Understanding Pressure Drops in Compressed Air Systems: Causes and How to Prevent It
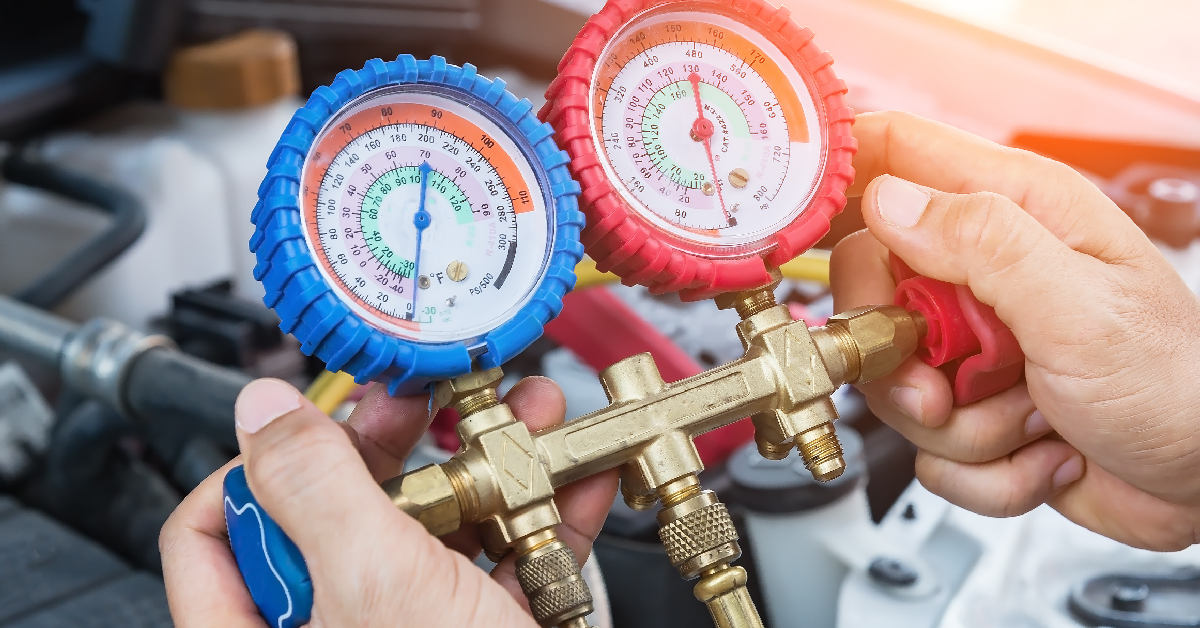
A pressure drop is a reduction in air pressure within a compressed air system as the air moves from the compressor discharge to the point of use. This phenomenon occurs as compressed air travels through the distribution system, and can happen at any stage between the compressor outlet and the final compressed air application. A well-designed compressed air system should ideally keep the pressure loss below 10% of the compressor's discharge pressure.
Pressure drops can cause a reduction in the operational efficiency of the production process, impacting energy usage, operation costs, and efficiency. Significant pressure drops can also adversely affect air compressor performance, leading to excessive energy consumption. Considering that compressed air is an essential and expensive utility for all industries, compressed air pressure drop is critical to avoid unwanted increases in energy and operational cost.
Why is my Compressed Air System Losing Pressure?
To ensure a consistent pressure level in a compressed air system, a seamless closed loop or connected hose is essential for the pressurised air to flow smoothly. Any changes to this system, such as loose parts, obstructions, or rough internal surfaces, can disrupt the airflow. These disruptions, leading to fluctuations in compressed air pressure, can be categorised into two primary issues — air distribution issues and air quality component problems.
Common causes of compressed air pressure drops include:
Compressed Air Leaks: Air leaks lead to low air pressure, which may disrupt operations and increase operating expenses. These leaks can arise from the piping system and all of the connections. Leaks can lead to a system’s pressure drop, affecting the performance of tools and equipment powered by compressed air. This can result in reduced productivity and potentially compromise product quality.
