Air Compressor Usage and Problems in Food Processing Plants
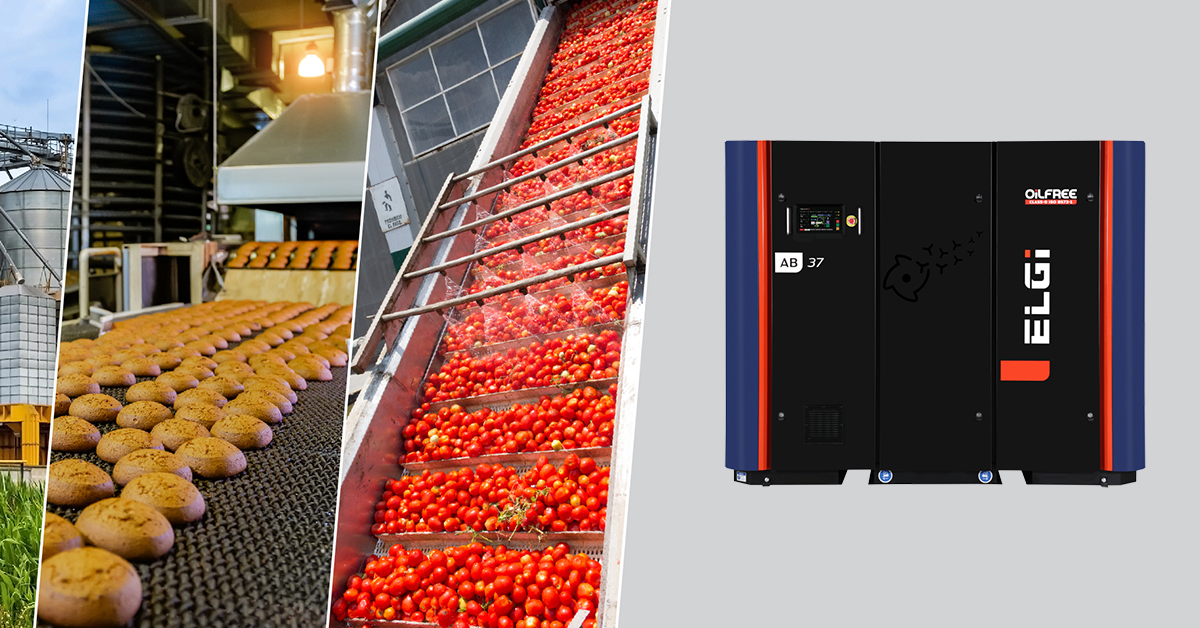
Air compressors play a pivotal role in food processing plants, ensuring that production processes are energy-efficient and uphold the highest standards of food safety. Compressed air is utilised for various applications, such as mixing ingredients, packaging movement with air filtration, and air filtration to create sanitary food products.
Oil-free compressors are vital for food safety, delivering Class ‘0’ oil-free air as per ISO8573-1 to minimise contamination risks. ELGi’s oil-free compressors are ISO22000 certified, aligning with Food Safety Management Standards in the Food & Beverage Industry.
The Case Against Oil-Lubricated Air Compressors in Food Processing Plants
Air compressors are indispensable in the food and beverage production process, playing key roles from activating valves and moving conveyor belts to handling delicate food items with precision. While compressed air systems are crucial, the type of air compressor used can significantly impact product safety and operational efficiency.
The Drawbacks of Oil-Lubricated Compressors:
Contamination Risk: Oil-lubricated compressors carry a risk of oil contaminating the compressed air, which can then contaminate food products. Such contamination can lead to product spoilage, and recalls, and tarnish a brand's reputation.
Increased Operational Costs: The potential for oil leaks not only poses a contamination risk but can also lead to increased maintenance and operational costs to prevent or address contamination.
Complex Maintenance: Oil-lubricated systems require regular oil changes, filter replacements, and disposal of used oil, complicating maintenance routines and increasing the environmental burden.
Conversely, oil-free compressors, such as those with dry screws or water-injected technology, eliminate the risk of oil contamination. These systems provide cleaner, Class ‘0’ oil-free compressed air, as defined by ISO8573-1, making them a safer and more compliant choice for food and beverage industry applications.
Choosing oil-free air compressors for food and beverage processing not only supports compliance with food safety standards but also reduces the risk of product contamination and recalls, ensuring the integrity of the production process and safeguarding consumer trust.
