Decoding Duty Cycles: Ensuring Efficient and Reliable Operation of Piston Compressors
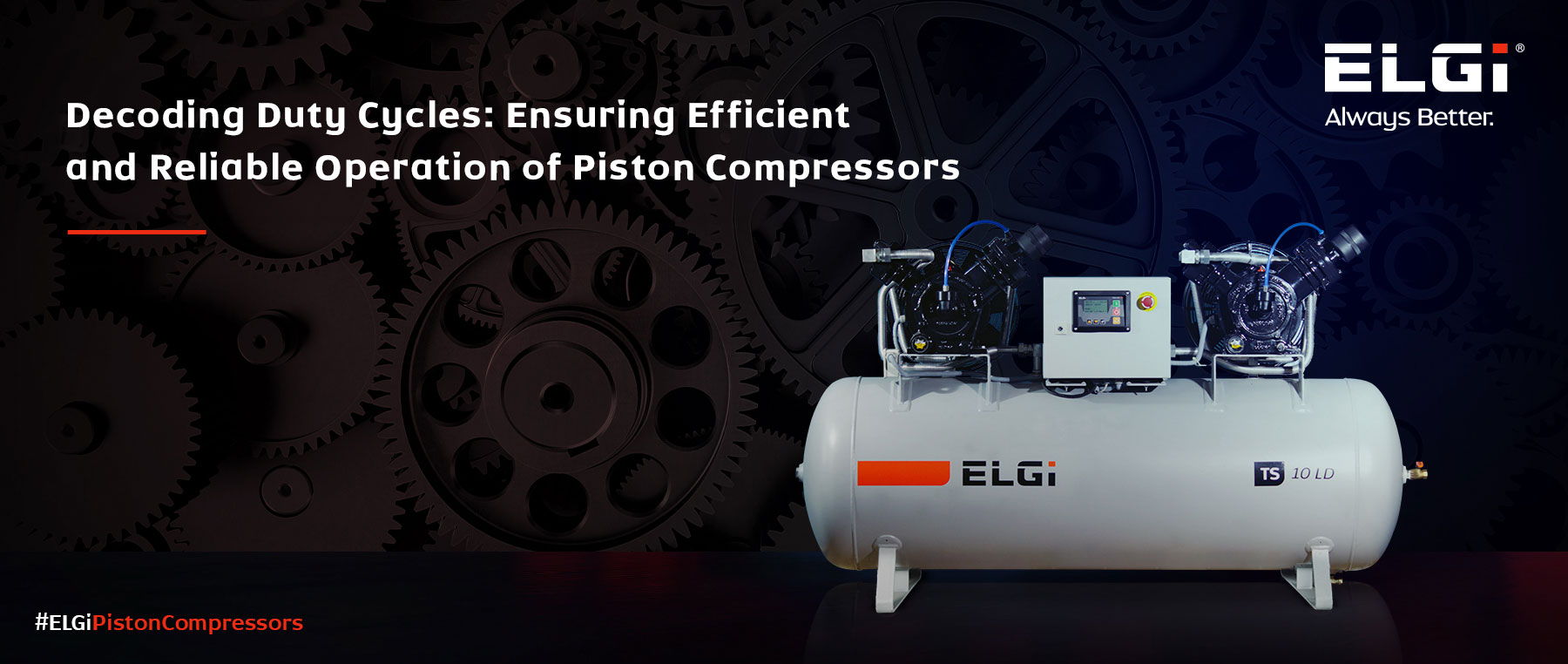
The duty cycle of piston compressors is a critical aspect to understand for an efficient and reliable operation.
Contrary to rotary compressors, which are built for continuous operation without the risk of damage from overheating, piston compressors have limitations due to their design that includes many moving parts, along with a rudimentary cooling and lubrication system. Therefore, piston compressors come with a specified operational duration to prevent wear and tear to the machine, unlike their rotary counterparts which can function continuously without issue.