Oil contamination: Oil contamination in compressed air lines can lead to damaged seals, with cracks or swelling as expected consequences. The presence of oil is particularly harmful to plastic components, often resulting in their splitting.
Lack of employee training: Educate your staff about the importance of leak detection in a compressed air system and how to report it. This will encourage a culture of energy efficiency and conservation.
Repair needs: Broken parts, such as intake filters, fans, manifolds, and on/off switches, often lead to pressure drops in air compressors.
Flow issues: Flow issues in compressed air systems can be caused by various factors, such as incorrect hose connectors, low gauges, and plugged intake filters. These issues disrupt the pressure flow, leading to inefficiencies and reduced performance.
How to Minimise Pressure Drops in Compressed Air Systems?
A holistic approach to system design and ongoing system maintenance is essential to minimise compressed air pressure drops. Aftercoolers, moisture separators, dryers, and other air treatment components should be incorporated into the compressed air system design to ensure the lowest pressure drop and maximum operating efficiency. The prescribed best maintenance practices should be followed and recorded after installation to ensure minimal pressure drops.
Additionally, compressed air users can also look at the following strategies to minimise pressure drops:
Redesign your compressed air system: Design the distribution system properly. Try modifying your system design to eliminate any intermediary components.
Problems with the distribution components: Inspect your hoses and tubing for airflow challenges like kinks, folds, or holes that can lead to pressure reductions. Replace the parts if you detect any defects.
Maintain the compressed air filters: To reduce moisture impacts, such as pipe corrosion, maintain air filters and dryers. Regularly clean your air filters and replace them if they are blocked or dirty.
Replace faulty parts: Regularly inspect your dryers, separators, and aftercooler to ensure they operate well. Replace these parts when they break down or fail to work efficiently.
Minimise air travel distance: Pressure drops can occur when air travels across extensive distances. Reduce the distance that the compressed air must travel through the distribution system. Keep the number of hoses and connectors in the distribution system to the least required numbers and avoid unnecessary usage of components that increase the air travel distance.
Minimize Pipe Length and Bends: Keep the compressed air piping system as short as possible and minimize the number of bends and fittings to reduce friction losses that contribute to compressed air drops.
Reset air compressor pressure regulators: Change the settings on your air compressor pressure regulators to avoid any energy loss. Replace the regulator with a new model if pressure loss continues.
Leak Management Program: Consider implementing a comprehensive leak management program that includes regular audits, leak tracking, and performance measurements to continuously improve compressed air pressure system efficiency.
Eliminate Pressure Drops in Your Compressed Air System with ELGi
Compressed air is an expensive utility, and pressure drops can be costly, wasteful, and unfavourable to production processes. However, addressing pressure drops through regular maintenance and monitoring can help keep your operations running efficiently, resulting in cost and energy savings.
ELGi offers the ELGi Air Audit to compressed air users to assess the complete compressed air system, detect leakage in the compressed air system, and provide recommendations on the system design to reduce pressure drops and thus improve the overall efficiency.
ELGi has incorporated the latest compressed air technology to help you prevent pressure losses. ELGi’s Air~Alert is an IoT-enabled data transmission and analysis service that monitors critical parameters of the compressed air system and provides real-time information on the compressor's pressure and energy consumption, allowing you to detect and diagnose issues like pressure drops. Air~Alert can also send alerts in case of any problems, helping companies improve their operational costs and, more importantly, energy efficiency. To learn more about how Air~Alert can help with pressure losses, contact your nearest authorised ELGi Channel Partner.
ELGi offers a comprehensive product lineup, including compressors, dryers, air filters, filters, and accessories that work together to create a seamless and efficient compressed air system, effectively prevent compressed air pressure drops and maintain the efficiency and reliability of your compressed air system.
Our vast Channel Partner network can also help improve, maintain, and repair your compressed air systems. To reach out to your nearest authorised ELGi Channel Partner, click here.
