Essential guide to air compressor maintenance
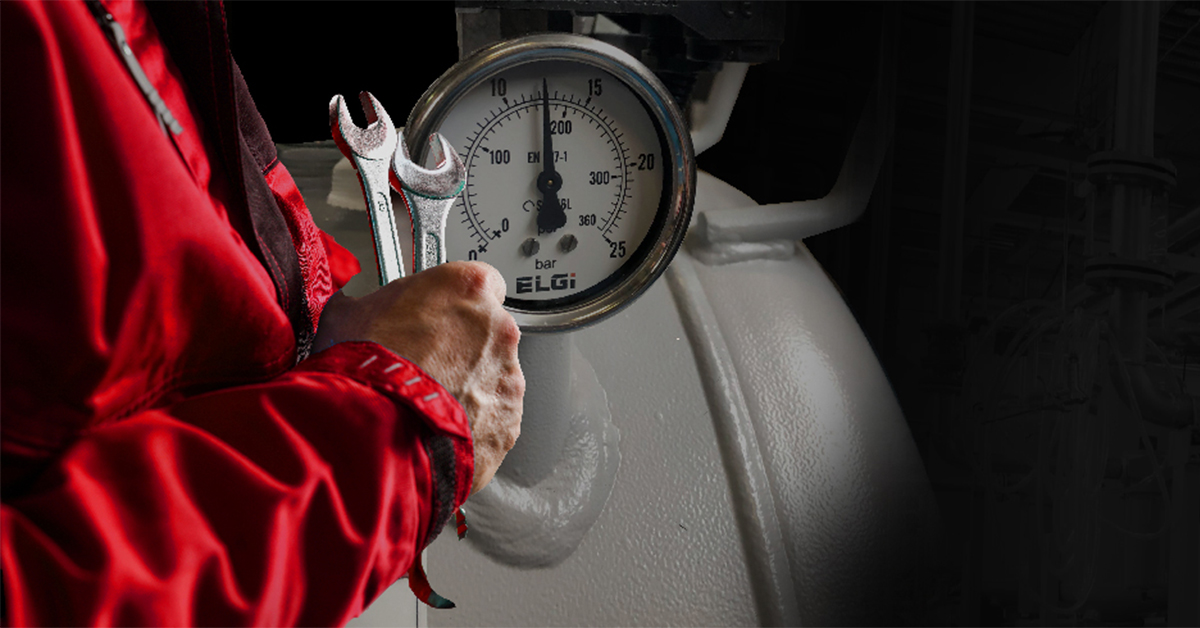
At the core of various industrial activities stands the industrial air compressor, an indispensable tool that drives machinery, processes materials, and enables different operations. Its crucial role in ensuring the smooth functioning of industrial processes cannot be emphasised enough, highlighting the undeniable necessity for its proper maintenance.
The importance of air compressor maintenance
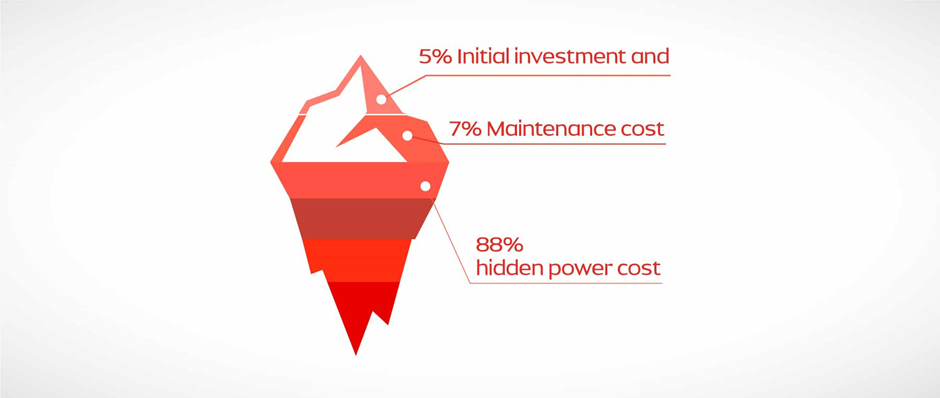
Maintaining air compressors is important for ensuring their operational efficacy, longevity, and safety. The consequences of neglecting regular maintenance can be profound, affecting not only the reliability and performance of the air compressor but also posing safety hazards, and incurring significant financial losses due to downtime. Adopting a comprehensive maintenance regimen is crucial for any enterprise depending on this vital machinery.
