Optimising Winter Performance: Comprehensive Maintenance Guide for Compressed Air Systems
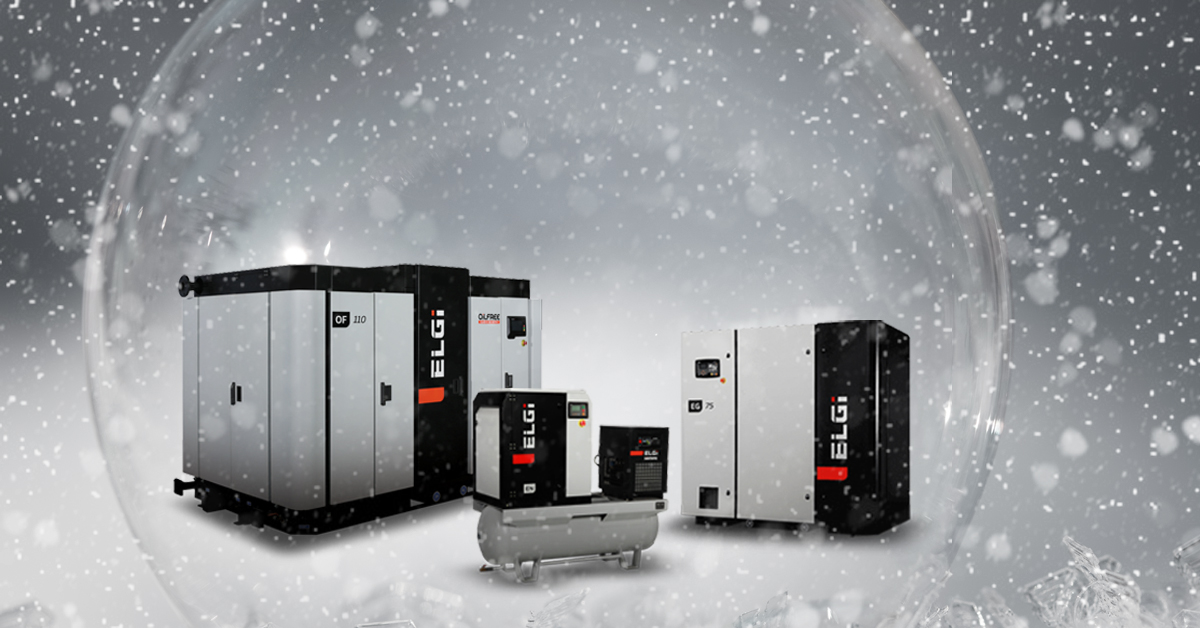
As the temperatures are dropping, it is essential to understand how the cold weather can affect your industrial air compressor efficiency. Air Compressors rely on a consistent air supply, and changes in density can impact their performance and efficiency. Cold weather can cause the lubricating oil in the compressed air system to become more viscous. This can lead to increased resistance in the moving parts, reducing overall efficiency and potentially causing damage if the oil is too thick to properly lubricate components. Cold air can hold less moisture than warm air in the compressed air system. When the compressed air cools down, any moisture present in the system may condense, leading to issues such as freezing in the lines or corrosion within the compressor. Rapid temperature changes, especially during shutdowns, can cause condensation inside the compressed air system. This condensation can lead to rust and corrosion, impacting the efficiency and lifespan of the equipment.
Being aware of these effects and taking proactive steps to prepare your compressed air system is crucial for the winter.
As temperatures drop, manufacturing companies face unique challenges, especially when it comes to maintaining high-quality compressed air systems. Winter brings its own set of hurdles that can compromise the efficiency and functionality of your industrial compressed air solution. To avoid costly repairs and downtime, it is essential to implement a winter air compressor maintenance plan.
Here is a list of steps you can take to safeguard your compressed air system during the colder months ahead.
Check your cooling system
Maintaining your cooling system is vital to prevent potential issues with the condensate in your industrial compressed air system. Ensure any exposed elements like drains or compressed air piping systems are properly insulated. This insulation not only avoids pipe damage but also prevents condensate from infiltrating the air supply.