Best Practices For Oil-Free Air Compressor Maintenance
To avoid problems, it is essential to follow best practices for air compressor maintenance in food processing plants. By following these practices, food processing plants can ensure optimal performance and safety of their air compressor systems.
Maintaining oil-free air compressors for the food and beverage industry involves several key steps:
Inspection: Regularly inspect the air compressor for leaks, bends, and unnecessary connections, and inspect all compressor components to ensure optimal performance.
Stabilisation: Maintain the proper operational environment to eliminate conditions that detract from performance and reduce the chances of faults.
Air Inlet: The air inlet should receive air only from clean, outdoor sources, and a filter or screen should be placed at the intake valve to keep the intake air clean. Replace any filters that require replacement due to dirt, lifetime, service interval, or other causes to avoid contamination.
Air Receiver: Air receivers store compressed air before it enters the production machinery, so check that the air receiver is clean and dry. Ensure that the safety valves on your air tank are set to at least 10% or 1 bar g above the operating pressure, and check that the safety valves are positioned in a way that prevents water from collecting inside the unit.
Air Distribution System: Ensure that the air distribution system is free of leaks, bends, and unnecessary connections.
Electrical Components: Ensure that the electrical components are not damaged and that the electric air compressor is properly grounded.
Tools: Ensure that any tools you have hooked to the oil-free compressors don’t have pulled triggers before you power up the machine.
Conclusion
These services and solutions aim to ensure the highest quality standards and the safety of the end products in various industries. Additionally, ELGi provides excellent service and post-sale support to its customers via a rapid response system, ensuring minimal downtime. Our Aftermarket offering includes special maintenance programs, remote monitoring systems, as well as genuine spare parts, to avoid unexpected compressor failures and ensure optimal performance.
RELATED BLOGS
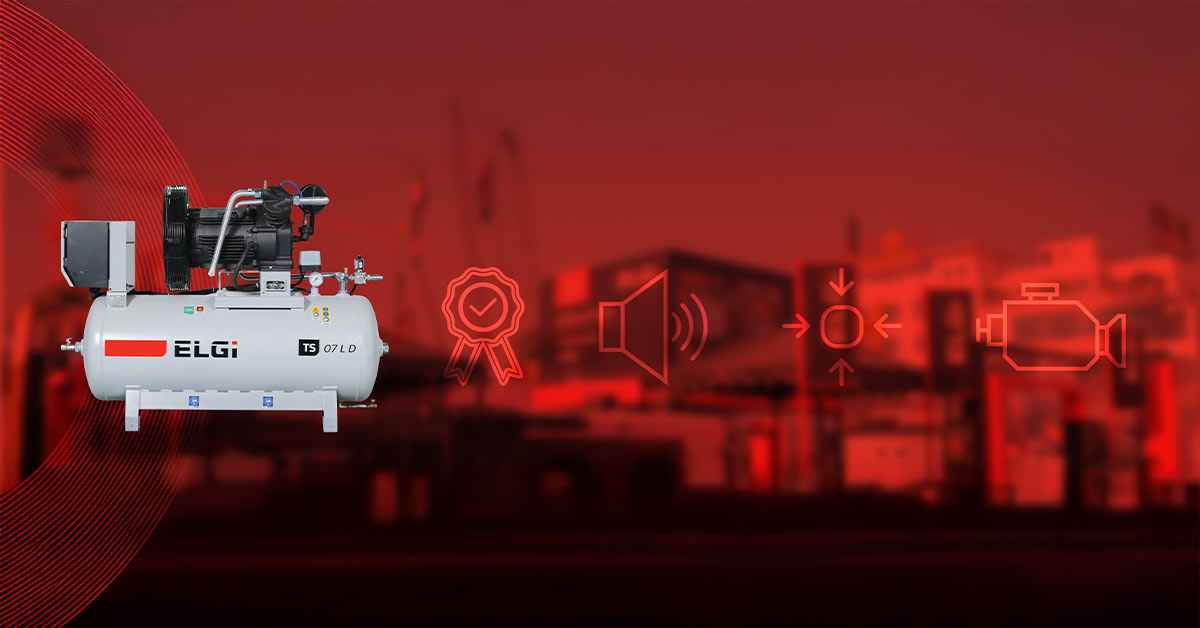
Compressed air is a critical element in many industrial operations, from powering tools to...
