Oil injected Air Compressors
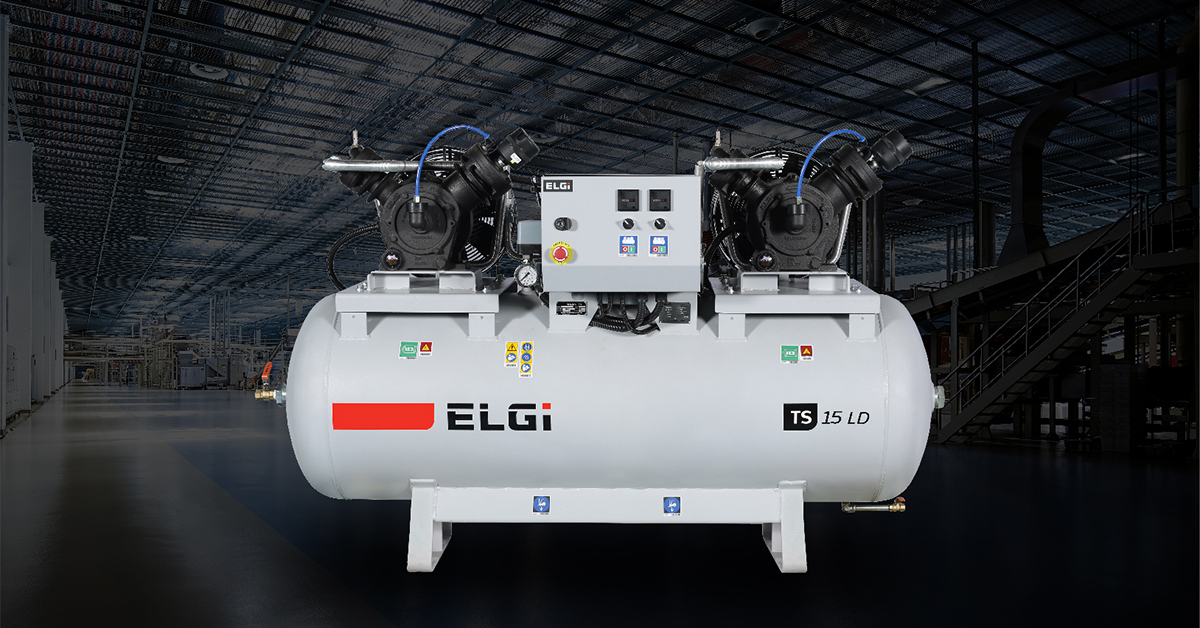
How Oil Lubricated Compressors Work and Their Role in Energy Efficiency
Oil lubricated compressors play a vital role in industries that demand a reliable and efficient compressed air supply. Known for their durability, energy efficiency, and cost-effectiveness, these compressors are particularly suitable for applications requiring continuous, high-performance air delivery. ELGi’s Oil lubricated air compressor range is designed with cutting-edge technology to meet the varied requirements of industrial applications, ensuring minimal maintenance and a low cost of ownership.
This blog explores the advantages, applications, and specifics of ELGi’s oil-lubricated screw compressors for industries across Europe, particularly for businesses seeking efficient, cost-effective solutions to their compressed air needs.
What is an Oil injected air compressor?
An oil injected air compressor, also known as an oil lubricated compressor, uses oil as a key component in the compression process to improve performance, durability, and efficiency. In these air compressors, oil is injected directly into the compression chamber, where it lubricates and cools the moving parts. This injection of oil not only reduces friction and wear but also helps to seal the compression chamber, ensuring efficient air compression.
Oil-injected compressors are commonly used in various industries where heavy-duty applications require a continuous, reliable source of compressed air. This makes them ideal for manufacturing, automotive, and other industrial applications that demand high performance and consistent output. ELGi, a leader in air compressor technology, offers a range of oil lubricated compressors, including models from the EG, EQ, EN and LD Series, each designed to meet diverse industrial needs.
How Do Oil injected air compressors Work?
An oil injected air compressor operates using a rotary-type positive displacement mechanism, usually with a screw configuration. Here’s a breakdown of the process:
- Air Intake: Atmospheric air is drawn into the compression chamber, where it’s directed towards a pair of interlocking rotors, or screws.
- Compression with Oil Injection: As the air flows through the rotors, oil is injected into the chamber. This oil serves three main purposes:
- Lubrication: It reduces friction between moving parts, such as the rotors, extending their lifespan and preventing wear.
- Cooling: ompression generates significant heat, and the oil absorbs this heat to keep the chamber’s temperature stable, preventing overheating.
