Oil-Free or Oil-Lubricated Screw Compressors: ELGi’s Guide to Choose the Right Technology for Your Application
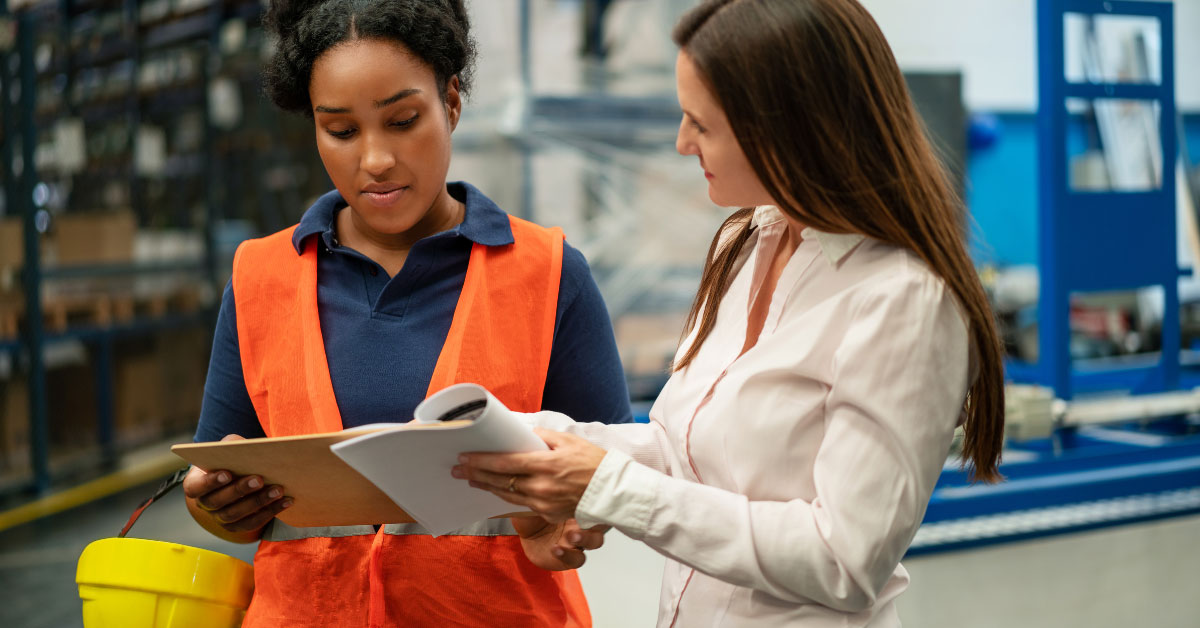
About Oil-Lubricated Air Compressors
Oil-injected compressors are frequently used in industrial, manufacturing, and small workshop environments. Within the compressed air system, these compressors use oil for lubrication, sealing, and cooling. This procedure causes a small amount of oil contamination in the air supply. With the use of air filters, ELGi offers options to deliver high-quality air. In order to reach Class 1 air purity standards for oil-lubricated screw air compressors, it is possible to install air filters and oil filters, and other compressed air accessories. However, for the highest air purity, it is recommended to use oil-free screw air compressors.
Importance of Oil-Free Compressors in Critical Applications: Maintaining Air Purity and Performance
Even minor oil contamination can lead to significant consequences for critical applications like food production and chemical or medical processes. For such situations, opting for an oil-free setup becomes crucial. These machines come at a higher cost compared to oil-lubricated ones, as oil-free compressors require a distinct cooling system due to the absence of oil for lubrication and cooling. These systems often rely on advanced air and water cooling methods to maintain optimal operating temperatures and ensure efficient compressor performance.
Oil-Free Air Compressors vs. Oil-Injected Air Compressors: Choosing the Right Solution for Your Needs
Air compressors are essential in various industries, playing an important role in generating compressed air for a wide range of applications. When selecting an air compressor, one of the fundamental decisions is whether to go with an oil-free or oil-injected model.
