
Rotary screw air compressors are a popular choice for industrial applications due t...
Read MoreDiesel vs. Electric Portable Air Compressors. The power source affects the maintena...
Read More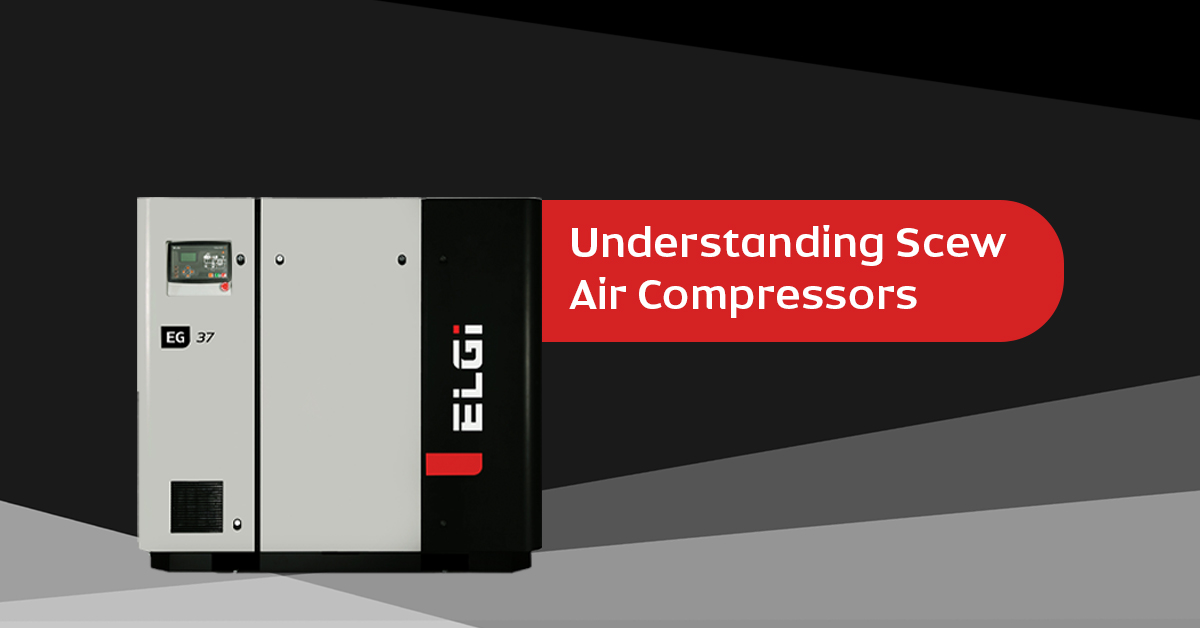