In extreme cold, consider employing trace heating. This step becomes crucial, especially if you're using a refrigerated air dryer for the compressor. Exposed pipes might drop below the compressed air system’s dew point, causing condensate buildup post-drying.
During winters, regularly inspect air intake openings to shield against excessive snow ingress. This precaution prevents air filter saturation or ice formation at the air intake points.
Check tanks for condensation
During the winter months, moisture can accumulate in your air compressor tanks. This moisture can freeze in cold temperatures. As a result, regular tank inspections are vital for identifying and addressing condensation buildup. The accumulated condensate not only corrodes tanks but also degrades compressed air purity, damaging downstream equipment. Implementing moisture removal systems or draining the excess condensate minimises the risk of damage while maintaining a high-quality industrial air solution.
Check drains for malfunctions
Malfunctioning drains can pose a significant risk in winter, as it can lead to water accumulation within the compressed air system. Ensuring the proper functioning of drains avoids potential disruptions in operations and prevents costly repairs.
There are two primary types of compressor drain valves that are used in the industry: timer and zero-loss electronic drain valves. Timer drains are popular due to their cost-effectiveness and easy installation, but incorrect timing can lead to condensate retention or unnecessary air wastage. Whereas the Zero-loss electronic condensate drain valve conserves compressed air during condensation release and can be easily maintained with a basic maintenance plan and regular check-up.
The EZL condensate drain valve is the latest advancement in drain valve technology. The ELGi Zero Loss (EZL) Drain Valve works on the principle of zero air loss, causing no loss to your industrial compressed air, and thus consequently saving energy.
Check compressed air dryers and filters
Compressed air dryers and filters are responsible for removing water from the compressed air system and are vital in preventing downstream freezing. Air filters can get clogged in winter due to ice buildup and increased rain or snow. This can result in pressure drops and increased contamination risks, impacting product quality. Regular cleaning and replacement schedules are essential to prevent blockages and maintain system performance.
Useful tip: If a dryer or oil-water separator for an air compressor is idle, it's smart to eliminate any standing untreated condensate or cooling water. This precaution prevents potential damage such as cracked pipes or coolers.
Identify and fix compressed air leaks
Compressed air leaks are common and costly issues in industrial compressed air systems. During winter, these leaks can worsen due to temperature fluctuations. Implementing air leak detection programs and promptly repairing leaks can significantly improve energy efficiency and reduce operational costs.
Heat trace or insulate your control lines
Consider using heat trace tape or insulation for your control lines. Freezing temperatures can affect compressor control systems, leading to issues like frozen tube lines and potential valve control problems, resulting in downtime. To prevent this, it is crucial to heat trace and insulate all pneumatic control lines. Extend heat tracing to condensate drains, storage tanks, and any air compression systems for enhanced performance and system reliability.
Invest in a heat recovery system
During winter, it is critical to maximise energy efficiency. Heat recovery systems for air compressors offer a sustainable solution by recovering and reusing the waste heat generated. This recovered heat can be utilised for heating air and water or other processes, reducing the overall energy consumption and operational costs of the plant.
Check out ELGi’s Heat Recovery System (HRS) which saves both cost and the environment by enabling manufacturing companies to recover up to 78% of the heat generated during the process of air compression. Customers can easily connect the Heat Recovery System and use the heat generated in the air compressor to heat up water and air for use in showers and boilers.
Contact Us for Optimised Air Compressor Solutions
If winterising your industrial compressed air system feels too daunting, invest in an air compressor maintenance plan from our ELGi Channel Partners. Conducting an ELGi Air Audit is strongly recommended to identify areas of loss or inefficiencies and improve your air compressor efficiency. Check out our blog to learn more about industrial air compressor audits.
At ELGi, we offer a complete range of air compressors for industrial use that include both fixed and variable speed compressors with both oil-injected and oil-free electric air compressors. ELGi’s wide service network across Europe is readily available to help you with your winterisation. To learn more about our solutions or request a quote, contact our experts or write to us at euenquiry@elgi.com.