RELATED BLOGS
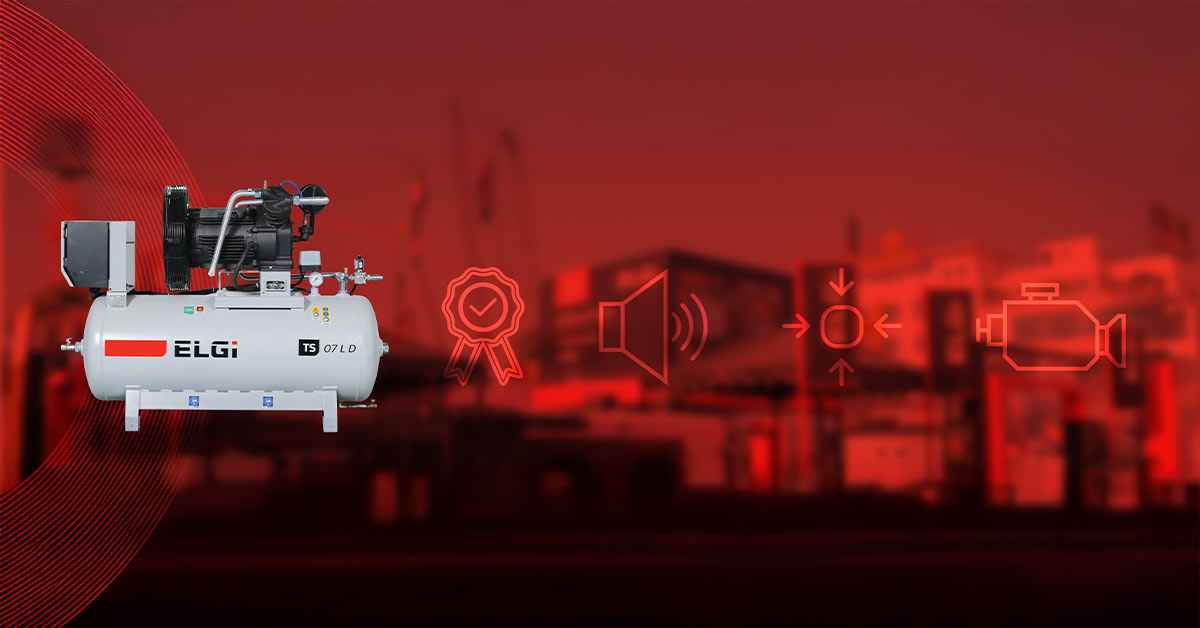
Compressed air is a critical element in many industrial operations, from powering tools to...
Read More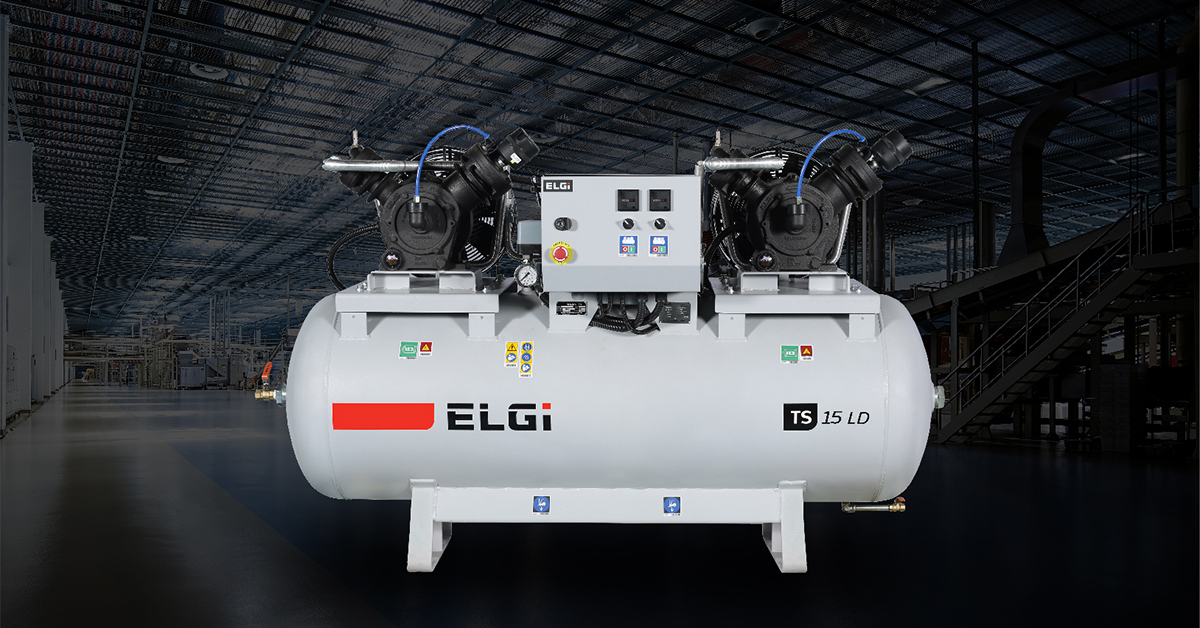
How Oil Lubricated Compressors Work and Their Role in Energy Efficiency Oil lubricated ...