Understanding Piston Compressors
Understanding how a piston compressor functions is crucial for comprehending its duty cycle. Piston compressors are widely used in applications such as industrial processes, air tools, and refrigeration systems. These compressors operate based on the principle of reciprocating motion, where a piston inside a cylinder compresses air or gas. The key components of a piston compressor include the cylinder, piston, valves, and motor. When the piston moves downward, it creates a vacuum, drawing in air or gas. On the upward stroke, the piston compresses the air or gas, increasing its pressure. This compressed air or gas is then discharged through the valves.
What is Duty Cycle?
Duty cycle refers to the operating time of a compressor compared to its resting or cooling-off time. It is typically expressed as a percentage and represents the compressor's running time ratio to the total cycle time. For example, a duty cycle of 50% means that the compressor operates for 50% of the total cycle time and rests for the remaining 50%.
Duty cycle is an essential parameter to consider as it indicates the compressor's capacity to sustain continuous operation without overheating or experiencing premature wear. It helps users assess the compressor's suitability for specific applications and prevents potential damage due to excessive usage. Understanding the duty cycle of a piston compressor helps you make informed decisions about how to operate and maintain it effectively.
Factors Affecting Duty Cycle
Several factors influence the duty cycle of a piston compressor. Firstly, the design of the compressor plays a significant role. Compressors built for continuous operations typically have sturdier components and better cooling mechanisms, allowing them to sustain higher-duty cycles. On the other hand, compressors designed for intermittent usage have lower duty cycle capabilities.
Operating conditions also affect the duty cycle. Higher ambient temperatures can reduce the compressor's cooling efficiency, leading to a lower duty cycle. Similarly, operating at higher pressures or under heavy load demands can increase the compressor's duty cycle.
Considering the intended application and usage is crucial when determining the duty cycle requirements. Applications with constant and heavy air demand, such as manufacturing processes, may require compressors with higher-duty cycles. Conversely, applications with sporadic or light air usage may require compressors with lower-duty cycles.
Also, regular maintenance, including proper lubrication and cleaning of filters, helps ensure optimal compressor performance and extends its duty cycle. Overlooking maintenance can lead to increased friction, reduced efficiency, and a shorter duty cycle.
Interpreting Duty Cycle Ratings
Manufacturers provide duty cycle ratings to help users understand the compressor's capabilities and limitations. These ratings are usually expressed as a percentage, such as 50%, 75%, or 100%. It's important to note that a 100% duty cycle rating doesn't imply continuous operation; rather, it indicates that the compressor is designed for longer periods of continuous usage compared to lower duty cycle rated models.
A compressor with a 50% duty cycle rating means it can operate for half the cycle time and needs equal resting time. This rating is suitable for applications with intermittent air demand, allowing the compressor to cool down adequately during resting periods.
Compressors with higher duty cycle ratings, such as 75% or 100%, can handle more extended periods of continuous operation before requiring rest. These models are better suited for applications with continuous or high air demand, such as industrial processes.
It's important to understand the duty cycle rating of a compressor and match it with the intended application. Exceeding the recommended duty cycle can lead to overheating, increased wear and tear, and potential compressor failure.
Each brand has its own recommended duty cycles based on their design standards. ELGi, for instance, suggests a 70:30 duty cycle as the ideal choice for their piston compressors.
Determining the Right Duty Cycle for Your Application
Consider the expected usage patterns and operating conditions to determine the suitable duty cycle for your application. Evaluate the air demand and duration of usage in your specific application. A lower duty cycle compressor may suffice if your application involves intermittent usage, such as inflating tires or occasional air tool operation. However, if you anticipate continuous or prolonged air demand, such as running air-powered machinery or industrial processes, in that case, it is advisable to choose a compressor with a higher duty cycle rating.
Additionally, assess the operating conditions in your environment. If you operate in a hot climate or in a confined space with limited ventilation, it may be necessary to select a compressor with a higher duty cycle rating to compensate for reduced cooling efficiency.