RELATED BLOGS
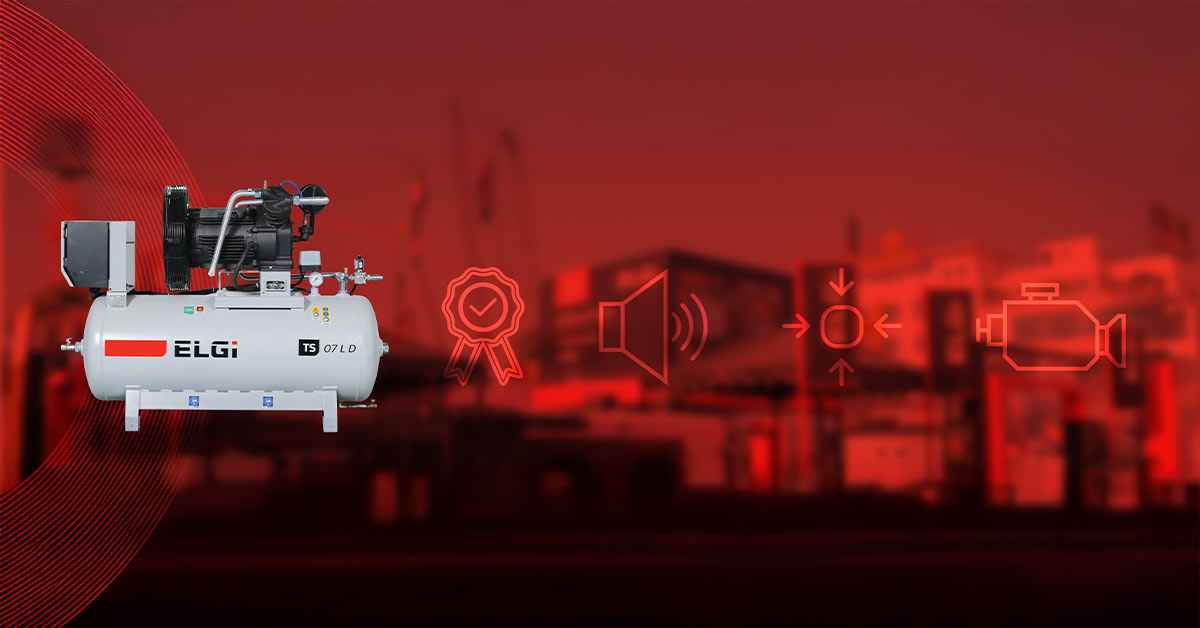
Compressed air is a critical element in many industrial operations, from powering tools to...
Read More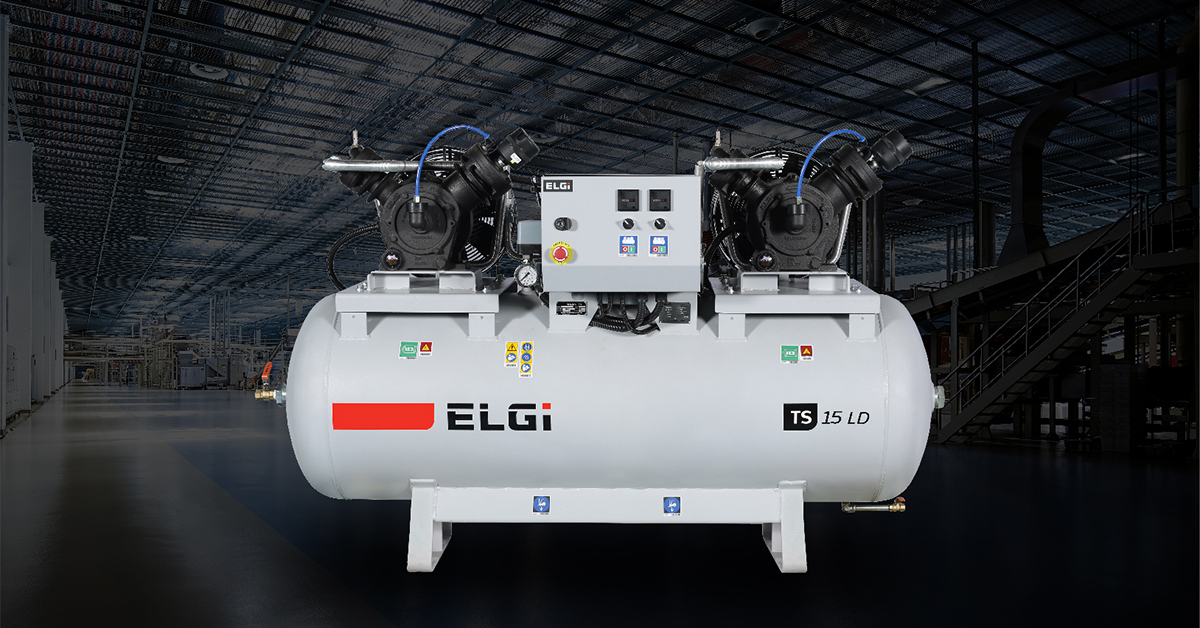
How Oil Lubricated Compressors Work and Their Role in Energy Efficiency Oil lubricated ...
