How to correctly size your compressed air system
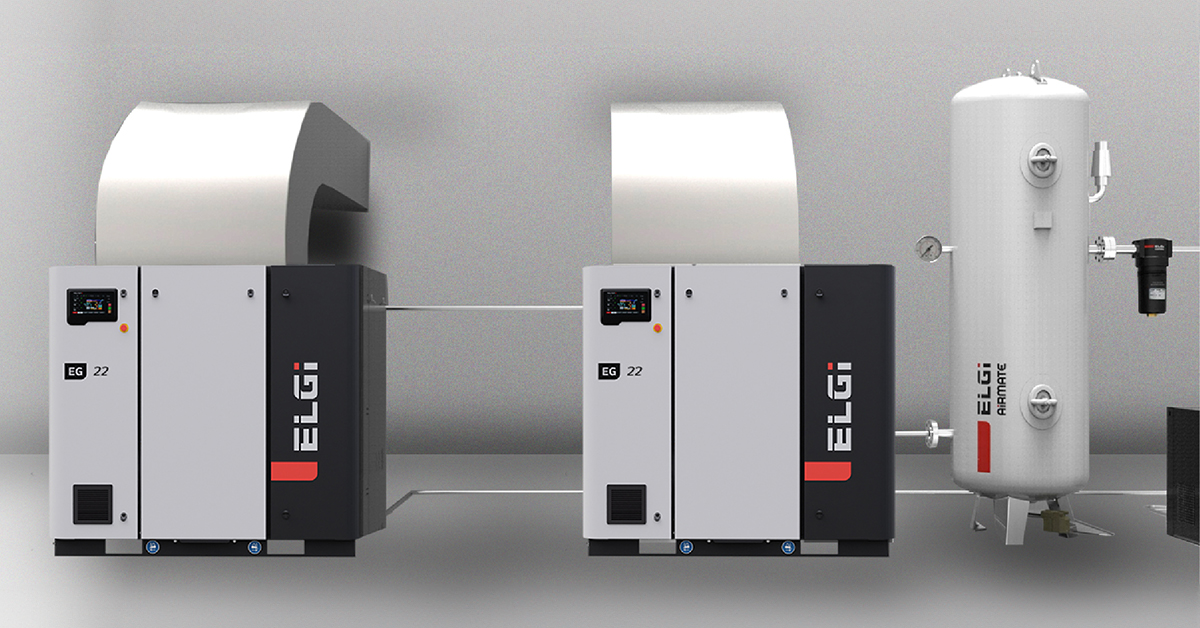
Understanding the importance of a well-sized compressed air system
In industrial environments, the significance of a well-sized compressed air system is paramount. These systems work as an ancillary framework for various operational requirements. Everything from essential air tools (pneumatic equipment) to complex machinery relies on a steady, uninterrupted supply of compressed air.
Properly sizing a compressed air system ensures optimal energy consumption, minimises energy waste, and reduces operating costs. Accurately sized systems deliver a consistent airflow to meet demand, ensuring reliable operation of equipment and preventing production delays. Compressed air equipment operating within its optimal capacity range lasts longer, reducing the need for frequent replacements and lowering overall lifecycle costs. By improving energy efficiency, reducing maintenance expenses, and extending equipment lifespan, a well-sized compressed air system offers significant cost savings over its operational lifetime.
The detrimental impact of incorrect compressor sizing
An oversized system leads to wasteful energy consumption and inflated expenses, while an undersized system strains to meet demands, causing wear and increased maintenance. This balance is crucial for economical and efficient operations.
ELGi's range of industrial air compressors, including rotary screw air compressors and reciprocating compressors, cater to various operational requirements, ensuring efficiency and system longevity.