When selecting a suitable air compressor for your business, a few fac...
Read More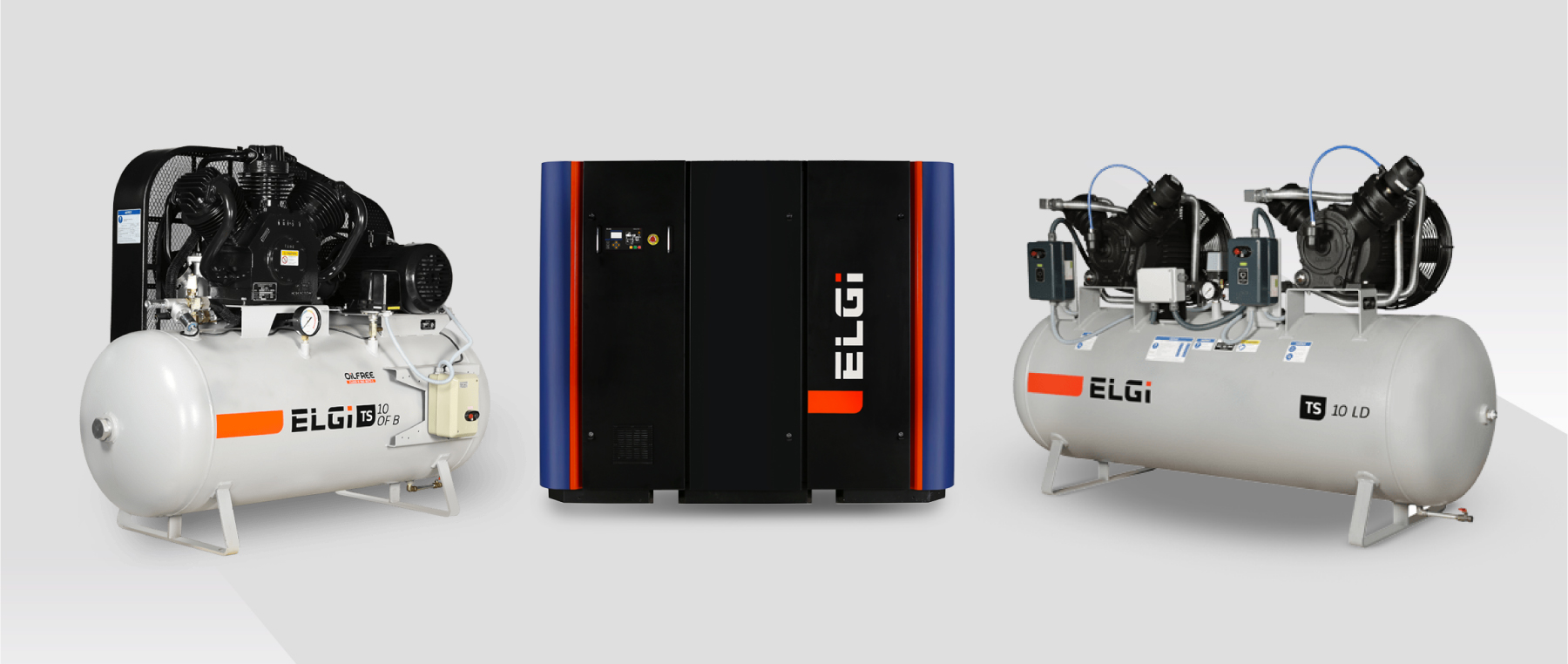
Rotary screw compressors and reciprocating compressors are the two mo...