Consulting the OEM's recommendations and guidelines specific to your chosen compressor model can provide valuable insights into the suitable duty cycle for your application. It's important to avoid pushing the compressor beyond its rated duty cycle to prevent performance degradation, premature wear, and potential breakdowns.
Effects of running at 100% Duty Cycle
Running a piston compressor at a 100% duty cycle can result in several detrimental effects, including:
- Increased risk of piston seizure within the housing of piston due to excessive heat in the cylinder.
- Valves may expand and become jammed when continuously exposed to higher temperatures, potentially leading to catastrophic compressor failure.
- Changes in oil properties can occur, leading to increased oil carryover.
- Continuous exposure to higher temperatures can cause greater condensate formation in the receiver tank, resulting in increased moisture carryover to downstream equipment and end devices.
- The accelerated wear and tear of internal components leads to higher maintenance costs.
Benefits of Understanding Duty Cycle
Understanding the duty cycle of piston compressors offers several benefits. Compressors designed for the intended duty cycle can handle the expected air demand without overheating or experiencing excessive wear, resulting in improved performance and longevity.
Moreover, matching the duty cycle to your application prevents unnecessary downtime and maintenance. When a compressor operates within its recommended duty cycle, it requires adequate resting time for cooling, lubrication, and internal component relaxation. This helps maintain optimal performance, reduces the risk of breakdowns, and minimizes the need for frequent repairs or premature component replacements.
However, it's essential to be aware of the limitations as well. Duty cycle alone cannot determine a compressor's overall quality or suitability for a specific task. Other factors such as build quality, motor power, and reliability also play significant roles in determining a compressor's performance. Therefore, it's crucial to consider duty cycle in conjunction with other specifications when selecting a compressor for your application.
Maintenance and Care for Optimal Duty Cycle Performance
Regularly inspecting and maintaining your compressor can help prevent issues and extend its duty cycle. Here are some key maintenance practices to consider:
- Regularly check and change the compressor's air filters to prevent dust and debris from entering the system, which can reduce efficiency and increase operating temperature.
- Keep the compressor clean and free from dirt, oil, and debris that may accumulate on the external surfaces and cooling fins. This helps maintain proper heat dissipation.
- Ensure adequate lubrication of the compressor's moving parts, following the manufacturer's recommendations. Proper lubrication reduces friction, minimizes wear, and contributes to optimal performance.
- Monitor the compressor's operating conditions, such as discharge pressure, temperature, and motor performance. Unusual or fluctuating values may indicate issues that require prompt attention.
- Regularly inspect the compressor's belts, hoses, and fittings for any signs of wear, leaks, or damage. Replace or repair damaged components promptly to prevent potential failures.
- Consider installing an automatic drain valve in the compressor's air tank to prevent moisture buildup, which can lead to corrosion and reduced efficiency.
By implementing these maintenance practices and adhering to the guidelines provided by the manufacturer, you can enhance your compressor's duty cycle performance.
By deciphering the duty cycle and considering its various factors, users can select an appropriate compressor for their application and prevent potential issues such as overheating or premature wear. Furthermore, proper maintenance and care plays a crucial role in enhancing duty cycle performance and prolonging the lifespan of the compressor.