Energy Efficiency 0f Compressed Air Systems
Investment Cost 16%
Maintenance Cost 6%
Energy Cost 78%
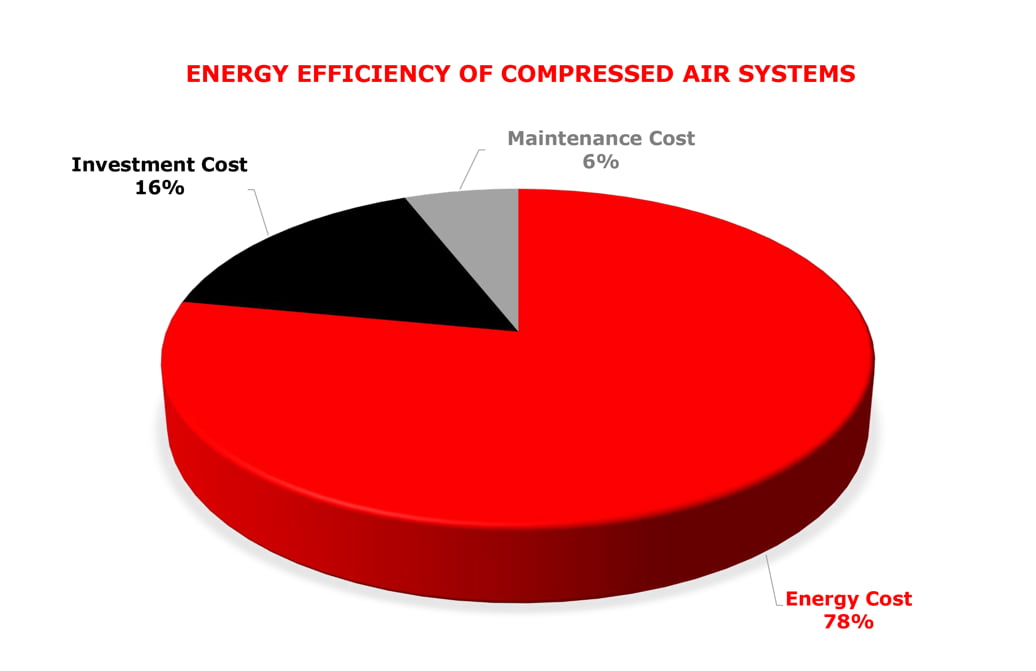
Tailoring to application requirements: Pressure, flow, and duty cycle
Determining the correct size for a compressed air system hinges on understanding requirements like compressed air pressure, airflow requirements, and duty cycle. Different tools and processes demand varying air pressures, and the system's flow rate must match the volume of air needed. Duty cycle consideration is vital in choosing between options like a variable speed screw compressor or a fixed speed rotary screw compressor. ELGi's variable speed screw compressors adjust to varying operational needs, optimising energy consumption and reducing maintenance costs. Check out our range of compressors best suited for your industry.
Certain specialised operations may require high-quality compressed air involving the use of entirely oil-free compressed air; for such instances, the system may benefit from employing oil-free compressors, delivering oil-free compressed air according to ISO 8573-1.
ELGi's oil-free air compressors are ideal for such operational requirements.
Energy efficiency: A greener way forward
In general, for example, fixed-speed compressors are more energy-efficient when operating near their full capacity. Selecting a compressor that closely aligns with the facility's demand profile ensures operational efficiency and avoids energy wastage. For instance, a compressor too large for the required demand may consume more power than necessary at lower capacities. In contrast, an undersized compressor might struggle to meet the air demand, leading to increased wear and potential operational interruptions.
Determining compressed air demand: A calculated approach
An accurate compressed air demand calculation is essential for system efficiency. It thoroughly evaluates all air-consuming equipment, peak demand periods, continuous operation requirements, and potential future expansions. This assessment should include both, current use and projected increases in demand. Compressed air demand fluctuates based on operational requirements, making adaptability a vital feature of an efficient system.
ELGi’s variable frequency drives adapt to the evolving demands by adjusting motor speed in real-time to match changing needs, enhancing overall system efficiency.
Optimising the piping System: Minimising pressure drop and energy loss
A well-planned piping system is critical for maintaining optimal compressed air pressure and reducing energy losses. Correct pipe sizing and strategic layout prevent pressure drops and ensure efficient airflow, with considerations for material choice to avoid corrosion and energy loss.
Confronting pressure drop issues
Pressure drops in compressed air systems can significantly reduce efficiency and increase energy usage. Issues like reduced air compressor capacity, improper compressed air piping size, lengthy piping routes, and obstructions can cause these drops. Addressing these factors is crucial for maintaining operational efficiency. Our compressed air experts offer comprehensive solutions, including efficient piping designs to minimise compressed air pressure drops.
Choosing the right compressor: Types and benefits
Selecting the appropriate compressor is fundamental to system efficiency.
Different types, such as oil-lubricated and oil-free air compressors, including rotary screws, reciprocating, and centrifugal compressors, offer various advantages. The choice should reflect the specific needs of the duty cycle, efficiency, and application capacity.
ELGi, one of the leading industrial compressor manufacturers, has a wide product range, allowing you to choose the right fit for your needs; our team of compressed air experts helps you make the best decision for your facility. Looking to buy a compressor, check out our Air compressor product page.
