Importance of ISO8573-1 Class ‘0’ oil-free compressed air for the Pharma Industry
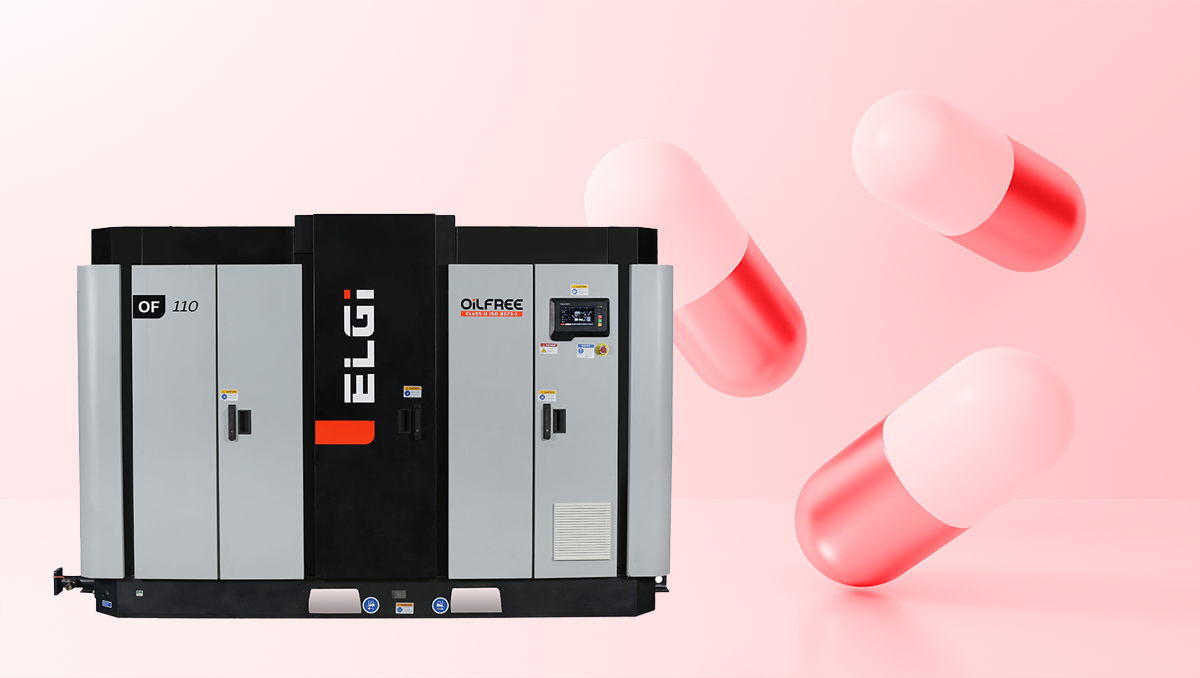
The pharmaceutical industry operates in a realm where precision, purity, and compliance are paramount. At every stage of production from formulation to packaging, ensuring uncontaminated environments is critical. Among the various tools enabling this, compressed air systems hold a unique position. For pharmaceutical applications, the golden standard is ISO 8573 class ‘0’ oil-free compressed air, ensuring the highest purity levels essential for safety and compliance. In this blog, we delve into why ISO 8573 class ‘0’ is crucial for pharmaceutical manufacturing and how it supports the compressed air pharmaceutical sector.
What is ISO 8573 class ‘0’ Certification?
ISO 8573-1 is an internationally recognised standard that specifies the permissible levels of contamination in compressed air. It classifies air purity across several categories, including oil, particles, and water content. Class ‘0’ is the highest achievable purity level, more stringent than Class ‘1’.
Why Class ‘0’ Matters:
Minimal Risk of Oil Contamination: Class ‘0’ ensures that compressed air is free of oil particles or vapours, making it suitable for sensitive applications.
Compliance with Pharmaceutical Standards: Meets stringent regulatory requirements, safeguarding product integrity.
Uncompromising Air Quality: Class ‘0’ guarantees clean compressed air, vital for contamination-sensitive industries like pharmaceuticals.
The Role of Clean Compressed Air in the Pharmaceutical Industry
Compressed air is an indispensable utility in pharmaceutical manufacturing. However, the compressed air quality directly impacts the safety, efficacy, and compliance of pharmaceutical products. Here’s how clean compressed air pharmaceutical supports operations:
Product Safety: Pharmaceutical products require uncontaminated environments during manufacturing. Compressed air that meets ISO 8573-1 class ‘0’ ensures minimal risk of contamination, maintaining product safety and efficacy.