RELATED BLOGS
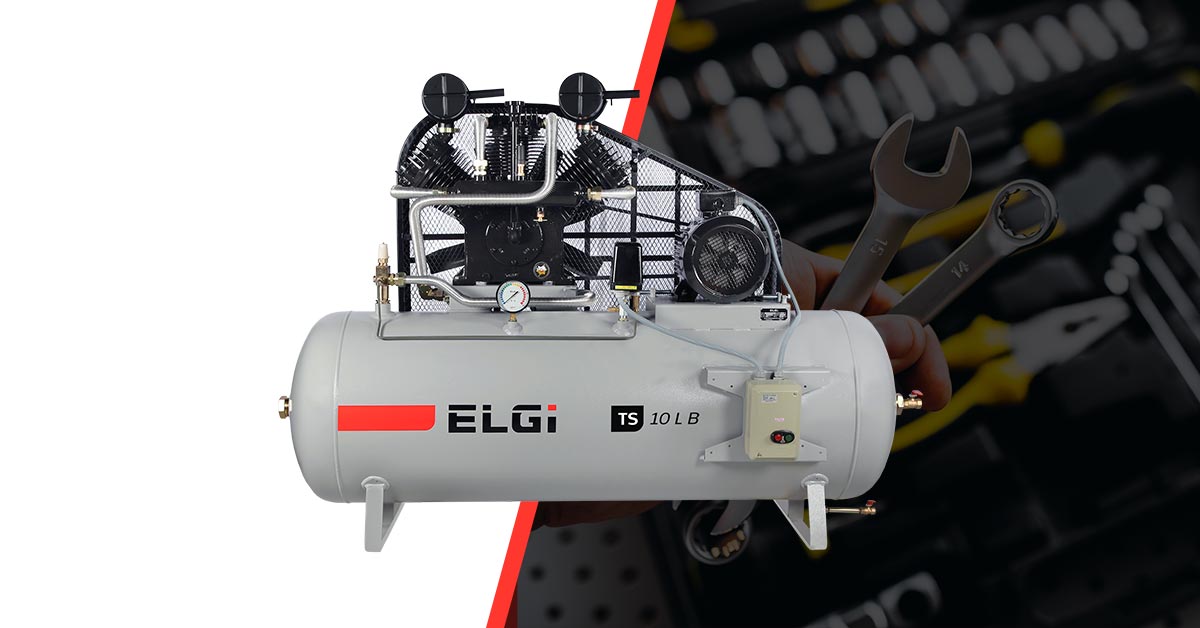
A reciprocating air compressor, also known as a piston compressor, is a positive di...
Read More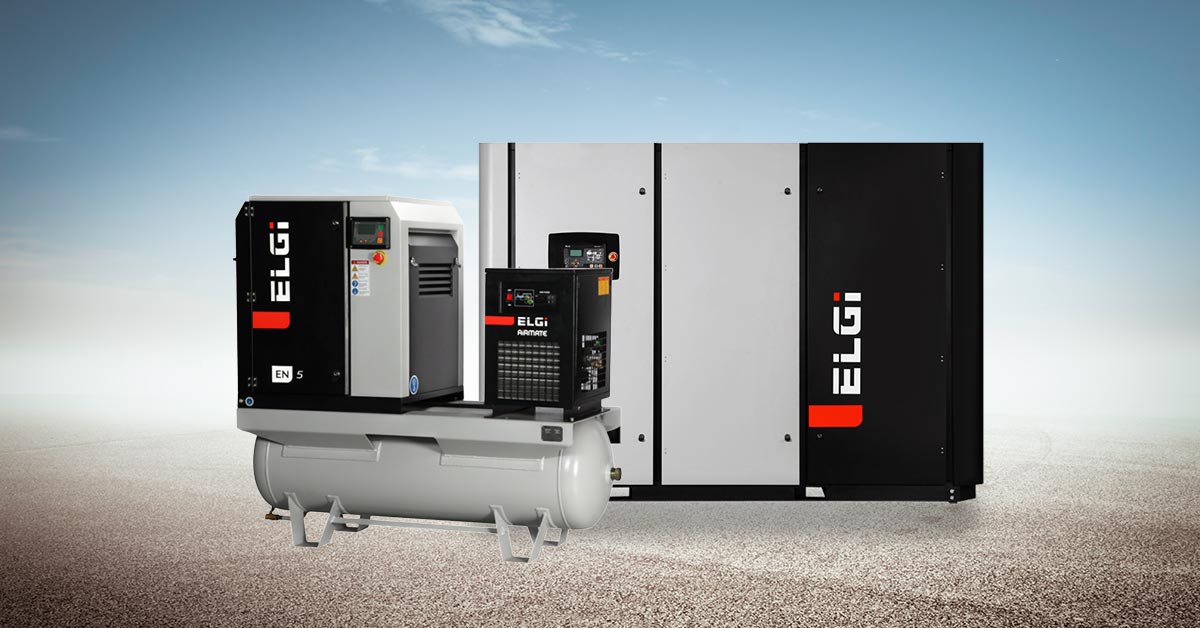
Rotary screw air compressors are a popular choice for industrial applications due t...