ELGi has some suggestions to facilitate your decision. There are some main criteria to look at when considering oil-free air compressors or oil-lubricated air compressors:
- Specific Application
- Air Quality
- Reduction in Maintenance Requirements
- Noise
- Initial cost and operating expenses
- Environmental considerations
Air Quality Required for your Application
When choosing the right air compressor technology for your application, one of the most important considerations is the compressed air quality, especially when comparing systems with the same nominal power and outlet delivery (flow rate, pressure, temperature). This is governed by Air Quality Standard ISO 8573-1, measuring the size and amount of contaminants, such as oil, dust, and water, in the compressed air.
ISO 8573-1 establishes seven sub-classes of air quality. For most applications, Class 2 air quality or lower is preferred due to higher traces of oil content in Class 3 and above. In applications where monitoring the oil content is critical, there's the choice between Class 1 and Class 0, with Class 0 representing the highest air quality standard achievable.
For an industry-specific overview, the following recommendations can be considered:
General Applications: Class 2 air quality is commonly suitable for industries with regular air quality needs.
Sensitive Applications: For applications with strict air quality requirements, choosing Class 1 or Class 0 is essential. Class 0 is the superior choice for the best air quality.
Oil-Free Environments: Industries like pharmaceuticals, food production, and electronics often require Class 0 air quality due to their zero tolerance for oil contamination.
Reduction in Maintenance Costs:
Comparing the two different technologies with each other, an oil-free screw air compressor’s purchase price would be higher compared to an oil-lubricated screw air compressor. An oil-free compressor tends to have a higher initial cost due to their specialized design and manufacturing processes. However, the oil-free technology offers a reduction in maintenance requirements and costs since oil is solely necessary for lubricating internal compressor parts rather than the airend. This could lead to decreased long-term operating expenses due to improved air system efficiency and lower maintenance demands. Generally, oil-lubricated compressors have a lower initial cost. However, operating expenses may be higher due to ongoing maintenance and oil purchases. Additionally, oil-lubricated compressed air systems also require more piping and compressed air accessories, such as dryers and filters, risking more leakage or necessary parts replacements within the compressed air system.
Noise of Screw Air Compressors:
Finally, there is the noise. Due to the dry technology, oil-free screw compressors would have a slightly higher noise level compared to oil-lubricated screw air compressors. Depending on the location of the compressor in the factory, the noise level can be an important criterion when choosing the right air compressor for your application. If you need a quieter environment, consider oil-lubricated compressors, as they're designed to be less noisy and produce less vibration. Because of the thorough lubrication, they produce less noise or heat. In industries where air quality is of utmost importance and an oil-free compressor is an absolute necessity, ELGi also offers an alternative version to the dry screw technology known as the AB Series oil-free compressor.
So, which technology should you choose? In short, it's not easy to definitively say one is better than the other, as it depends on your specific needs. For instance, if you run a general manufacturing business with a 24/7 screw compressor, needing ISO 8573-1 Class 1 compressed air, and your compressor is close to employees, an oil-lubricated screw air compressor with filtration could be the right choice to safeguard your air system. On the other hand, if you're a pasta manufacturer seeking highly pure air (ISO8573-1 Class 0) and aiming to reduce maintenance costs, an oil-free screw air compressor might be the better option.
For several years, the pharmaceutical industry has seen water injected oil free compressors as a highly efficient alternative to traditional oil-free, dry screw two-stage compressors. It delivers the same ‘Class 0’ compressed air in a much simpler, one stage design whereby water is injected into the air-end as opposed to oil thereby cooling it down and sealing the system.
Consequently, the compressor and air-end are running at a much lower speed than a dry screw compressor, which translates in increased reliability, lower parts wear, less maintenance and better energy efficiency.
Still not sure what technology to choose? Contact our ELGi compressed air experts.
