Evolution of Screw Air Compressors
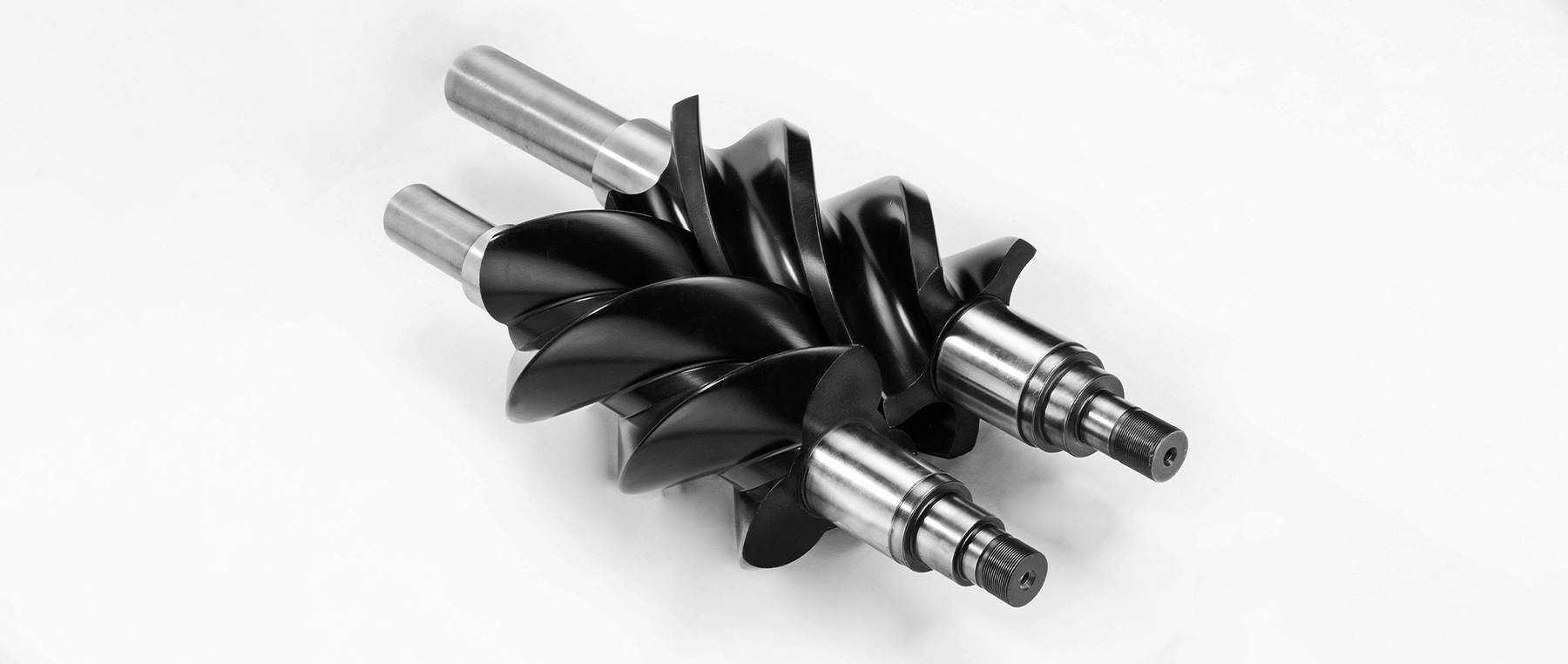
The concept of air compressors dates back thousands of years. The earliest versions were bellows, used to fan furnaces, increasing their heat and enabling ancient humans to forge superior metals for their tools and weaponry.
With the advent of the steam engine, these machines quickly became the preferred choice for powering air compressors. This was later superseded by Internal Combustion (IC) engines, which served as the driving force behind reciprocating air compressors. As industries grew in scale and complexity, the demand for more efficient compressors - requiring minimal maintenance and capable of extended operational periods - soared. The rotary air compressor emerged as the solution to these needs.
