Industry 4.0: Revolutionizing Manufacturing with IoT, AI, and Advanced Robotics
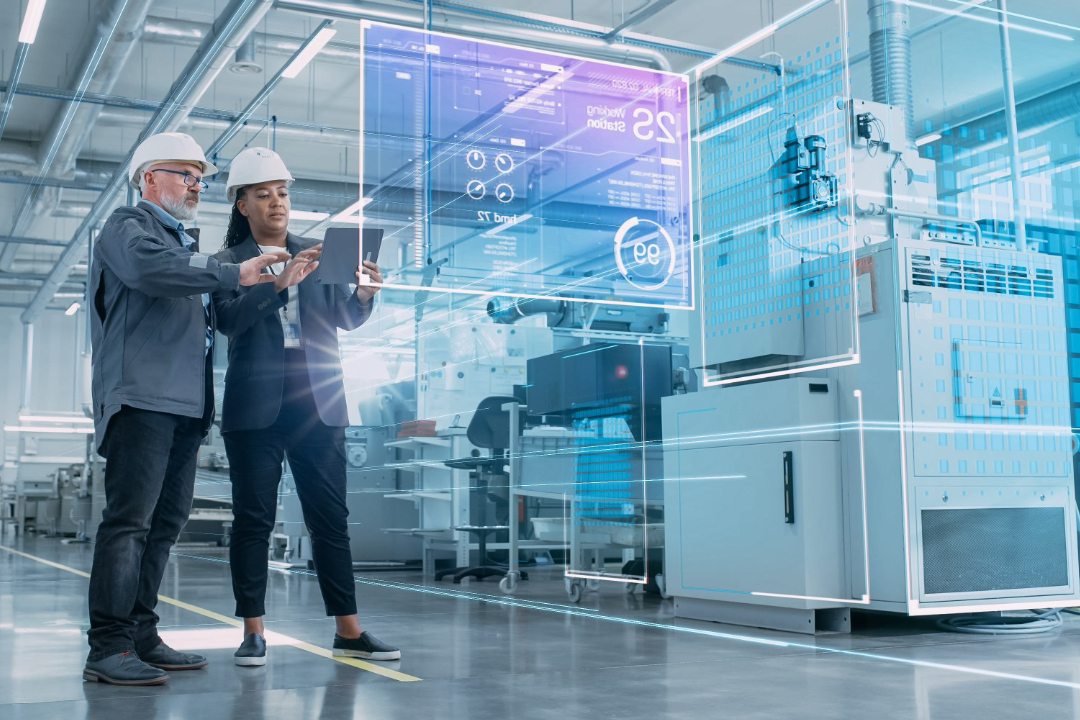
Industry 4.0 represents a paradigm shift in manufacturing. It is characterized by the seamless integration of various cutting-edge technologies, including the Internet of Things (IoT), Big Data, AI, and cloud computing, into manufacturing processes. This transformation, fueled by advancements in industrial automation and robotics, is reshaping traditional manufacturing by boosting productivity, increasing precision, significantly lowering labor costs, enhancing quality and competitiveness. As industries adopt automation and robotics, they are experiencing a revolutionary shift in how goods are produced, assembled, and delivered.
Industrial automation involves the use of control systems, such as computers or robots, and information technologies to handle different processes and machinery in an industry to replace human intervention. This technology encompasses a range of applications, from simple mechanization to advanced robotics and artificial intelligence.
Automation in manufacturing started with mechanization, where machines were used to enhance manual processes. However, todayโs automation is much more sophisticated, integrating advanced robotics and AI to create systems that can operate autonomously, learning and adapting to optimize performance continuously. This shift has led to the development of smart factories, where interconnected machines communicate with each other to improve efficiency and productivity.
Advanced Robotics: Revolutionizing Manufacturing
Robotics plays a crucial role in the modern manufacturing landscape. Advanced robotics systems are designed to perform complex tasks. Robots can operate continuously without fatigue, leading to higher productivity. Their high accuracy reduces defects, resulting in superior product quality. Additionally, robotics supports the move towards โLights Outโ manufacturing, enabling factories to operate without human presence.