RELATED BLOGS
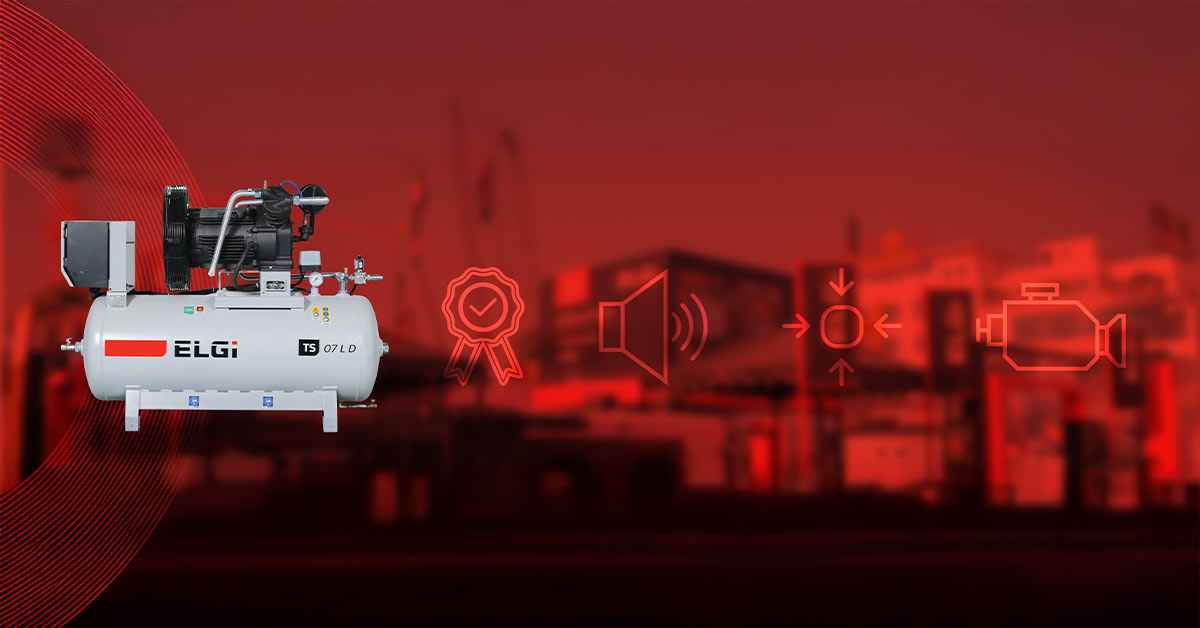
Compressed air is a critical element in many industrial operations, from powering tools to...
Read More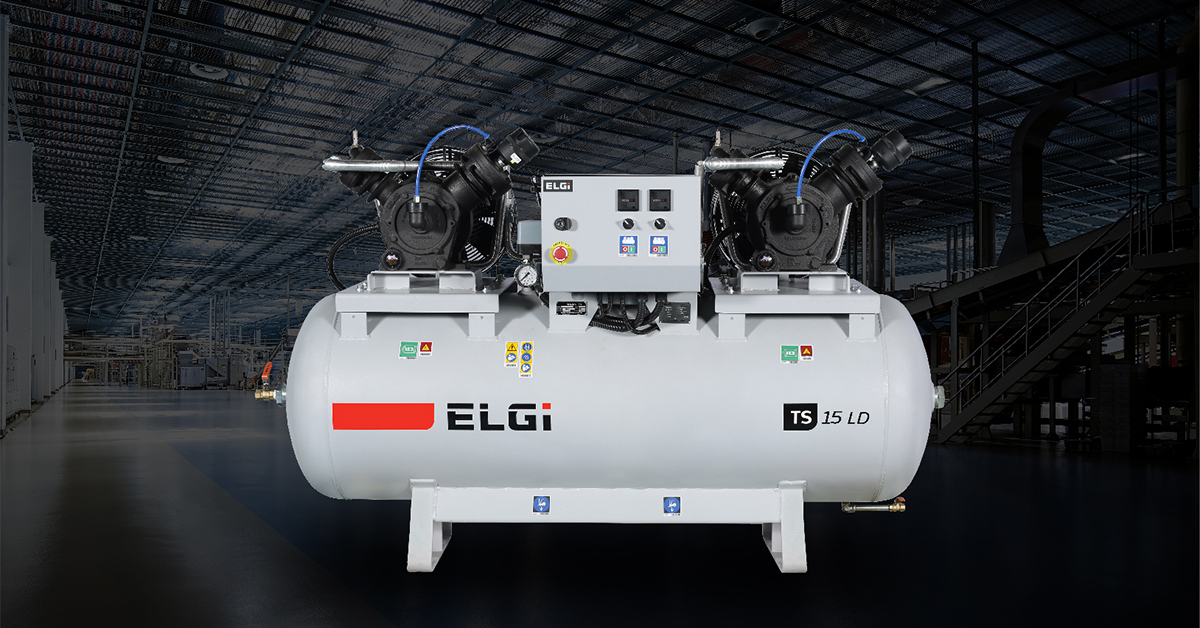
How Oil Lubricated Compressors Work and Their Role in Energy Efficiency Oil lubricated ...