Regulatory Compliance: Pharmaceutical regulations demand stringent compressed air quality standards to prevent product recalls and safeguard public health. Clean compressed air for pharmaceutical operations ensures compliance with these standards.
Protecting Critical Equipment: Oil contamination can damage sensitive manufacturing tools, increasing maintenance costs and downtime. Using oil-free compressed air minimises equipment wear and prolongs operational life.
Applications of ISO 8573-1 class ‘0’ Compressed Air in Pharmaceuticals
Compressed air plays a vital role in various pharmaceutical processes, each demanding the highest levels of air purity:
Capsule and Tablet Production: Compressed air is used throughout tablet production, including mixing, granulation, coating, and packaging. Class ‘0’ compressed air ensures that oil contamination doesn’t compromise product quality.
Packaging Operations: Blister packs, vials, and containers are cleaned and dried using compressed air. ISO 8573-1 class ‘0’ compressed air guarantees sterility and prevents moisture-related spoilage.
Instrumentation and Automation: Compressed air powers valves, conveyors, and other automated systems essential for precise pharmaceutical manufacturing. Clean air ensures seamless operations without oil contamination risks.
Fermentation Processes: Sterile compressed air is used to aerate fermenters in drug manufacturing. Class ‘0’ compressed air ensures no microbial contamination, vital for producing high-quality biopharmaceuticals.
Drying of Medicines: Compressed air assists in vacuum drying processes, ensuring moisture removal from products like tablets, syrups, and gels.
Benefits of ISO 8573-1 class ‘0’ Compressed Air for Pharmaceuticals
The pharmaceutical sector demands air purity levels that leave no room for compromise. Here are the core benefits of using ISO 8573-1 class ‘0’ compressed air:
Guaranteed Product Integrity: Class ‘0’ compressed air ensures that products remain untainted by oil or other contaminants, protecting their efficacy and safety.
Reduced Downtime and Maintenance Costs: Oil-free compressed air eliminates the risk of contamination-related equipment failure, reducing cleaning and maintenance efforts.
Regulatory Confidence: Compliance with ISO 8573-1 class ‘0’ standards ensures that pharmaceutical manufacturers meet stringent industry regulations with ease.
Environmentally Friendly Operations: Class ‘0’ air compressors, like ELGi’s oil-free models, reduce environmental impact by eliminating oil disposal and lowering energy consumption.
Enhanced Brand Reputation: Pharmaceutical companies using clean compressed air build trust with regulators, customers, and stakeholders, reinforcing their commitment to quality.
Why Choose ELGi’s ISO 8573-1 class ‘0’ Compressed Air Solutions?
ELGi is a trusted leader in compressed air technology, offering cutting-edge solutions tailored to pharmaceutical applications. ELGi’s oil-free air compressors deliver clean compressed air for pharmaceutical manufacturing, ensuring compliance, efficiency, and reliability.
ELGi’s Oil-Free Compressor Series:
AB Series Oil-Free Rotary Compressors:
- 100% ISO 8573-1 class ‘0’ certified.
- Incorporates proprietary rotor technology for superior performance.
- Designed for minimal lifecycle costs.
OF Series Two-Stage Compressors:
- Ensures consistent delivery of oil-free compressed air.
- Features advanced coatings to maintain air purity.
- Built for energy efficiency and durability.
Key Advantages of ELGi’s Class ‘0’ Air Compressors:
Unmatched Air Purity: Guaranteed oil-free air for contamination-sensitive applications.
Energy Efficiency: Proprietary technology reduces energy consumption, lowering operational costs.
Durability: Built to last with minimal maintenance requirements.
Compliance and Certification: Fully certified to meet ISO 8573-1 class ‘0’ and ISO 8573-7 microbial safety standards (for ELGi’s AB Series).
Optimising Compressed Air Systems for Class ‘0’ Compliance
Achieving and maintaining Class ‘0’ compliance involves more than just selecting the right air compressor. Here’s how pharmaceutical companies can optimise their compressed air systems:
Regular Maintenance: Scheduled servicing ensures compressors operate at peak performance. ELGi’s maintenance plans include health checks, timely filter replacements, and air quality monitoring.
