The Critical Role of Compressed Air Quality in the Pharmaceutical Industry
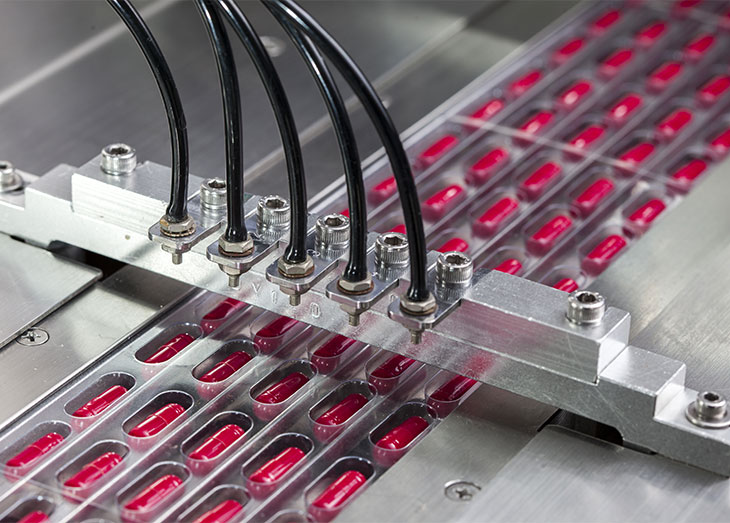
The global pharmaceutical sector is renowned for its stringent regulations and high standards. Every pharmaceutical compa ny adheres to strict guidelines, such as Good Manufacturing Practice (GMP), the European Pharmacopoeia, Food and Drug Administration (FDA), or International Council for Harmoniza tion of Technical Requirements for Pharmaceuticals for Human Use (ICH). These regulations ensure the quality, safety, and efficacy of pharmaceutical products.
In 2021, India’s domestic pharmaceutical market experienced remarkable growth, with an annual rate of 17.7 percent, sur passing the 13.7 percent recorded in July 2020. The Indian pharmaceutical industry is projected to expand its market size to USD 65 billion by 2024, a substantial increase from its val uation of USD 42 billion in July 2022. This exponential growth positions India as a prominent player in the global pharmaceu tical market.
Moreover, the Indian pharmaceutical sector has made signifi cant contributions during the COVID-19 pandemic by offering cost-effective global healthcare solutions during health emer gencies. This track record of success has led to the anticipa tion that the pharmaceutical market revenue in India will reach USD 130 billion by 2030.
Quality of Air is Critical
Compressed air is a cornerstone utility in the pharmaceutical industry. Quality of air plays a vital role in the processing of ingredients and the instrumentation side. The applications of compressed air in the pharmaceutical industry are diverse.
Nitrogen Generation: Filtered oil free compressed air is used to produce Nitrogen, which is then used in the packaging process, blanketing coating applications, or purging of equip ment.
Process Air: Compressed air comes into direct contact with products during various processes, such as jet milling, fluid bed mixing and blending, fermenters, or tablet coating.
Cleaning: Compressed air is used for cleaning and purging equipment between different batches of production.
Product Moving: Compressed air is utilised for moving prod ucts or facilitating the filling process.
Instrumentation Air: Pneumatic systems in production lines also rely on compressed air for their operation.
Any form of contaminants in the air can disrupt the functionality of the pneumatic systems and potentially lead to production quality issues. This will occur if the process air comes in direct contact with the product. Depending on the production layout, during blow-off from a pneumatic system, air may come into contact with the product. In order to prevent contamination of the final product, the air needs to be as clean as possible. With increasingly stringent quality control requirements and grow ing regulatory standards, the pharmaceutical industry must prioritise the quality of compressed air used in its production facilities.
PHARMA INDUSTRIAL INDIA