Key points to consider for air compressor maintenance
Operational Efficiency: Regular maintenance ensures that air compressors run optimally, directly impacting energy consumption (and therefore, costs), and operational output.
Durability: A consistent upkeep routine extends the lifespan of air compressors, safeguarding against premature wear and tear.
Safety: Proactive maintenance minimises the risk of accidents, ensuring a safe working environment for personnel.
Cost Savings: Regular maintenance of air compressors helps avoid the need for emergency repairs and reduces the likelihood of costly interruptions in operations due to downtime.
Benefits of well-maintained compressed air systems
A comprehensive maintenance routine boosts operational efficiency, reducing energy costs. It extends the lifespan of the air compressor, ensuring it serves your needs for years to come. More importantly, it keeps the work environment safe for everyone involved, mitigating the risk of accidents caused by equipment failure.
Key components of a compressed air system
Understanding the intricate structure of your industrial air compressor is essential for effective maintenance and troubleshooting. Let us dive into the fundamental components that play pivotal roles in the compressor's operation, highlighting their functions and importance:
Compressor Airend: This is the heart of the air compressor, responsible for compressing the air. This component is crucial for the conversion of mechanical energy into pneumatic energy.
Air Receiver Tank: Tanks act as storage vessels to hold compressed air until it is needed. It plays a key role in maintaining constant pressure in the system, reducing the compressor's load by minimising its on-off cycles, and aiding in moisture separation.
Motor: The motor supplies the power needed for the compressor unit to function. Electric motors are available in various types, with kilowatt ratings that match the size and demands of the compressor system.
Pressure Switch: It is a critical safety and operational device that automatically starts and stops the compressor when the air pressure reaches preset upper and lower limits. This ensures the system operates within safe pressure levels and conserves energy.
Water and Oil Separators: These components are integral to maintaining the purity of the compressed air. Water separators remove moisture from the air, preventing water accumulation in the system that can lead to corrosion and damage. Oil separators remove the condensate formed during the process of compression. This condensate can harm the environment if not appropriately treated before being released into the environment.
Air Filters: Protect the compressor's internal components by filtering out dust, debris, and particulate matter from the air before it enters the compressor chamber. Clean air is essential to prevent wear and maintain efficiency.
Intake Air Control Valve: This valve regulates the amount of air that enters the compressor chamber. Proper functioning of this valve is essential for efficient operation, as it adjusts the compressor's load based on the demand for compressed air.
Safety Valves: These are designed to automatically release air if the pressure within the compressor or air receiver tank exceeds safe levels, preventing potential accidents or damage to the system.
Understanding these components and their functions within the air compressor system enables more effective maintenance and operation, ensuring that your compressor runs smoothly and efficiently. Regular checks and maintenance of these parts can significantly extend the lifespan of your air compressor and enhance its performance and energy efficiency.
The consequences of inadequate maintenance
Neglecting air compressor maintenance can result in several issues, from minor inconveniences to major safety hazards. Increased energy consumption, decreased efficiency, and the high cost of unplanned repairs are just the tip of the iceberg. Without regular upkeep, air compressors can suffer from decreased performance, increased energy consumption, and, ultimately, failure. This can lead to interrupted operations, inflated energy bills, and potential safety hazards, emphasising the need for consistent maintenance.
Looking for complete maintenance solutions for your compressed air systems? Contact our team now.
Following an equipment maintenance checklist
Adhering to the manufacturer's recommended maintenance schedule is key. However, consider the compressor's environment and adjust the maintenance frequency accordingly. Regular service intervals prevent minor issues from becoming major problems.
Book a team of experts for air compressor inspection.
Essential maintenance tasks
Oil and Filter Changes: Regularly check and replace the oil in oil-lubricated compressors, and don't forget to inspect and replace air filters to prevent contamination.
Cleaning: Keep the compressor unit, tank, and hoses clean to ensure optimal airflow and prevent clogs and corrosion.
Leak Checks and Tightening: Regularly inspect for leaks and tighten connections to maintain system integrity and efficiency.
Worn Parts Replacement: Inspect and replace belts, seals, and other parts showing wear to prevent breakdowns.
Lubrication and Safety Checks: Lubricate moving parts and test safety valves and features to ensure the compressor operates safely and smoothly.
Air Compressor Valves: Ensure smooth valve operation, suction valves left open for longer durations may lead to loss in efficiencies.
Ensure the best air compressor maintenance service for your systems. Contact our team now.
Identifying and addressing common problems with compressed air systems
Staying vigilant for indicators of malfunction in your air compressor can significantly mitigate the risk of downtime and costly repairs. Early detection and corrective measures for common issues not only ensure the longevity of your equipment but also its operational efficiency.
