ELGi’s march towards Global Leadership in Compressor Technology

ELGi Equipments Limited is a leading air compressor Technology & manufacturer with a broad line of innovative and technologically superior compressed air systems. ELGi has earned worldwide distinction for designing sustainable solutions that help companies achieve their productivity goals with low ownership costs. The company has ambitious growth plans to realize its global aspirations, discovers P.K Balasubbramaniian in an interview with Dr. Jairam Varadaraj, Managing Director, ELGi. Excerpts:
Q. How would you present ELGi Equipments to a new audience?
From a small reciprocating air compressor manufacturer in the 1960s, today, ELGi is a global player in the compressed air market. At ELGi, our aspiration is christened as “Conquer K-2 (CK2)” – detailing our aspiration to be the No. 2 in the Global Air Compressor Market by 2027 and drawing inspiration from Mount K2, the second highest peak in the world and arguably, the toughest peak to ascend among the eight thousanders. We believe in continually building on the products, process, people and technology to achieve our aspiration.
Across geographies, we offer customers a complete range of compressed air solutions from oil-lubricated and oil-free rotary screw compressors, oil-free reciprocating compressors and centrifugal compressors, to dryers, filters and downstream accessories.
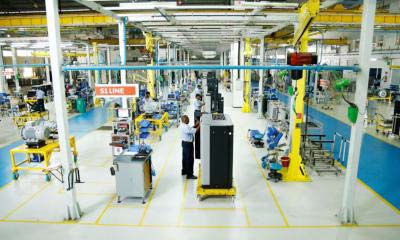
Today, we’ve direct presence in over 20 countries and a global footprint spanning over 120 countries across the world. Our stateof-the-art manufacturing facilities in India, Italy and the USA power a 400+ product strong portfolio. ELGi is possibly the only company in the world that makes its own air ends, pressure vessels, castings, motors and conducts complete machining and compressor assembly.
Unlike other compressor companies that focus on core parts, and with a view to meeting our quality focus and ensuring seamless product delivery, we’ve orchestrated the selective backward integration of our manufacturing facilities. All of this at the ELGi Air Centre Plant, which spans over 5 million square feet of manufacturing space at our headquarters in India.
Over the years, our expansion plans have comprised several acquisitions across the world spanning Rotair SPA in Italy, Pulford and Advanced Air in Australia, Pattons Inc. and more recently Michigan Air Solutions in USA.
Q. You are a pioneer in cutting edge compressed air technology. What are the product innovations you have come up with in your current range?
At ELGi, our definition of Always Better is closely coupled with us always being the customer’s choice. And across the world, customers incur significant ownership costs, considerable maintenance requirements and relatively poor reliability. At ELGi we’ve questioned this, connected the dots and developed technology specifically applied to solving an existing need in a new way.
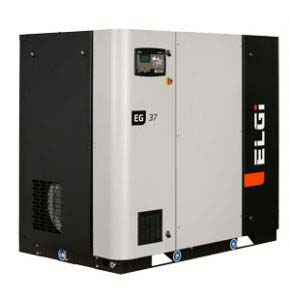
And our 400+ product range bears testimony to this; for example, the lubricated screw (ELGi Global (EG) series and Encapsulated (EN) Series) and oil free screw air compressors are highly reliable, energy efficient and operate at low energy costs. Our Oil free (OF) series and ‘Always Better’ (AB) series of oil free screw compressors are class zero certified by TUV in accordance with the ISO 8573 standards and the heat recovery systems (HRS) help companies recover approximately 96% of the waste heat generated during the compression process which can then be re-utilized for heating of air and water.
We’ve also innovated to address the compressed air needs of companies who have historically suffered the constraints of high cost, poor reliability, and low efficiency in order to have oil free air.
The ELGi AB ‘Always Better’ series, a disruption in oil free compressed air technology, offers every customer across the globe, a no-compromise, oil free solution at approximately 8 – 10% reduced lifecycle cost when compared with prevailing oil free technology. Finally, our compressed air experts across the world offer specialized services to help customers identify potential areas of energy savings and provide them with solutions guaranteeing the optimum use of compressed air.
Q. What are the technological innovations you have showcased recently in your pursuit to be ‘Always Better’?
Since its inception, ELGi has adopted innovation as a key differentiator, keeping pace with global compressor technology trends and evolving customer needs. And we believe our technological capability is a key foundation. Not just the know-how of technology but the know-why of technology pertaining to the core elements and critical parts of the compressor.
As I mentioned earlier – ELGi is possibly the only company in the world that makes its own air ends, pressure vessels, castings, motors and conducts complete machining and compressor assembly. ELGi is also focused on leveraging latest technologies like machine learning and has its own IOT platforms to deliver innovative advantages to its customers.
