Factors to consider achieving energy efficiency in compressed air system
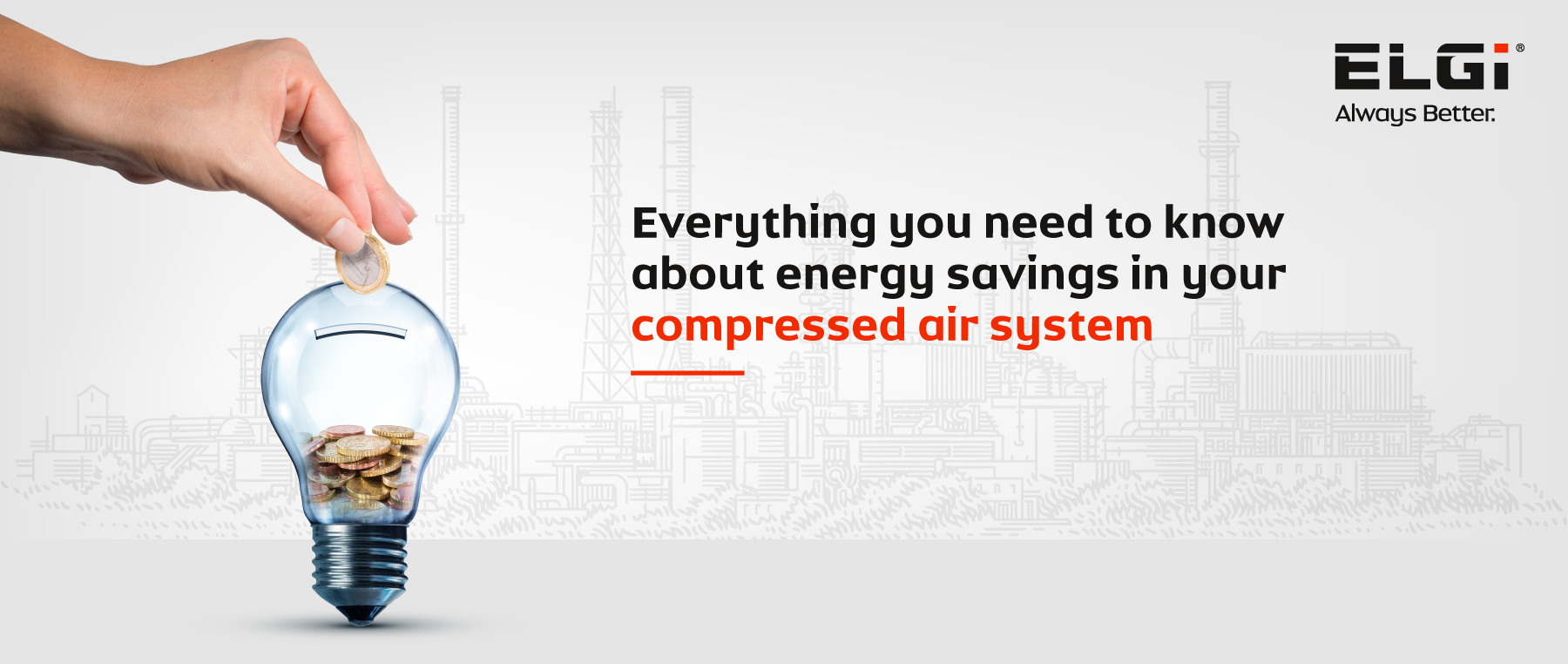
Energy costs contribute significantly to the overall life cycle cost of a compressor, and even modest reductions in compressor energy consumption can lead to substantial savings for the customer.
Organizations can achieve significant energy savings and reduce operational costs by implementing best practices. Businesses can enhance energy efficiency and sustainability by understanding the key components and operation of the systems, assessing their performance, and implementing proven strategies.
Factors influencing energy consumption in compressors
Here are the primary factors influencing a compressor's energy use:
- Compressor Selection and Sizing
- Choice of Air Accessories
- Piping Infrastructure
- Operating Pressure
- Postponed Maintenance
- Created Demand
- Air Leakage
- Coordination of Multiple Compressor Operations
- Heat Generated During Compression
Best Practices for Energy Efficiency
Compressor Selection and Sizing:
Choosing the right type and capacity of the compressor is crucial during the initial plant setup. It's essential to consider selecting the appropriate oil-lubricated or oil-free compressor for optimal energy efficiency. Installing downstream filters to remove oil particles instead of relying solely on an oil-free compressor can help avoid energy loss caused by pressure drop across filters. Additionally, avoiding oversized compressors running in extended unloading conditions can help prevent energy wastage.