Read More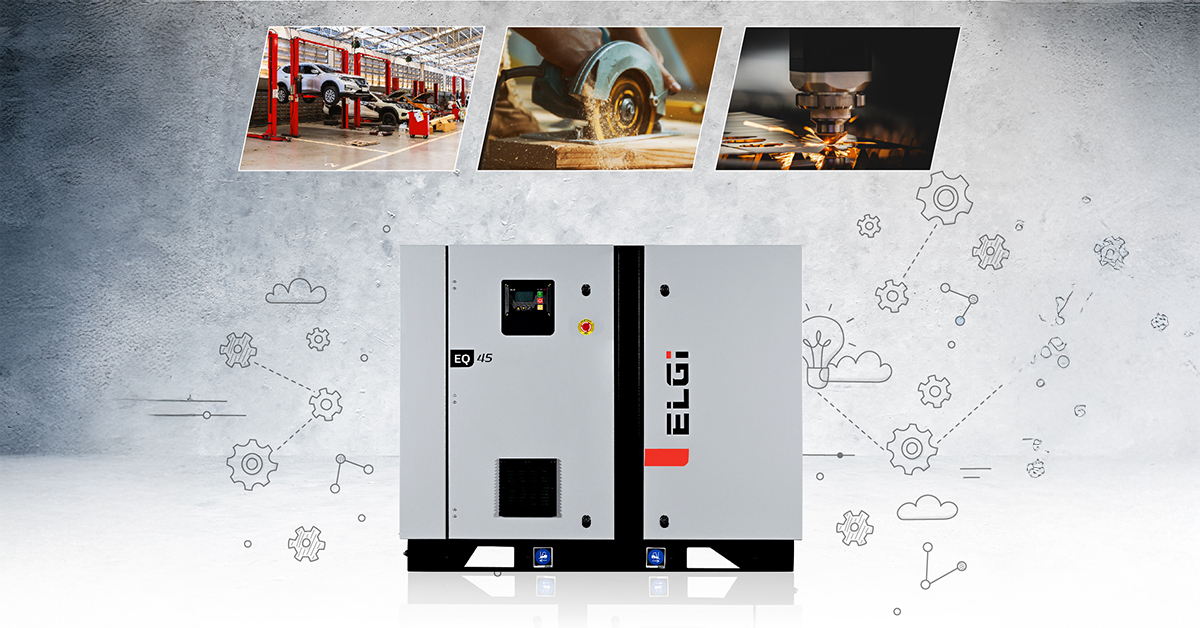
Why the ELGi EN Series is Ideal for Compact Industrial Compressed Air Solutions Busine...