Read MoreDiesel vs. Electric Portable Air Compressors. The power source affects the maintena...
Read More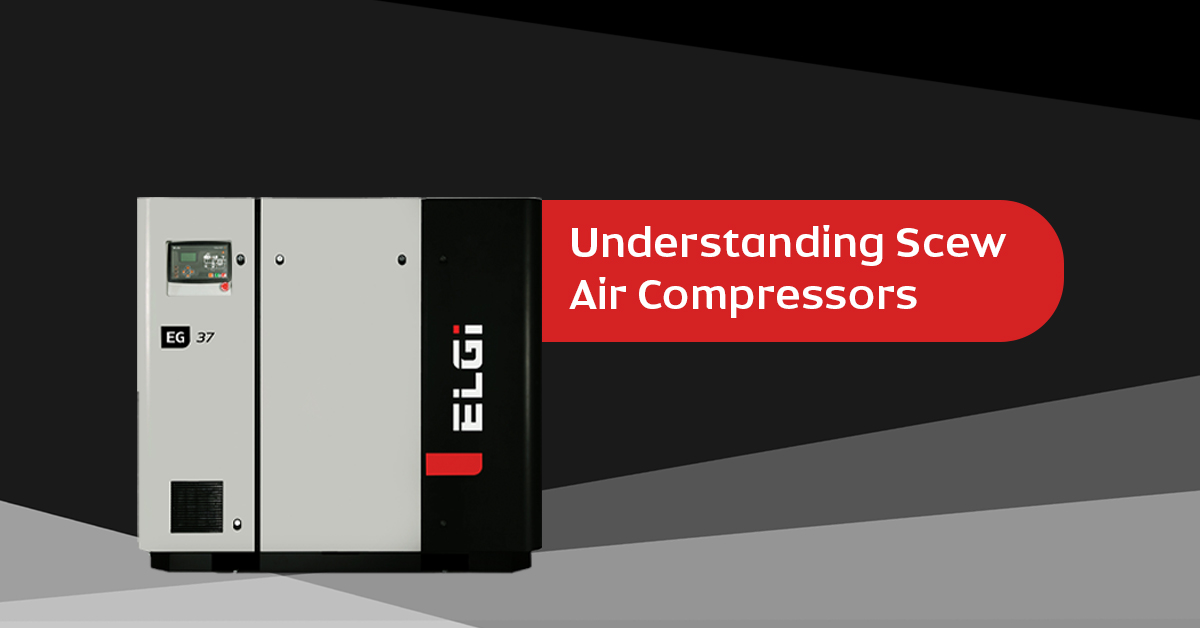
When selecting a suitable air compressor for your business, a few fac...