- Sealing:Oil helps seal any gaps between the rotors and the chamber, improving compression efficiency by minimizing air leaks.
- Air-Oil Separation: Once the air is compressed, the oil must be separated from it before the compressed air exits the compressor. The air-oil mixture goes through an air-oil separator, where most of the oil is filtered out and recirculated back into the compressor.
- Air Discharge: The now clean, compressed air exits the compressor for immediate use or storage in a tank, depending on the system’s configuration.
- Cooling and Recirculation of Oil: The separated oil is filtered, cooled, and then recirculated into the system to repeat the process.
This method of compression makes oil-injected compressors incredibly reliable and efficient, capable of delivering a steady stream of high-quality compressed air, even under continuous, heavy-duty operation.
Applications of Oil lubricated compressors Across Industries
Oil lubricated air compressors are used across a broad range of industries, offering consistent and efficient compressed air supply for various applications:
Manufacturing and Production: In the manufacturing sector, compressed air is essential for driving tools, powering assembly lines, and supporting packaging processes. ELGi’s oil injected air compressors like the EG Series provide the continuous, reliable air supply needed to keep production lines running smoothly.
Automotive Industry: The automotive industry relies heavily on compressed air for powering tools, pneumatic systems, and painting applications. ELGi’s oil-lubricated screw compressors offer the necessary power for these tasks, enhancing efficiency in assembly and repair processes.
Food and Beverage: Compressed air is critical in bottling, sealing, and packaging within the food and beverage industry. ELGi’s compressors, especially with food-grade oil options, deliver reliable performance that supports stringent hygiene standards required in this sector.
Oil and Gas: For industries like oil and gas, which require robust equipment, oil lubricated compressors such as ELGi’s EQ Series handle demanding tasks, from offshore drilling to pipeline maintenance.
Chemical Industry: In the chemical industry, compressed air powers instruments, control systems, and various pneumatic tools. The lubricated screw compressor design provides the necessary air quality and reliability for these critical applications.
Woodworking Industry: Woodworking requires precise tools that rely on compressed air for cutting, shaping, and finishing tasks. ELGi’s EN Series compressors, with their compact design and efficient air delivery, are ideal for woodworking applications, ensuring smooth operations.
ELGi Oil Lubricated Compressor Models
ELGi offers a range of electric lubricated screw air compressors, each tailored for specific industry needs. Here’s a closer look at some of the top models:
EG Series Screw Air Compressors: The EG Series is designed with durability and ease of maintenance in mind. These compressors feature a quiet operation, which is advantageous for environments where noise control is essential. The EG Series uses advanced air-oil separation to reduce oil carryover, ensuring high-quality compressed air delivery, while its VFD technology offers substantial energy savings.
EG Series Screw Air Compressors: The EG Series is designed with durability and ease of maintenance in mind. These compressors feature a quiet operation, which is advantageous for environments where noise control is essential. The EG Series uses advanced air-oil separation to reduce oil carryover, ensuring high-quality compressed air delivery, while its VFD technology offers substantial energy savings.
EQ Series Screw Air Compressors (11–45 kW): Known for reliability and minimal maintenance requirements, the EQ Series offers unmatched performance for medium to large applications. It’s ideal for industries with high air demands, as it can maintain continuous air flow under demanding conditions. The EQ Series stands out as a robust choice for SMEs looking for a low total cost of ownership.
EN Series Screw Air Compressors (2.2–15 kW): The EN Series is compact and efficient, designed to fit in space-limited environments. It provides reliable air supply for small to medium applications, particularly in manufacturing and assembly settings. The EN Series minimises operational costs and pressure losses, which makes it an economical choice for smaller businesses in Europe.
LD Series Two-Stage Reciprocating Compressors: The LD Series combines direct drive efficiency with advanced two-stage reciprocating technology, offering high reliability for carpentry, automotive services, and general manufacturing. With motor power ranging from 2.2 kW to 11 kW, these compressors deliver optimal performance and durability for diverse industrial needs.
The Impact of Oil injected air compressors on the Global Energy Mix
Oil injected air compressors play a significant role in the global energy landscape due to their widespread use across industries, contributing to the overall energy demand. In industrial sectors, compressed air can represent up to 10% of a facility's total electricity consumption, and in some manufacturing plants, this figure may be even higher. This highlights the importance of energy efficiency in air compressors, as even small improvements in efficiency can have a sizable impact on global energy consumption. Learn more about electric lubricated screw compressors application in various industries.