Read More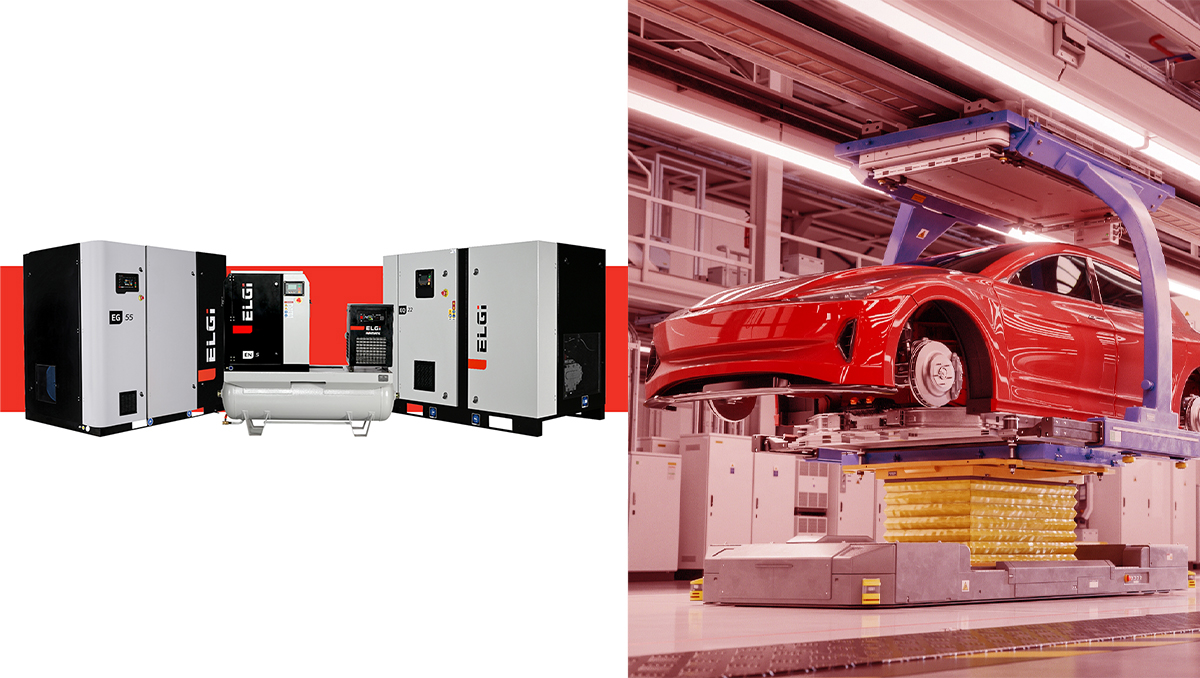
Compressed air is an invaluable resource in the automotive industry, powering everything f...
Read More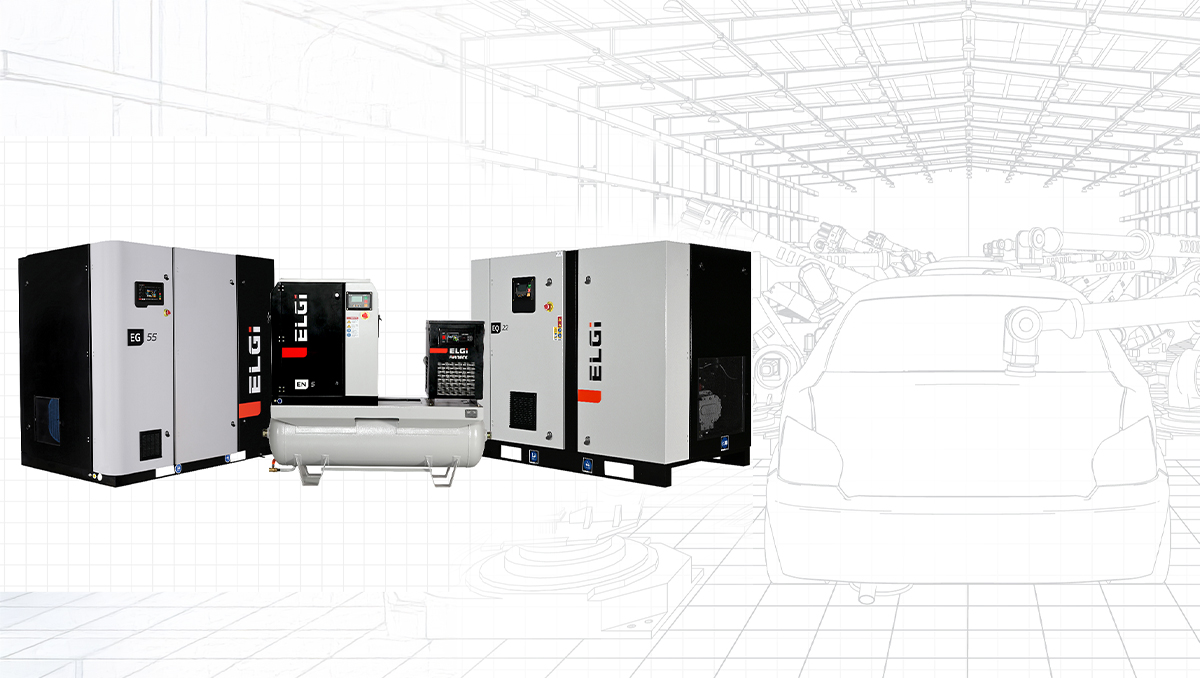
The automotive industry is one of the most dynamic and technology-driven sectors, requirin...