Implement Air Audits: Conduct periodic air audits to identify inefficiencies and optimise system performance. ELGi’s experts help companies achieve maximum energy savings.
Monitoring Compressed Air Quality: Install compressed air quality sensors to continuously monitor for contaminants, ensuring compliance with ISO standards.
Customised Solutions: Use ELGi’s tailored service plans to align your compressed air system with your specific manufacturing needs.
Future Trends in Clean Compressed Air for Pharmaceuticals
As pharmaceutical manufacturing evolves, the demand for advanced compressed air systems continues to grow. Future trends include:
Smart Compressors: Advanced IoT-enabled compressors that monitor performance and predict maintenance needs.
Sustainability Initiatives: Increased emphasis on energy-efficient solutions to reduce environmental impact.
Stricter Regulations: Enhanced compressed air quality standards to ensure better product safety.
ELGi remains at the forefront of innovation, offering state-of-the-art solutions to meet these emerging challenges.
Conclusion
For the pharmaceutical industry, air purity is non-negotiable. ISO 8573 class ‘0’ compressed air ensures the highest levels of cleanliness, supporting safe, efficient, and compliant operations. From protecting product integrity to reducing maintenance costs, the benefits of clean compressed air in pharmaceutical manufacturing are vast.
ELGi’s oil-free compressors are engineered to deliver reliable, energy-efficient, and Class ‘0’ certified compressed air, making them the ideal choice for pharmaceutical companies across Europe. Invest in ELGi’s solutions to guarantee the purity and performance of your compressed air system and safeguard the future of your operations.
Achieve excellence in pharmaceutical manufacturing with ELGi’s cutting-edge Class ‘0’ compressed air systems.
RELATED BLOGS
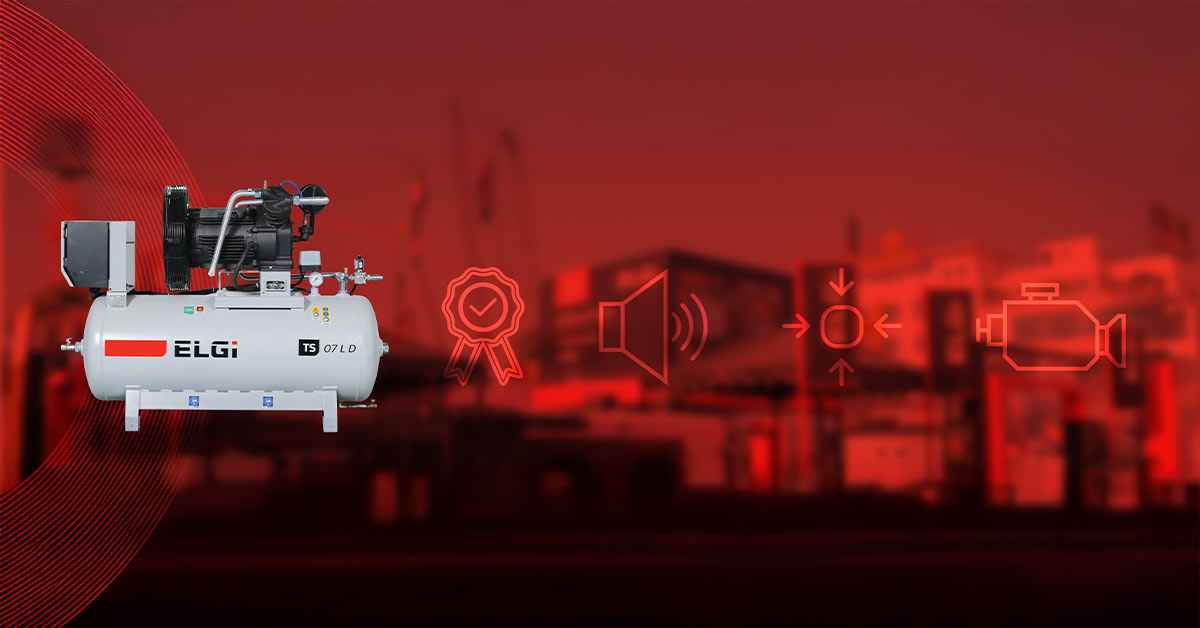
Compressed air is a critical element in many industrial operations, from powering tools to...