Overheating: Often a result of poor ventilation or a clogged air filter. Solutions include:
- Ensuring adequate airflow around the compressor.
- Regularly cleaning or replacing air filters to prevent blockages.
- Your maintenance schedule should include plans for intake air control valve cleaning.
Air Leaks: Can significantly reduce efficiency and performance. Solutions involve:
- Conducting regular inspections of compressed air receiver tank, pipelines, hoses, fittings, and air compressor filters.
- Tightening connections or replacing damaged components as necessary.
- Ensure your maintenance plans include air dryer maintenance.
Unusual Noises: Rattling, knocking, or hissing sounds can indicate various issues, such as loose parts or air leaks. Addressing these sounds involves:
- Tightening any loose components.
- Inspecting for and sealing any leaks.
- Uneven bearing clearances
Moisture Buildup in the Air Receiver Tank: This can lead to corrosion and water contamination in the air system. This is applicable for both external air receivers as well as air compressors with dryer. Solutions include:
- Regularly draining the tank to remove accumulated water.
- Regularly checking if the automatic drain is working properly.
- Ensure your maintenance schedule has planned inspections for the drain for the air compressor.
- Regular air receiver inspection can lead to timely detection for onset of cracks and material fatigue.
High Oil Carryover: This issue is particularly concerning for oil-lubricated compressors because it compromises air quality. Solutions include:
- Checking and replacing oil separators regularly.
- Ensuring proper maintenance of the compressor's oil levels and condition.
- Invest in water and oil separator for air compressors for increasing operational efficiency
Proactive maintenance and prompt attention to these common issues can dramatically enhance the performance and lifespan of your air compressor, avoiding unnecessary expenses and ensuring continuous, efficient operation.
Request a quote for compressed air maintenance services. Contact our team now.
Safety precautions during compressed air maintenance
Safety should always be the top priority. Ensure that all maintenance is performed with the compressor off and fully depressurised. Follow the manufacturer's guidelines and wear appropriate safety gear to prevent accidents.
Contact us for all your air compressor service requirements
Planned maintenance schedule/ Industrial preventive maintenance checklist
Regular, thorough maintenance is the key to a long-lasting, efficient air compressor. Adhering to a strict compressed air equipment maintenance checklist ensures that your air compressor remains a reliable asset in your industrial operations, safeguarding against unexpected downtime and ensuring workplace safety.
Talk to our experts for a detailed plan for your screw compressor maintenance. Contact our team now.
RELATED BLOGS
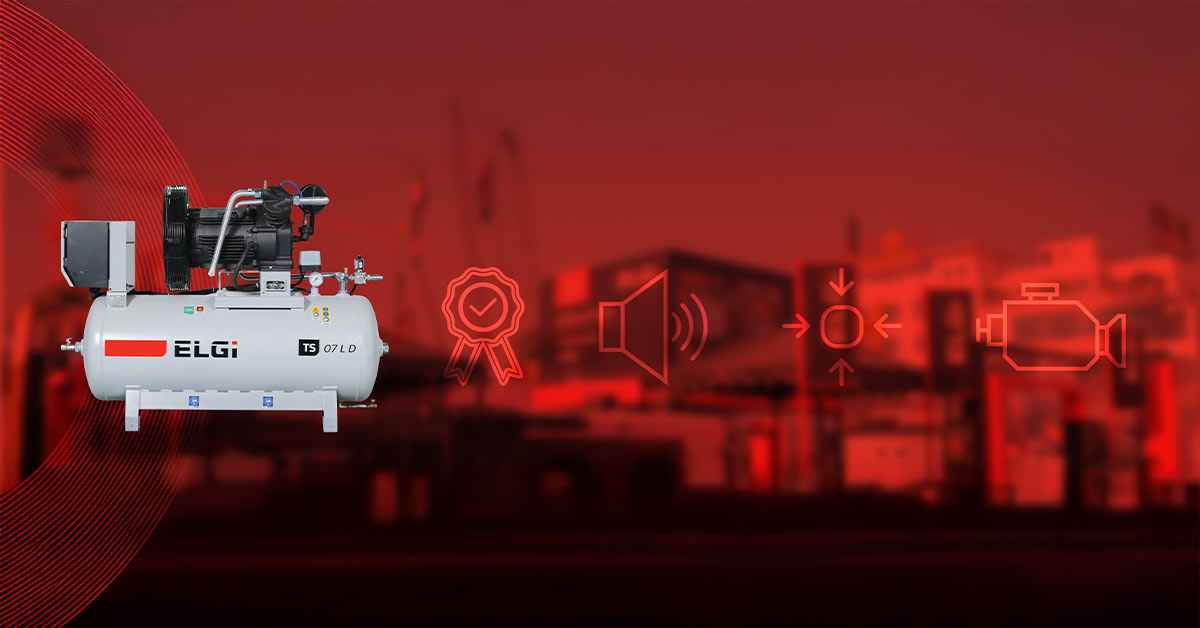
Compressed air is a critical element in many industrial operations, from powering tools to...