Over the years, both compressors have evolved significantly, becoming highly efficient and technologically sophisticated. However, traditional reciprocating air compressors come with inherent drawbacks. The most significant is the carryover of lubricating oil into the compressed air. Although filtration can eliminate a substantial amount of oil, it cannot remove it entirely. Multiple layers of filtration, such as pre-filters, high-efficiency coalescing filters, and activated carbon filters, are effective in substantially reducing oil presence but cannot guarantee complete oil-free air.
However, these filters are not without their own set of challenges. Coalescing filters, for instance, fail to eliminate fine oil vapors above 20°C, which leaves minute oil aerosol particles in the air. Moreover, activated carbon filters lose their efficacy at filtration temperatures above 40°C, as the carbon absorbs the oil vapor, becomes saturated, and, consequently, is ineffective. Besides, the disposal of used filters is another conundrum to consider, as improper disposal may lead to environmental contamination.
Regardless of this environmental concern, numerous industrial sectors require completely oil-free compressed air. Examples include the food and beverage, pharmaceuticals, electronics, automotive painting, textiles, paper, and cosmetics industries. These sectors require a wide operating temperature range of 0-45°C, air purity standards surpassing ISO 8573-Class I, elevated safety levels, environmentally friendly operation, and more. The most advanced filtration technology currently available cannot meet such demanding air purity standards.
Introduction of oil-free screw air compressors
Screw air compressors are positive displacement machines that use two intermeshing rotors to compress air. As air enters the compressor, it gets trapped between the rotors' lobes and is progressively compressed as the rotors rotate. Traditionally, these compressors rely on oil for lubrication and cooling, which helps reduce friction, dissipate heat, and provide an airtight seal. However, the presence of oil in the compressed air can lead to contamination issues in specific industries, impacting product quality and compromising processes. This has led to the development of oil-free screw compressors, which operate without lubricating oil in the compression chamber, ensuring clean and high-quality compressed air output. Despite their numerous benefits, oil-free screw air compressors were not without technological and manufacturing hurdles, particularly concerning overheating issues due to the lack of lubricating oil in the compressor chamber. Additionally, filtration was necessary, as hydrocarbons and other impurities from the surrounding air needed removal before the air's point of use. These challenges dampened their widespread adoption. However, these issues spurred a new development: the injection of oil into the compression cavities to aid in sealing and providing a cooling effect for the heat generated during compression. In these so-called 'oil-flooded' rotary screw compressors, the oil was separated from the compressed air, cooled, filtered, and recirculated. The injected oil served a dual purpose, lowering the compression temperature and trapping external particulates from the incoming air, thereby effectively reducing the burden on the subsequent air filtration process. As these innovations mitigated the initial problems faced by oil-free compressors, there was a shift towards oil-flooded compressors, which consequently increased in popularity.
Yet, the demand for a genuinely oil-free compressor persisted, especially in industries where even the slightest oil presence in the processed air could have disastrous consequences. For example, microscopic oil particles could seriously damage precision electronic circuits or critical semiconductor components. Traces of lubricating oil in processed food and beverages could pose severe health risks. Pharmaceutical applications also require immaculately clean air. The same goes for paper mills, textiles, high-gloss automotive painting, and several other sectors.
While Western countries had rigorous regulations governing air purity for these critical applications, countries in Asia, including India and China, had more lenient rules. However, it was only a matter of time before these countries also adhered to stricter regulations. Even though industries continued to utilize filtration to eliminate trapped oil, the complexity and cost of filtration equipment, the resulting air pressure drops, and the inability to ensure 100% oil-free air remained issues. This scenario presented a significant opportunity for a company like ELGi.