Read More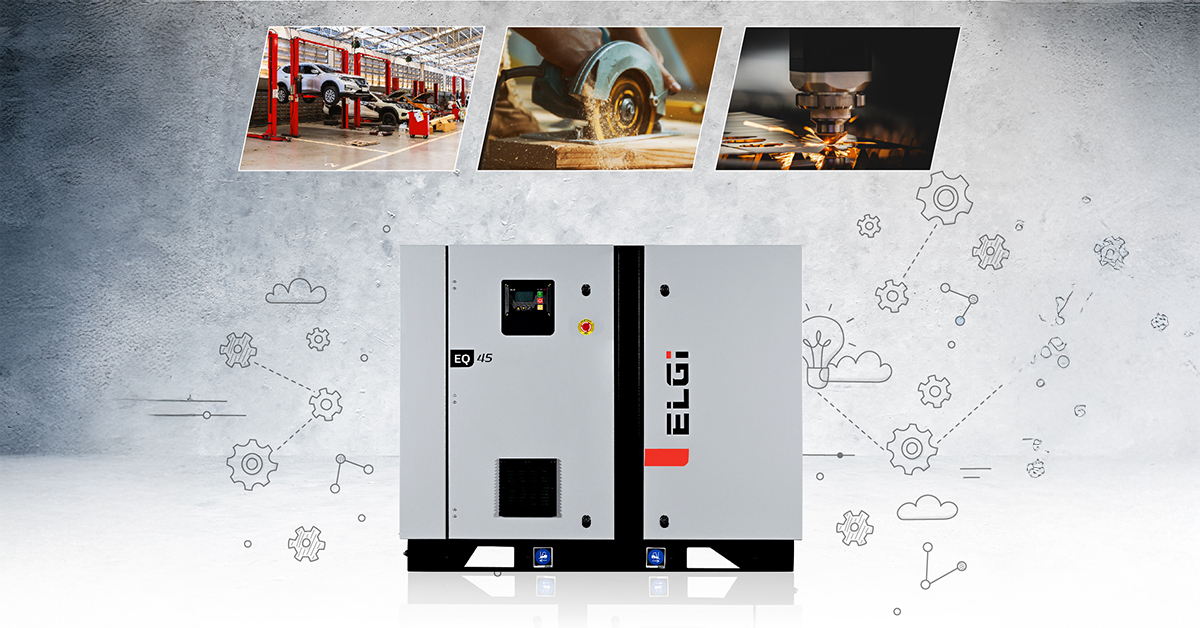
Why the ELGi EN Series is Ideal for Compact Industrial Compressed Air Solutions Busine...