As the global focus shifts towards energy conservation and sustainable practices, the demand for energy-efficient oil lubricated compressors has grown. ELGi’s compressors, such as the EG Series with Variable Frequency Drive (VFD), are designed to dynamically adjust power use based on air demand, optimizing energy consumption and reducing operating costs. For large-scale industries across Europe and beyond, these efficiency improvements translate into reduced energy costs and a smaller carbon footprint, supporting global sustainability goals.
By reducing power requirements, these compressors contribute to a shift towards greener energy use, helping countries meet emission reduction targets while maintaining industrial productivity.
Why is Efficiency Important in Oil injected air compressors?
Efficiency is crucial in oil injected air compressors for several reasons, impacting not only the operational costs of individual businesses but also broader economic and environmental factors.
Cost Savings: Energy-efficient compressors like ELGi’s lubricated screw compressors use less electricity, which translates to significant cost savings for businesses.
Reduced Environmental Impact: Energy-efficient compressors reduce power consumption, contributing to a lower carbon footprint. This is especially important as companies across Europe strive to comply with strict environmental regulations and reduce their environmental impact. By using an oil lubricated air compressor with optimized efficiency, businesses can help support a greener, more sustainable future.
Longevity and Reliability: Efficient compressors tend to operate with less stress on components, which extends the equipment's lifespan. By maintaining optimal performance, efficient compressors require fewer repairs and experience less downtime, leading to a more reliable compressed air system.
Adaptability to Variable Demand: Industries with fluctuating air demands benefit greatly from efficient compressors equipped with technologies like VFD, which adjusts the compressor’s power based on real-time requirements. ELGi’s electric lubricated screw air compressors with VFD technology adapt dynamically, allowing facilities to save energy by operating only at necessary power levels, thus reducing wear and maximizing energy efficiency.
Compliance with Energy Standards: Many regions, especially in Europe, have strict energy standards that industrial equipment must meet. High-efficiency oil injected compressors help companies adhere to these regulations, avoiding penalties and maintaining compliance with environmental and energy guidelines.
Conclusion
In industries that rely heavily on compressed air, such as manufacturing, automotive, and food processing, the role of an efficient oil injected air compressor cannot be overstated. These compressors provide the necessary durability, efficiency, and cost-effectiveness for demanding applications. ELGi’s range of oil lubricated air compressors, including the EG, EQ,EN and LD Series, offers tailored solutions to meet the diverse needs of industrial sectors, with a strong emphasis on energy efficiency, reliability, and operational cost savings.
With ELGi’s advanced oil lubricated compressors, businesses in Europe can achieve operational excellence while contributing to a more sustainable future. Contact ELGi today!
RELATED BLOGS
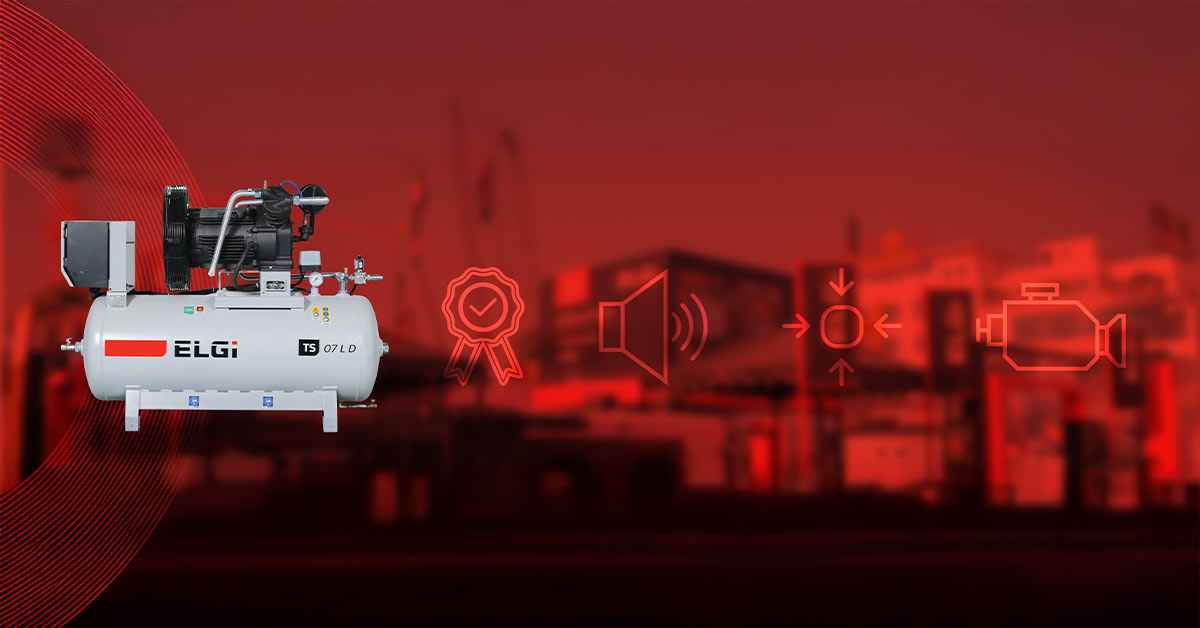
Compressed air is a critical element in many industrial operations, from powering tools to...