The Evolution and Features of ELGi's Oil-Free Screw Air Compressor
ELGi set out to innovate the oil-free screw air compressor, eliminating the necessity for oil as a medium for heat dissipation during compression. By early 2005, the initial prototype had been assembled and tested. By the beginning of 2008, a test compressor was installed at a user facility for validation, and by the following year, five more were set up at various locations. These models underwent 10,000 hours of validation, and regular sales commenced by early 2011.
Today, ELGi's proprietary oil-free technology, equipped with an inter-cooler, has proven its effectiveness in demanding industrial applications with over 150,000 cumulative hours of operation. The fully-packaged ELGi-NE series features models with high volumetric efficiency, delivering from 500 to 1800 cubic feet per minute (cfm) and pressures of up to 10 bars (kg/cm2). These models meet superior safety standards and are designed to minimize energy loss and air outlet temperatures. Moreover, they're energy-efficient and compact. ELGi's oil-free air compressors utilize two-stage compression with external water jacket inter-cooling and a unique eta-V profile rotor, enabling high swept volume, low operating noise, and reduced vibration, accomplished by combining radial roller bearings with 4-point axially loaded ball bearings.
Several innovative features contribute to their performance: carbon-impregnated stainless steel air seals, helical grooved non-contact bronze oil seals, high-performance Visco-seals at the suction and discharge rotor ends, a clever method of PTFE and PFA (Teflon) dry lubricant coating on carbon steel rotors, an efficient helix-angled timing gear, robustly designed cupro-nickel intercooler and aftercooler, heat exchangers that offer superior corrosion resistance, and optimally designed capacity control valves. These elements ensure high efficiency, safety, durability, easy maintenance, and low operating cost.