Read More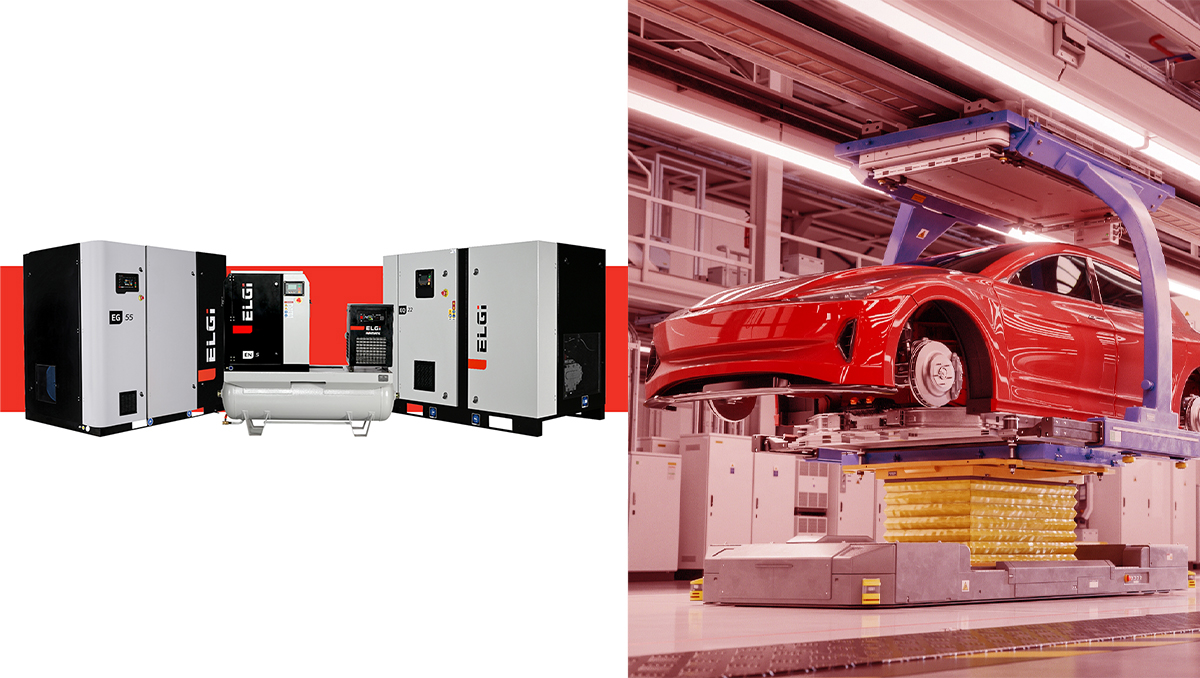
Compressed air is an invaluable resource in the automotive industry, powering everything f...
Read More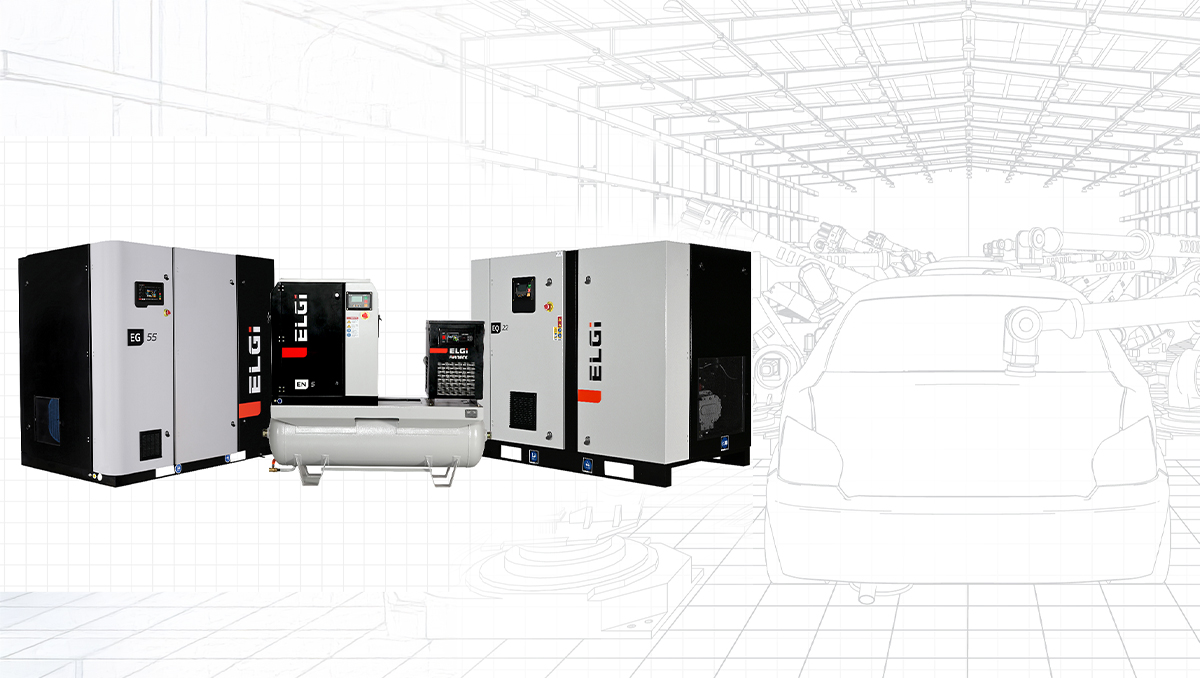
The automotive industry is one of the most dynamic and technology-driven sectors, requirin...
