Diagnosis and resolution of compressor vibrations and cooling fan failure in an industrial plant
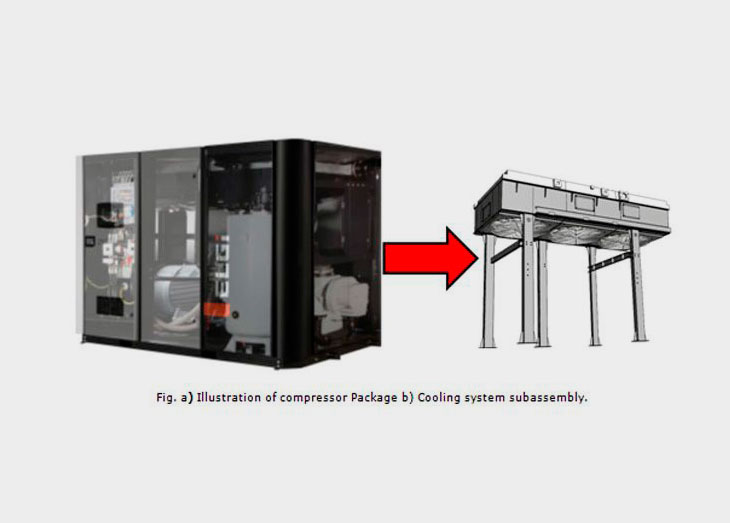
The issue of fan vibration has been a significant cause behind curtailed operations and shutdowns at various industrial plants. The article, authored by M.Jeyaselvan, Senior Principal Specialist-Technology who heads the NVH & CAE Expertise teams at ELGi Equipments Limited, provides a detailed analysis of the causes for these malfunctions. While probing the root causes for cooling fan vibrations and abnormal noises, the article gauges the different diagnostics behind these defects, thereby providing a structured approach for sustainable optimal solutions for safe and smooth operations of the plant.
Screw compressors form a critical asset in the process industries, wherein most manufacturing processes are aided by compressed air. Being a part of the positive displacement family, the periodic flow oscillations result in fluctuating dynamic forces leading to noise and vibrations in a screw air compressor. This article explains an investigation where a compressor exhibits high vibrations and noise levels leading to failure of the axial fans in the cooling system, along with a sustainable, robust solution to assure uptime and reliability for the uninterrupted operation of the plant.
The screw air compressor under discussion delivers compressed air at 2500m3/h at a pressure of 7bar as per the requirements of the specific industrial application. The motor and the compression element (airend) are coupled by a torsional resilient coupling that is dynamically isolated to minimize the transmission of structural excitation forces to other subsystems of the compressor. The outer rotor axial fans in the parallel configuration are equipped with bell-mouths for the efficient and quiet operation of the compressor. In the illustrated case, the cooling fan failures led to the shutdown of the compressor, thereby stalling the plant operation.
Prime causes for the Cooling Fan Vibrations and Abnormal Noise
There are various reasons for possible malfunctioning of a cooling fan, viz. wear and tear, excessive system resistance, accelerated fouling of coolers from the installation environment, surges in supply voltages, improper maintenance of coolers, etc. In this case, the cooling fan exhibits high vibrations and abnormal noises resulting from worn-out failure and anomaly in vibration levels.

Investigative teardown analysis of the stator-rotor rub pattern combined with the bearing bore wear pattern hypothesizes conical whirling as a possible cause for premature failure. The stator-rotor rub due to excessive dynamic deflection led to insulation peeling off in the drive end side of the motor fan, supporting the hypothesis of the conical whirling of the impeller.
Investigative diagnostics for excessive vibrations in Compressor
Numerical analysis and experimental verification
The dynamic characteristics of the fan subassembly were analysed through a numerical simulation of the complete cooling system and the subassembly of the fan, motor, suspension and support structure. Experimental verification and updating of the numerical model were achieved through an instrumented impulse generator and piezoelectric accelerometers mounted on the stator hub. The fundamental bouncing and tilting modes were established for possible excitation from residual unbalance. Detailed analysis indicates that the dynamic behaviour of the subassembly possesses adequate design margins for safe operation.