Compression efficiency is significantly enhanced due to the precise clearances between the helical rotors and the compression chamber, a testament to the unique eta-V profiles designed by ELGi. This rotor design reduces pressure losses and increases stage efficiencies, leading to a comprehensive increase in adiabatic efficiency.
ELGi's Innovations in Oil-Free Screw Compressor Technology
Only a select few companies worldwide can design oil-free screw compressors. Components such as capacity control valves, air-end bearings, timing gears, and the air-end stage gear are all lubricated with oil.
Therefore, despite the absence of lubricating oil in the rotors and the screw chamber, the machine still features an oil circuit, which includes the oil pump, cooler, filter, and oil sump. In addition, a water circuit provides cooling water to the intercooler, aftercooler, and the 1st and 2nd stage air-ends.
This project has been a fruitful journey for ELGi. According to industry observers, ELGi is one of only five global corporate entities capable of designing and manufacturing oil-free air-ends. This is a testament to our innovative prowess in this challenging domain.
RELATED BLOGS
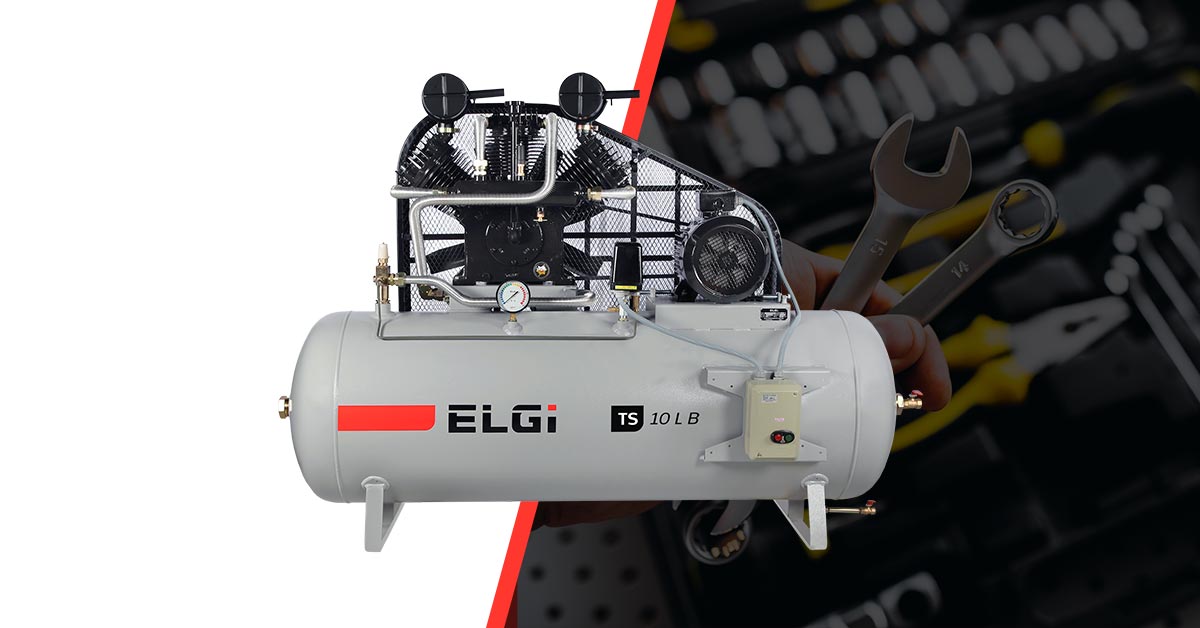
A reciprocating air compressor, also known as a piston compressor, is a positive di...
Read More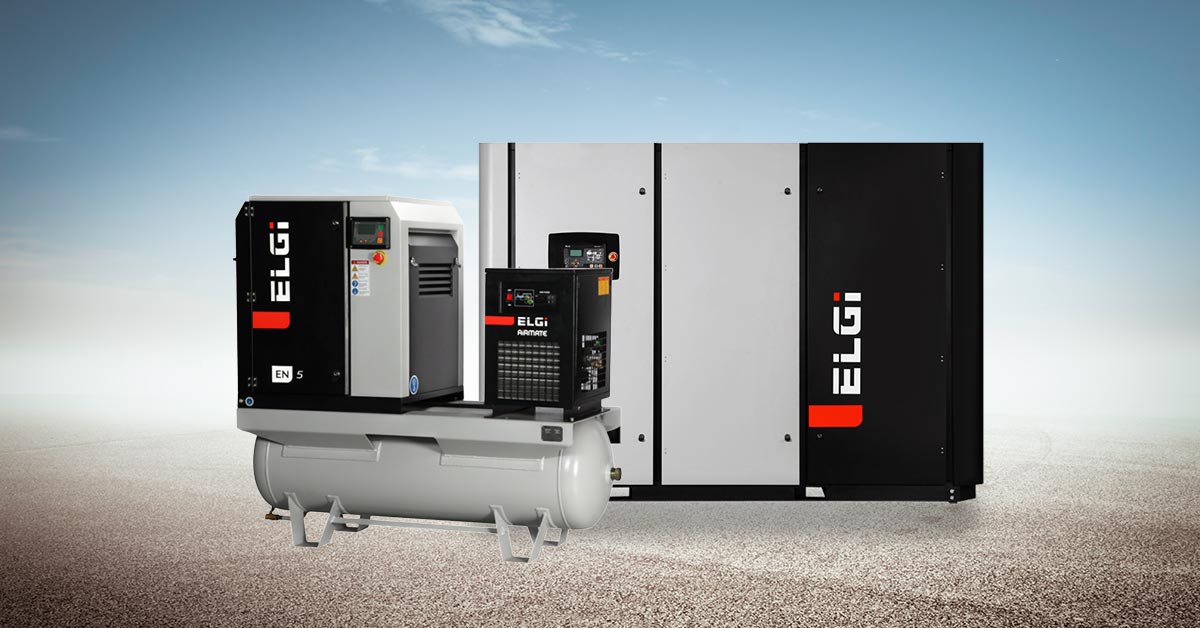
Rotary screw air compressors are a popular choice for industrial applications due t...
Read MoreDiesel vs. Electric Portable Air Compressors. The power source affects the maintena...