Read More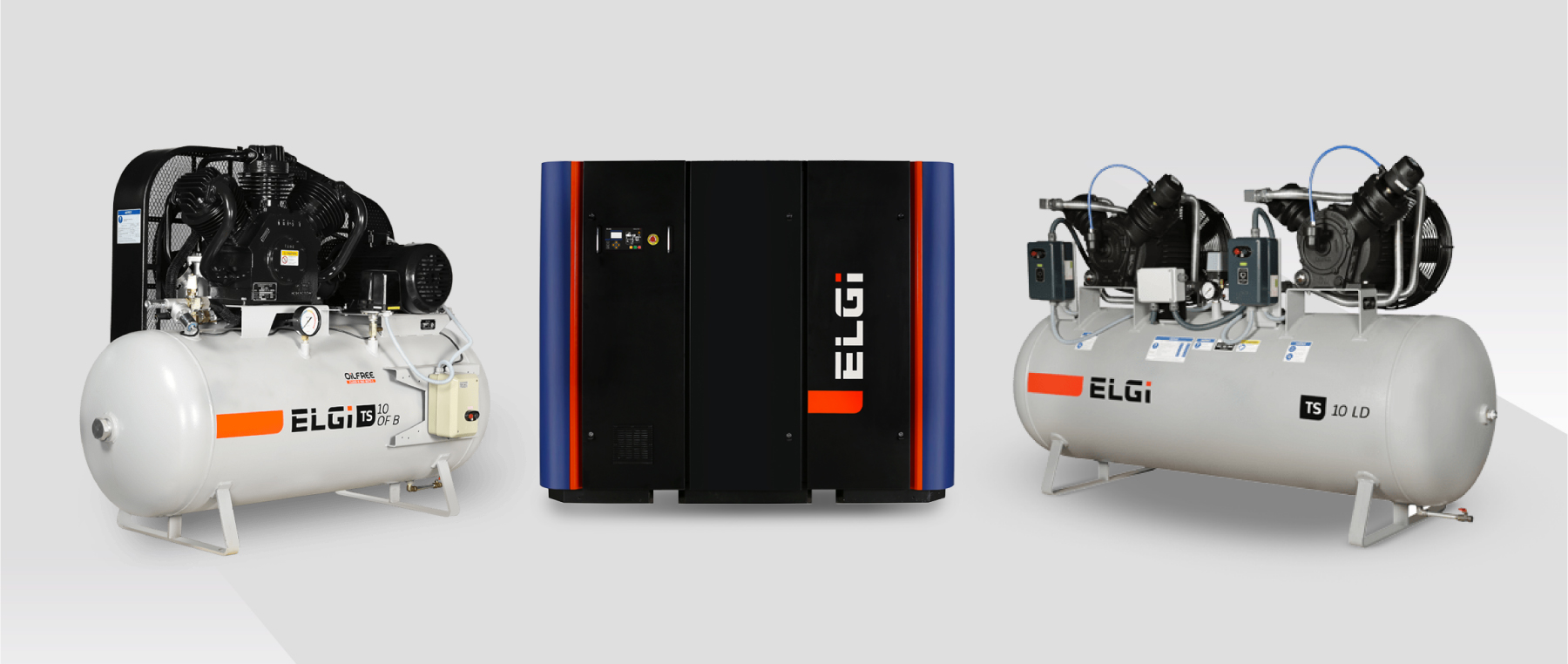
Rotary screw compressors and reciprocating compressors are the two mo...
Read More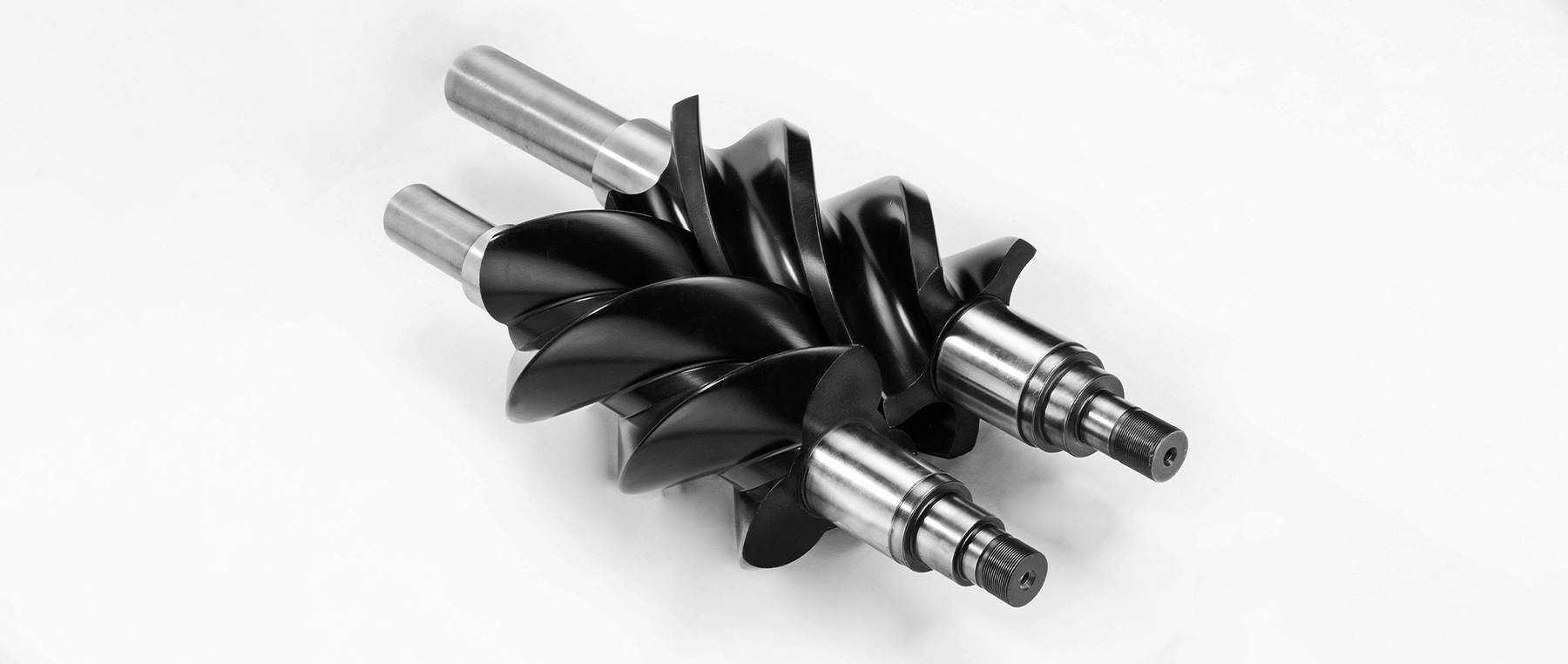