Read More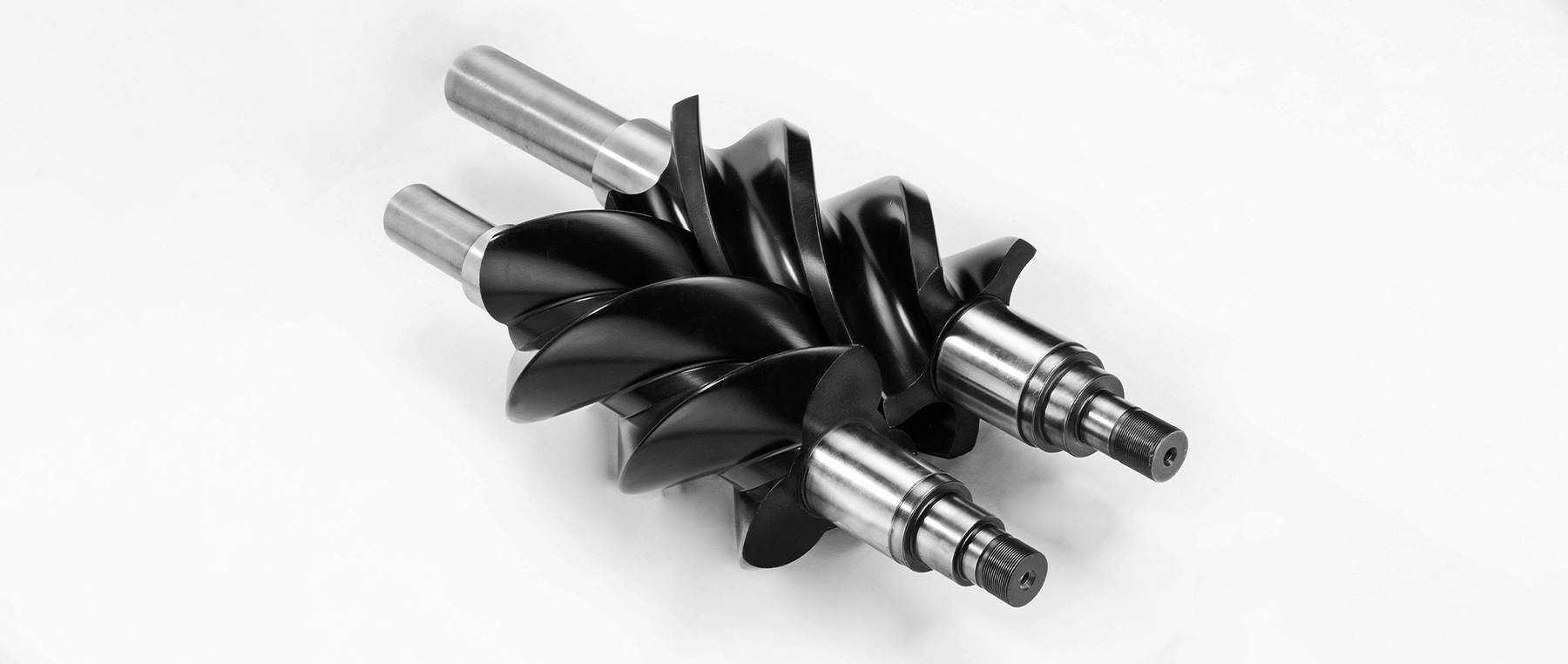
The concept of air compressors dates back thousands of years. The...
Read More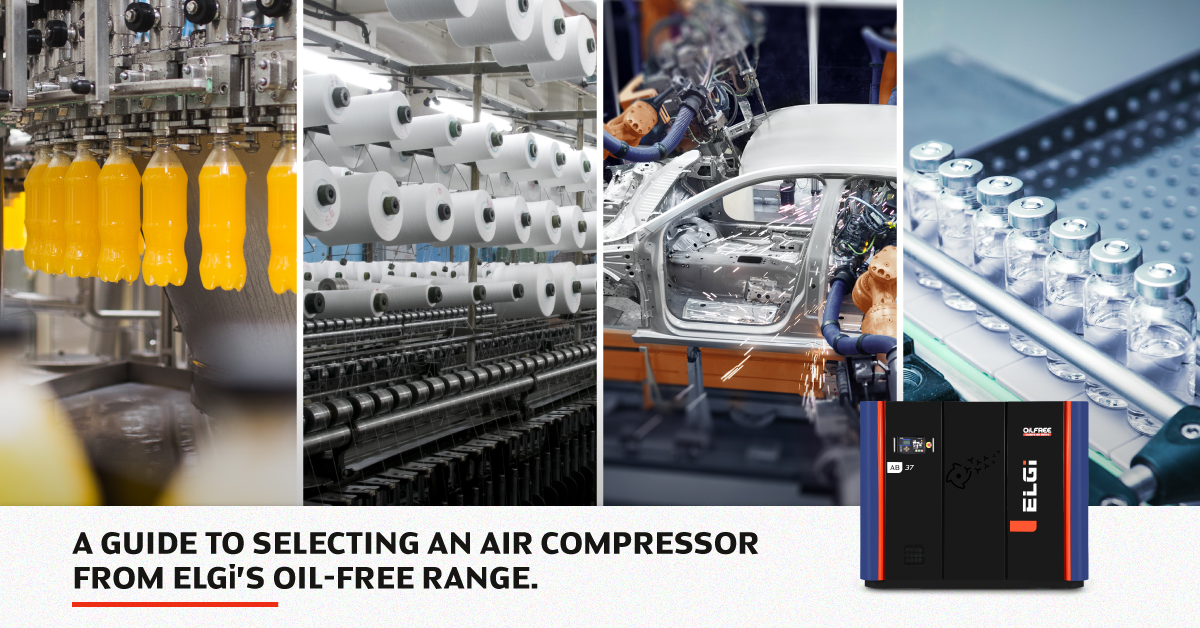
ELGi has been delivering an extensive range of compressed air s...