Today, our global technology center, focuses on building compressed air solutions that help organizations lower energy consumption and operating costs, while achieving their productivity goals. With a strong team comprising about 200 employees, our technology breakthroughs aim to transform the conventional boundaries of compressor technology with a relentless focus on increasing performance and energy efficiency.
Q. What are the efforts you make to help the customer achieve his productivity goals, while keeping the cost of ownership low?
At ELGi, our definition of ‘Always Better’ is closely coupled with us always being the customer’s choice –
- Developing products with the best Life Cycle Cost (LCC) for every customer
- Guaranteeing best in the industry uptime
- Reaffirming our commitment to Reliability via providing our customers with robust warranty periods.
- Driving cost leadership through technology
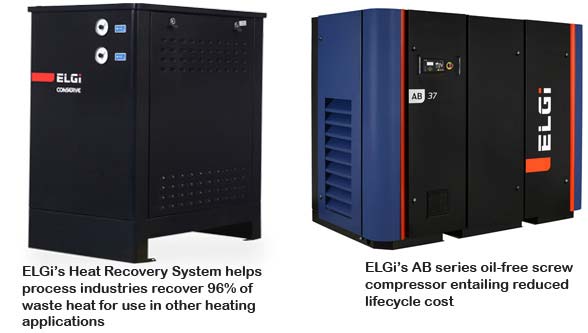
Now, how do we ensure we keep the cost of ownership low for every customer? Today, the world’s electricity consumption has been accelerating and according to recent estimates stands at approximately 25 trillion kwh. Out of this, 42% of electricity generated is utilised to power industries worldwide and 28% of this 42% is used to power industrial electric motors. Out of this 28%, approximately 10-12% of the electrical energy is consumed by air compressors. With a typical air compressor ranging between 11 and 250 kW running for 8000 hrs for 5 years with 70% loading, approximately 90% of the cost incurred by the customer is the energy cost. The initial investment cost and the maintenance cost stands at 5% each.
At ELGi, we focus on building the most efficient compressors which ensure efficient energy consumption and thereby lower energy costs for all our customers. We also focus on ensuring zero downtime for our customers via a relentless focus on quality, reliability and highly responsive service. With this, our compressors stay up and running and help our customers achieve their productivity goals while keeping the cost of ownership low.
Q. You recently got NABL accreditation. What’s its significance? Does this mean you have made your QA system more stringent?
Yes, our proprietary Metrology Department has recently been accredited by NABL (National Accreditation Board for Testing and Calibration Laboratories) in the field of mechanical – dimension, pressure and torque.
The ELGi Metrology Department was set up to ensure every product undergoes the right measurement through the usage of accurate and precise measuring equipment, resulting in a reduction in variation in accordance with the ISO/IEC 17025-2017 norms. Over the years, the laboratory facilities have been upgraded with computerised master equipment and data acquisition systems. The calibration results from the ELGi Metrology lab have been authenticated through Inter laboratory comparisons specified by NABL.
Today, our NABL accredited Metrology Department plays a crucial role in ensuring enhanced reliability and performance consistency across ELGi’s product portfolio of 400+ compressed air systems. This is in line with ELGi’s relentless focus on high quality and customer centric compressed air solutions. At ELGi, we believe in pushing the boundaries every day in our quest to be “Always Better”.
Q. Any capacity additions envisaged in your manufacturing facilities?
Our current capacity will comfortably meet customer demand for the foreseeable future. As we anticipate demand and supply uncertainty during the COVID-19 crisis, we will focus on adding flexibility to our production lines to better serve customer needs. For the long term, we will consider indigenizing production in significant markets such as the USA to further improve our lead times and to de-risk against global disruptions such as the COVID-19 crisis. Finally, we will continue to explore opportunities to improve our quality
through vertical integration.
Q. What are the industry 4.0 solutions you have implemented for smart manufacturing and enhancing productivity?
Digitalization has taken precedence across all industrial operations. Real-time data analysis, digitalized monitoring and machine learning are just some of the technologies being introduced under the concept of Industry 4.0.
Some of the industry 4.0 solutions we’ve implemented as part of our smart manufacturing focus span – automated capturing of testing data in the screw compressor and airend assembly lines, automated unit movement through shuttle systems in the portable compressor assembly line, fully automated balancing machine and gantry system in the rotor bay, and the automated assembly conveyor line for large and small airends in the airend assembly and automated oil filter assembly line. These have resulted in significant productivity enhancements across all our manufacturing facilities.
Q. The Heat Recovery System you have introduced is a path-breaking development. How are the industries benefitting from this?