Read More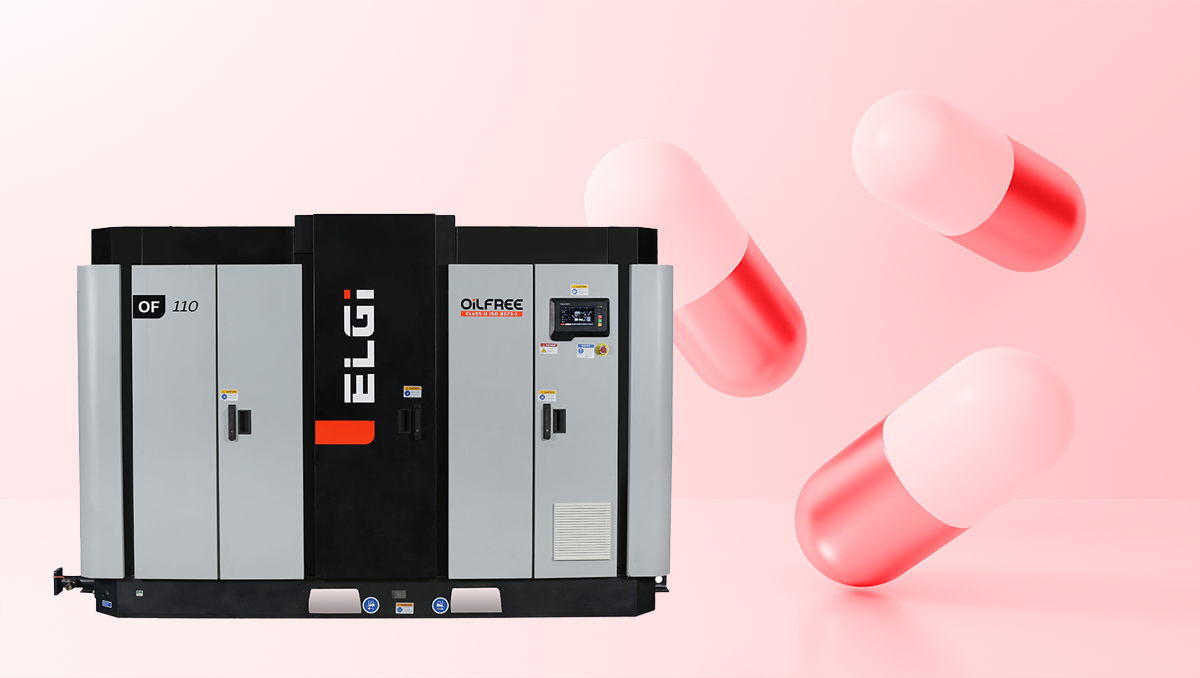
The pharmaceutical industry operates in a realm where precision, purity, and compliance ar...
Read More
Rotary screw air compressors are essential machines used in many industrial applications a...
