Technology Has A Profound Capability To Solve Environmental Issues And Build A Sustainable Future
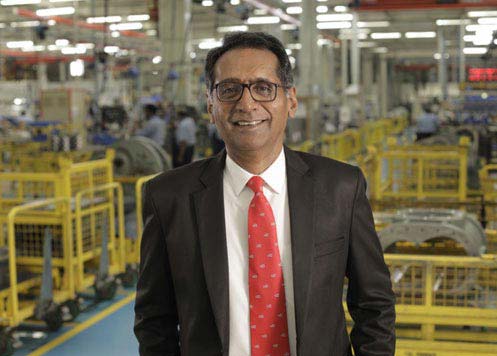
In an interview with BW Businessworld, Jairam Varadaraj, Managing Director, Elgi Equipments talk about technology, sustainability standards and environment.
How do you position ELGi? What products ELGi is manufacturing and for how long? And how it is benefiting the environment?
ELGi was founded as a reciprocating air compressor and garage equipment manufacturing company in the 1960s. With continuous engineering improvements, investment in R&D and infrastructure, and technology partnerships, we indigenized the development of rotary screw air compressors in the 1980s. Today weโre one of the global leaders in the compressed air space with an extensive range of innovative and technologically advanced compressed air solutions. We do business in over 120 + countries while weโre directly present in the USA, Australia, Bangladesh, Brazil, the Gulf, India, Indonesia, Italy, Kenya, Malaysia, Nigeria, Philippines, Thailand, Vietnam, Spain, the Czech Republic, Bulgaria, Poland, the Netherlands, Sweden, and Denmark. Over the years weโve earned worldwide accolades for designing customer-centric, compressed air solutions that are sustainable, and help companies achieve their productivity goals while ensuring a lower total cost of ownership. Our portfolio of 400+ products ranges from oil-lubricated and oil-free rotary screw, centrifugal and reciprocating compressors, to dryers, filters, and downstream accessories; weโve state-of-the-art manufacturing facilities in India, Italy, and the USA. Our products serve a wide variety of applications across industries ranging from manufacturing, food & beverage, construction, pharmaceuticals, and textiles.
The environment is significantly impacted by the worldโs accelerating electricity consumption i.e., approximately 25 trillion kWh. Now 42 percent of this electricity is used to power industries worldwide and 28 percent of this 42 percent is used to power industrial electric motors. Out of this 28 percent, approximately 10-12 percent of the electrical energy is consumed by air compressors. With a typical air compressor ranging between 11 and 250 kW running for 8000 hours for 5 years with 70 percent loading, approximately 90 percent of the cost incurred by the customer is the energy cost. At ELGi, weโre focused on building energy-efficient compressors which ensure efficient energy consumption and thereby lower energy costs for all our customers. While our customers gain via lowered energy costs, weโre also enabling companies to reduce carbon emissions and lower the overall impact on the environment.
What are the roles technology play when it comes to sustainability?
Technology is changing our world. In my opinion, technology has a profound capability to solve environmental issues and build a sustainable future. At a fundamental level, technology has created โgreenerโ ways to interact in our world. From LED light bulbs to email and more recently virtual meeting interfaces, technology is constantly evolving to increase its own sustainability.
Weโve seen tremendous advances in compressor technology, over the last 360 years, ranging from power to efficiency i.e., we went from air billows to the highly sophisticated compressor technologies plants use around the world today. Today, technology in the compressed air industry focuses on helping organizations lower their operating costs while achieving their productivity goals, all of this while achieving new levels of performance and efficiency. For example - new motor technology increases efficiency and performance. Variable speed drives reduce energy loss and modulate the on-off operation, IoT based applications have enabled compressors to be connected via mobile systems thereby ensuring performance monitoring and predictive maintenance over secure networks.
At ELGi, our technology teams focus on staying ahead of the curve, while developing technology breakthroughs aimed at transforming the conventional boundaries of compressor technology with a relentless focus on increasing performance and energy efficiency.
How is ELGi contributing to managing and reducing carbon emission?