Read More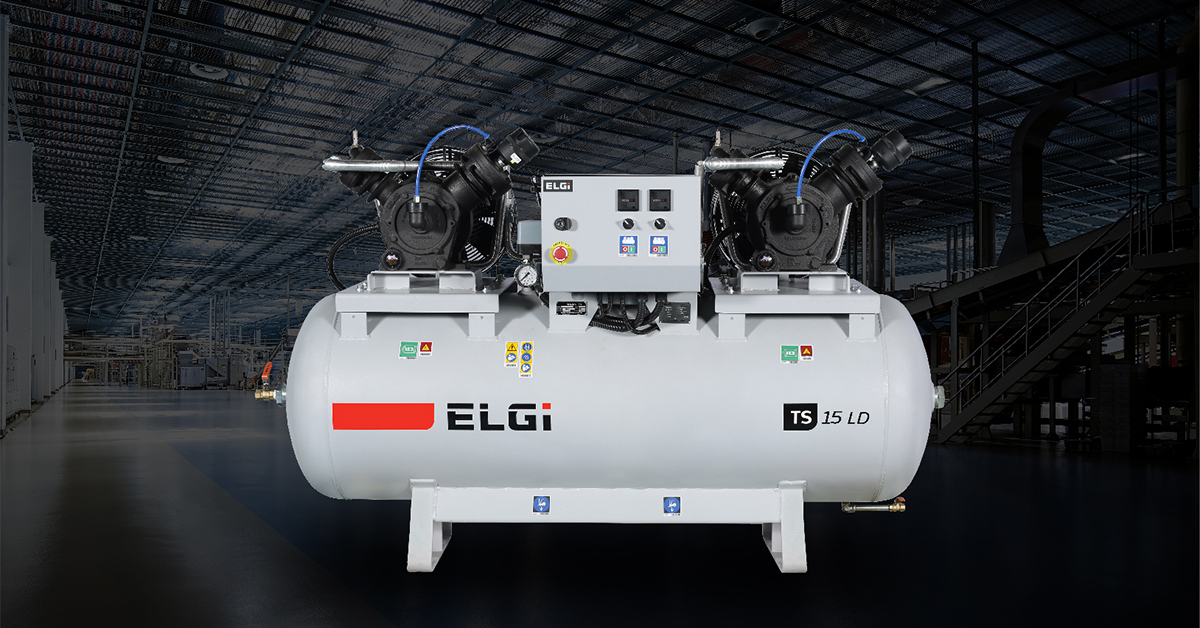
How Oil Lubricated Compressors Work and Their Role in Energy Efficiency Oil lubricated ...
Read More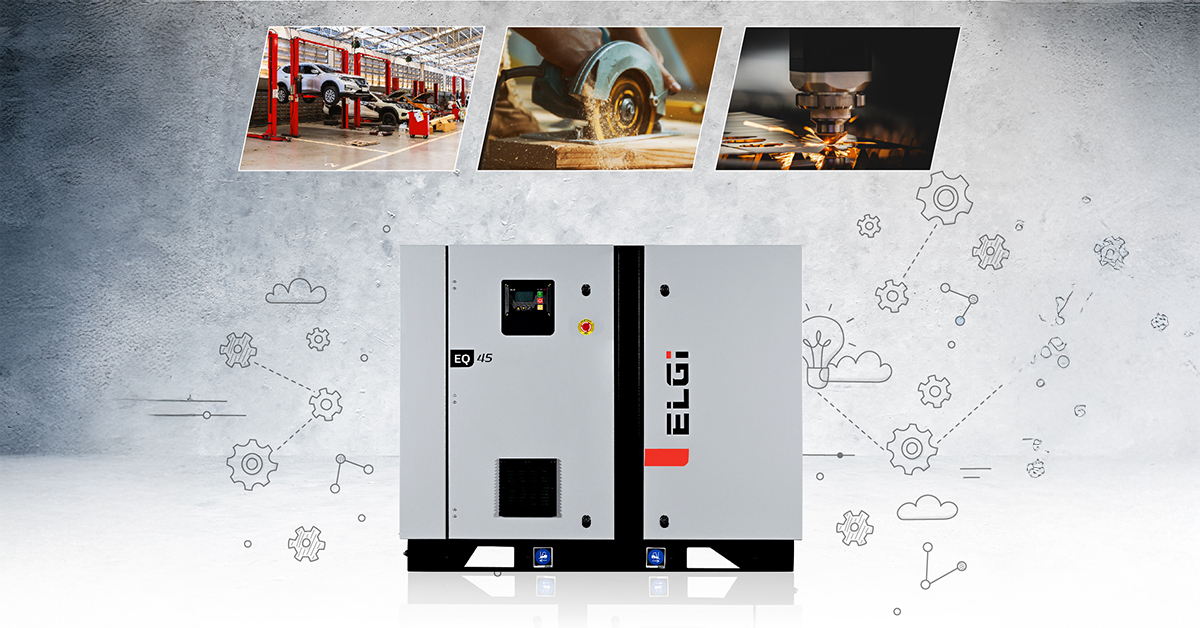
Why the ELGi EN Series is Ideal for Compact Industrial Compressed Air Solutions Busine...