Read More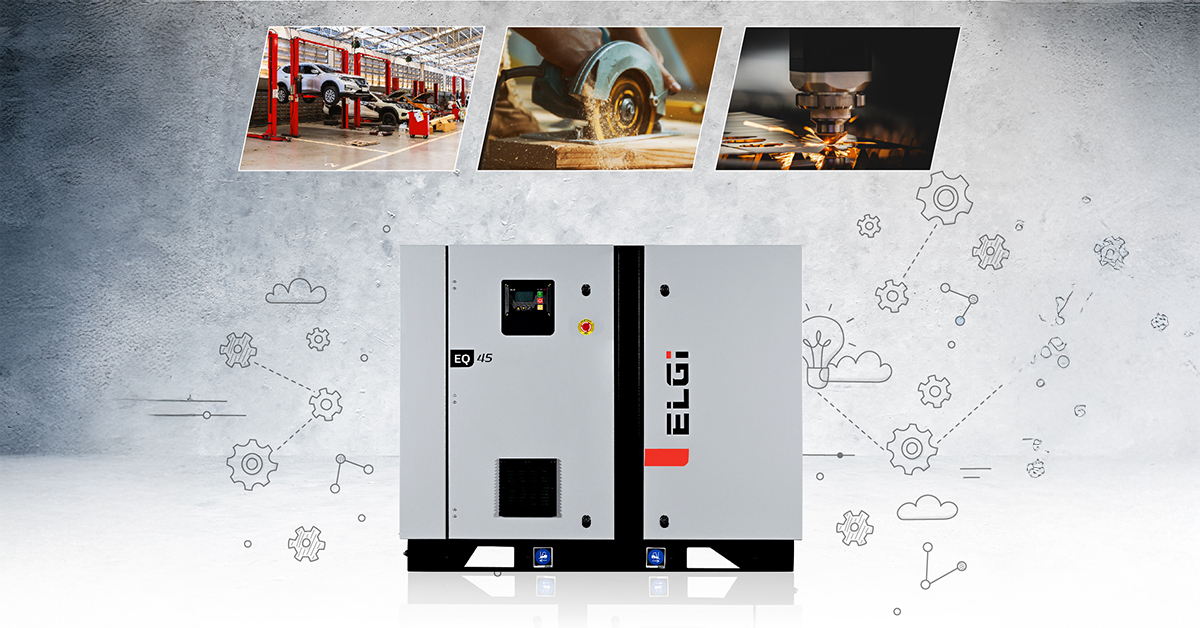
Why the ELGi EN Series is Ideal for Compact Industrial Compressed Air Solutions Busine...