Read More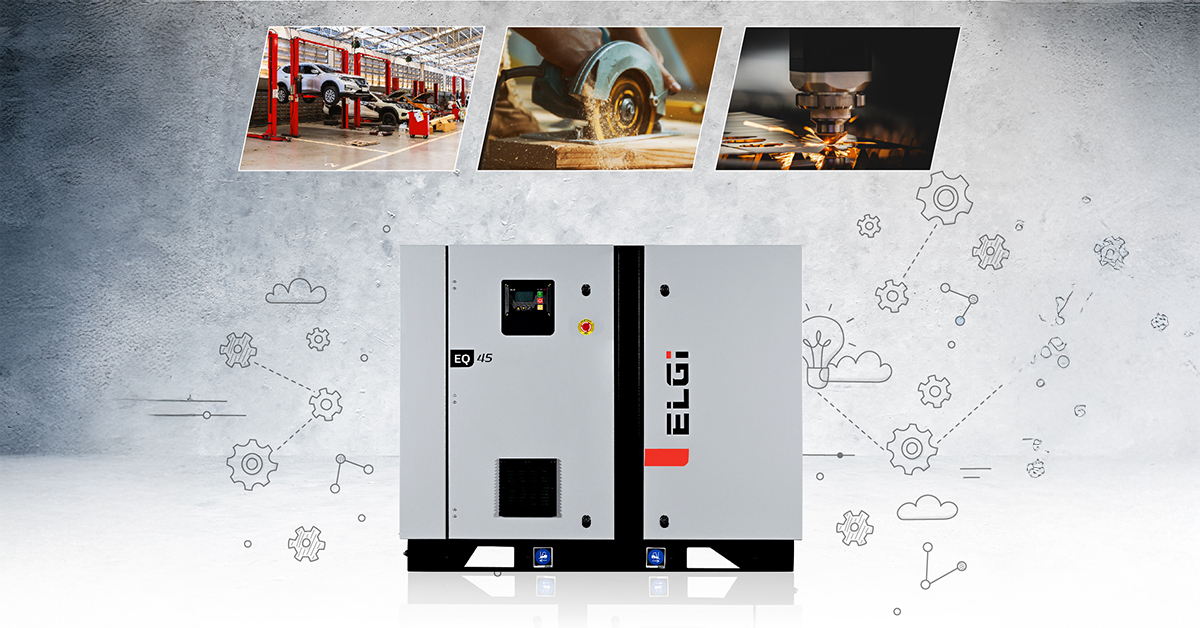
Why the ELGi EN Series is Ideal for Compact Industrial Compressed Air Solutions Busine...