It is, without a doubt, that burning fossil fuel is the globe's biggest source of human-caused greenhouse gases and the primary cause of climate change. At ELGi our commitment to addressing climate change comprises of several low carbon initiatives coupled with a longer-term sustainability roadmap. For one we've undertaking initiatives focused on reducing the carbon footprint of our manufacturing facilities and offices, together with a clearly defined focus on building energy-efficient products that enable companies around the globe to reduce their carbon footprint.
Allow me to expand. Weโve introduced 5 to 10% energy efficiency improvements across our product ranges in recent years. This has resulted in a considerable reduction in total energy consumed by our compressors driving critical applications worldwide. For example, our Heat Recovery Systems (HRS) enables companies to capture up to 96% of wasted heat generated during the compression process. The system converts wasted heat into hot water that can then be utilized for heating purposes. This, in turn, reduces the need for additional heating systems running on conventional power thereby reducing CO2 emissions.
Our plant maintenance, machining, and engineering teams work on the employment of new technology and best practices to reduce our impact on the environment. For example - renewable energy generated through windmills contributes to approximately 15 percent of the total power consumed at our manufacturing units. Our plant operations have achieved over 24 percent energy efficiency with the implementation of IoT enabled energy management systems. Aside, on World Earth Day, 2020 we introduced the ELGi โSteps for Changeโ program to encourage each of our employees to take environmental action and be socially responsible. With this, every ELGi employee across the globe has committed to undertaking a small but significant environment-friendly initiative. The program has seen our employees explore emission-reducing lifestyle changes, plastic pollution action, university and school teaching, tree planting, local clean-ups or even switching to a more plant-based diet, all of this resulting in a positive impact for the environment while ensuring we collectively do our bit to reduce our carbon footprint across the world.
What is "Vertically Integrated Manufacturing System" and how it gives control over the quality and design of an air compressor?
ELGi is one of the only companies in the world to make its own air ends, pressure vessels, castings, motors while conducting complete machining and compressor assembly, unlike other compressor companies that focus on core parts. In line with our quality focus and to ensure seamless product delivery, we've orchestrated the selective backward integration of our manufacturing facilities. All of this at the ELGi Air Centre Plant, which spans over 5 million square feet of manufacturing space at our headquarters in India.
Every ELGi screw air compressor is built with a proprietary high precision airend; our in-house built, rotor grinding machines are best-in-class and ensure rotor finishing with very close tolerances. Our vertically integrated processes have greatly enhanced our manufacturing
capabilities, helping maintain high-quality standards and providing scope for design innovation, while our foundry facilitates design flexibility and high-quality castings. We have also developed in-house FEA, CFD, NVH, and Industrial design capability, to ensure continuous innovation.
How ELGi's products are energy efficient? And what makes them good for the environment?
Improved energy efficiency is derived from better technology and a better understanding of customer applications. ELGi's screw compressors have large airends running at slow speeds to produce compressed air. An airend is the heart of a screw compressor and it comprises two screws that rotate in opposing directions. Their rotation draws a volume of compressed air and compresses it to the required pressure. The size of the screws determines the volume of air. ELGi's airend design employs large rotors rotating at low speed, which offers high volumetric efficiency, thereby, resulting in the lowest energy consumption. While we already offer motors of efficiencies ranging from IE1 to IE4, for the next stage of efficiency, we are working on motors that are custom matched to our airend size, allowing for optimum power consumption. Finally, our machines are designed with variable frequency drives (VFDs) that help save power during fluctuating air demand.
As manufacturers, we believe it is our responsibility to right size compressors for our customerโs requirements. We have invested in training our sales team to study customer applications and recommend the right size of compressors. This ensures our energy-efficient products provide customers with significant savings in energy costs translating to a reduction in carbon footprint while reducing the environmental impact.
What special features make an ELGi product stand out in the market?
We have an ambitious aspiration and our definition of Always Better is closely coupled with us always being the customerโs choice. How do we do this?
