Five Factors that Stand Critical While Upgrading Air Compressor
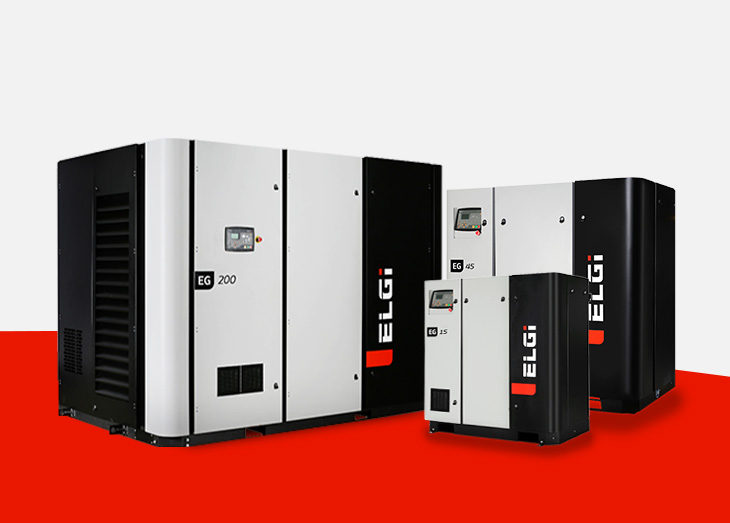
Compressor manufacturers upgrade air compressors every 3-4 years to enhance energy efficiency, reliability, and add new features, says Karthik Srinivasan.
Thanks to rapid technological advancements that the products are getting more efficient in meeting customer needs. Understanding the efficient life cycle of a product stands essential and so as stays true in case of Air compressors. Compressor manufacturers are continuously trying to lead the market on energy efficiency, superior performance, and reliability. Hence, the users of air compressors must be aware of the advanced product options available in the market.
The technological advances in control systems and the evolution of the Internet of Things (IoT) provide further motivation to upgrade air compressors at the right time. Compressor manufacturers upgrade air compressors every three to four years on average to enhance energy efficiency and reliability, add new features, and so on. This becomes critical that users or customers are aware of the key factors that must be considered while upgrading their air compressors.
1. Energy Efficiency
Of the total life cycle cost (LCC) of an air compressor, the energy cost contributes more than 75 per cent, and it is an important factor to consider. Once the energy cost of the existing compressor is determined which can be done through an air audit or a simpler total input power measurement, the benefits of a new compressor can be evaluated in terms of energy costs. In cases where the user's duty cycle of the air compressor has increased significantly over time due to additional production activities, the savings will be more beneficial with a shorter return on investment. Additionally, if the plant needs a higher flow for expansion, it is an opportunity to consolidate the need and evaluate for upgradation. The size of the machine (in kW) must also be considered, as larger units tend to generate higher savings potential.
2. Breakthrough products
Compressor users must also keep an eye out for innovative and advanced products that will result in better performance. Such ground-breaking advancements increase the plant's overall efficiency and performance and effectively meet the users' needs. For example, growing plant production needs will also need a different compressor technology, such as the transition to centrifugal compressors for larger volumes of compressed air.
3. Advanced features
Upgraded air compressors also provide manufacturers with significantly advanced controller functionality, IoT capabilities, and more intelligence via new sensors. Such features result in increased uptime and enhanced energy efficiency insights and provide inputs for optimised operational settings in addition to 24x7 remote monitoring from anywhere in the world. These features also play a salient role in instances of air compressor failure at various plants that often result in heavy losses in productivity. Improvement in consumables' life and/or reliability is another factor. All these features not only make the compressors more efficient but also futuristic and more reliable.
4. Unplanned maintenance costs
With older compressors, the need for frequent intervention increases to keep them in a reliable state, eventually leading to recurring maintenance and repair costs. An appropriate time to evaluate and upgrade your air compressor is when the cost of repairs reaches a certain level of approximately 40 to 50 per cent of the compressor value, along with the lower energy efficiency of older products.
5. Return of Investment (RoI)
The RoI is another important factor that users must consider while upgrading the compressor. With improved energy costs, the RoI can be evaluated to meet the customer's target.
IPF ONLINE