Read More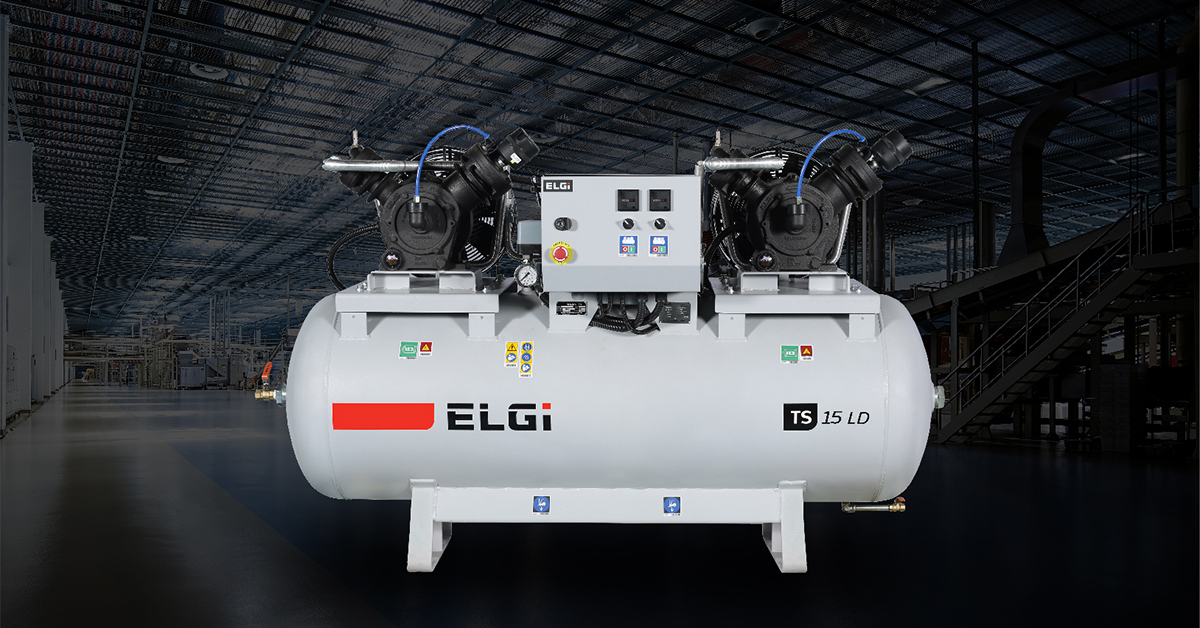
How Oil Lubricated Compressors Work and Their Role in Energy Efficiency Oil lubricated ...
Read More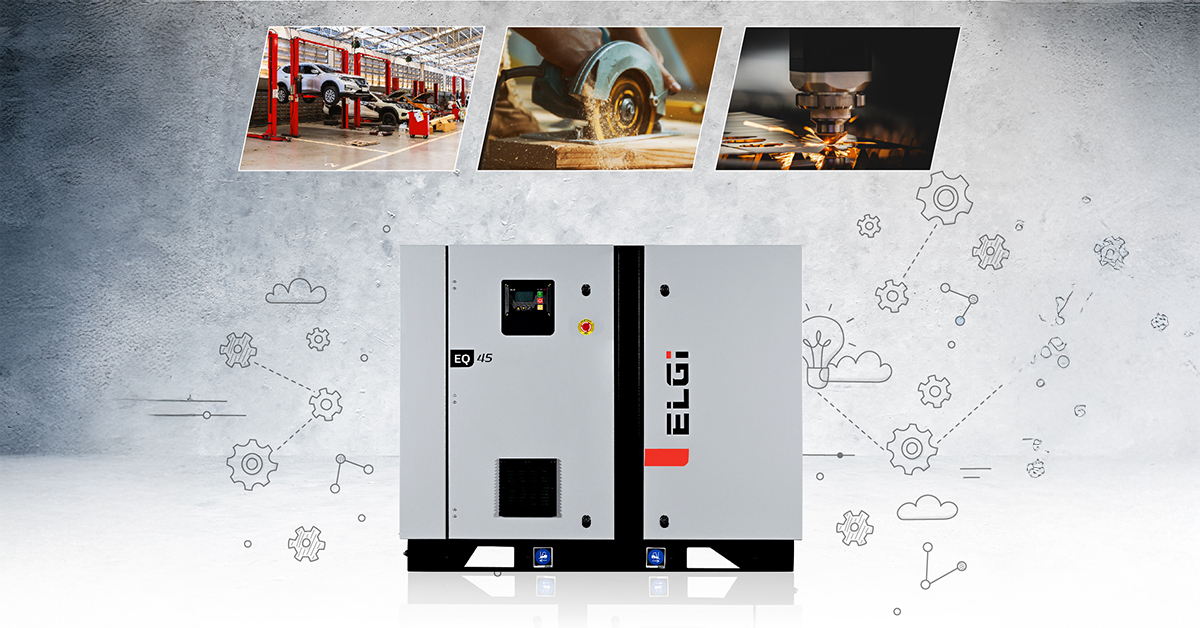
Why the ELGi EN Series is Ideal for Compact Industrial Compressed Air Solutions Busine...
