The difference between rotary screw air compressors and reciprocating air compressors
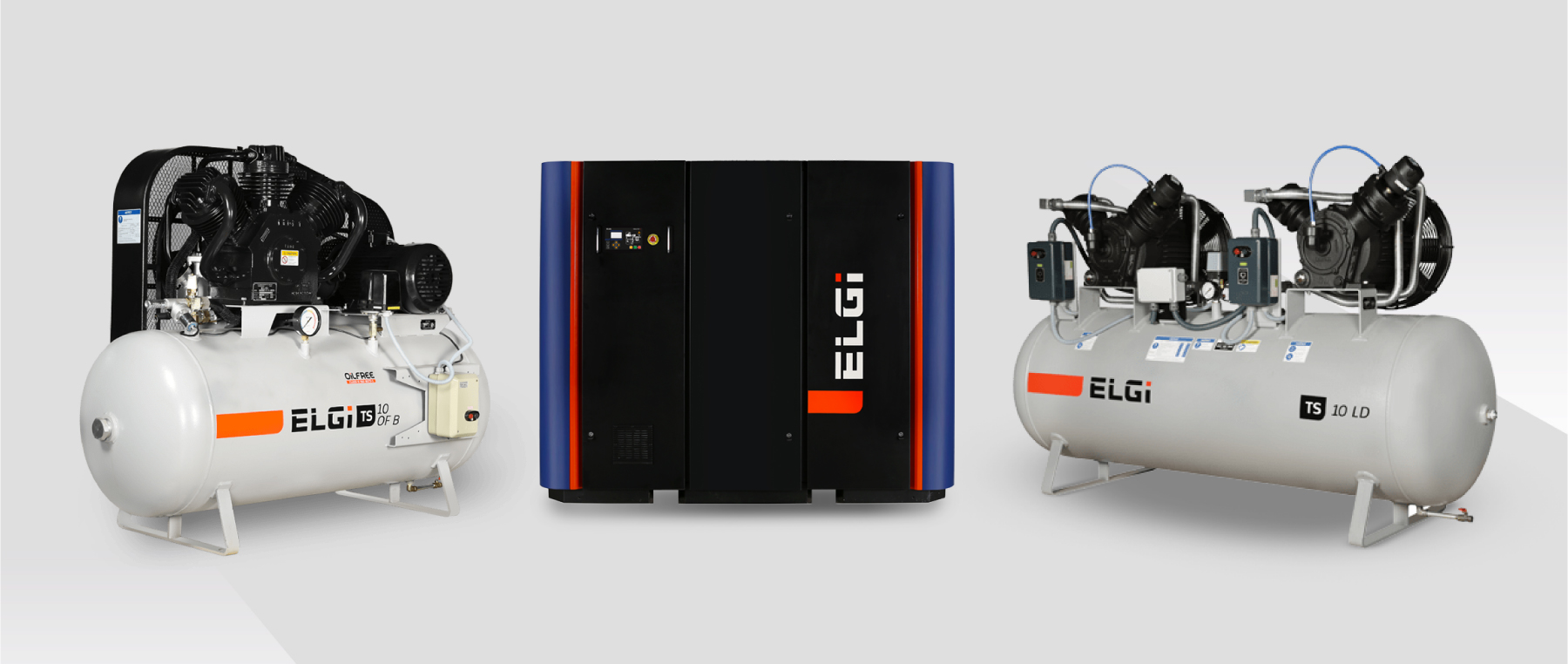
The key difference between Rotary Screw Air Compressors and Reciprocating Air Compressors is the mechanism in which they compress air.
Their distinct features can be understood in terms of:
System design
Rotary screw air compressors have a couple of meshing spiral screws called rotors for compressing the input air. While reciprocating air compressors employ pistons moved by a crankshaft for compressing the air.
Components involved
With just two moving parts (screws) that have a small gap between them, screw air compressors are not subject to much wear and tear. Even in models where the two screws come in contact with each other, they donโt encounter any friction, which is why they are less likely to break down.
On the other hand, reciprocating air compressors have several moving parts like pistons, piston rings, connecting rods, and inlet-outlet valves due to which they are noisier and may need stocking of spares.
Temperature
The internal heat produced by screw air compressors during operation is between 80 - 99 degrees celsius. The heat production is limited, as there is no friction between the screws. The oil or lubricant used between the rotors and casing creates a non-wearing seal that can eliminate the heat with the help of a thermostatically managed fluid circuit.
In reciprocating air compressors, the pistons operate at temperatures between 150-200 degrees celsius. The high temperatures are due to the friction caused by the movement of piston rings against the cylinder walls.
Oil filtration
The chances of finding residual oil in an oil-lubricated screw air compressor are very low, because this unit has a three-stage oil filtration system. The oil content is typically below three particles per million (PPM).
However, a reciprocating air compressor does not have an oil filtration system, which is why, its outlet air can be more contaminated than a screw air compressor. The oil content in the air also increases when piston rings and oil rings deteriorate, allowing oil to move up to the compression side.
Air-receiver tanks
Itโs often tricky to choose the appropriate size of an air-receiver tank when you use a rotary screw air compressor, as most of the associated applications donโt need a tank at all. This unit is devised to deliver a continual stream of compressed air without any disruption or pulsation. If the airflow requirement of your tool is less than what is produced by the air compressor, then you wouldnโt need a tank at all.
On the other hand, piston-based compressors come with air-receiver tanks in which they store air and remove pulsation before it runs the connected applications. Once the tank is full, one can operate the equipment.
Individual benefits of both the models
The top advantages of choosing a screw air compressor are:
- Continuous air supply
- Higher duty cycle
- Better durability
- Higher overall efficiency
- Lower ambient noise
- Higher airflow per rated power
Few reasons why some operators still prefer a reciprocating air compressor are:
- Very high pressure requirements
- Spare parts management
- Lower duty cycle
At ELGi, we offer both rotary screw and piston-based reciprocating air compressors. Although reciprocating air compressors make for a good option for low capacity requirements, your facility may need more energy-efficient units when the demand for associated applications increase. Rotary screw air compressors are compact, quiet, and reliable with a consistent airflow. They will give you a stable air supply for a variety of applications across industries.
To schedule a free air compressor selection call, please write to us at communications@elgi.com.