Read More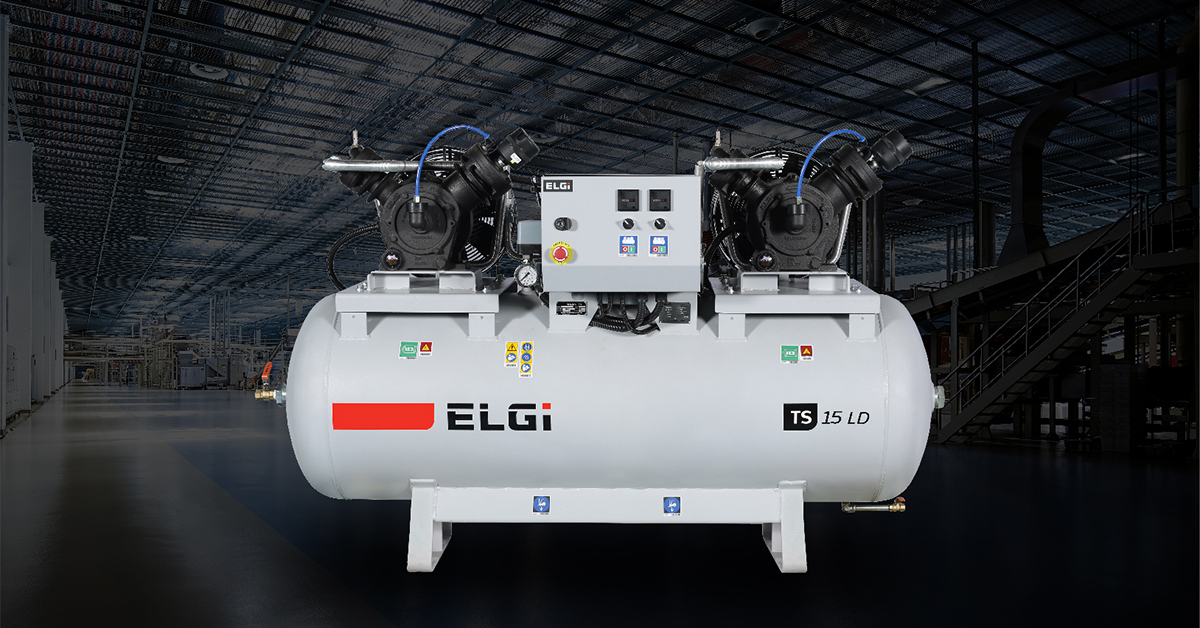
How Oil Lubricated Compressors Work and Their Role in Energy Efficiency Oil lubricated ...