Read More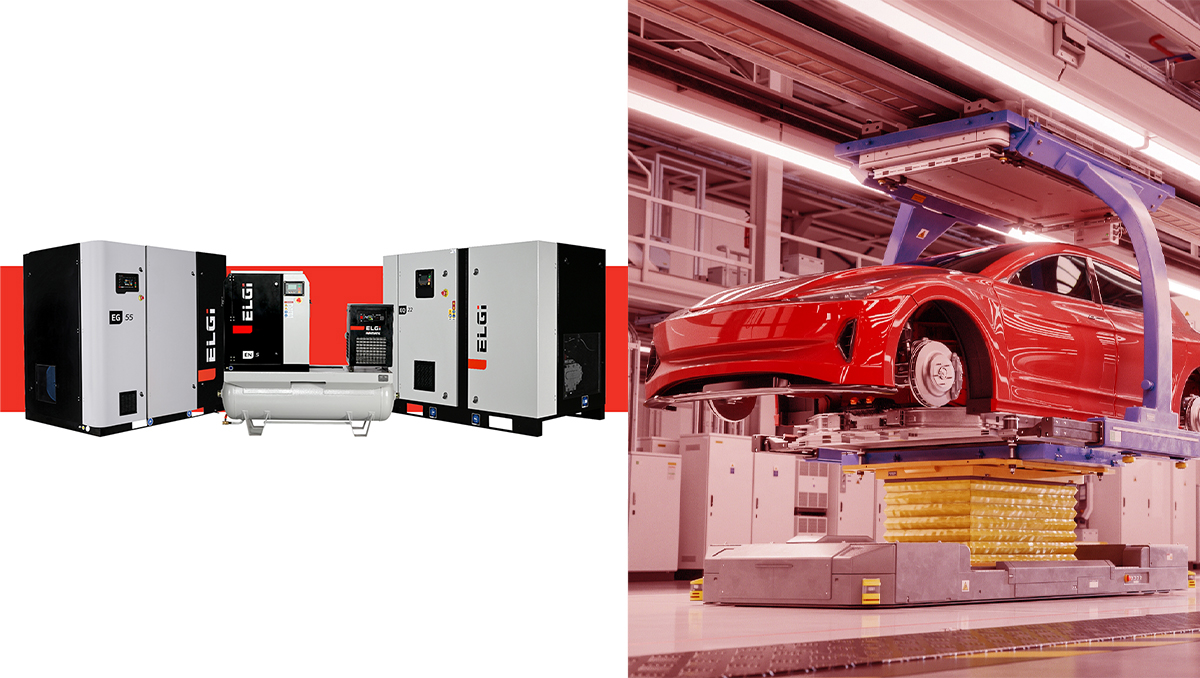
Compressed air is an invaluable resource in the automotive industry, powering everything f...
