Air~Alert: An IoT-Enabled Solution for Air Compressors
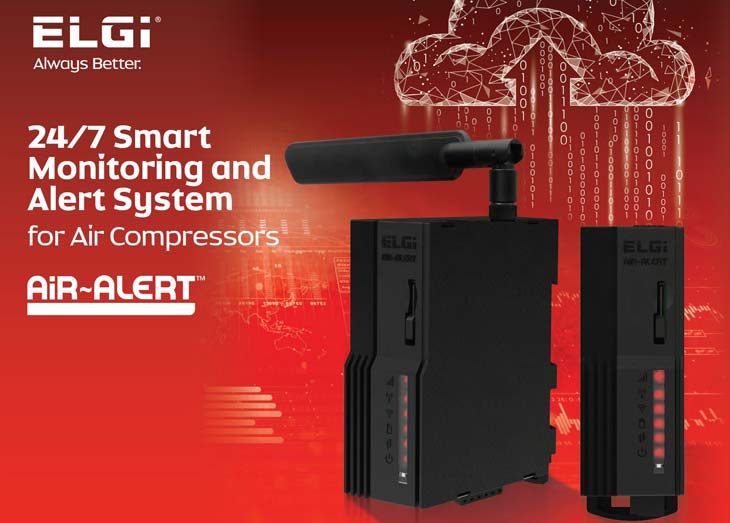
Mechanical air compressors have been used in several industrial applications for a long time, ever since their recorded invention in the 18th century. Air compressors have become more advanced and complex with the advent of multiple technologies, such as reciprocating, rotary, and centrifugal air compression. Electronic controllers have added more efficient, safe, and reliable ways to operate an air compressor. Fast forward to today, with highly advanced computational design and analysis tools, the introduction of smart electronic controllers with several sensors, and the Internet of Things (IoT) enabled solutions, air compressor systems are becoming smarter, more efficient, and highly reliable.
In this article, one can learn how an IoT-enabled solution for air compressors works and how it will improve machine performance and operation while allowing 24x7 monitoring of compressor operation from anywhere in the world!
To start with, the fundamental objectives of any industrial IoT solution are to enable the following with the help of smart data analysis:
Improve Uptime of the Machine: Maximize productivity by alerting maintenance needs and predicting failure ahead of time.
Improve Operational Efficiency: In the case of air compressors, it should enable improvement in energy efficiency, and improved operational efficiency in maintenance activities.
Remote Monitoring: Allow access to real-time status and historical data of the equipment from anywhere in the world.
In the context of air compressors, all the points indicated above are vital, and a solution needs to be comprehensive.
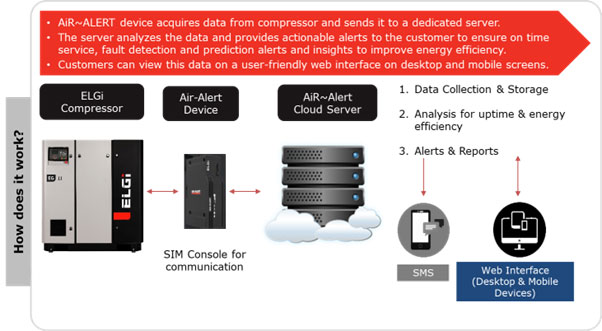
Introducing ELGiโs Air~Alert
Air~Alert is a state-of-the-art Industrial IoT solution for air compressors. The figure above illustrates how it works.
Improved Uptime
Gone are the days of manual logging and potentially missing on-time service of compressors. With Air~Alert, the users get an advanced notification when the service is due for the compressor based on the data from the controller. It also enables the scheduling of planned maintenance at a convenient time without hurting the productivity of the plant.
What more? Intelligent algorithms sort and structure huge amounts of data from each compressor and analyse for any abnormal operating parameters, including pressure, temperature, load-unload counts, trips, etc., and send out an appropriate warning alert via email if any major functionality of a compressor subsystem is at risk. The user and the service provider can then analyse the root cause and act ahead of time, avoiding major and expensive failures while ensuring the productivity of the plant is not lost.
With more machines connected and analysis of more and more data, the system will get even better at predicting failures ahead of time!
Improved Energy Efficiency
It is a known fact to many that for an air compressor, approximately 80% of its life cycle cost comes from energy costs. Therefore, it is critical to understand if the compressors are operating efficiently. By understanding the pattern in utilization % of a compressor based on load and unload hours of operation, the data enables us to determine if there is potential for energy savings.
For example, if a fixed-speed compressor has a utilization of 70% by adding a Variable Frequency Drive (VFD) to the unit, energy savings of up to 25% can be achieved. Similarly, if the utilization is very low in a particular shift of plant operation, the data will help in determining if having an exclusive smaller compressor for that shift will result in energy savings. Furthermore, if the utilization pattern keeps increasing over a period without any change in processes or additional need, it is an indication to evaluate any leakage or inappropriate use of compressed air in the plant.
Remote Monitoring
With all the benefits of improving uptime and enabling energy efficiency improvement, Air~Alert also allows the user to monitor the live status and view historical data of the compressor unit from anywhere in the world, 24/7. A monthly summary report is also sent to the users to understand the service needs, utilization details, and any failure trips. With more and more machines connected, future advancements in data science tools and artificial intelligence will only enhance these features further. The air compressor industry is poised to witness significant improvements in this area in the upcoming years!
Air~Alert: Your compressors connected!
MACHINEMAKER