Read More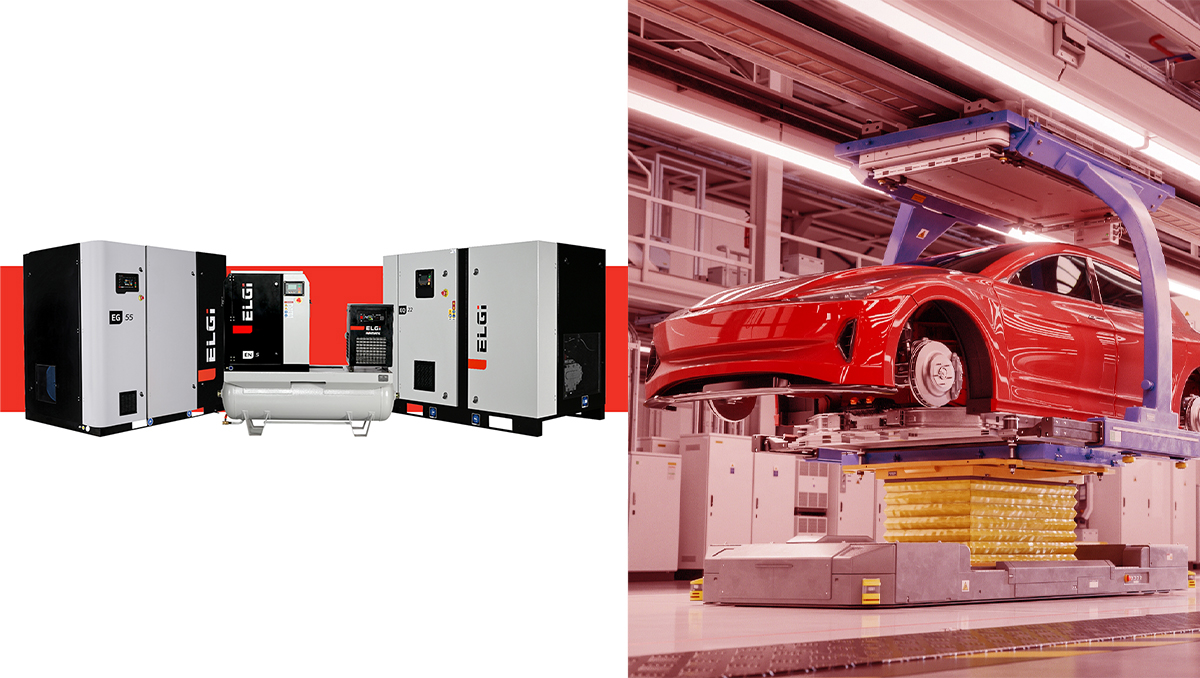
Compressed air is an invaluable resource in the automotive industry, powering everything f...