Read More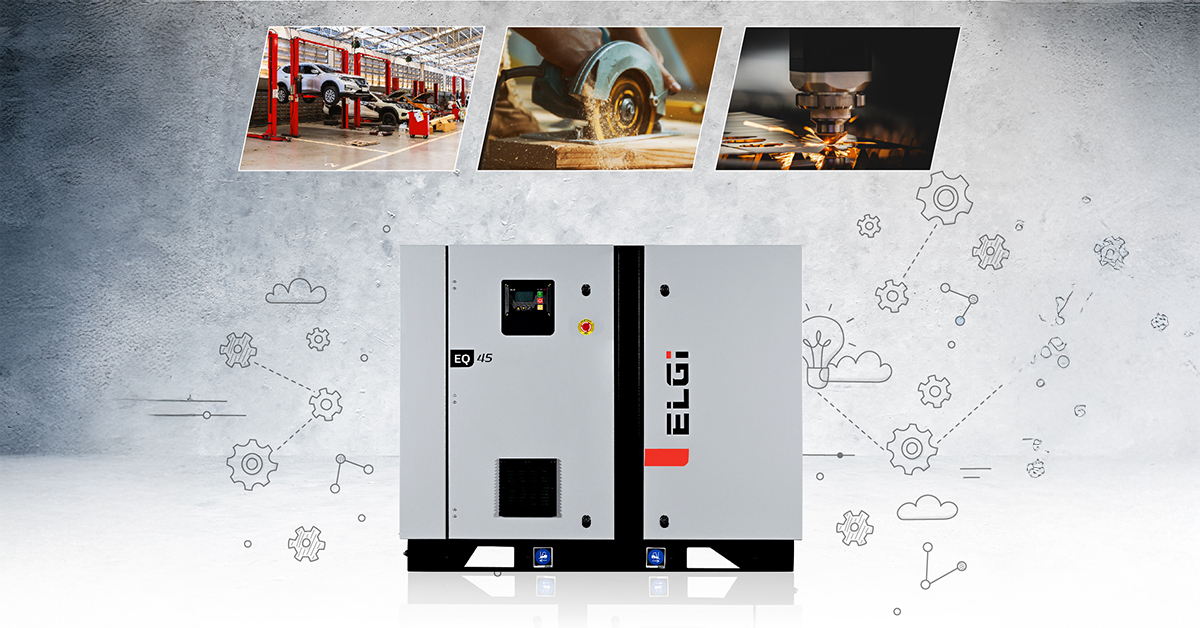
Why the ELGi EN Series is Ideal for Compact Industrial Compressed Air Solutions Busine...
Read More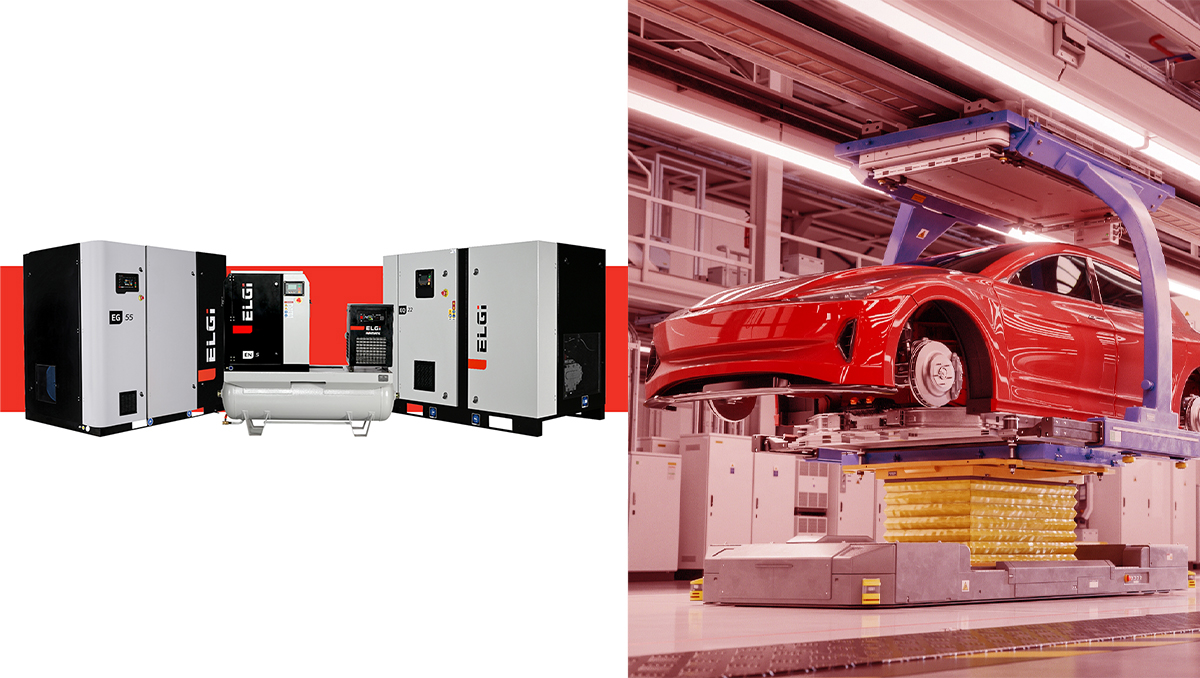
Compressed air is an invaluable resource in the automotive industry, powering everything f...