Read More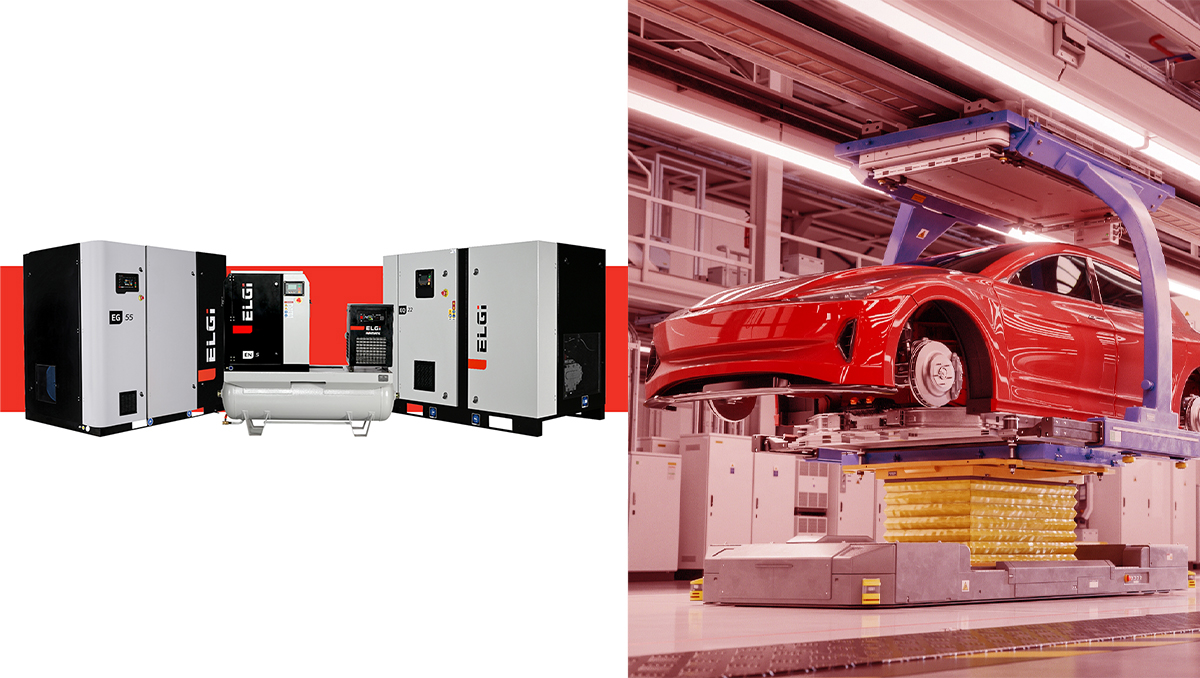
Compressed air is an invaluable resource in the automotive industry, powering everything f...
Read More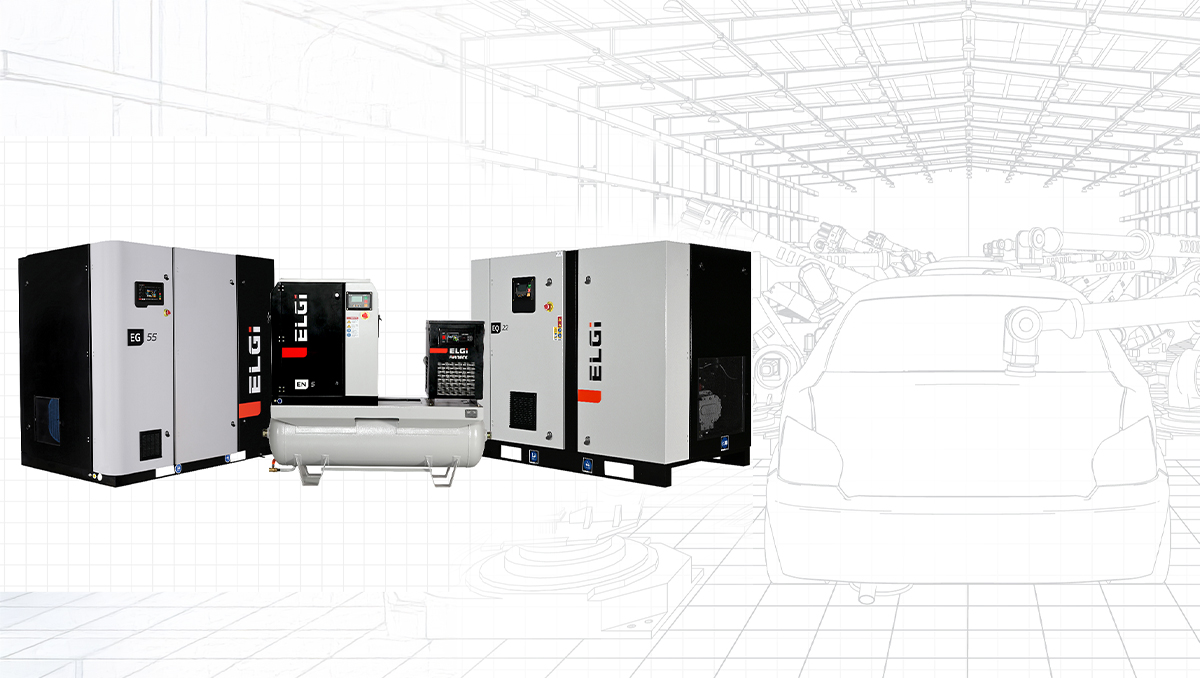
The automotive industry is one of the most dynamic and technology-driven sectors, requirin...