Read More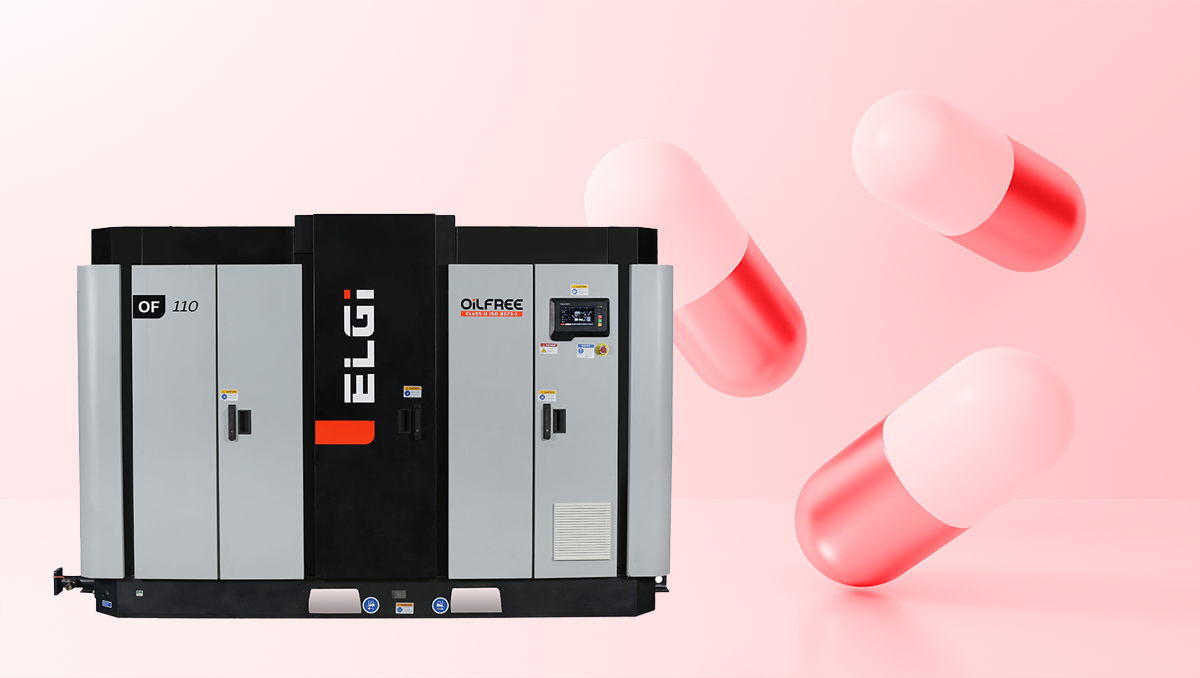
The pharmaceutical industry operates in a realm where precision, purity, and compliance ar...
Read More
Rotary screw air compressors are essential machines used in many industrial applications a...
