Air Compressors in Chemical Manufacturing: Boosting Safety and Efficiency in Hazardous Environments
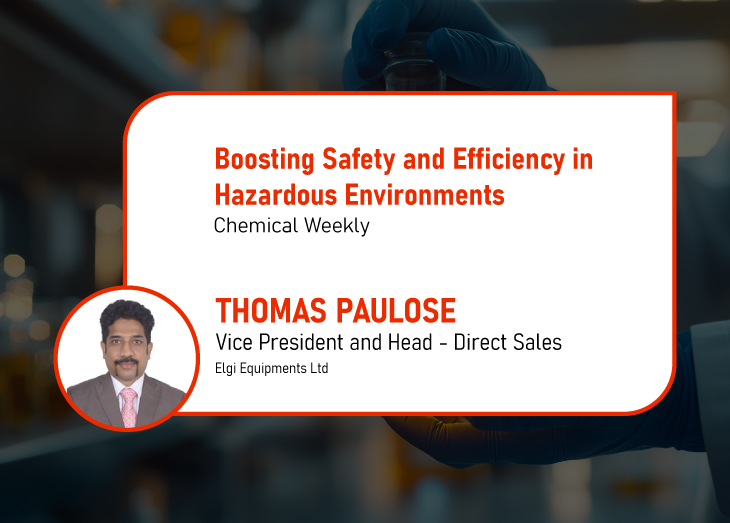
The chemical industry is synonymous with precision, safety, and reliability. In this sector, processes often involve hazardous substances, complex reactions, and delicate controls, making operational efficiency a paramount concern. One of the critical components supporting this operational landscape is the air compressor. Air compressors play an essential role in various aspects of chemical production, including pneumatic controls, material transport, and maintaining safe, contaminant-free processes. Their ability to operate in hazardous environments while ensuring both performance and safety has made them indispensable to chemical manufacturing facilities worldwide.
Role of compressed air in chemical production
Clean, dry compressed air is critical in chemical manufacturing, serving various functions like material conveyance, process control, and safety assurance. Meeting specific air quality standards presents a significant challenge for the chemical sector.
Compressed air finds application in critical processes such as mixing, conveying, and packaging within the chemical industry. The quality of compressed air holds paramount importance, directly impacting product quality and manufacturing process efficiency. Precise conditions are often required for chemical processes, and contaminated compressed air introduces impurities, jeopardizing product quality, purity, and consistency.
In chemical production, air compressors serve as the backbone for a range of applications, contributing directly to both safety and productivity. The most common functions of air compressors in the industry include:
Process Air: Compressed air is vital for various chemical manufacturing functions, including cleaning, aeration, and product transport. High-quality compressed air ensures the absence of contaminants, preserving product purity and integrity. In applications where air comes into direct contact with products, maintaining air purity is critical to prevent costly production disruptions and ensure compliance with industry standards.
Operation of Control Valves and Cylinders: Control mechanisms like valves and cylinders are essential for automation and precision in chemical processes. Air compressors, power these components, enabling precise control and efficient operation. Reliable compressed air systems improve the accuracy and productivity of manufacturing processes by ensuring these mechanisms function seamlessly.
Safe Material Handling: Material handling in the chemical industry demands safety, particularly in environments with explosion risks. Air-operated fluid pumps, driven by compressed air, provide a secure method for transporting hazardous substances. By eliminating electrical ignition sources, these pumps are ideal for handling volatile materials safely and reliably.
Nitrogen Generation: Compressed air systems are instrumental in generating nitrogen through filtration processes. Nitrogen is widely used in inerting, blanketing, and purging applications to prevent oxygen reactions. A dependable supply of compressed air ensures a continuous and efficient nitrogen generation process, enhancing safety and productivity in chemical manufacturing.
Air Curtains: Air curtains create invisible barriers that safeguard clean and controlled environments within production areas. These barriers help prevent contamination by blocking dust, fumes, and other pollutants. Maintaining such controlled environments is essential for ensuring product quality and protecting worker safety in chemical manufacturing.
Product Drying: Drying is a crucial stage in many chemical production processes, and compressed air plays a key role in expediting this step. High-quality compressed air ensures efficient, uniform drying, which is critical for achieving consistent product quality. Integrating air compressors into drying operations can enhance productivity and reduce process times.
Mixing and Agitation: Consistent mixing and agitation are vital for achieving uniformity in chemical solutions. Air compressors, power mixers and agitators, ensuring thorough blending of ingredients. This uniformity is essential for maintaining the quality, performance, and stability of chemical products.
Pneumatic Conveying: Pneumatic conveying systems, powered by compressed air, enable the efficient movement of materials such as powders and granules within the manufacturing process. These systems promote rapid, safe, and contamination-free material transfer, improving production efficiency and maintaining clean environments.
Packaging: Compressed air is crucial in packaging processes, including sealing, labeling, and other final production steps. By ensuring secure and efficient packaging, compressed air helps maintain product quality, extend shelf life, and meet regulatory requirements.
Oil-Free Air Compressors: A Game Changer in Chemical Manufacturing
Oil-free air compressors are particularly advantageous in chemical manufacturing due to their ability to deliver 100% contaminant-free air. These compressors are designed to operate without lubricants in the compression chamber, eliminating the risk of oil contamination that could compromise product quality or disrupt sensitive processes. The following benefits underscore their importance:
Enhanced Product Quality: Oil-free compressors ensure the air used in production processes is completely free of contaminants, maintaining product integrity and consistency.
Improved Safety: In hazardous environments, the absence of oil minimizes risks associated with oil mist or vapors, which could be flammable or reactive.
Reduced Maintenance: Oil-free systems require less maintenance related to oil changes or filtration, resulting in lower operational costs and less downtime.
Regulatory Compliance: Many chemical manufacturing applications are governed by stringent air quality standards. Oil-free compressors help facilities meet these requirements, avoiding compliance issues or penalties.
Performance Benefits of Air Compressors in Chemical Manufacturing
Air compressors offer numerous performance benefits that significantly enhance the efficiency of chemical manufacturing processes. One of the key advantages is their ability to deliver a consistent supply of compressed air, which is vital for maintaining precision in chemical processes, particularly in applications like pneumatic controls. Even slight fluctuations in air pressure can impact the accuracy of valves and actuators, but air compressors ensure stable pressure, improving both product quality and process efficiency. Additionally, modern air compressors are designed for durability and reliability, reducing the risk of unplanned downtimeโa critical factor in the chemical industry, where delays can lead to financial losses and safety hazards.
Technologies like variable speed drives (VSD) have further enhanced their reliability, allowing compressors to operate more efficiently with less wear and tear. Another significant benefit is energy efficiency. As energy consumption is a major cost concern for chemical plants, air compressors have evolved to be more energy-efficient, with innovations such as VSDs enabling them to adjust output based on demand. This not only minimizes energy consumption but also helps lower operating costs, making air compressors an economically and environmentally favourable choice for chemical manufacturing facilities.
CHEMICAL WEEKLY