Selection of Air Accessories:
Proper selection of accessories for the air compressor plant significantly impacts the energy efficiency of the compressed air system. Careful consideration should be given to the size and type of downstream filters, dryers, and receivers. Inadequate selection can lead to excessive power consumption, hampering the production process. Issues like lower sizing of downstream filters resulting in extreme pressure drop and power consumption, lower sizing of refrigerant dryers causing moisture carryover and production process disruption, higher sizing of desiccant dryers leading to excessive purge loss and power consumption, and undersized storage receivers increasing energy costs on load/unload compressors should be avoided.
Piping Infrastructure:
The design of the piping layout has a long-term impact on the compressed air system's efficiency. Inefficient piping layout designs can lead to excessive pressure drop, increased leakage, and subsequent escalation of energy costs over time. Factors to consider when designing the compressed air piping layout include the choice of piping material (e.g., aluminium or plastic instead of MS/GI pipes), the layout's configuration (looped or non-looped), the number of joints, bends, elbows, and tees, preference for welded or O-ring joints over threaded joints, and determining the appropriate diameter for the main header and sub-headers.
Operating Pressure:
Operating the compressor at a higher pressure than necessary can significantly increase energy consumption. It is advisable to set the compressor load and unload pressures based on the end user's requirements and estimated pressure drop between the compressor and the farthest point of application. Generally, in systems operating at 7 bar pressure, each one-bar increase in operating pressure results in a 7% rise in energy consumption. Thus, optimizing the operating pressure helps minimize energy bills.
Timely Maintenance:
Regular maintenance and timely replacement of consumables, following the recommended maintenance schedule provided by the OEM, are essential for trouble-free operation and efficient compressor performance. Delaying maintenance and neglecting consumable replacements such as air filters, air/oil separator elements, and coolant/lubricant can lead to increased pressure drop across filters, increased energy consumption, and reduced compressor capacity. It's crucial to prioritize maintenance to ensure optimal energy efficiency.
Artificial Demand:
Artificial demand refers to increased compressed air consumption due to operating at higher than necessary pressures. Unregulated compressed air use, leakage, blowing applications, tools, air motors, and pneumatic cylinders consume more compressed air as system pressure increases. Artificial demand can be reduced by lowering the operating pressure and setting the compressor load/unload pressures within the optimum range, aligning with the end user's requirements.
Air Leakage:
Leaks within a compressed air system can significantly impact your operational budget due to increased electricity consumption. These leaks can account for up to 20% of the compressor's total energy cost in manufacturing and processing plants. The primary areas where leaks commonly occur are at connection joints, including valves, unions, couplings, and fittings. Besides the financial implications, leaks can also lead to a drop in system pressure, reducing the efficiency of pneumatic tools or machines reliant on compressed air. For example, an air-operated actuator may struggle to close a valve, potentially resulting in product rejections.
A simple method for estimating the amount of leakage in a system involves turning off all point-of-use devices or pneumatic tools and starting the compressor. The total leakage percentage can be calculated by recording the average time the compressor cycles on and off.
The calculation is as follows: % Percentage = [(T x 100) / (T + t)], where T represents on-time in minutes and t represents off-time in minutes.
Ideally, a properly maintained system should have a leakage percentage of under 10% relative to the compressor's capacity.
Multiple Compressors Operation:
Unmanaged control schemes for multiple compressors can lead to unnecessary power consumption, increased maintenance, and operational issues. Implementing an automatic control system using a compressor controller is crucial, especially for systems with more than three compressors. The controller communicates with all system compressors and selects the most suitable combination based on a control algorithm and operator input. Running compressors within a single pressure band arrangement, incorporating variable speed compressors, and ensuring adequate storage receiver capacity help optimize power consumption and minimize wasted unloaded run time.
Heat Recovery Systems:
During the compression process, all the electrical power is converted to heat energy, which is typically wasted if not utilized. Heat recovery systems offer an opportunity to harness the waste heat generated by compressors. Approximately 96% of the overall electrical energy consumption can be recovered, including heat dissipated in the oil cooler, aftercooler and radiated from the drive motor. By implementing a heat recovery system, around 76% of the waste heat can be effectively used for heating air and water, reducing the need for additional equipment and minimizing CO2 emissions.
In the face of escalating energy expenses, the performance and efficiency of your compressed air systems have never held more significance. ELGi's Air audit offers a valuable solution for users to uncover potential avenues for energy conservation within their compressed air system, consequently reducing overall operational costs. Our comprehensive Audit Report meticulously identifies opportunities for energy savings, ranging from significant to moderate and minor, while providing actionable recommendations for short-term, medium-term, and long-term energy conservation measures. The report further includes a thorough financial analysis, estimating the costs and benefits of implementing these measures. By employing a wide array of advanced, portable diagnostic and measuring instruments, the audit process generates precise data, facilitating detailed analysis and yielding a more dependable foundation for identifying energy-saving prospects, evaluating performance, and assessing economic feasibility. Additionally, ELGi's Air audit bestows customers with the added advantage of reducing wear and tear and maintenance expenses over the entire lifespan of the compressed air system.