Read More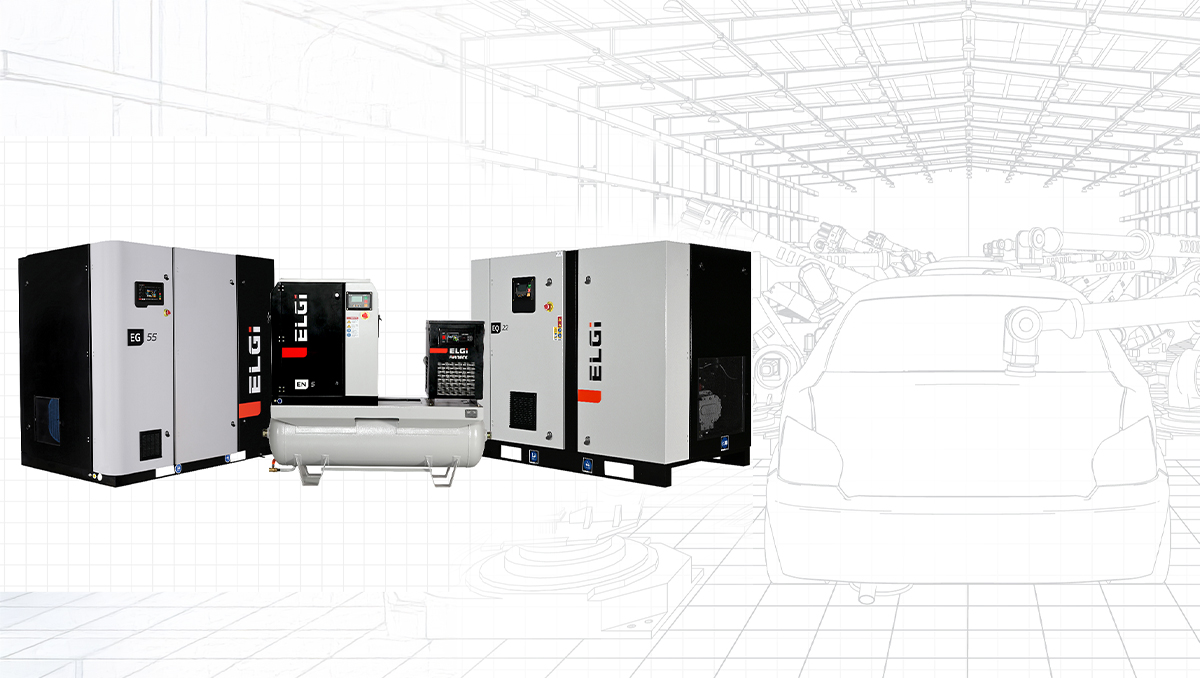
The automotive industry is one of the most dynamic and technology-driven sectors, requirin...
Read More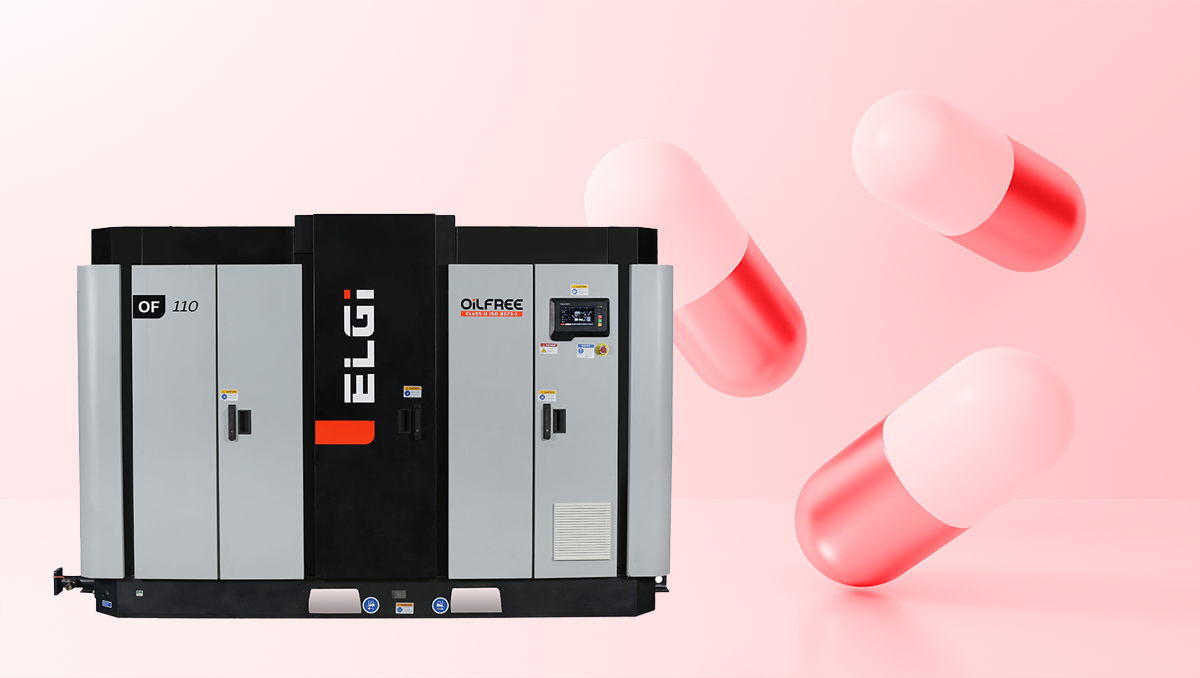
The pharmaceutical industry operates in a realm where precision, purity, and compliance ar...