Read More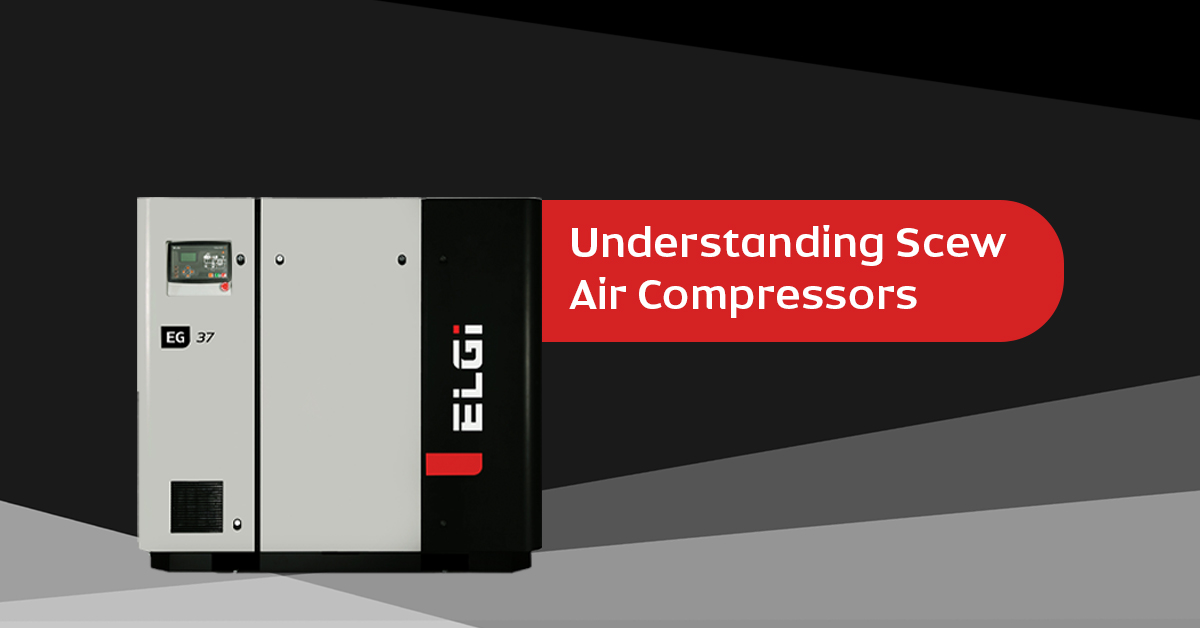
When selecting a suitable air compressor for your business, a few fac...
Read More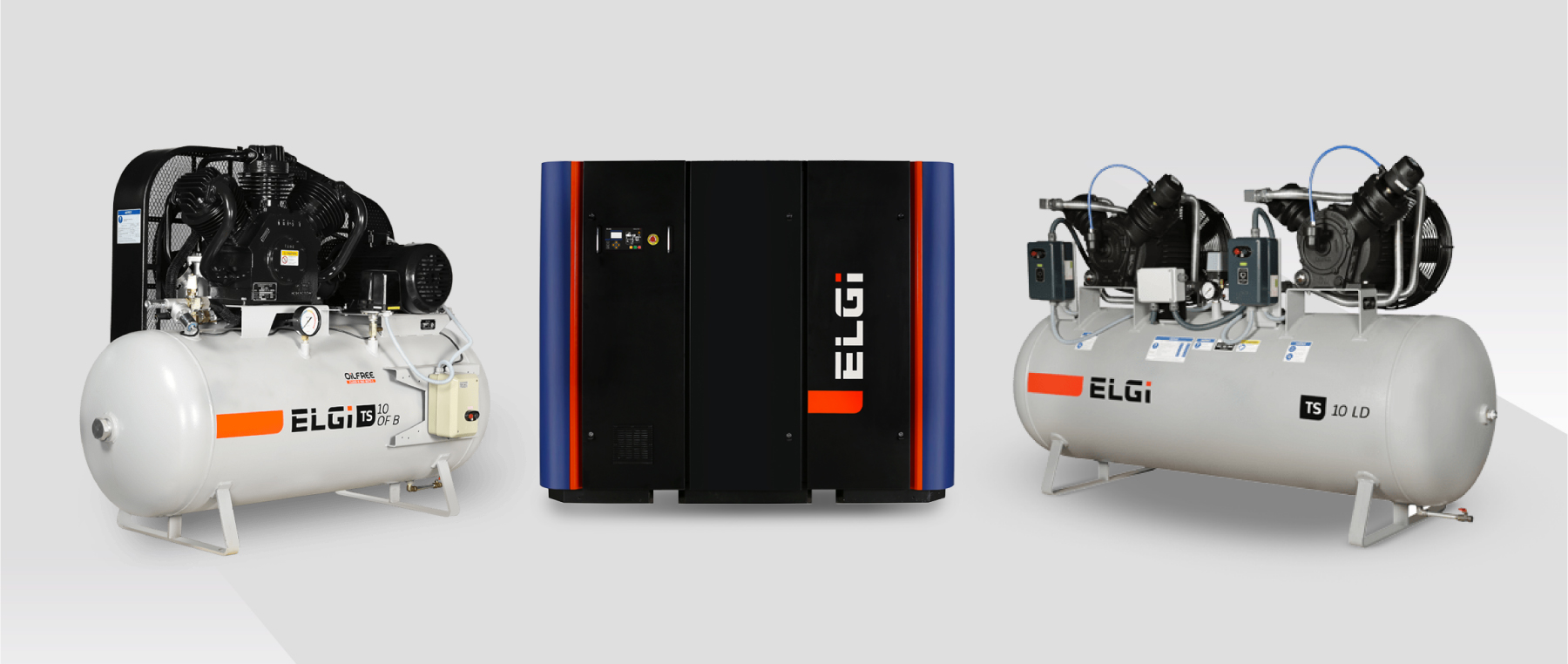