Read More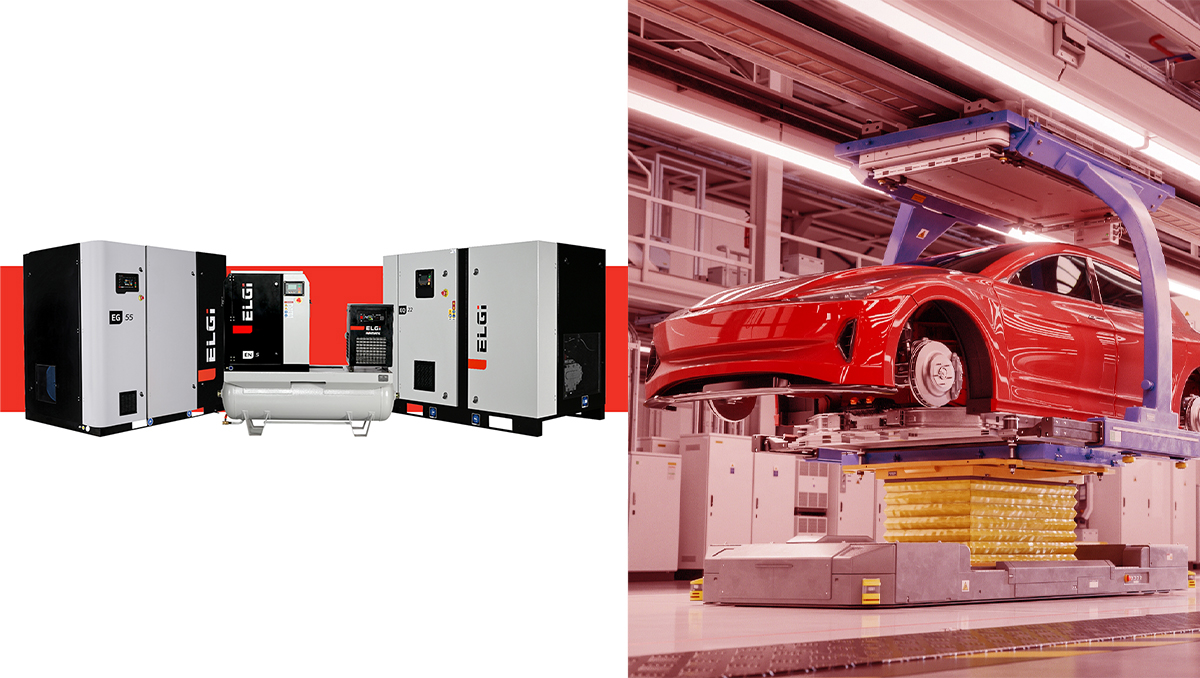
Compressed air is an invaluable resource in the automotive industry, powering everything f...
Read More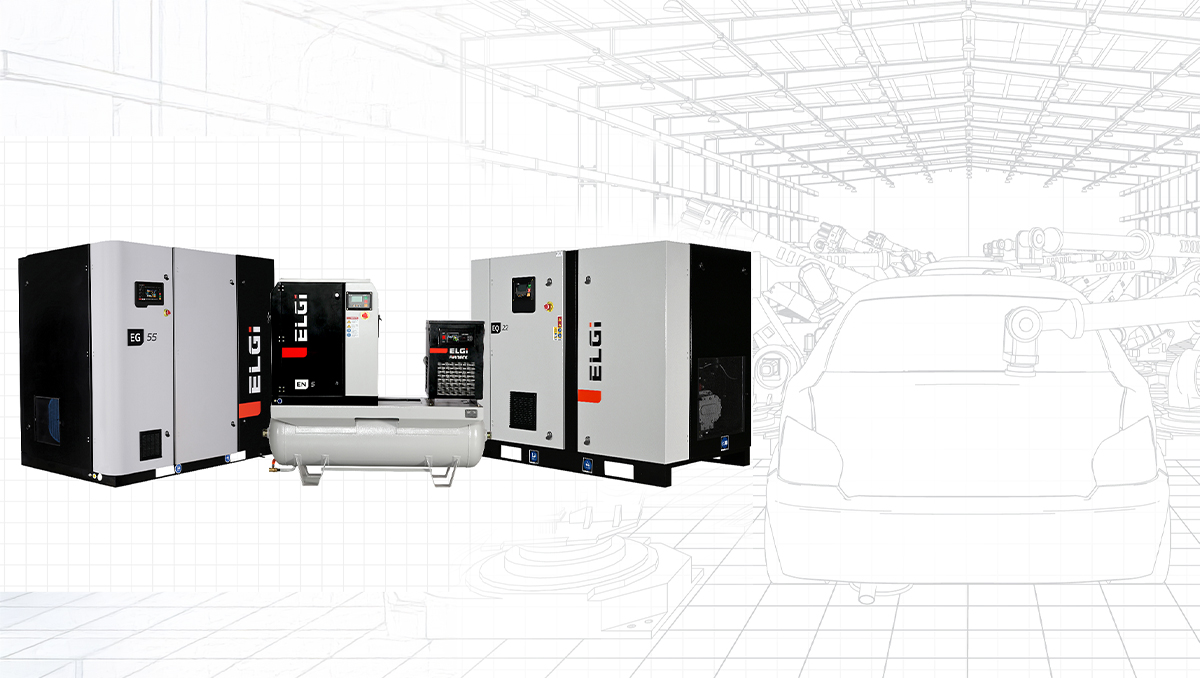
The automotive industry is one of the most dynamic and technology-driven sectors, requirin...