ISO 1217– The global standard
ISO 1217 sets rigorous standards for accurately measuring air compressor performance. These standards mandate precise methods for determining key performance indicators such as volumetric compressed air flow rates, pressure, power consumption, and overall isentropic efficiency. Specifically, air compressors must be tested consistently, using a reference atmospheric condition and specifying how to account for variables such as intake air temperature and humidity. The standard also delineates how to calculate the FAD (Free Air Delivery) to ensure that the airflow rate is measured at actual working conditions, providing a realistic assessment of the compressor's capability. By adhering to these stringent requirements, facilities can ensure that the compressors they select are efficient and capable of delivering the performance needed for their specific industrial applications.
Compliance with ISO 1217, thus, is not just about meeting regulatory benchmarks; it’s about guaranteeing operational efficiency and longevity of the compressed air system, aligning with the global standards of accuracy and reliability across a spectrum of different types of compressors.
Integrating air receivers for enhanced efficiency
Incorporating air receivers or tanks into the compressed air system can significantly boost efficiency for the correct air compressor size. These components help stabilise demand fluctuations, contributing to energy savings and prolonging the compressor's lifespan by reducing cycling.
Ensuring compressed air quality with treatment components
Compressed air quality is crucial in compressed air systems. Components like filters, dryers, and condensate drains are essential for removing impurities, ensuring the compressed air supply’s purity, and protecting the system, air compressor, and tank as well as air industrial equipments.
Emphasising routine maintenance for optimal performance
A regular maintenance schedule for your compressed air system is vital for ensuring longevity and peak performance. Simple checks, even in operating conditions, like noticing air compressor pressure drops, variable airflow requirements, changes observed through sight glasses, operational inefficiencies with air compressor tanks, or tell-tale holes/inspection holes in the case of oil-lubricated compressors, can all be forewarnings of something amiss.
Constant servicing and checks are crucial to avoiding unexpected breakdowns and maintaining efficiency.
Monitoring for peak performance
Regular monitoring of pressure levels, compressed air quality, and overall system performance is essential for early problem detection to ensure air compressor efficiency. This involves consistent checks and monitoring tools to track and manage system performance and schedule timely air compressor maintenance.
ELGi’s state-of-the-art remote monitoring systems employ the latest instrumental and control technology to ensure your system runs without any snags, and possible future breakdowns or malfunctions are foreseen to reduce downtime and plan scheduled maintenance well in advance.
Why ELGi stands out in compressed air solutions
ELGi stands at the forefront of providing customised compressed air solutions, from system planning to after-sales support. From selecting the best air compressor for industrial use to designing an efficient pressurised air system and ensuring compressed air treatment, ELGi's team of compressed air experts offers comprehensive support. Choosing ELGi means investing in a solution that meets today's needs and is equipped for future challenges.
RELATED BLOGS
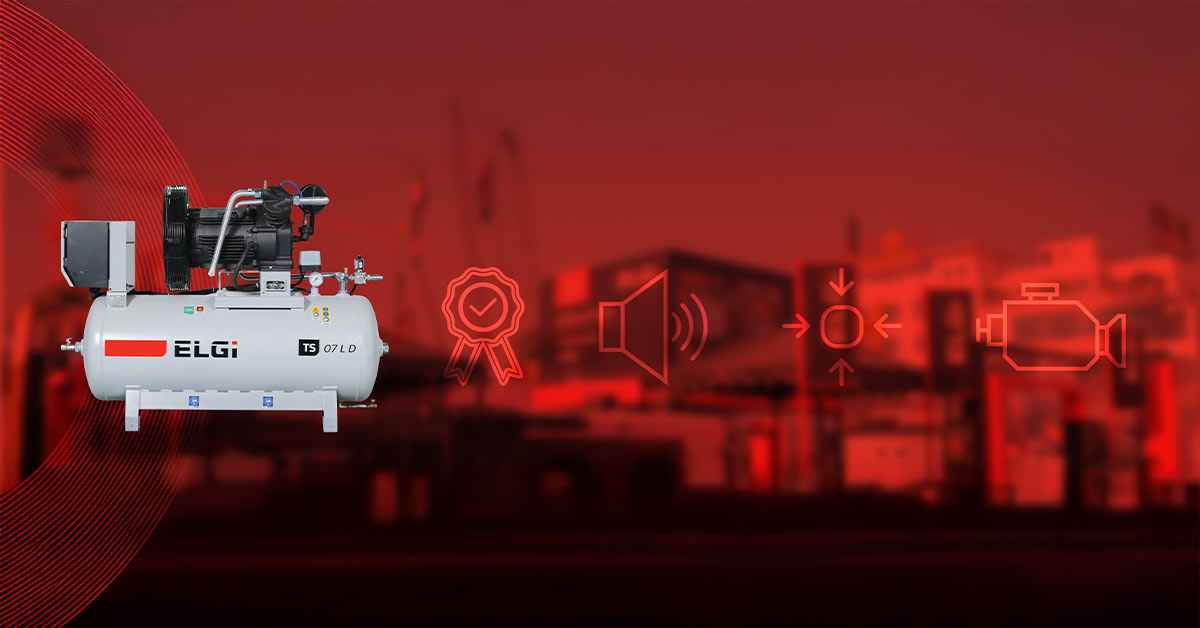
Compressed air is a critical element in many industrial operations, from powering tools to...
