What is the best way to choose the appropriate compressor for your water well?
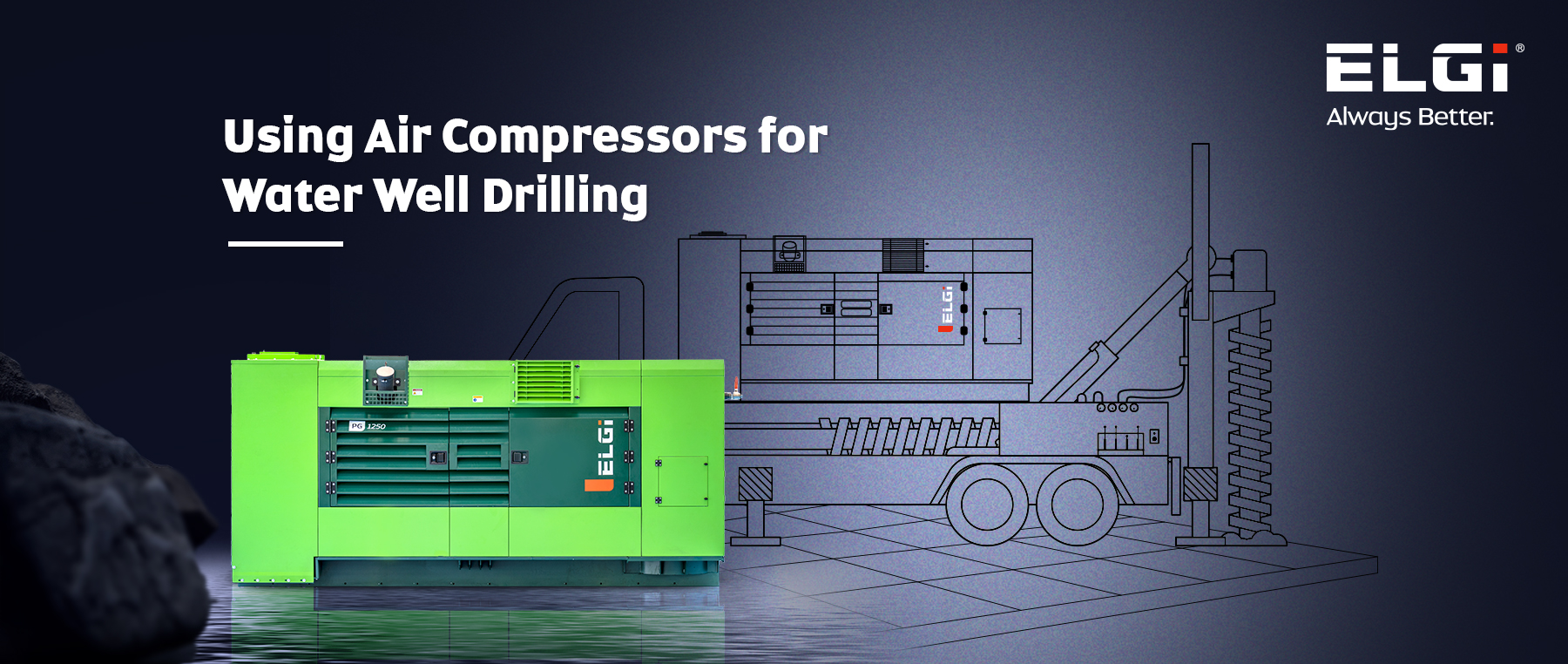
Water well drilling is a process for accessing underground water sources. Drilling a well requires efficient and effective techniques for residential, commercial, or agricultural purposes. One such method involves air compressors, which play a vital role in drilling.
ELGi manufactures durable and high-performance compressors to meet the specific needs of water well drilling operations. These compressors are designed to work seamlessly with water well rigs and are accompanied by essential accessories such as drilling rods, casing pipes, and a hammer. Adopting DTH drilling is standard practice when drilling for deeper water wells. This method efficiently penetrates medium to complex formations, providing impactful hammering directly at the bottom of the hole, ensuring effective drilling.
Compressed Air for Water Well Drilling
The primary function of an air compressor is to compress air, which is then released under pressure to operate the drilling equipment effectively. A typical air compressor system in drilling includes the compressor unit, receiver tank, pressure gauges, hoses, and drilling tools like hammers and bits.
Air compressors are essential for drilling. Compressed air breaks up rock or soil formations by creating a percussive action through the drilling tool. The air also carries cuttings to the surface through the annular space between the drill pipe and borehole walls, ensuring continuous clearing and stability during drilling.
Air-powered drilling offers advantages like faster speeds, increased efficiency, and suitability for various geological formations. It also minimizes water contamination and cuttings formation, making it ideal for environmentally sensitive areas.
Stages of Water Well Drilling Operation
In a standard water well drilling process, the procedure generally involves the following phases:
- Firstly, a substantial hole, varying between 20-200 feet, is bored into the ground using the Over Burden hammer. This drilling step establishes the casing pipe, forming a structural wall for the well.
- The purpose of this initial drilling activity is to remove the top layer of the earth's crust, which helps in preventing any unwanted materials from collapsing into the well.
- Subsequently, the actual size hole is drilled to access the water resource. In the current scenario for India, the typical well depth spans from 800 to 1200 feet, influenced by the regional water table levels.
Preparing for Water Well Drilling with Air Compressors
Before commencing water well drilling with air compressors, thorough preparation is essential. Here are some key steps to consider:
a) Site Assessment and Planning:
Conduct a comprehensive assessment of the drilling site to determine the geological conditions, potential obstacles, and environmental considerations. This information will help determine the required drilling techniques, tools, and equipment.
b) Equipment and Tool Selection:
Determine the suitable equipment by considering factors like the depth of the well, formation hardness, and anticipated flow rate based on the site assessment and specific drilling requirements. Choose the appropriate air compressor, drilling rig, tools, and accessories accordingly.
c) Site Preparation:
Enhance the efficiency and effectiveness of the drilling process by adequately preparing the drilling site, and clearing any vegetation or debris that could impede the drilling. Additionally, establish a safe and easily accessible area for the drilling rig, air compressor, and related equipment to ensure a smooth drilling operation while minimizing potential setbacks through adequate planning and preparation.
Water Well Drilling Process with Air Compressors
There are two pivotal stages involved in the operation of water well compressors.
1. Drilling Stage: During this phase, compressed air is utilized at the necessary pressure to ensure efficient performance of the drilling hammer. This stage constitutes approximately 75-80% of the total drilling cycle, making the compressor's performance crucial to the profit margins of the drilling rig owner. ELGi's compressors are designed to deliver the required volume of compressed air to guarantee optimal drilling results.
2. Flushing Stage: This stage involves the use of maximum compressed air flow to remove any cuttings or debris from the drilled hole. The flushing stage is critical for the overall fuel consumption of the compressor, as excessive flushing can lead to higher fuel usage. Typically, this stage makes up about 10-15% of the complete drilling cycle.
In addition, there exists an idling state during which the compressor does not deliver any air but stays operational. This state usually coincides with the rig undergoing rod-changing activities.
Remember to select the appropriate air compressor for the specific drilling requirements and follow proper maintenance practices to ensure optimal performance and longevity. With air compressors, you can access clean and reliable groundwater sources, meeting the water needs of various applications.