Read More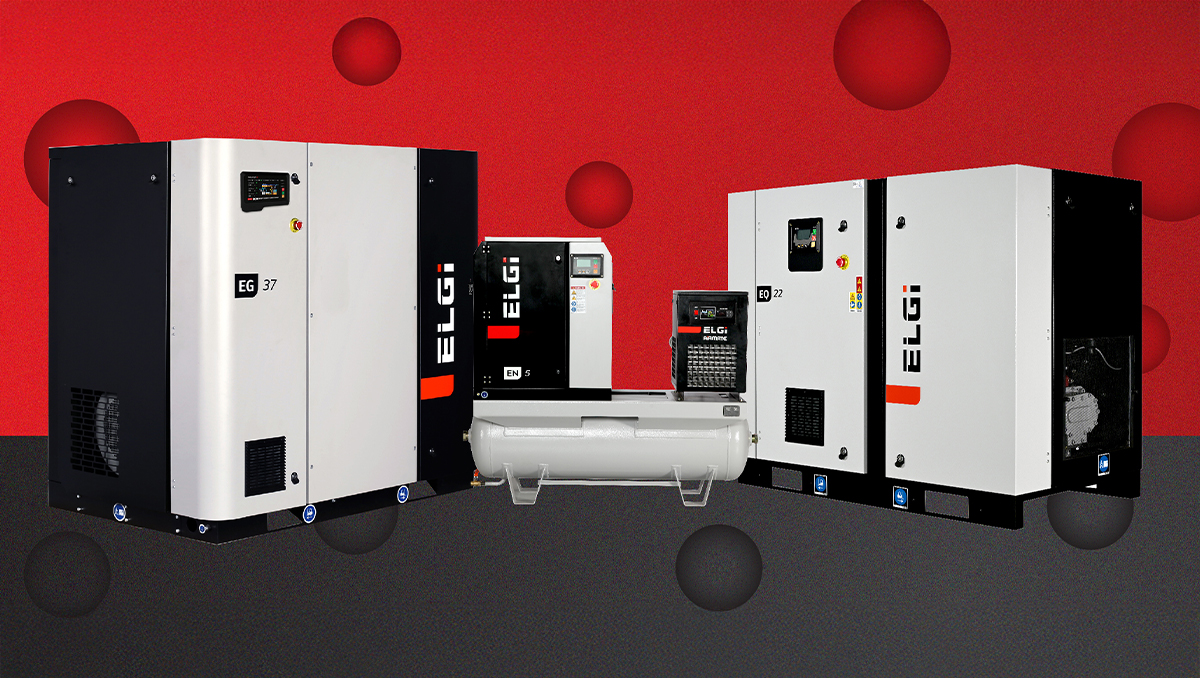
Choosing the right rotary screw compressors is crucial for your industrial operations. In...
Read More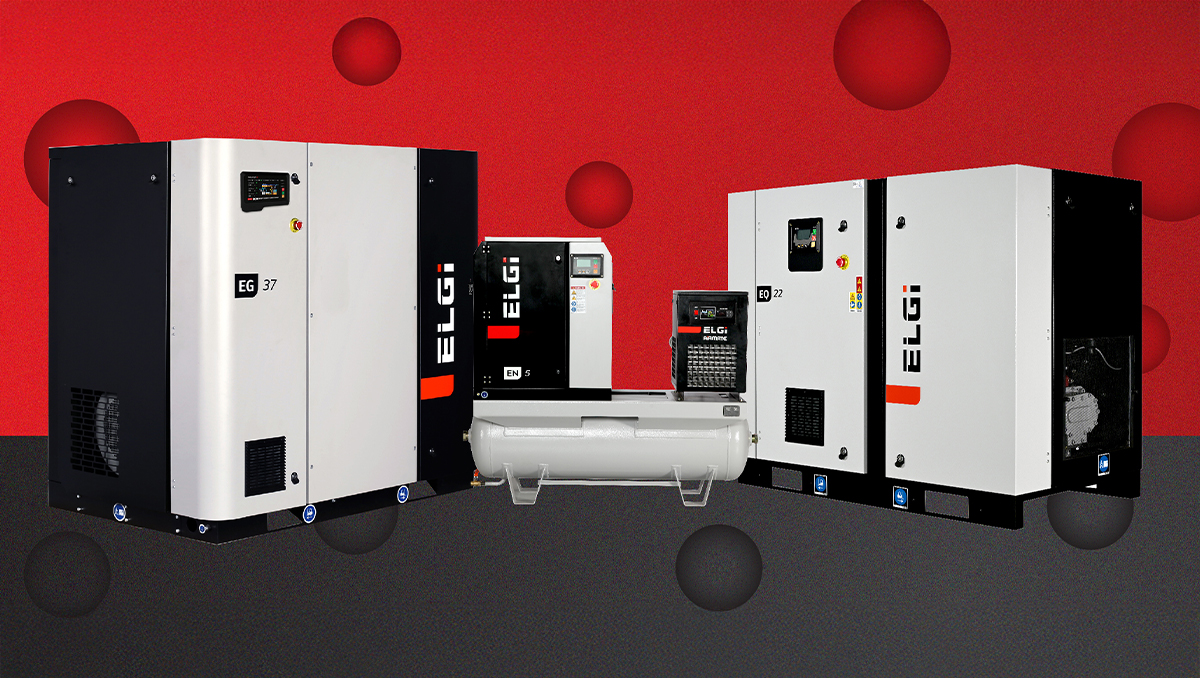
Choosing the right rotary screw compressors is crucial for your industrial operations. In...