Read More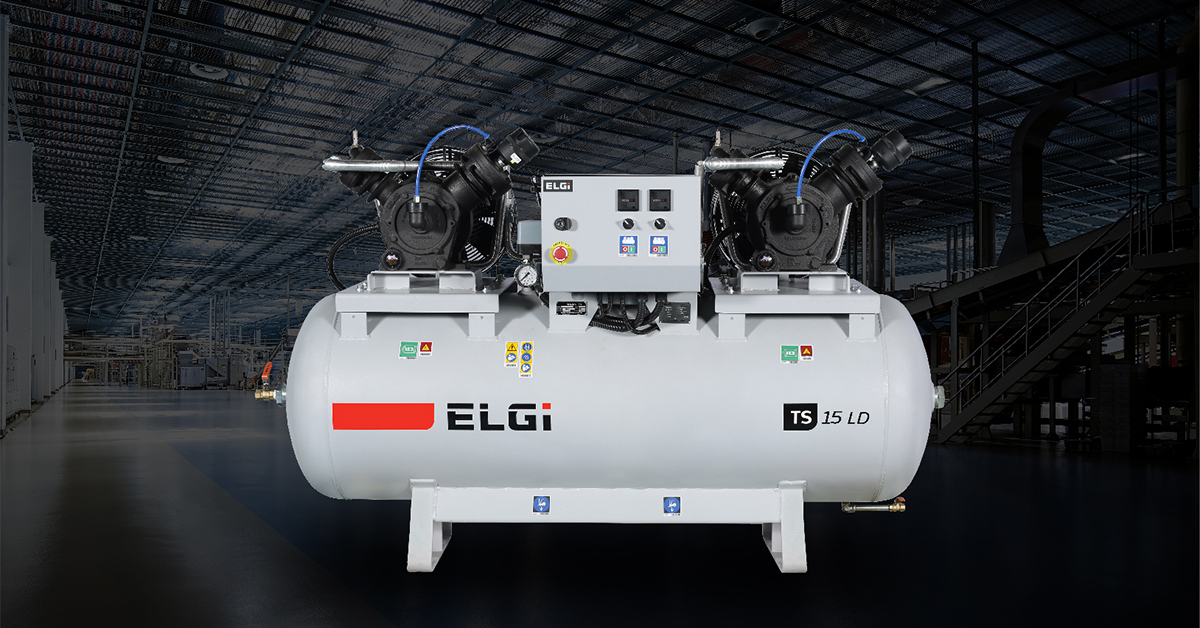
How Oil Lubricated Compressors Work and Their Role in Energy Efficiency Oil lubricated ...