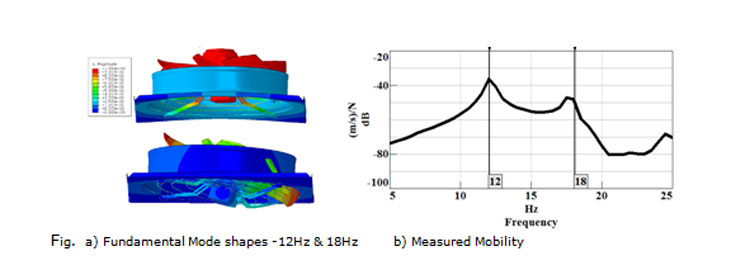
Deep dive diagnostics
The unbalanced excitation frequency of the fan at 22.5Hz was far from the fundamental structural modes to cause dynamic amplification. Hence, it was anticipated that the residual unbalance might be abnormally higher, resulting in higher vibration levels. Hence, the fan motor assembly was driven by a standalone variable frequency drive to analyse residual unbalance behaviour during the coast up and coast down operation. Despite having adequate safety margins, the system resulted in dynamic amplification causing high vibrations. The bouncing mode remains constant at 12Hz, whereas the tilting frequency increases from 18Hz to 22Hz. While operating on approaching the fanโs rated operating speed, this resulted in dynamic amplification of the vibration due to the gyroscopic stiffening of the assembly.
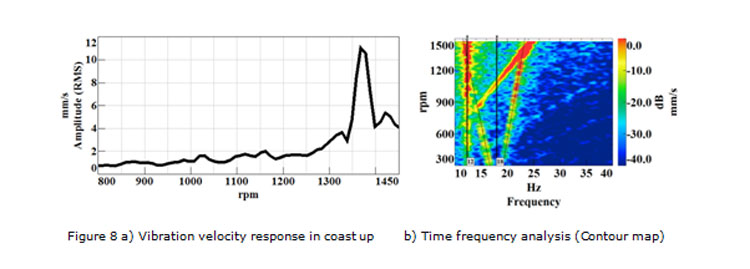
Optimal Solution through Structural Dynamic Modification
Subsequent to the identification of the root cause, solutions were sought through dynamic structural modification of the suspension assembly after detailed evaluations of the strain energy and their density distributions. The modified suspension assembly with the cooling fan accounted for the gyroscopic stiffening and was designed and verified through mobility transfer function measurements for effectiveness.
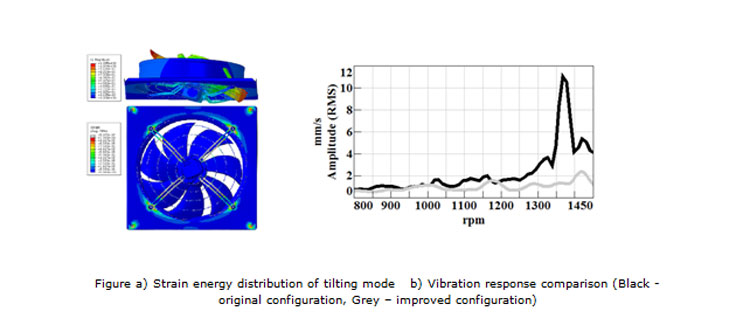
Verification trials indicated that the vibration response levels were found to be significantly lesser, ensuring smooth and safe operation of the fan motor subassembly, eliminating stator-rotor rub, and leading to the continuous and safe operation of the plant.
Conclusion
The stator-rotor rub failure of a fan motor in the cooling system assembly that led to the shutdown of the 250 kW compressor was investigated in detail. The application of engineering know-how aided by a systemic approach and tools led to sustainable solutions to the real-world engineering problem. This structured approach resulted in a comprehensive resolution, thereby reassuring the customers of the promise of a reliable product and an assured uptime.
Article by M.Jeyaselvan, Senior Principal Specialist-Technology who heads the NVH & CAE Expertise teams at ELGi Equipments Limited
ENGINEERING REVIEW