Read More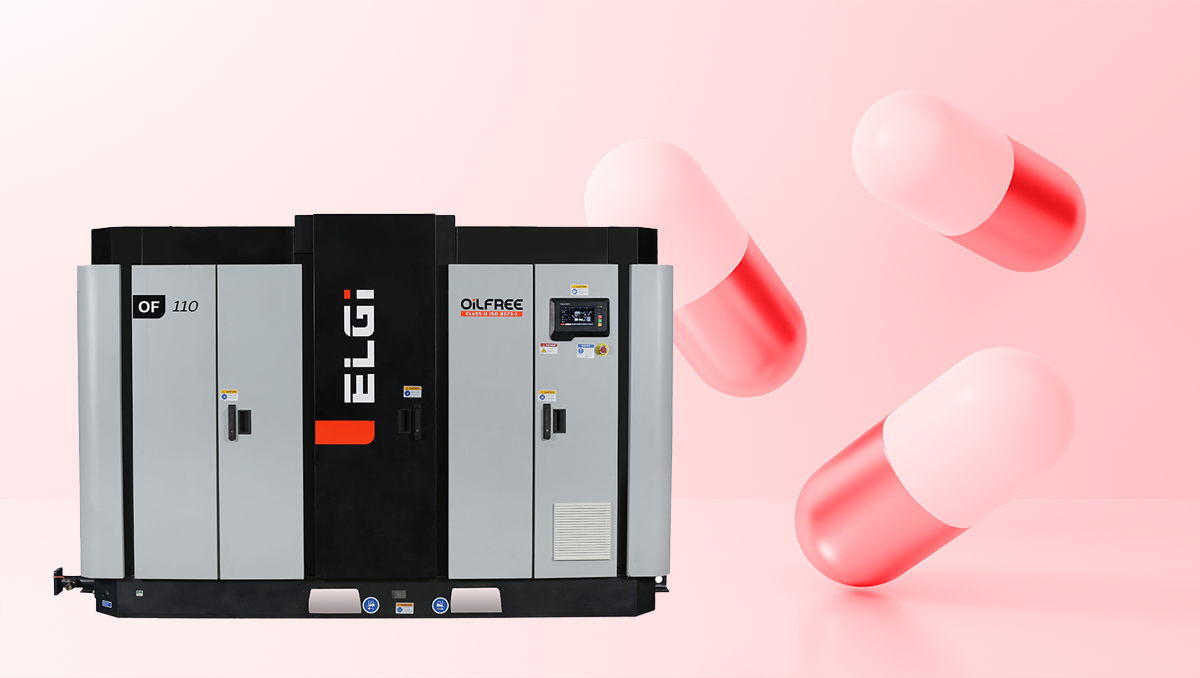
The pharmaceutical industry operates in a realm where precision, purity, and compliance ar...
Read More
Rotary screw air compressors are essential machines used in many industrial applications a...