Read More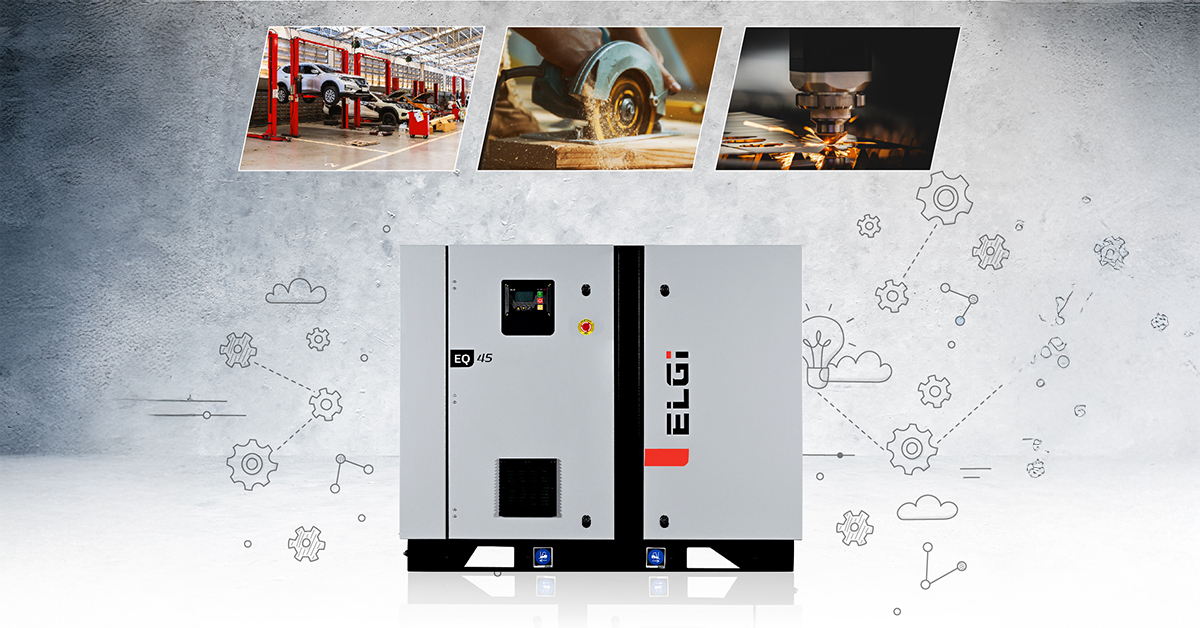
Why the ELGi EN Series is Ideal for Compact Industrial Compressed Air Solutions Busine...
Read More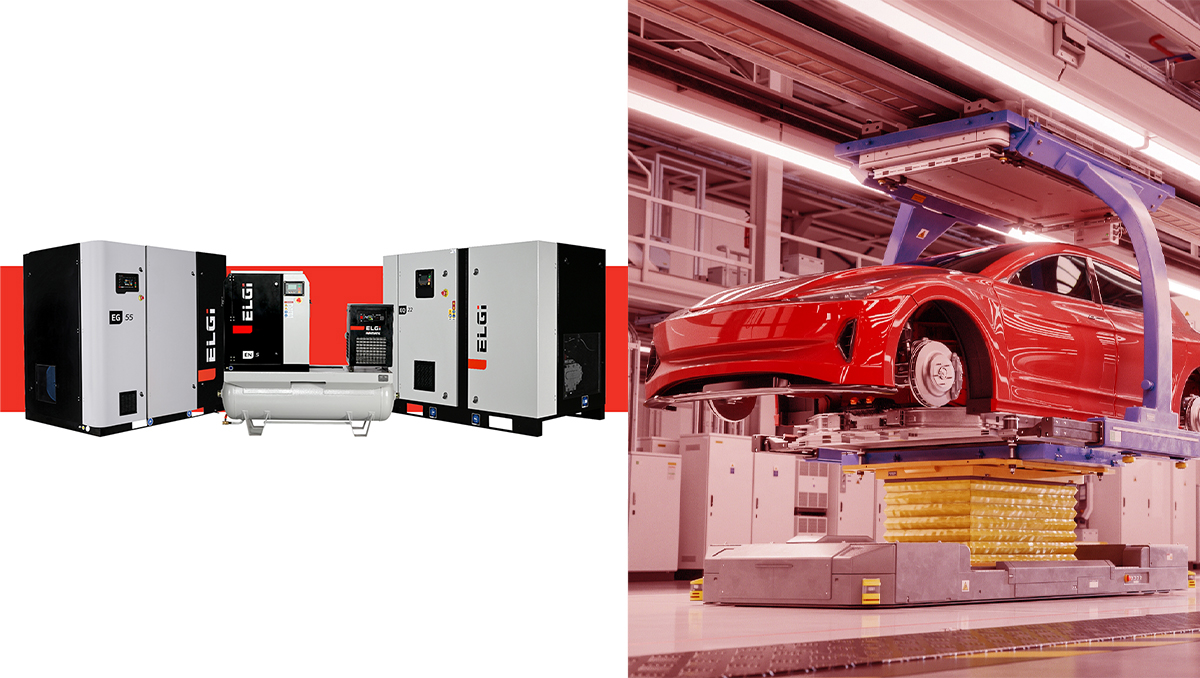
Compressed air is an invaluable resource in the automotive industry, powering everything f...