Cost reduction is a significant advantage of advanced robotics. By automating repetitive tasks, manufacturers can reduce labour costs and decrease waste, resulting in considerable long-term savings. Additionally, modern robots are highly adaptable; they can be easily reprogrammed for different tasks, enabling quick adjustments to evolving production needs.
Safety in manufacturing is improved as robots can take on hazardous jobs, reducing the risk of workplace injuries. This not only protects workers but also fosters a safer overall environment. Moreover, advanced robotics integrates seamlessly with IoT and AI, enabling real-time data collection and analysis. This integration helps optimize manufacturing processes and predict maintenance needs, contributing to smarter production systems.
The Role of AI in Manufacturing
AI plays a crucial role in transforming manufacturing through various applications in industrial automation. According to World Economic Forum, the global AI in manufacturing market is valued at $3.2 billion in 2023 and is poised to grow to $20.8 billion by 2028.Technologies like machine learning and computer vision enable robots and automation systems to perceive their environment, make informed decisions, and learn from experiences. This leads to predictive maintenance, where AI analyzes sensor data to foresee machinery failures, thus minimizing downtime and prolonging equipment lifespan. Additionally, AI-driven quality control employs computer vision for real-time product inspection, ensuring higher quality and less waste. AI also enhances supply chain optimization by analyzing extensive data to improve inventory management and logistics, resulting in cost savings and better resource use. Lastly, machine learning helps identify inefficiencies in production processes, promoting continuous improvement and increased productivity.
Enhancing Productivity and Precision
The integration of advanced robotics and AI in manufacturing processes leads to significant improvements in productivity and precision. Robots can work continuously without breaks, handling tasks with consistent accuracy and speed. This reduces the likelihood of errors and increases the overall output of manufacturing operations.
Moreover, the use of AI in manufacturing allows for real-time monitoring and control of production processes. AI systems can analyze data from sensors and machines to detect anomalies and make adjustments on the fly, ensuring optimal performance and reducing waste. This real-time feedback loop enhances the overall efficiency of manufacturing operations.
Reducing Labor Costs
One of the most significant advantages of industrial automation and robotics is the reduction in labor costs. By automating repetitive and labor-intensive tasks, manufacturers can reduce their reliance on human labor, leading to substantial cost savings.
However, the shift towards automation does not necessarily mean job losses. While some low-skilled jobs may be displaced, automation creates new opportunities for higher-skilled positions. Workers are needed to design, program, and maintain automated systems, leading to the emergence of new roles and career paths in the manufacturing sector.
Impact on Quality and Competitiveness
The integration of IoT, AI, and advanced robotics in manufacturing not only enhances efficiency but also significantly improves the quality and competitiveness of products. With real-time data collection and analysis, manufacturers can achieve higher standards of quality control, reducing defects and ensuring consistency. AI-powered systems can predict and resolve potential issues before they arise, maintaining the highest levels of quality throughout the production process.
Furthermore, the ability to quickly adapt to market changes and customer demands through flexible and automated manufacturing processes positions companies to stay competitive in a rapidly evolving market. These technological advancements enable manufacturers to deliver superior products at a faster pace, providing a substantial competitive edge.
The future of manufacturing is undoubtedly intertwined with the continued advancement of industrial automation and robotics. As technology evolves, we can expect even more sophisticated robots and AI systems that can perform an increasingly wide range of tasks.
The integration of IoT, 5G, and blockchain into manufacturing is revolutionizing the industry by enhancing connectivity, data exchange, and operational agility. These technologies enable real-time monitoring and control of manufacturing processes, leading to significant improvements in efficiency, quality, and flexibility.
Moreover, the quick return on investment (ROI) that companies are experiencing is a testament to the transformative power of these innovations. By optimizing operations and reducing downtime, manufacturers can achieve substantial cost savings and gain a competitive edge in the market. As these technologies continue to evolve, they are likely to further enhance the capabilities and profitability of manufacturing enterprises.
(Disclaimer: The views and opinions expressed in this article are those of the author and do not necessarily reflect the official policy or position of Machine Maker)
MACHINE MAKER