Read More
Rotary screw air compressors are essential machines used in many industrial applications a...
Read More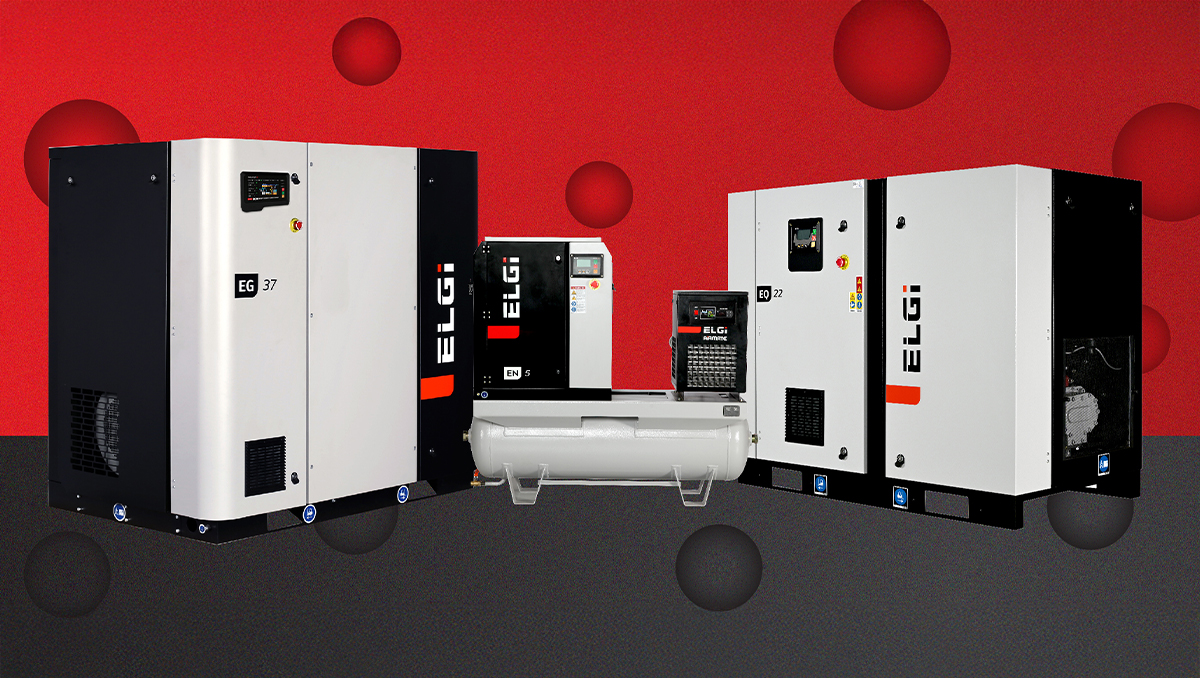
Choosing the right rotary screw compressors is crucial for your industrial operations. In...