Read More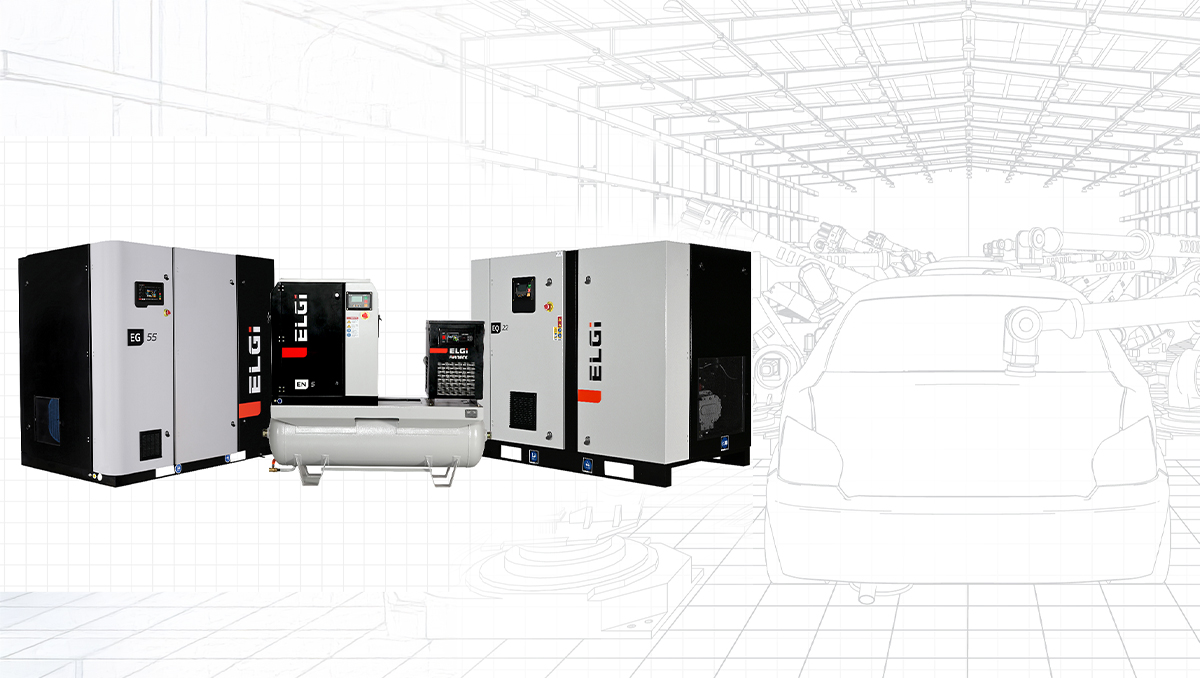
The automotive industry is one of the most dynamic and technology-driven sectors, requirin...
Read More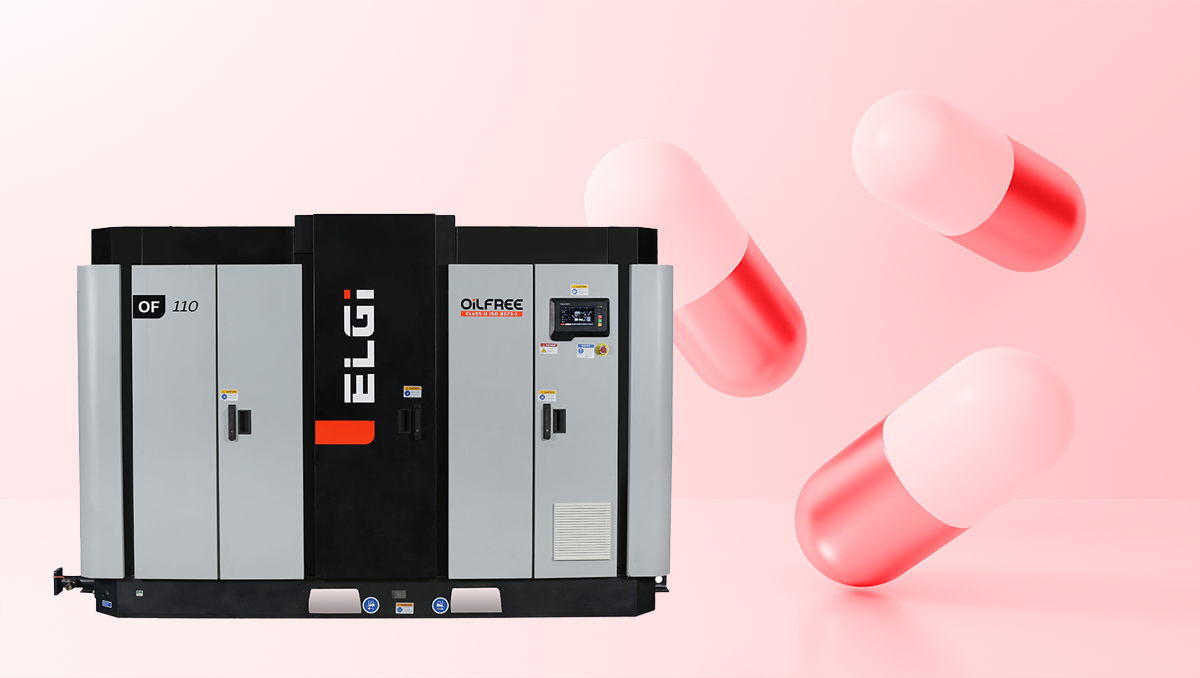
The pharmaceutical industry operates in a realm where precision, purity, and compliance ar...