The concept of air compressors dates back thousands of years. The...
Read More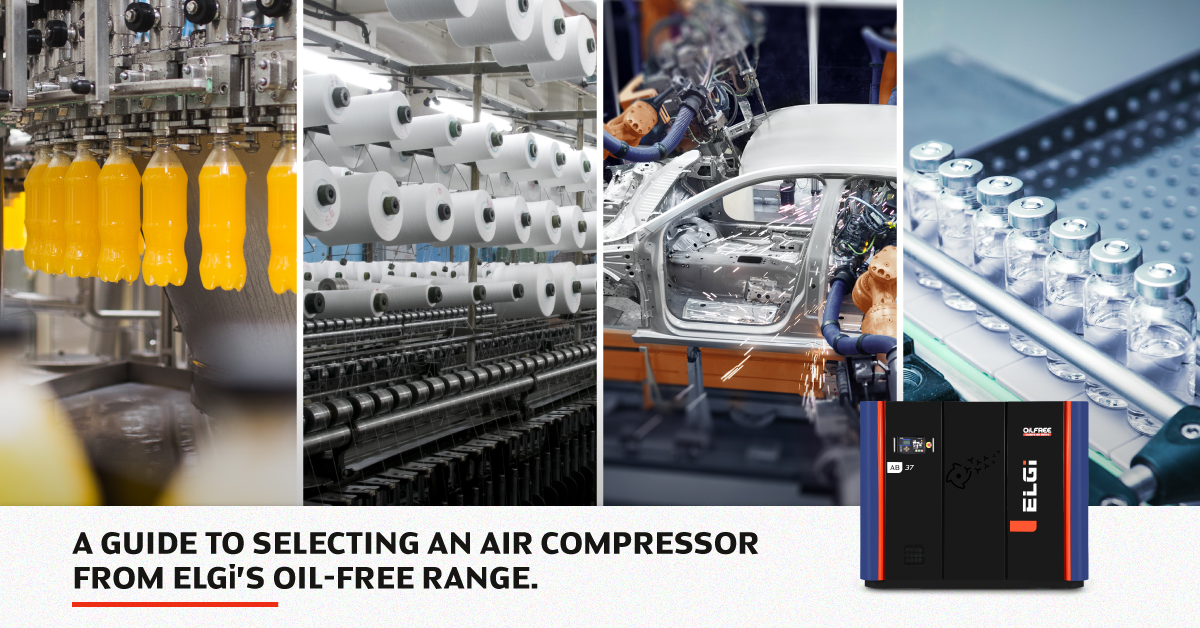
ELGi has been delivering an extensive range of compressed air s...
