Industry story on Minimising Downtime in the manufacturing world for a electrifying future
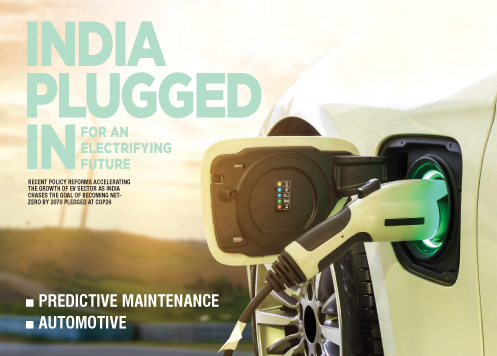
Oil-free compressor manufacturer ELGi Equipments, for instance, invests in technologically advanced CNC machines driven by servo motors and servo systems to deliver high-quality products and gain high productivity and uptime at its manufacturing plants. โThese machines must be operated and maintained in the right condition to retain accuracy, speed, and quality to ensure capital efficiency,โ says Balaji Radhakrishnan, Vice President โ Maintenance, Elgi Equipments Limited.
He underlines that unplanned disruptions in these machines due to downtime and quality issues significantly affect production, impacting customer promised delivery commitments. โHence, there was a need to leverage technology to study the performance and condition of critical parts, which enabled us to proactively manage their maintenance process, resulting in the highest uptime, performance, and zero unplanned downtime.โ Elgi uses solutions like machine collision sensors which allow them to detect collisions or sudden overloads due to abnormal process parameters. โWe have been able to fix ranges for the process conditions and monitor changes online.โ Radhakrishnan explains the sensors pick up variations and trigger the automatic machine interlock system to put the machine on safe standby mode. โThis helps us to analyze and implement corrective actions,โ he said. These sensors have helped them identify operator errors, train them to follow systems, and update the process parameters.
Some of the latest technologies implemented by Elgi Equipments include IoT-enabled energy management system and low-cost automation with predictive maintenance system. โWe have implemented an IoT-enabled energy management system in our state-of-the-art manufacturing plant at Kinathukadavu. IoT-enabled machines, all connected and sharing data seamlessly, were deployed to analyze the captured data using advanced statistical tools, identify energy-saving opportunities, improve systems, and conserve energy,โ says Radhakrishnan.
Their plant operations have managed to achieve over 24% energy efficiency with the implementation of IoT-enabled energy management systems, resulting in power reductions of around 1.02 megawatts per year and significant savings in annual power spending. โWe continuously monitor the machine design parameters by introducing the vibration sensors, humidity sensors, temperature sensors, voltage measuring sensors, and emission measuring sensors that are connected with mini PLC,โ he says.
MANUFACTURING TODAY