Read More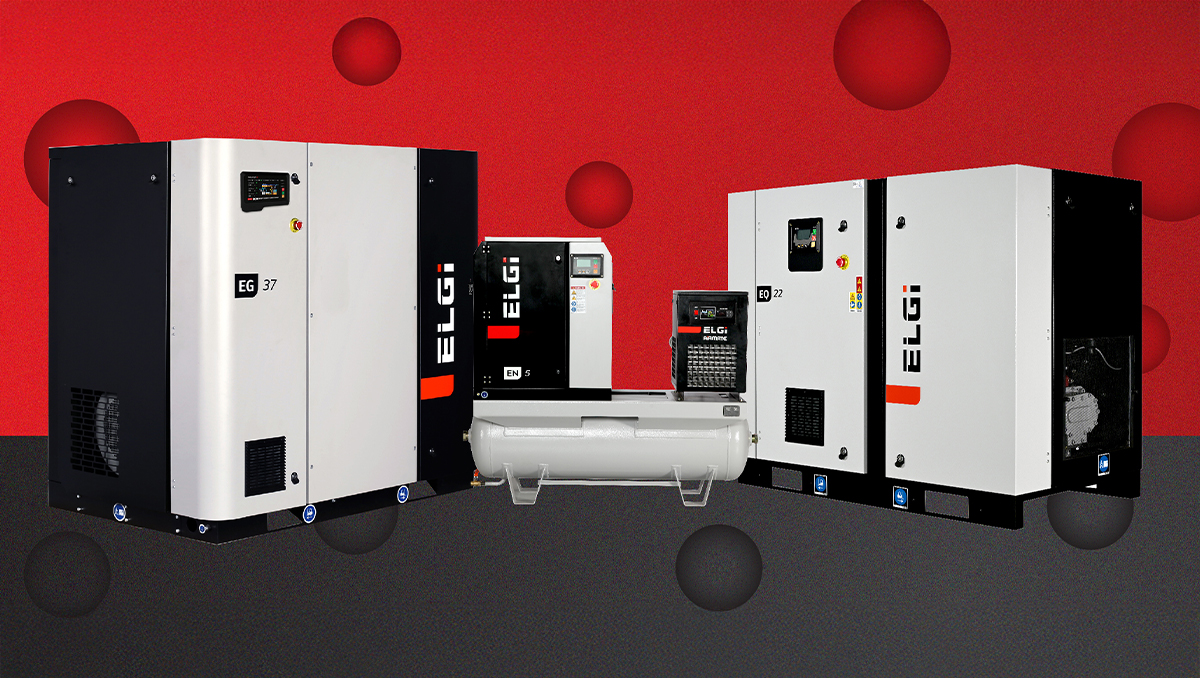
Choosing the right rotary screw compressors is crucial for your industrial operations. In...
Read More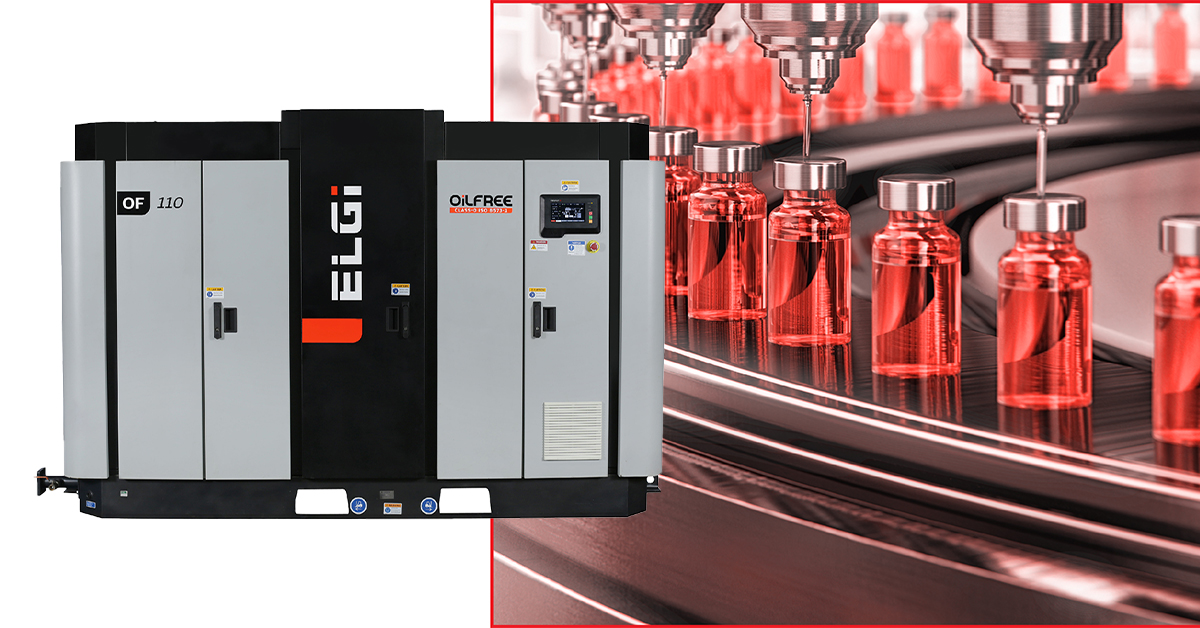
The pharmaceutical industry relies heavily on precision, sterility, and efficiency in ever...
Read MoreBe the first to get updates, learn more and join our explorative world by subscribing to our official compressed air journal.
SUBSCRIBE