Rotary screw compressors and reciprocating compressors are the two mo...
Read More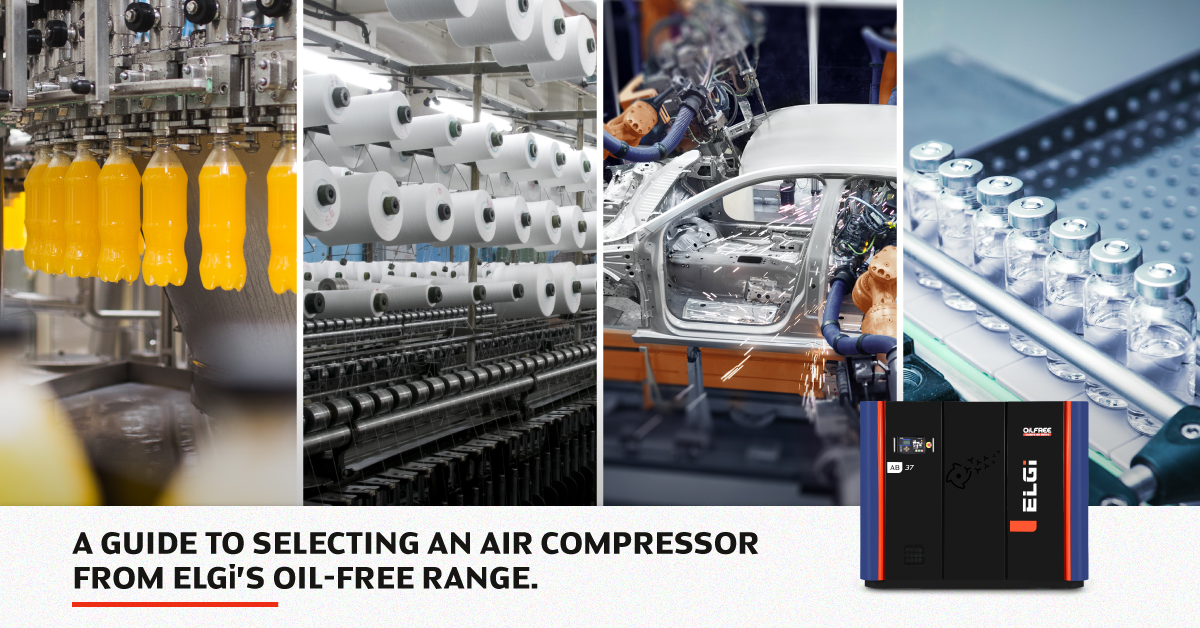
ELGi has been delivering an extensive range of compressed air s...