ยท Developing products with the best Life Cycle Cost (LCC) for every customer
ยท Guaranteeing best in the industry uptime
ยท Reaffirming our commitment to Reliability by providing our customers with robust warranty periods.
Weโve also recognized the need to adopt a management philosophy that builds vertical excellence in each operating function and customer-centric horizontal excellence across the business, operations, and support functions. At ELGi, we endeavor to accomplish ordinary tasks in an extraordinary manner and turn extraordinary ambitions into ordinary tasks. Our commitment to quality, coupled with TQM excellence led to us winning the Deming Prize in 2019, becoming one of the first compressor manufacturers to do so in over 60 years. Every ELGi product bears testament to our hallmarks of reliability and performance while meeting or exceeding industry-specific demands such as energy-efficiency, cost-efficiency, ruggedness, zero oil tolerance, or air delivery precision. At ELGi, we believe in pushing the boundaries, every day, in our quest to be โAlways Betterโ.
Does COVID-19 have hit the demand of the air compressors?
Well, the global air compressor market was estimated to be USD 15 billion with a forecasted CAGR of about 2 โ 3% year on year, pre-COVID 19. The pandemic has caused a significant impact worldwide. However, we're positive about the upsurge in industrialization globally, as we move ahead to recovery; while essential service industries will recover relatively faster, other businesses could have a gradual recovery. Industrial investments together with infrastructure projects and swift urbanization will be just some of the growth drivers for the compressed air industry. Escalating concerns about sustainability and building a carbon-neutral future, together with government policies pertaining to energy conservation, will drive the adoption of energy-efficient air compressors. In a shrunk economic condition, customers are not going to be driven by brands, as much as by value proposition. For Elgi, this is advantageous as our value proposition is high; we expect to be strongly placed in terms of customer receptivity. Our company vision is โAlways be the choice everywhereโ. We aspire to live up to this commitment every day for our customers, suppliers, distributors, employees, investors, and society.
What are ELGi's views on a greener environment? And what aspects do ELGi follow to a part of the journey?
I believe the pandemic has caused us to take a renewed look at the impact of our actions on the planet's ecological stability. Rising temperatures, wildfires, droughts, floods, hurricanes, debilitating air pollution, inordinate waste, and plastic waste choking our oceans. What do they indicate? Green initiatives that improve energy efficiency, reduce dependence on fossil fuels, and invest in preserving and restoring nature are quintessential to building a sustainable future.
At ELGi, weโre taking small but steady steps to protect and restore the Earth and our natural resources. While Iโve touched upon some aspects earlier - our manufacturing processes are planned and designed to use fewer natural resources, reduce pollution and waste, and recycle and reuse materials. Every year, more than 20 lakh liters of rainwater generated through rainwater harvesting is used for maintaining the green zone at our manufacturing plant. We recycle and reuse the waste sand generated at the ELGi Foundry; converting this into solid blocks and bricks, then used for construction. Every year, over 3000 trees are planted around our manufacturing units. Furthermore, we encourage our employees to build dense, native forests at all of our factory locations using the Miyawaki technique which involves planting native species. Our employees together with their family members have planted more than 6000 trees for now. We aim to plant 30,000 trees over the next three years.
How does ELGi fulfill its Corporate Social Responsibility (CSR)?
At ELGi, our commitment to making a difference and developing sustainable communities for the future is strongly embedded in our ethos. Some of the initiatives undertaken as part of our social responsibility for 2019-20 include projects in the areas of Education, Social Development, Medical Relief, Sports, Women Empowerment, Cultural Protection, etc. The ELGi Matriculation Higher Secondary School was established, way back in 1989 and since then, has enabled hundreds of children, from low-income families to defy the odds and fulfill their dreams, by offering them access to affordable, quality education. For over 30 years, the ELGi School has lived up to its vision of "giving back to society by developing good citizens through holistic quality education at a subsidized cost." Today, some of the school's alumni, employed by multinational companies, are pursuing careers in engineering, chartered accountancy, medicine, and biochemistry.
READ MORE