Read More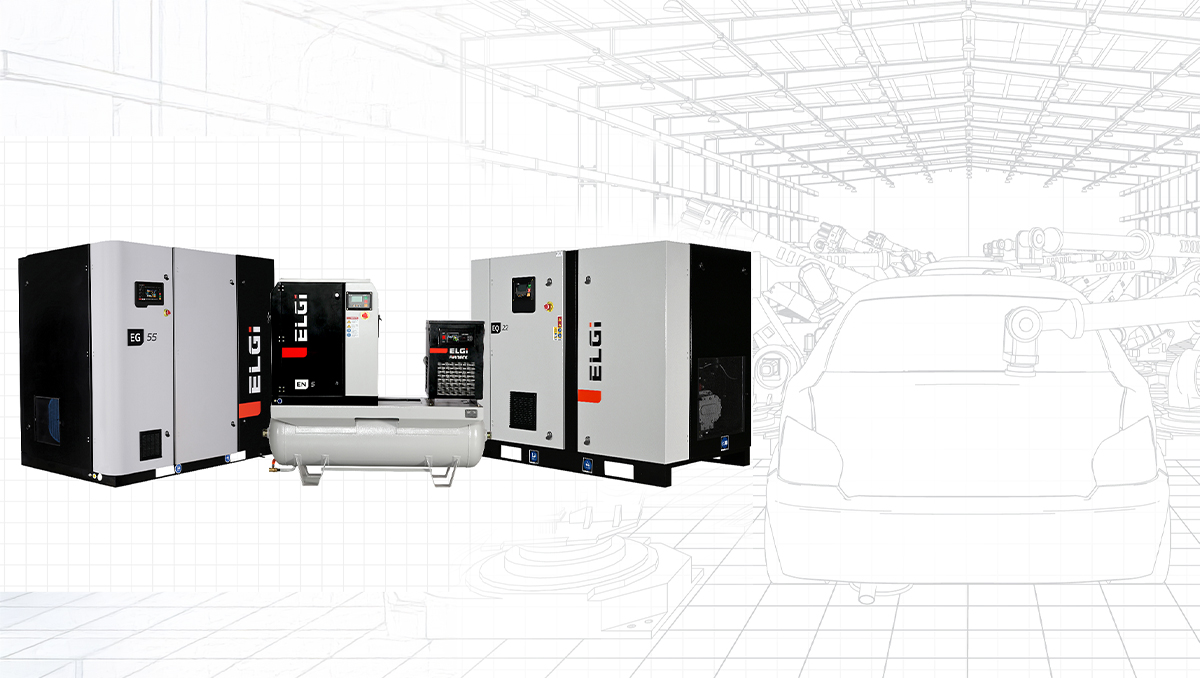
The automotive industry is one of the most dynamic and technology-driven sectors, requirin...
Read More
Rotary screw air compressors are essential machines used in many industrial applications a...
Read More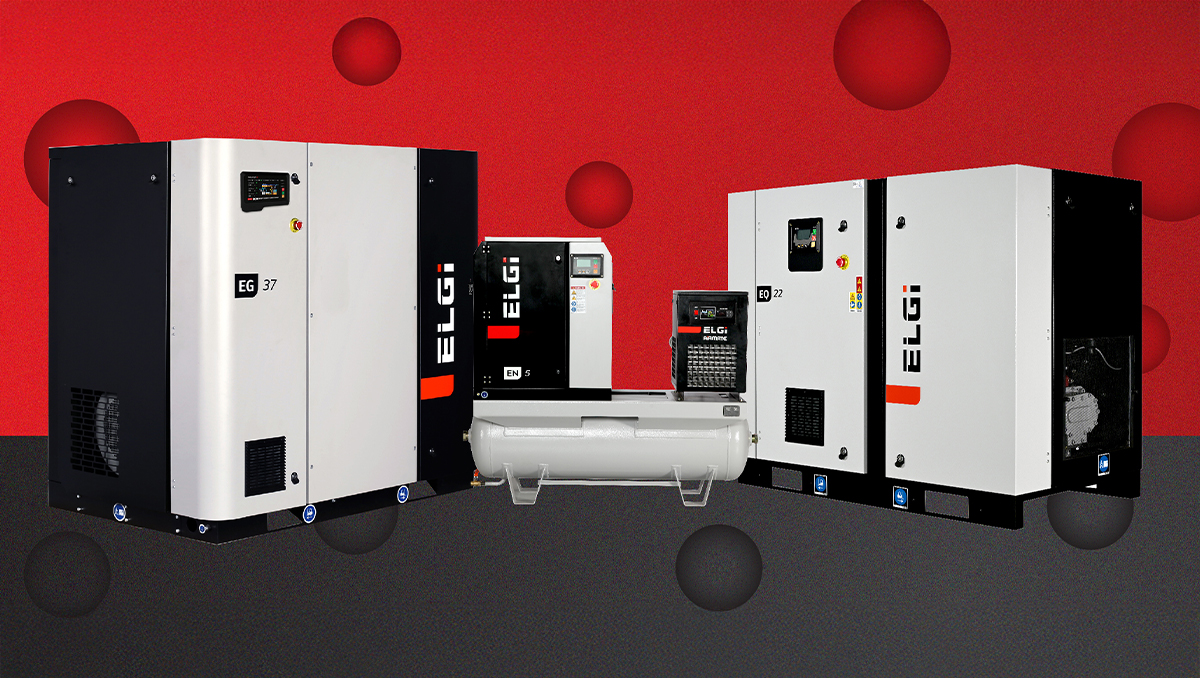
Choosing the right rotary screw compressors is crucial for your industrial operations. In...