Read More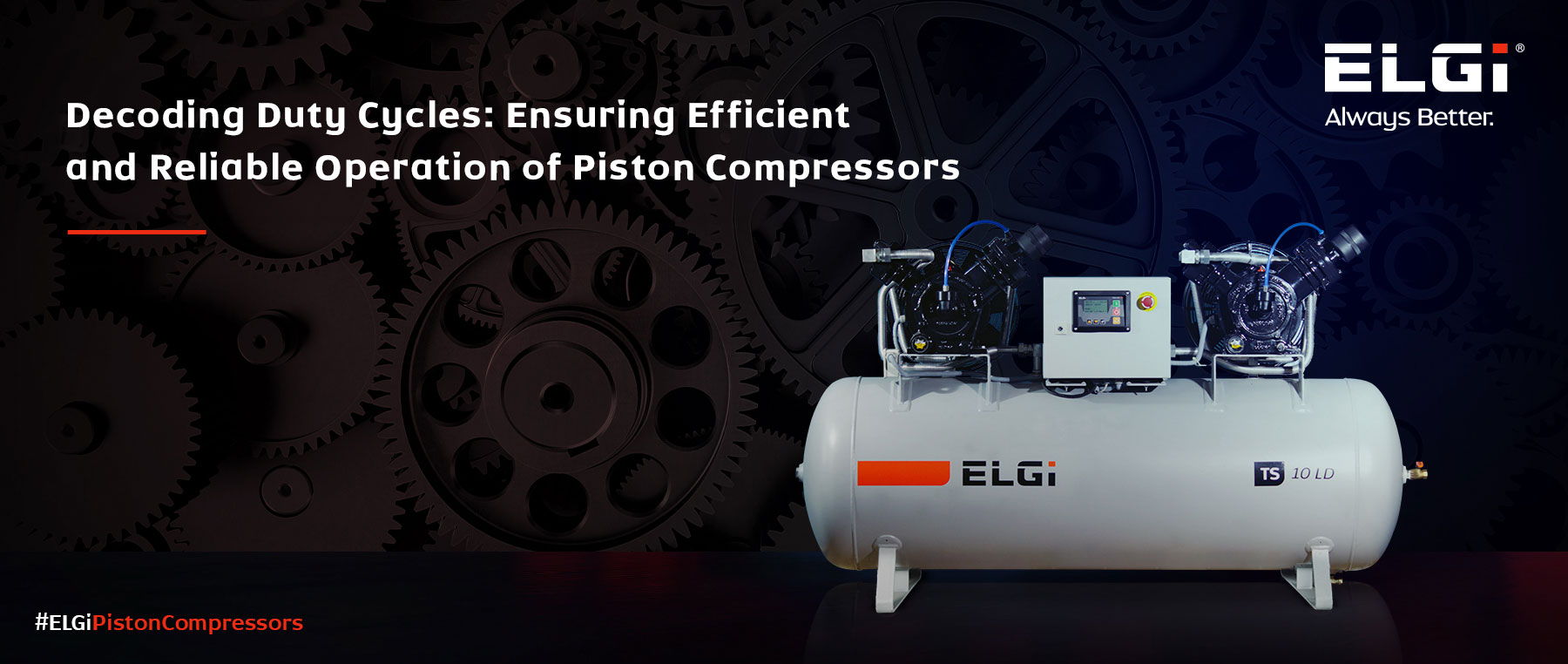
The duty cycle of piston compressors is a critical aspect to understand for an effi...
Read More