Building Gender Diversity in Manufacturing
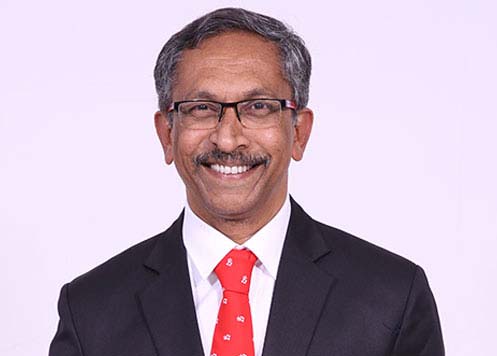
AP: Kindly tell us a bit about your organization and particularly about your role, especially your job title.
RJ: From a small reciprocating air compressor manufacturer in the 1960s, today, ELGi is a global player in the compressed air market. At ELGi, our aspiration is christened "Conquer K-2 (CK2)" โ detailing our aspiration to be no. 2 in the Global Air Compressor Market by 2027. We believe in continually building on the products, process, people and technology to achieve our aspiration.
Today, we have direct presence in over 20 countries and a global footprint spanning over 120 countries across the world. Our state-of-the-art manufacturing facilities in India, Italy and the USA power a 400+ strong product portfolio.
In my role, I am responsible for the people function of the Elgi business system (EBS) which is driven by our total quality management (TQM) practices. We won the 2019 Deming prize for sustained application and leverage of TQM practices across the organization. An important part of my role is strategy. We believe organizational strategy is driven by People, Product and Processes with which we aim to achieve synergies and scale across the organization.
AP: Given the unique challenges in your industry, can you tell us about key initiatives you have taken to drive gender diversity at ELGi?
RJ: We have been working to continuously improve gender diversity and create an equal opportunity environment in our global operations. We are concentrating more on building equality focused practices in every aspect of our business rather than being singularly obsessed with achieving the arithmetic number of gender diversity.
We have been following flexible workhours and location policy for a very long time, much before these became an established practice in various industries. We were one of the first few to encourage these in the manufacturing industry, way back in 2008.
Our vocational training institute runs a 3-year program, post which the graduates join our manufacturing facilities. This program has 50% women participants. This has helped us build and sustain gender diversity right at the start of the talent pipeline.
AP: How do you engage and educate the ecosystem of workers and their families to foster more participation from women at work?
RJ: When we decided to go global and set our aspirations beyond the Indian boundaries, one of our primary focusses was on our workmen. We knew, for us to survive and thrive in the globally competitive world, our workmen must think and act with a global mindset. To aid this process, we built a highly customized 2-year program for them. The aim was to build self-managed teams on the shop floor where the workmen would choose leaders amongst themselves and rotate this leadership role in a democratic fashion. This helped us create a culture which was tolerant of diversity of various types.
Offering the kind of exposure, such as attending courses conducted in a prestigious college, elevated their confidence, pride and status. The workmen ensured that they sent their children for higher education to good institutions. Many of them have become professional engineers, accountants, etc. Some work in ELGi and many are serving in private and Government organizations.
AP: Can you tell us about unique roles or career paths that women have chosen to pursue at ELGi?
RJ: What makes ELGi the preferred choice for women to work is the goal oriented, purpose-driven culture that permits each one of them to bring their authentic selves to the table, resulting in learning and a sense of belonging and fulfilment, every day. We have women in all functions, roles, and levels within the organization. We are a hard-core mechanical engineering industry, yet we have women leaders in functions like design, manufacturing, product management and quality.
AP: How do you measure impact of diversity on key business performance parameters?
RJ: There is enough data in public domain which points in the direction of benefits of gender diversity. Our belief is that diversity of all kinds is a necessary condition for a unit to thrive.
One of the ways we measure this is by identifying diversity of various types in a business meeting. We are cognizant of the importance of such diversity in various programs and decision-making processes in our organization.
AP: What role are technology and technology tools playing in enabling gender parity? Can you give us some specific examples?
RJ: Technology is a very significant enabler in achieving diversity objectives. Our flexi work hours and flexi location policies are backed by technology which enables the same.
Across the world, automation, digital technologies and tools have also enabled women to upskill, and actively participate and contribute at their workplaces, while staying updated with knowledge in their domains.
At ELGi our learning and development team has built an online portal that is accessible to our employees. This learning program helps them to improve their knowledge, perform better in their current roles and keep an eye on career growth opportunities available for them.
There are misconceptions that women cannot work in manufacturing because there is a lot of heavy lifting. But today, most of the shop floor is automated with hauls and lifts that do all the heavy lifting. All that needs to be done is to train women to work in such plants. We need to overcome any apprehensions and perceived barriers to women working in plants through better awareness building and education.
AP: In conclusion, what would be your advice to someone who is beginning to build a global and diverse workforce?
RJ: Firstly, the people who are considering joining the company should be told about various policies and practices which are aligned to build a global and diverse workforce.
Secondly, specifically for women employees, we must continue to build the notion that manufacturing is a great career option. Today, manufacturing is a progressive industry focused on the global markets and offers immense diverse opportunities to everyone including women leaders. We are an industry where you see the value addition right in front of your eyes and is more tangible than services.
READ MORE