Read More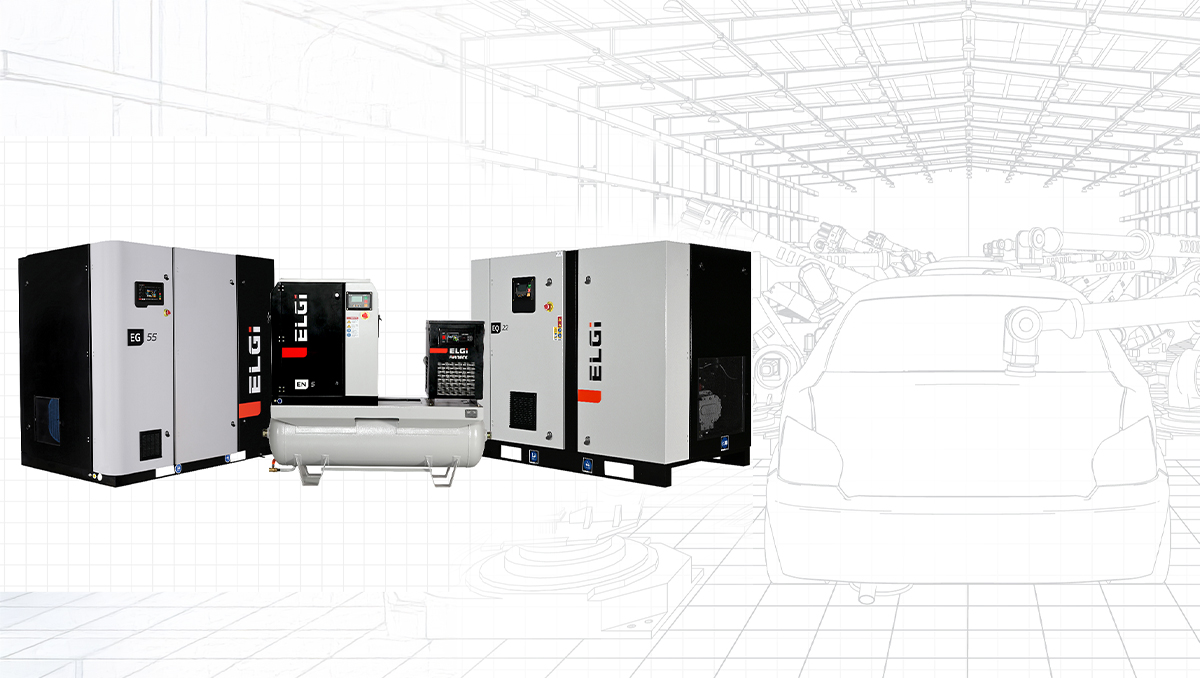
The automotive industry is one of the most dynamic and technology-driven sectors, requirin...
Read More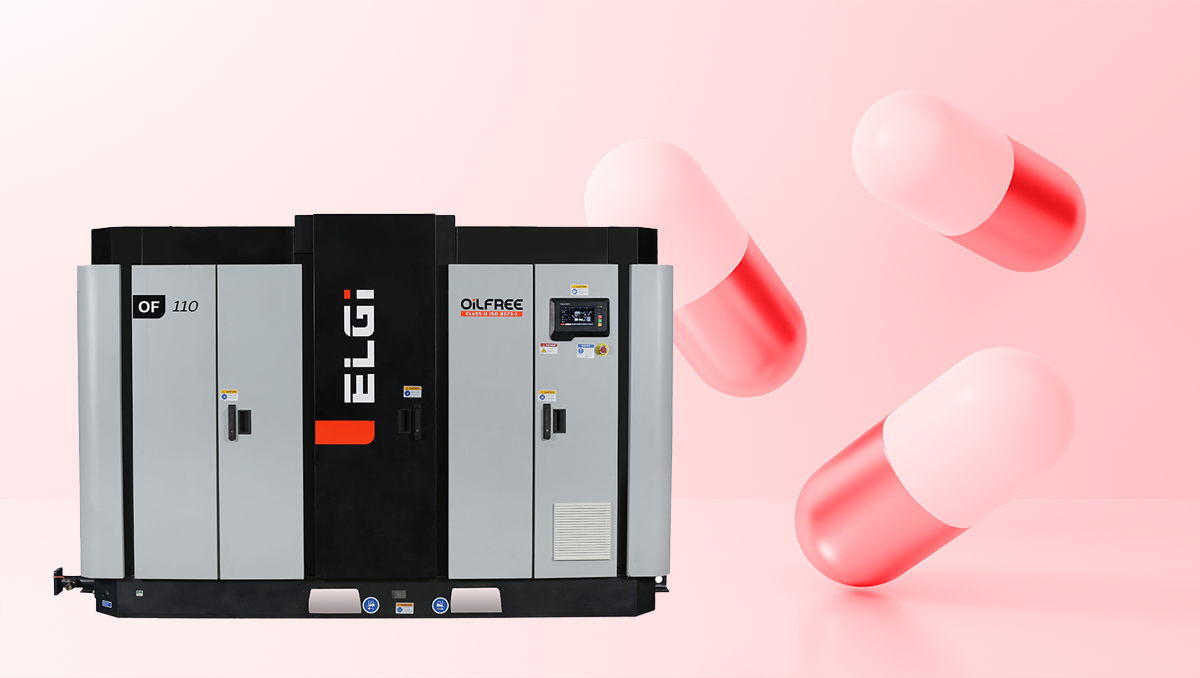
The pharmaceutical industry operates in a realm where precision, purity, and compliance ar...