Read More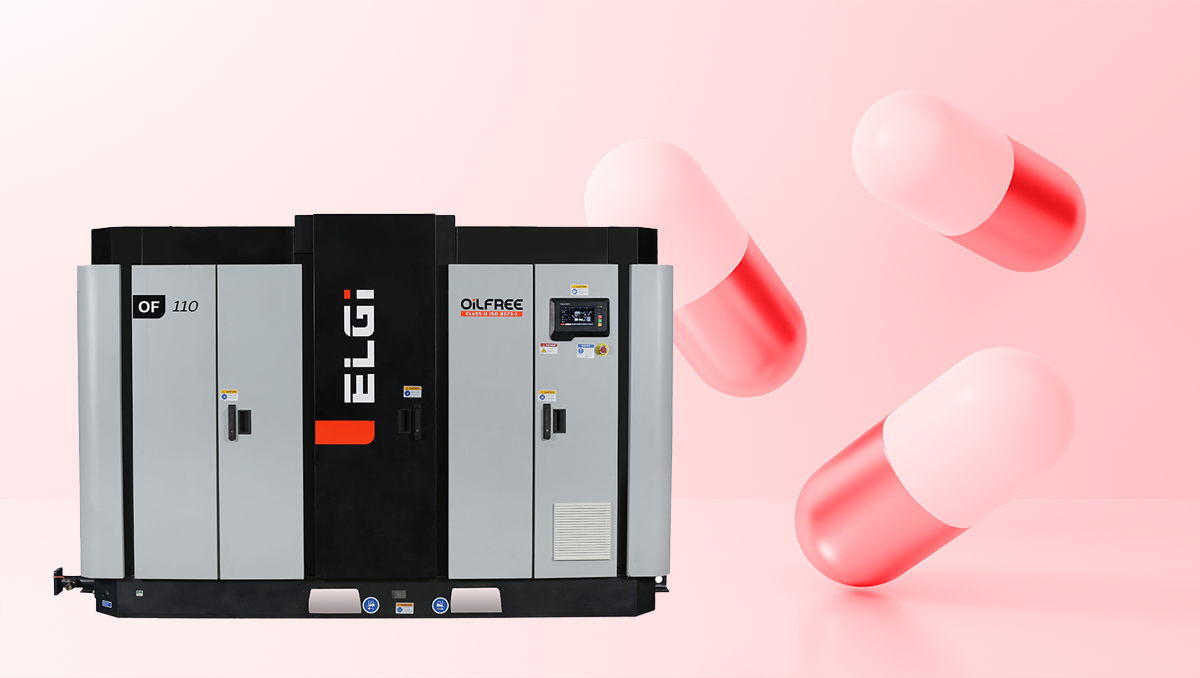
The pharmaceutical industry operates in a realm where precision, purity, and compliance ar...
Read More
Rotary screw air compressors are essential machines used in many industrial applications a...
Read More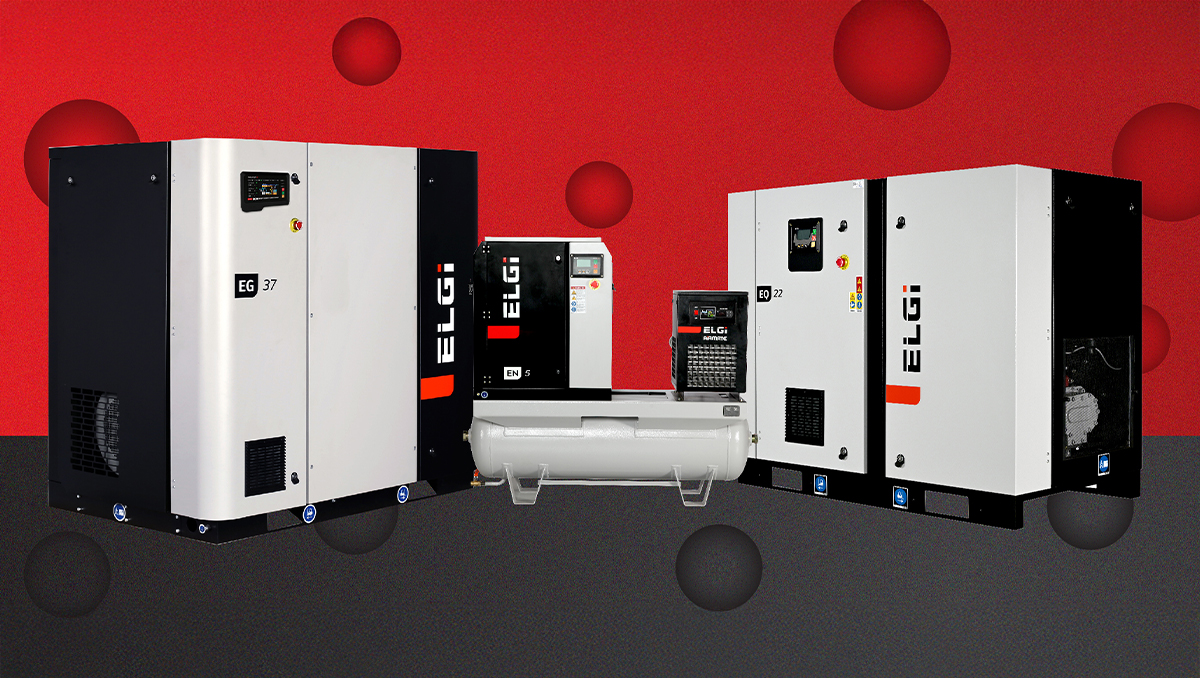
Choosing the right rotary screw compressors is crucial for your industrial operations. In...