Read More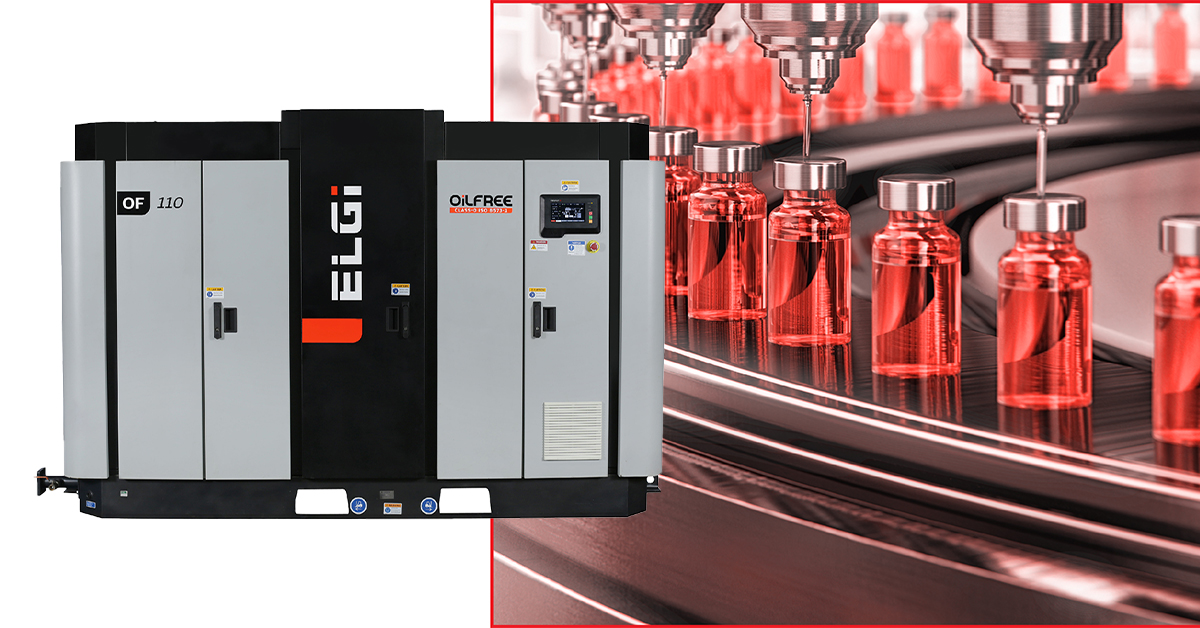
The pharmaceutical industry relies heavily on precision, sterility, and efficiency in ever...
Read MoreBe the first to get updates, learn more and join our explorative world by subscribing to our official compressed air journal.
SUBSCRIBE