Read More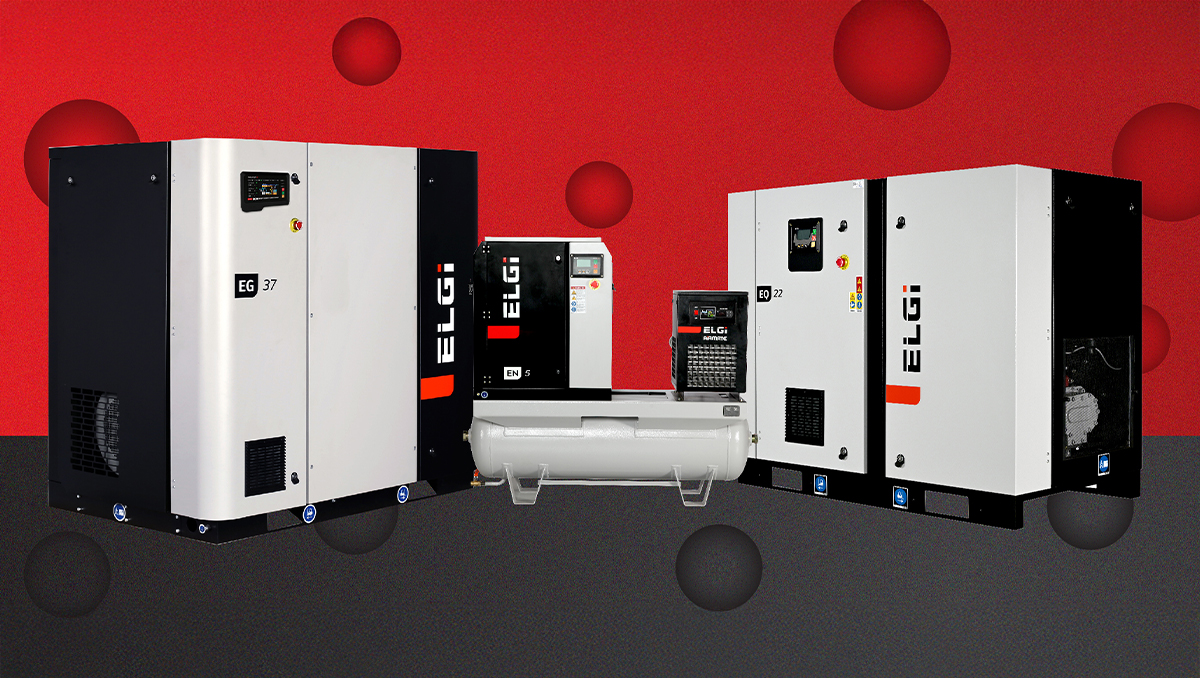
Choosing the right rotary screw compressors is crucial for your industrial operations. In...
Read More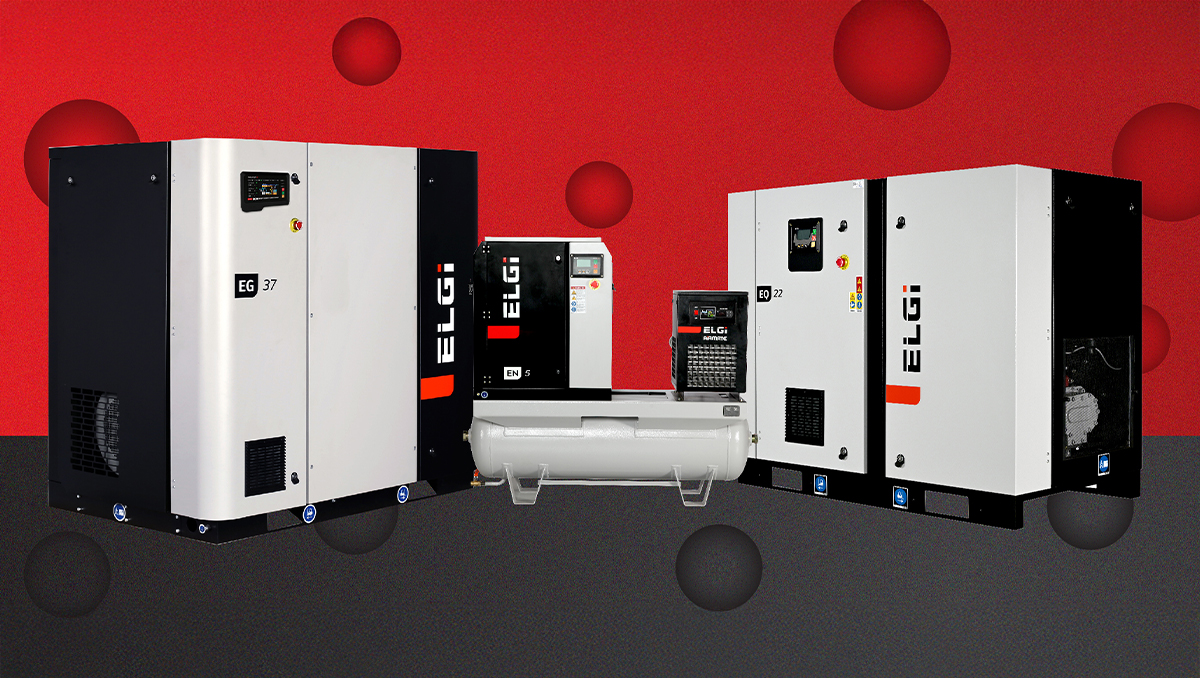
Choosing the right rotary screw compressors is crucial for your industrial operations. In...