Read More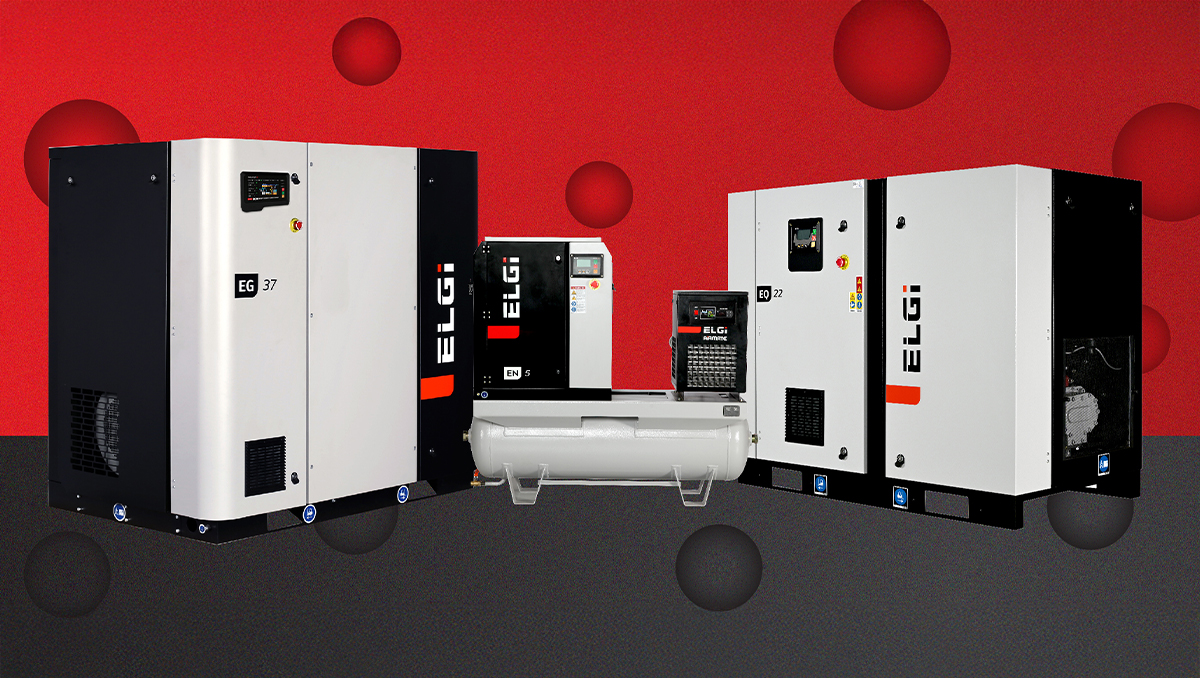
Choosing the right rotary screw compressors is crucial for your industrial operations. In...