Read More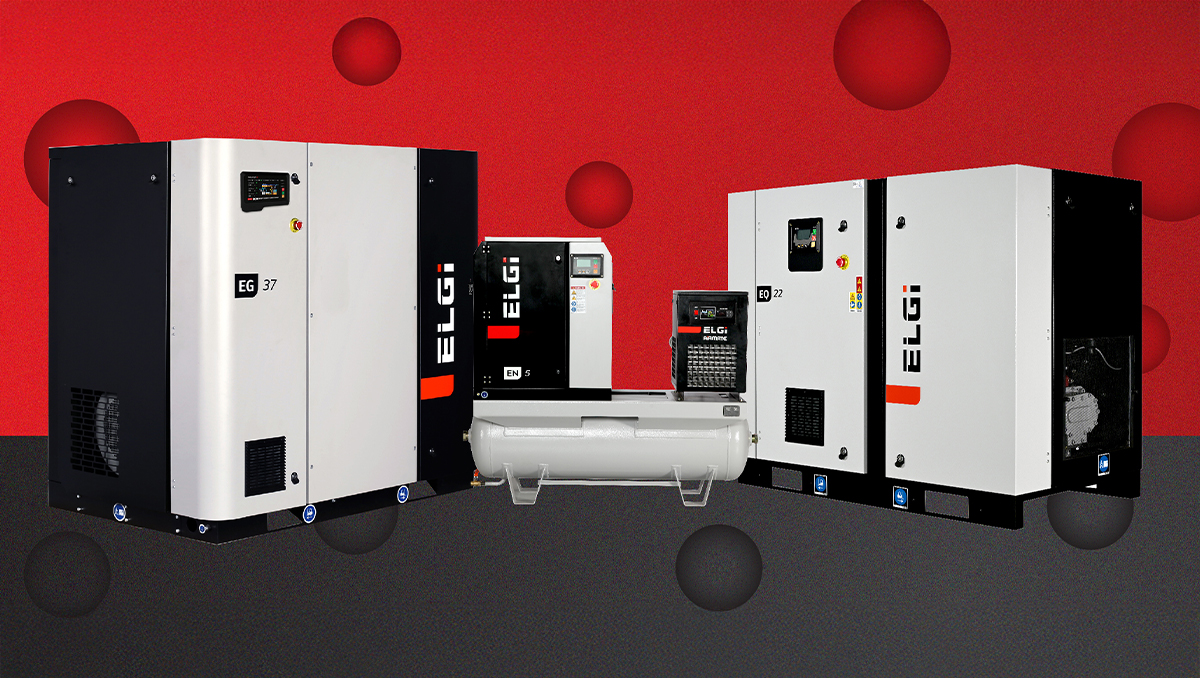
Choosing the right rotary screw compressors is crucial for your industrial operations. In...
Read More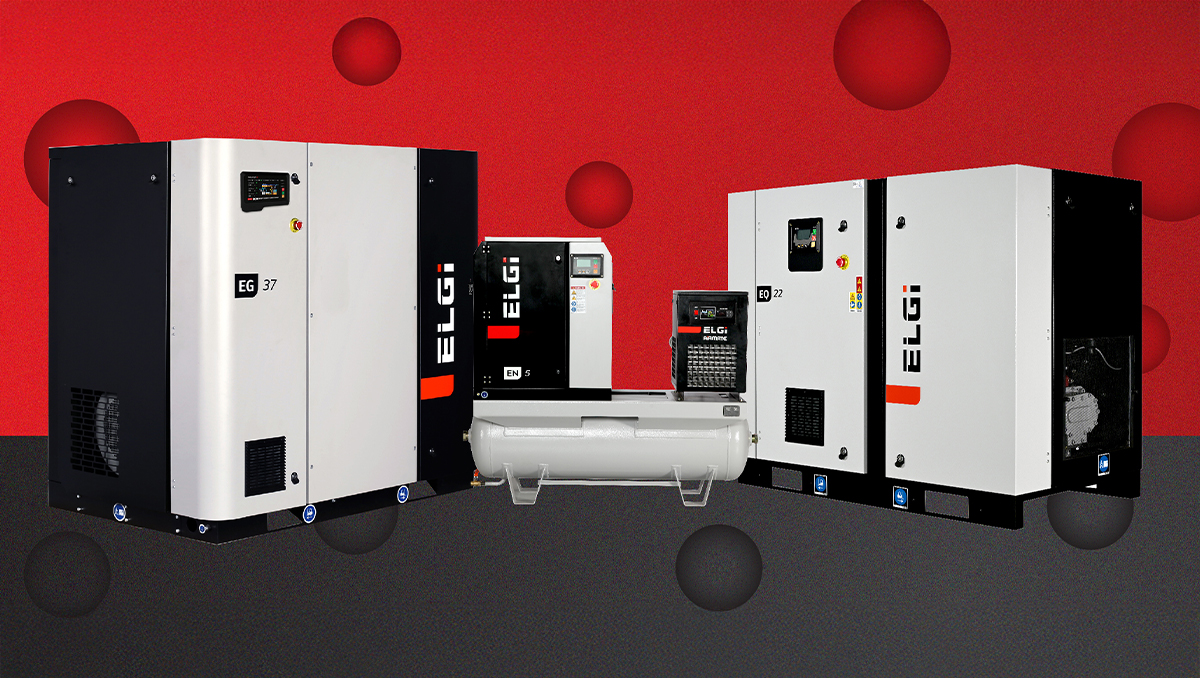
Choosing the right rotary screw compressors is crucial for your industrial operations. In...