Read More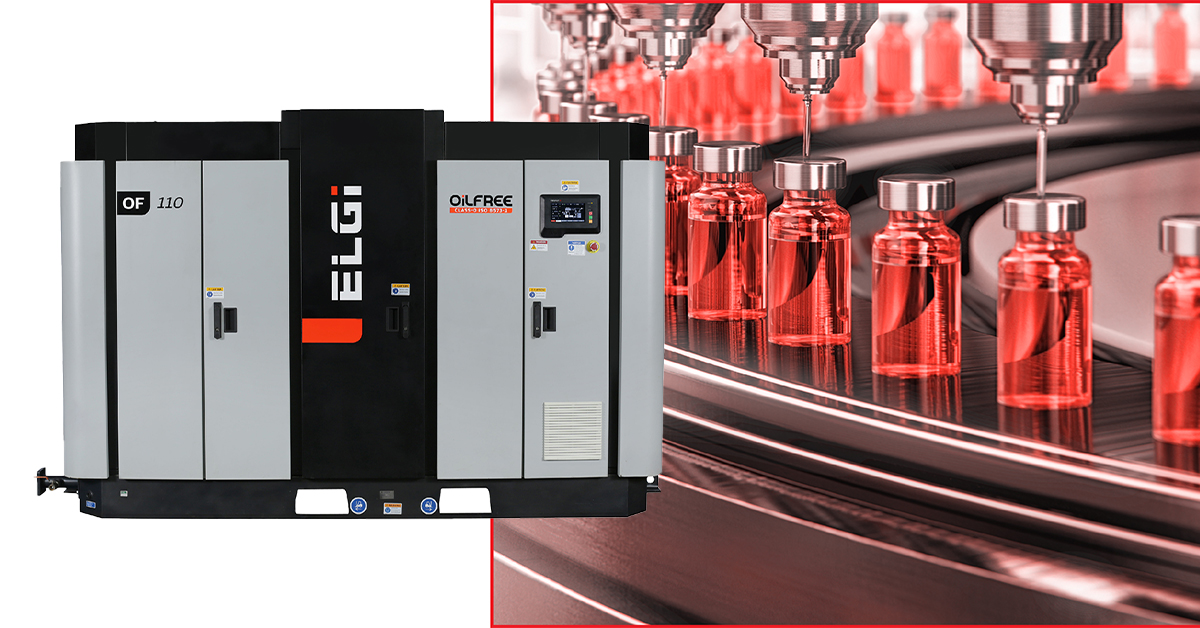
The pharmaceutical industry relies heavily on precision, sterility, and efficiency in ever...
Read MoreBe the first to get updates, learn more and join our explorative world by subscribing to our official compressed air journal.
SUBSCRIBE