Read More
Rotary screw air compressors are essential machines used in many industrial applications a...
Read More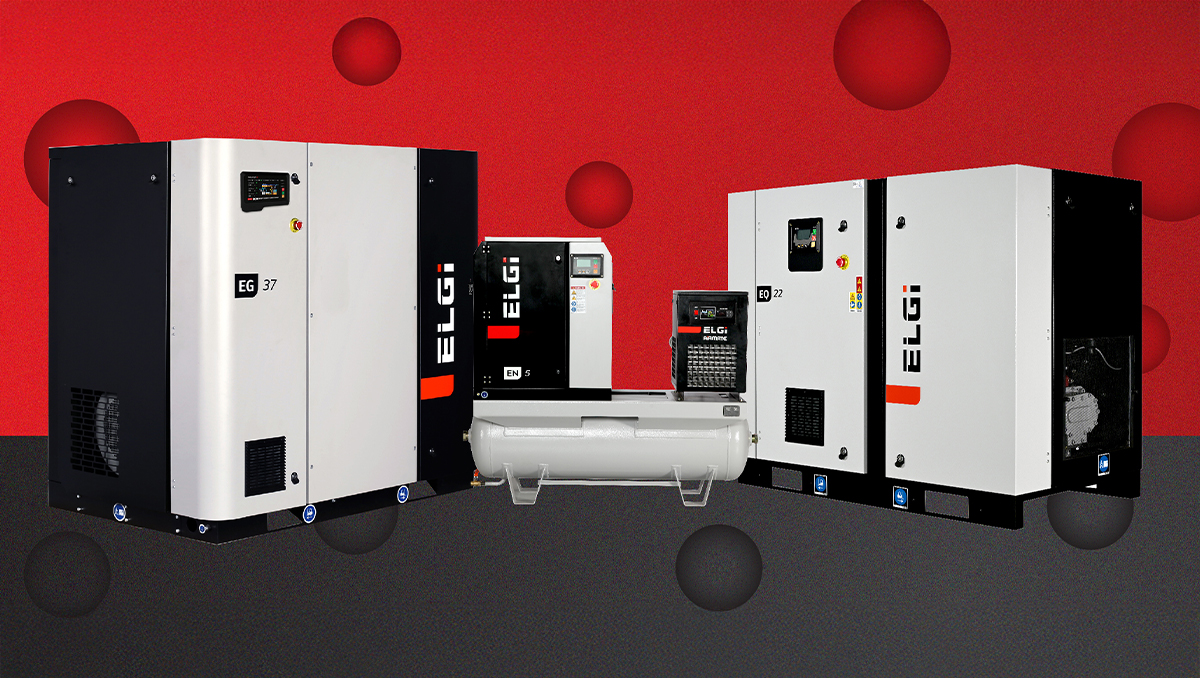
Choosing the right rotary screw compressors is crucial for your industrial operations. In...