Read More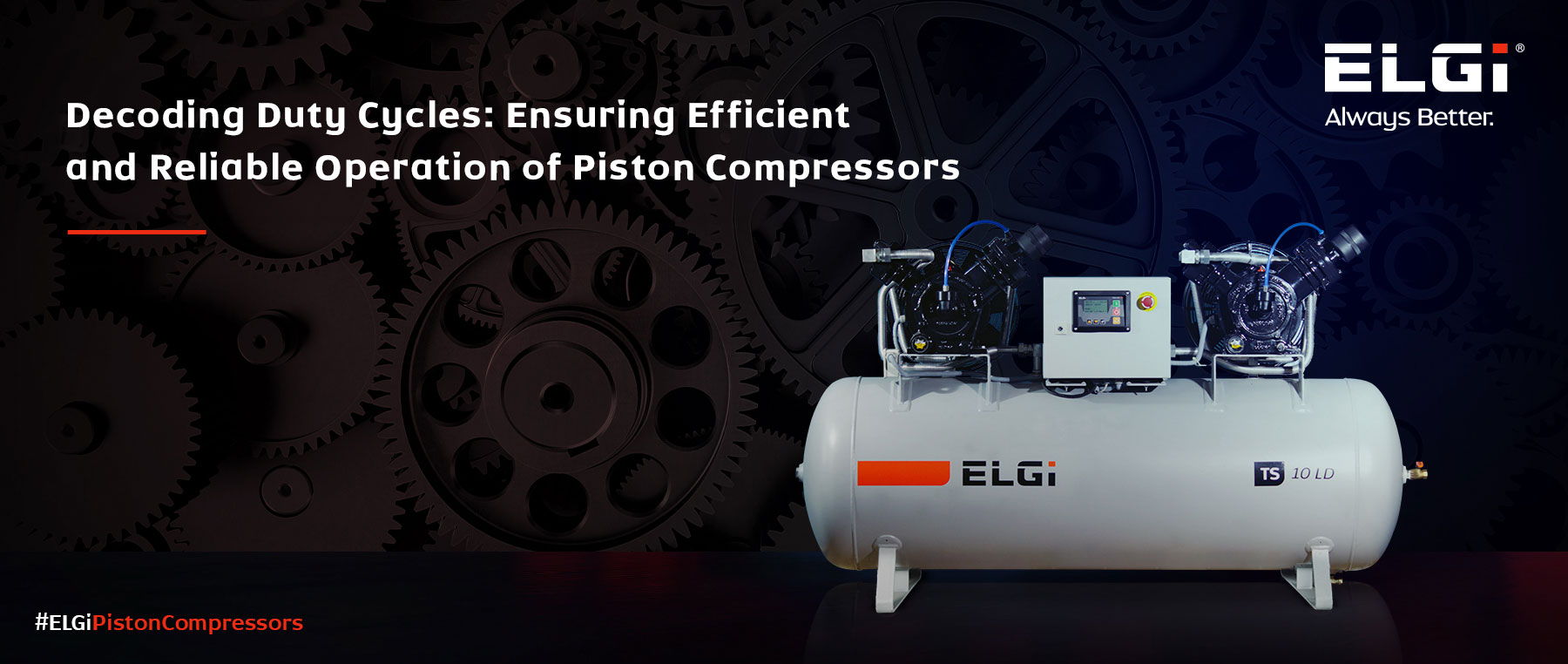
The duty cycle of piston compressors is a critical aspect to understand for an effi...