Read More
Rotary screw air compressors are essential machines used in many industrial applications a...
Read More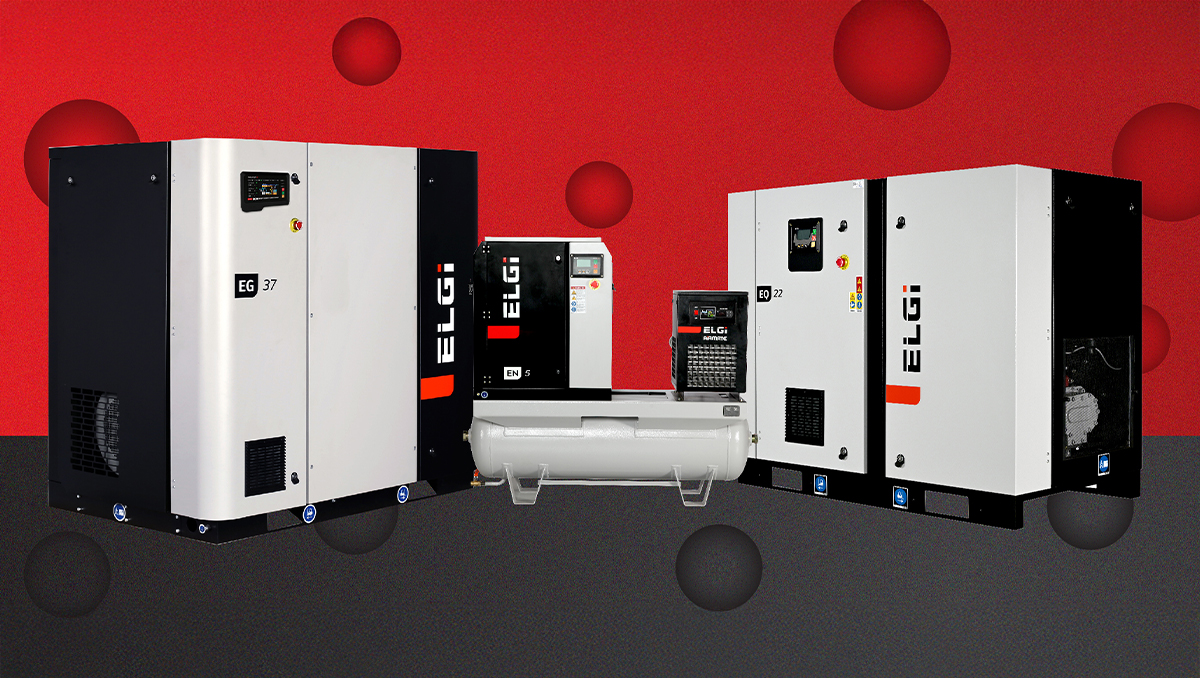
Choosing the right rotary screw compressors is crucial for your industrial operations. In...