Read More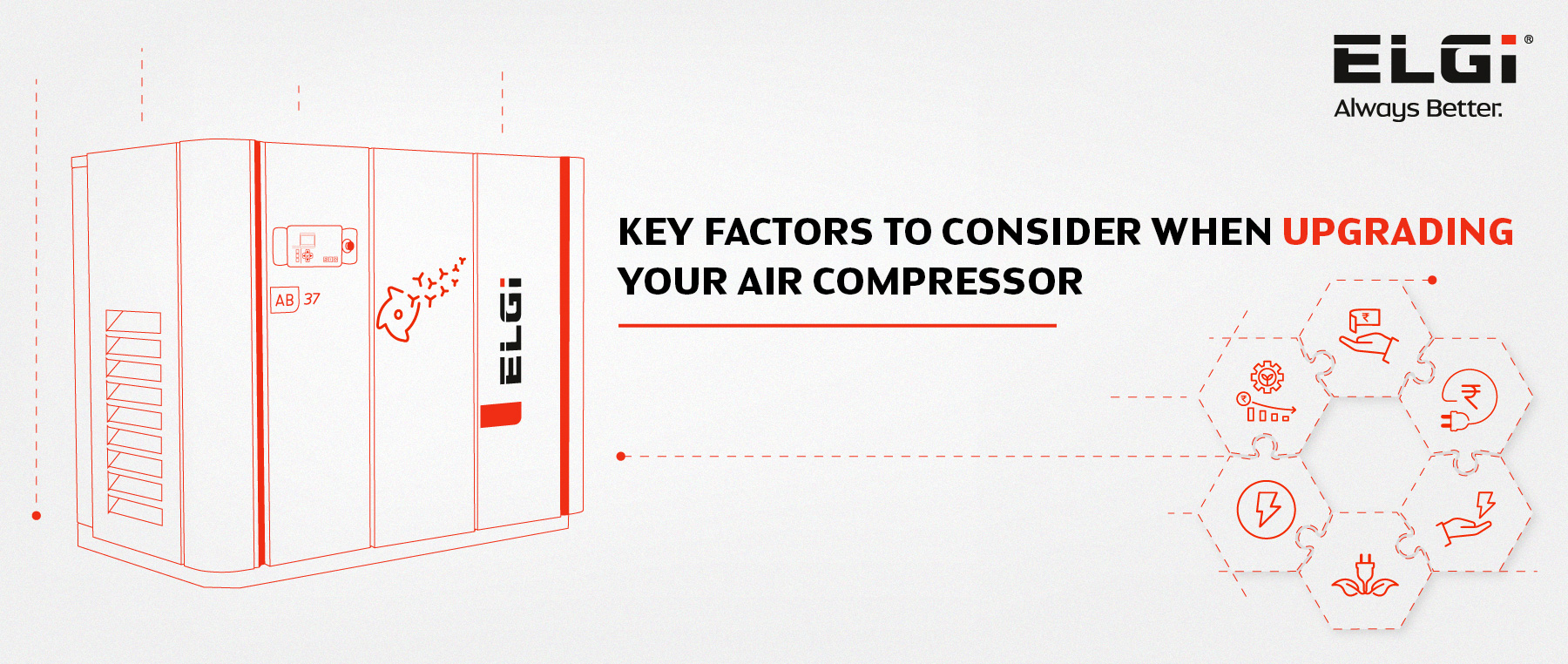
Upgrading your air compressor is a critical decision that can significantly impact ...
Read More