Read More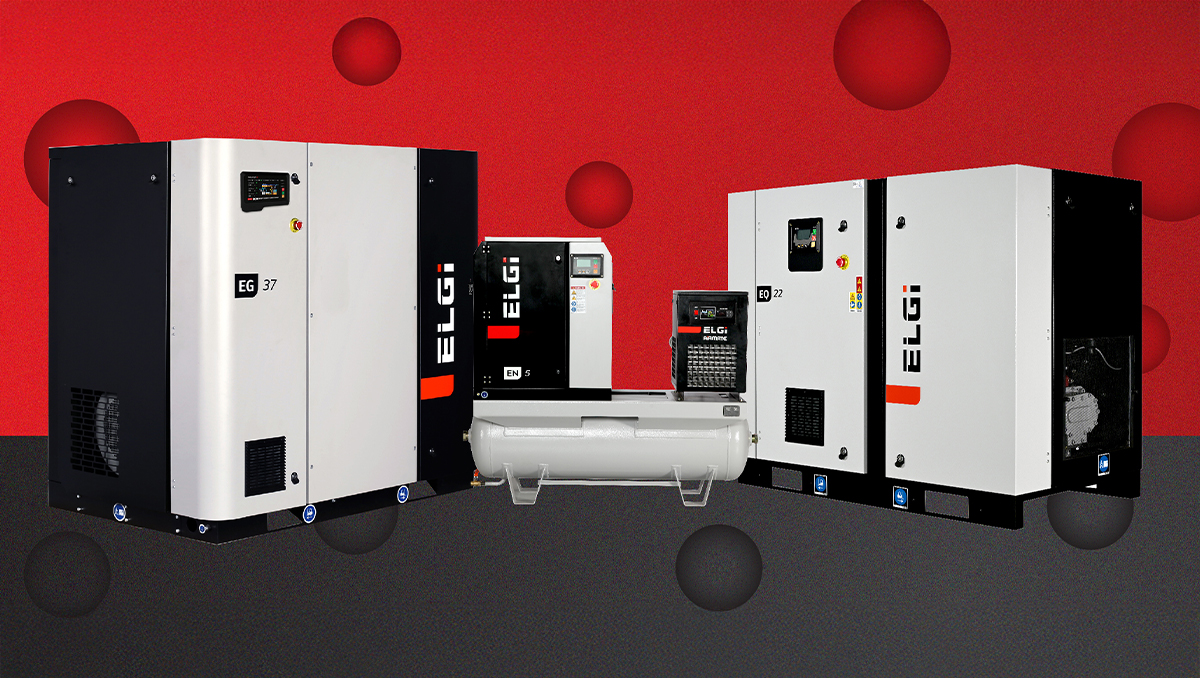
Choosing the right rotary screw compressors is crucial for your industrial operations. In...