Read More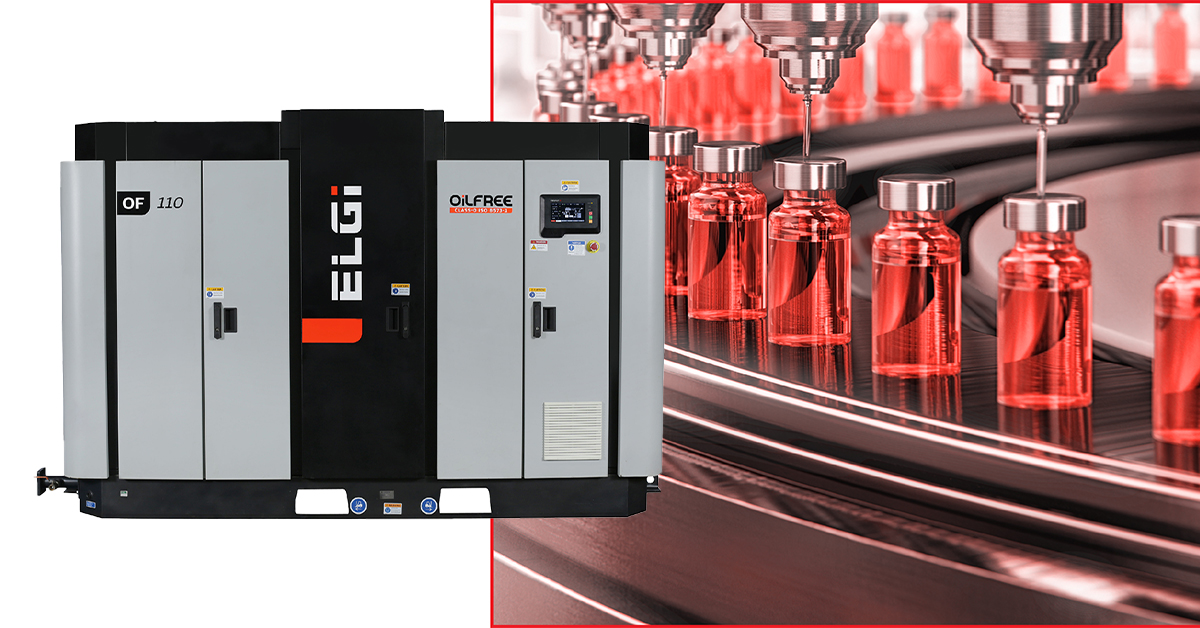
The pharmaceutical industry relies heavily on precision, sterility, and efficiency in ever...
Read More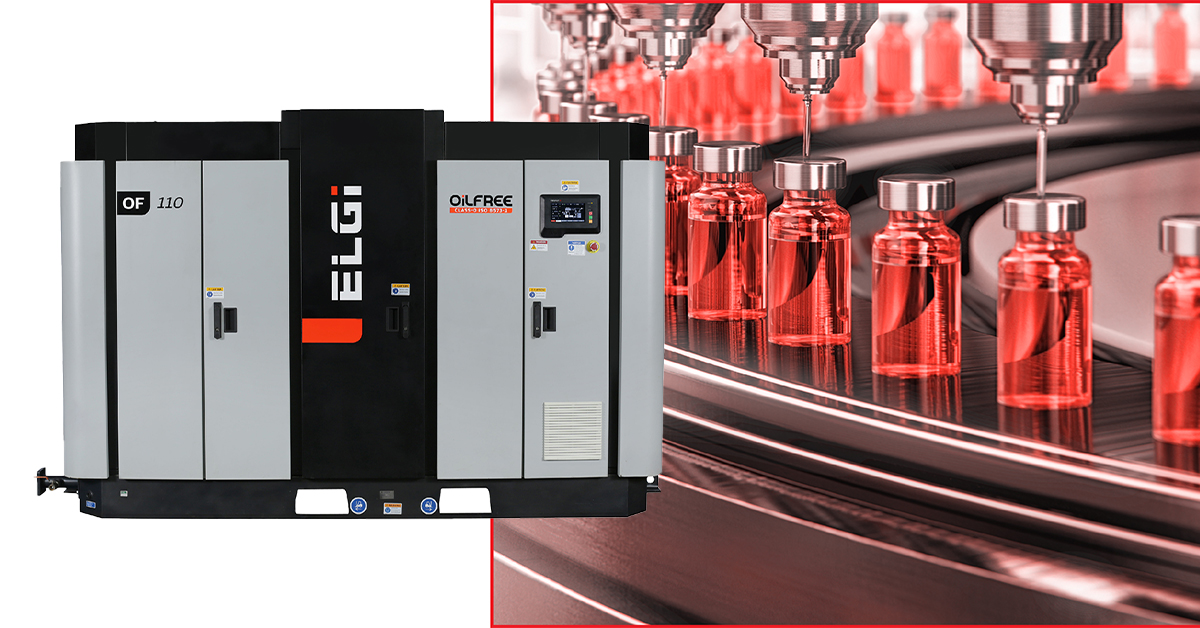
De farmaceutische industrie is sterk afhankelijk van precisie, steriliteit en efficiëntie...
Read MoreBe the first to get updates, learn more and join our explorative world by subscribing to our official compressed air journal.
SUBSCRIBE