Read More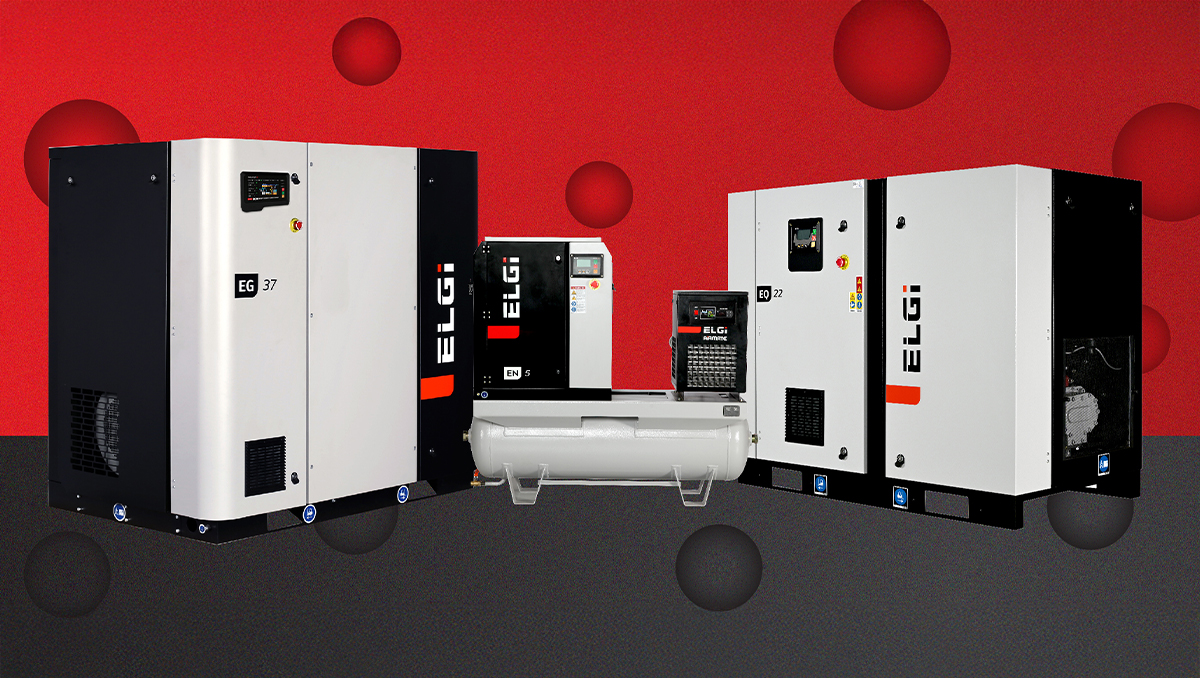
Choosing the right rotary screw compressors is crucial for your industrial operations. In...
Read More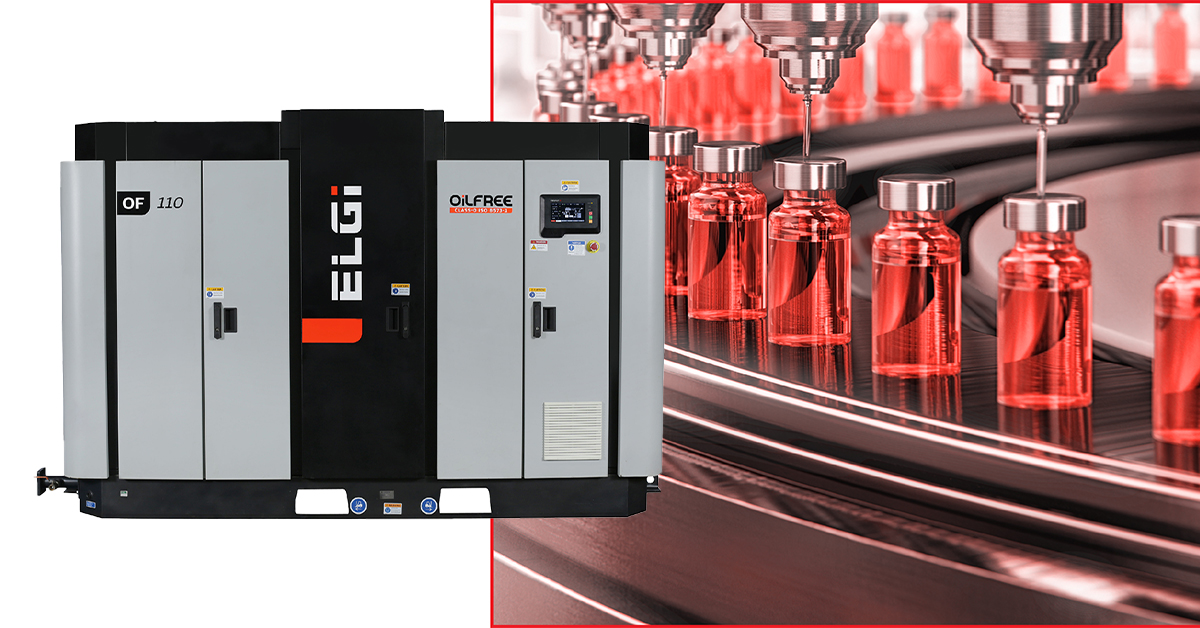
The pharmaceutical industry relies heavily on precision, sterility, and efficiency in ever...
Read MoreBe the first to get updates, learn more and join our explorative world by subscribing to our official compressed air journal.
SUBSCRIBE