Read More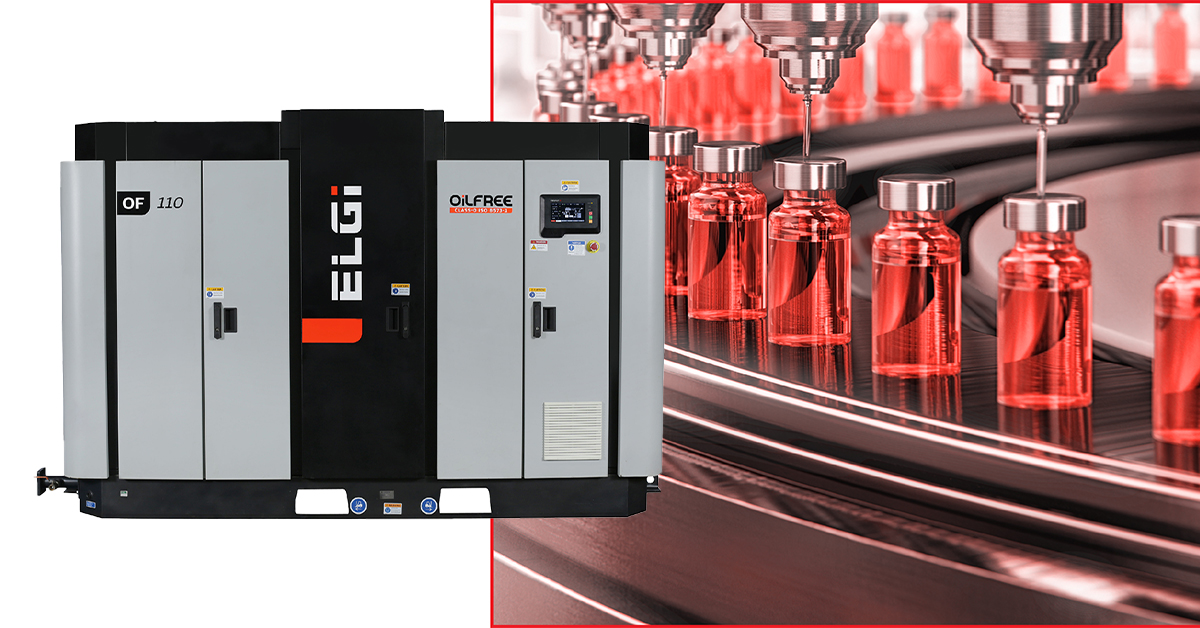
The pharmaceutical industry relies heavily on precision, sterility, and efficiency in ever...
Read MoreBe the first to get updates, learn more and join our explorative world by subscribing to our official compressed air journal.
SUBSCRIBE