ELGi’s Heat Recovery System (HRS) helps companies to recover approximately 96% of the waste heat generated during the compression process which can then be utilized for heating air (space) or water. This in turn eliminates additional equipment requirements to heat water or air, thereby eliminating the CO2 emissions to a large extent. Our Heat Recovery System (HRS) is best suited for customers across process industries spanning paper, sugar, food and beverages, dairy, textiles, etc., mainly companies who require compressed air and use hot water for their process requirements.
One of our customers, a paper mill, experienced the benefits of the HRS system, within the first few hours of installation, by way of continuous warm water availability with no external heating. With the implementation of HR 110, the customer was able to recover a heat load of ~ 89.14 kWh / 0.077 MKcal through the continuous water supply of ~2000 lit/hr at a temperature of ~70°C throughout the year. This resulted in an annual energy savings of 800~900 tonnes of LP steam and a carbon emission reduction of ~170-190 tonnes of Co2 / Yr. With the ELGi’s energy efficient compressor and heat recovery system, our client was able to achieve significant energy savings resulting in accomplishing the target stipulated by PAT Scheme I and winning the prestigious GREENCO award.
Q. You play an exemplary role in skill development, empowering women in particular. What are your HR policies helping in realizing this goal?
Women are largely under represented and underutilized in the manufacturing workforce, representing one of the largest pools of untapped talent for manufacturers all over the world. A study on Indian women in the manufacturing sector reveals that women represent only about 3% in core engineering industry, while this number stands at 12% in sectors such as electronics. At ELGi we have women leaders in almost every function, ranging from the shop floor, to design, engineering, quality and IT. They’re blazing trails and inspiring other women, every step of the way. Having said that, we have a long way to go in order to meet our diversity goals of a 50:50 gender ratio balance across the workforce.
Looking back, we rolled out a structured flexible location policy as early as 2008, becoming one of the very few manufacturing companies to have done so. We recognize that training is a critical component when it comes to building sustainable communities (not just women) for the future.
Our vocational training school conducts a 3-year program post which the graduates join our manufacturing facilities. Today’s batch has over 50% women in the class. We’re excited about being able to build diversity right at the very start of the talent pipeline. Also, a 5-day working week is a strong enabler; even our shop floor works a 5-day week. We are one of very few companies to have implemented this years ago.
Q. You have an ambitious growth plan. What are your recent initiatives to achieve your global aspirations?
To accomplish our growth goals, our strategy will include, in addition to organic growth, business acquisitions across the world with specific focus on India, Europe, USA, Australia, Indonesia and Thailand.
Our recent acquisition of Michigan Air Solutions in USA will strengthen our presence in the North American Market. We have opened our European headquarters in Belgium and we are continuing to strengthen our sales, service and channel partners’ network across Europe. On the value proposition dimension of strategy, we are focusing on innovation centered around energy efficiency and oil-free and quality to be the best in the world.
Q. What are the challenges ahead for you?
Our teams are engaged with predicting and planning for the consequences of COVID-19. Specifically, we anticipate challenges in demand, supply, employee safety, and general business continuity. As we gain more comfort around this new normal, we will refocus our attention on our strategic markets and initiatives towards CK2, our ambition to be the second largest compressed air manufacturer in the world.
Q. You also champion in your CSR activities. Could you enlighten us on some of your recent initiatives?
Well, we’re certainly committed to helping build sustainable communities for the future. The ELGi school, established in 1989, has been providing holistic and affordable education to more than 1,400 children, from the rural community in Vellalore, a panchayat town situated on the outskirts of Coimbatore city. Today, while we’re in the process of moving to a brand new campus, students from orphanages will receive free, high quality, education from pre-primary to higher secondary level. Though I’ve mentioned it earlier, the ELGi vocational training programme is a good example of how skill development can open up new doors for youngsters from underprivileged backgrounds. We’ve hired close to 200 students who have completed the three-year vocational training program.
We’re also committed to promoting fitness as a means to ward off lifestyle related diseases and promote cancer awareness. In this vein, we have been an active sponsor of the Coimbatore Marathon, the proceeds of which support the Coimbatore Cancer Foundation in its efforts to spread cancer awareness among the masses. Earlier, last year we have also sponsored the Susan G. Komen’s Race for the Cure®, a marathon focused on fundraising for advancement in breast cancer treatment.
Q. What’s your vision for ELGi?
Our CK2 aspiration to be the second largest air compressor brand continues to be our business ambition. As we emerge from the initial shock of the COVID-19 crisis, we believe that our CK2 aspiration will be a rallying cry for our employees to engage with our stakeholders towards a common goal. Our company’s vision is for ELGi to “Always be the choice everywhere”. We aspire to live up to this commitment everyday for our customers, suppliers, distributors, employees, investors, and society.
VIEW ARTICLE