Read More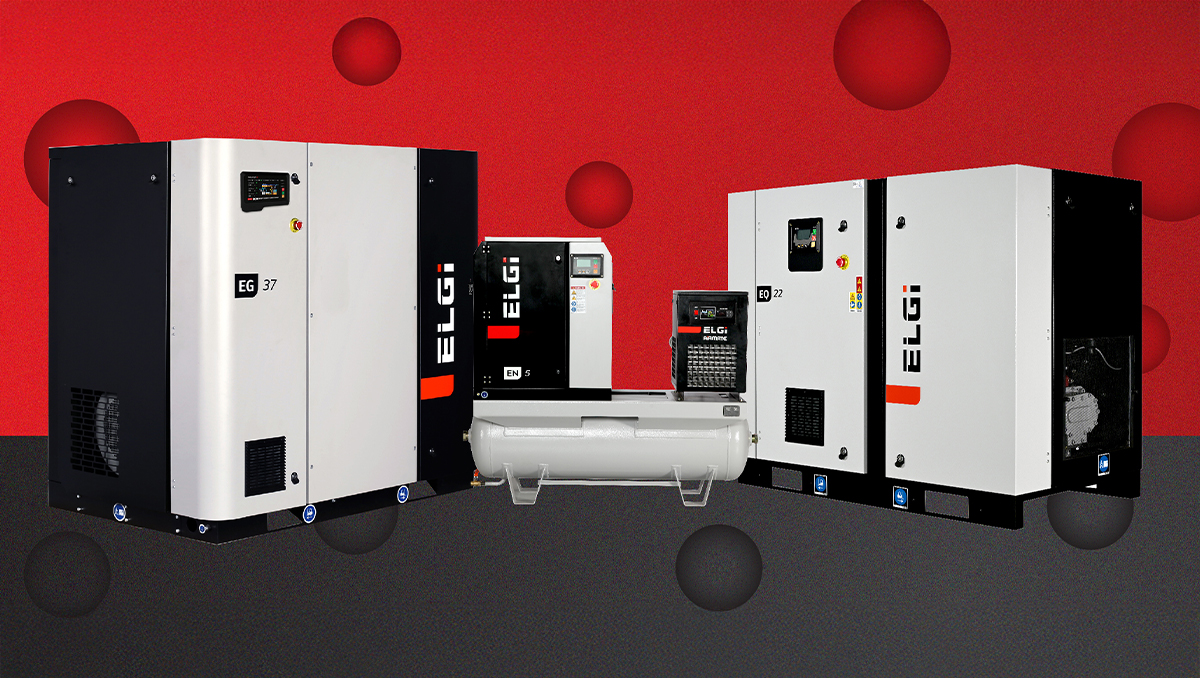
Choosing the right rotary screw compressors is crucial for your industrial operations. In...
Read More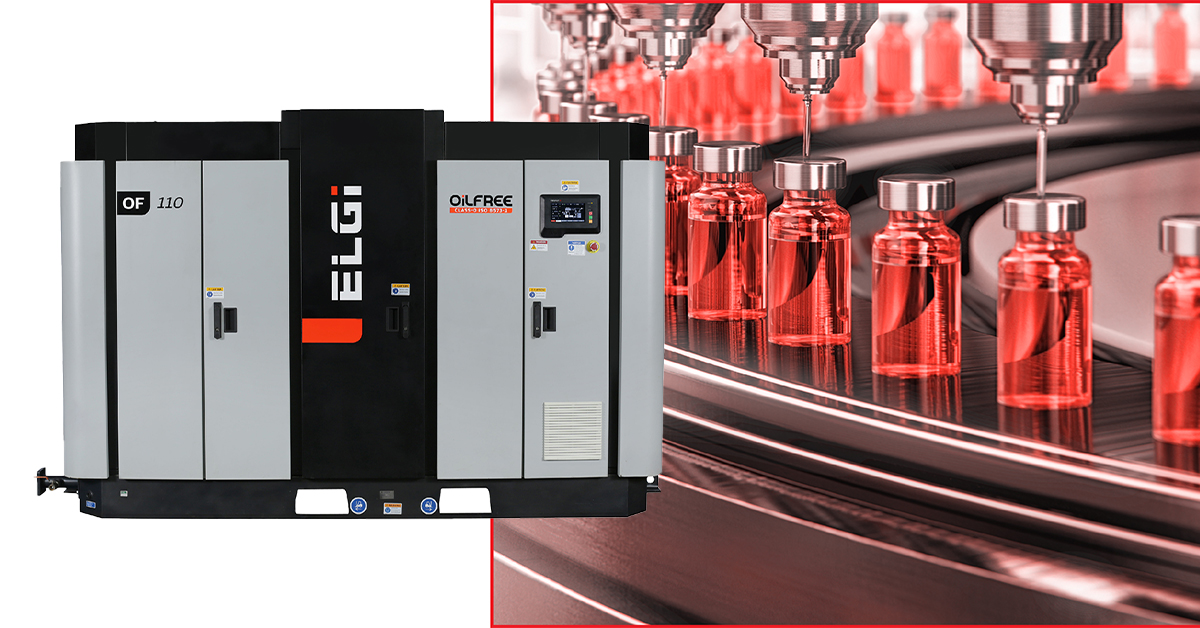
The pharmaceutical industry relies heavily on precision, sterility, and efficiency in ever...
Read MoreBe the first to get updates, learn more and join our explorative world by subscribing to our official compressed air journal.
SUBSCRIBE