Read More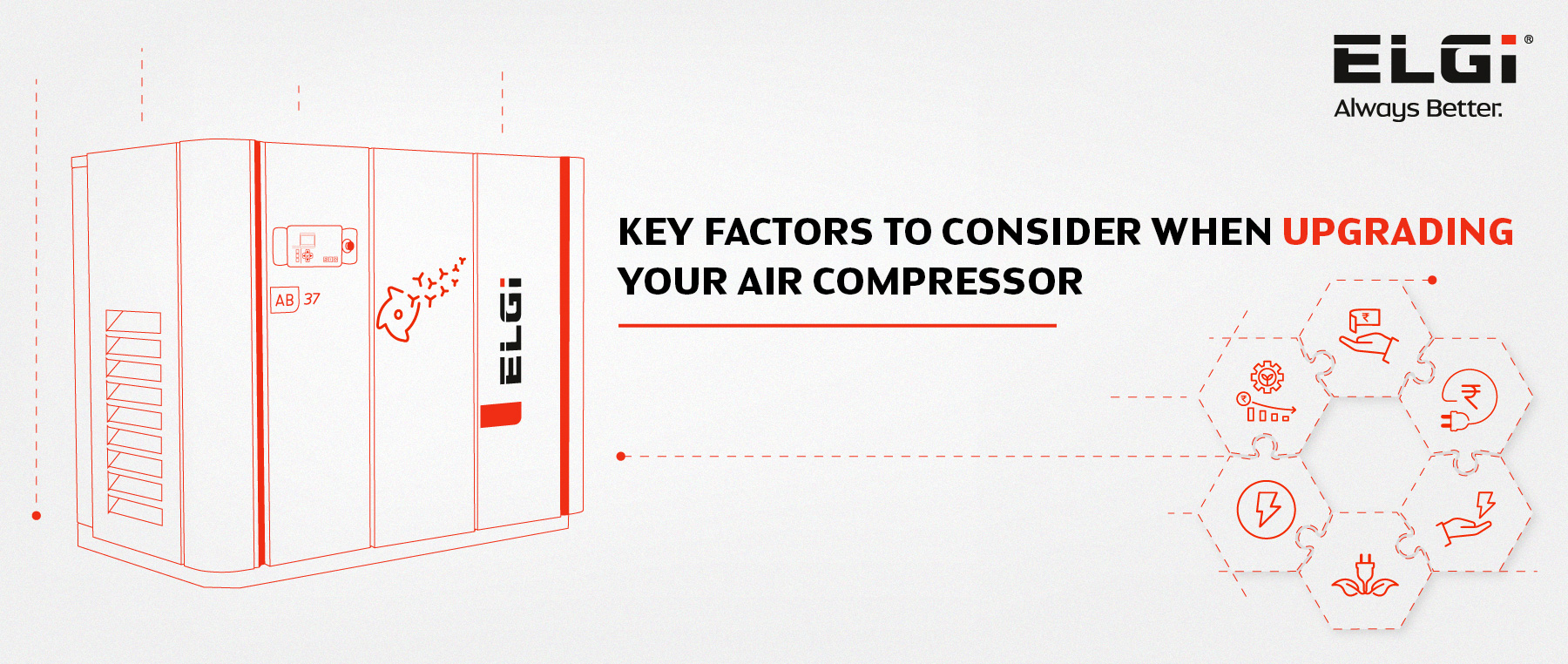
Upgrading your air compressor is a critical decision that can significantly impact ...
Read More