Read More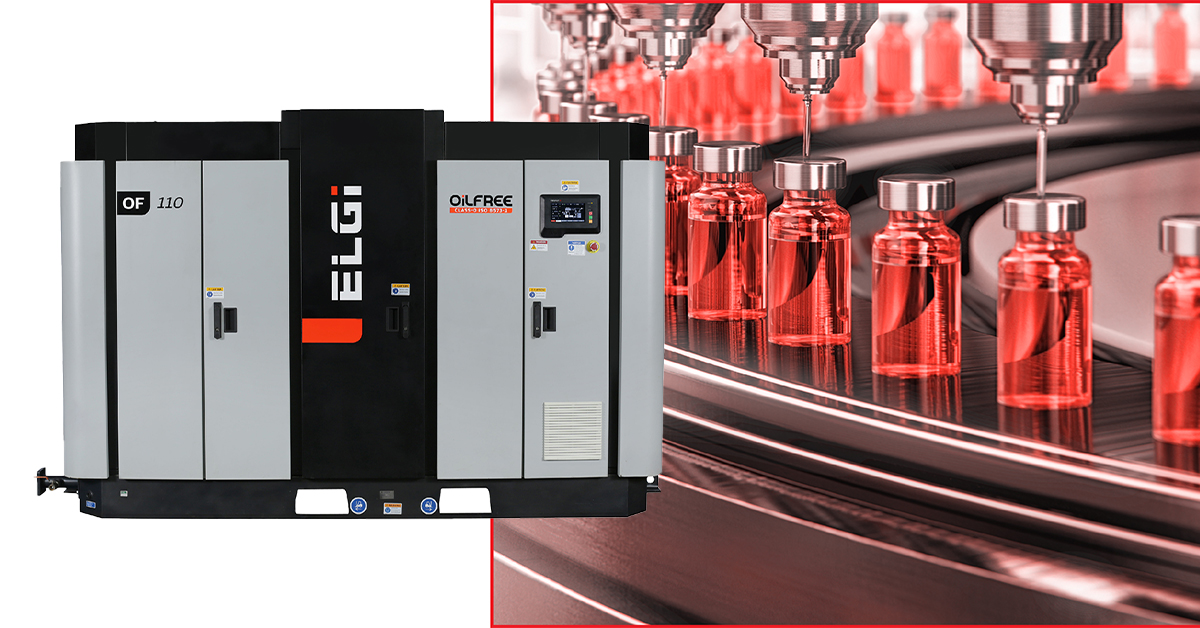
The pharmaceutical industry relies heavily on precision, sterility, and efficiency in ever...
Read More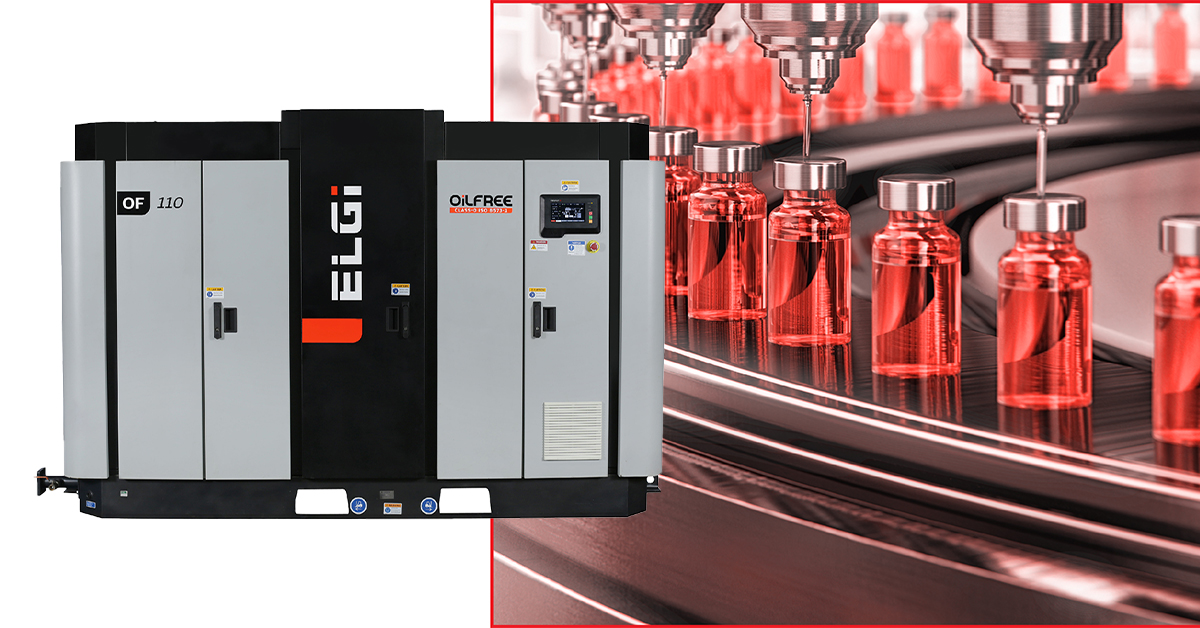
De farmaceutische industrie is sterk afhankelijk van precisie, steriliteit en efficiëntie...
Read MoreBe the first to get updates, learn more and join our explorative world by subscribing to our official compressed air journal.
SUBSCRIBE