Aria classe zero: raggiungi i Tuoi obiettivi di sostenibilità garantendo al tempo stesso una qualità del prodotto conforme alle normative
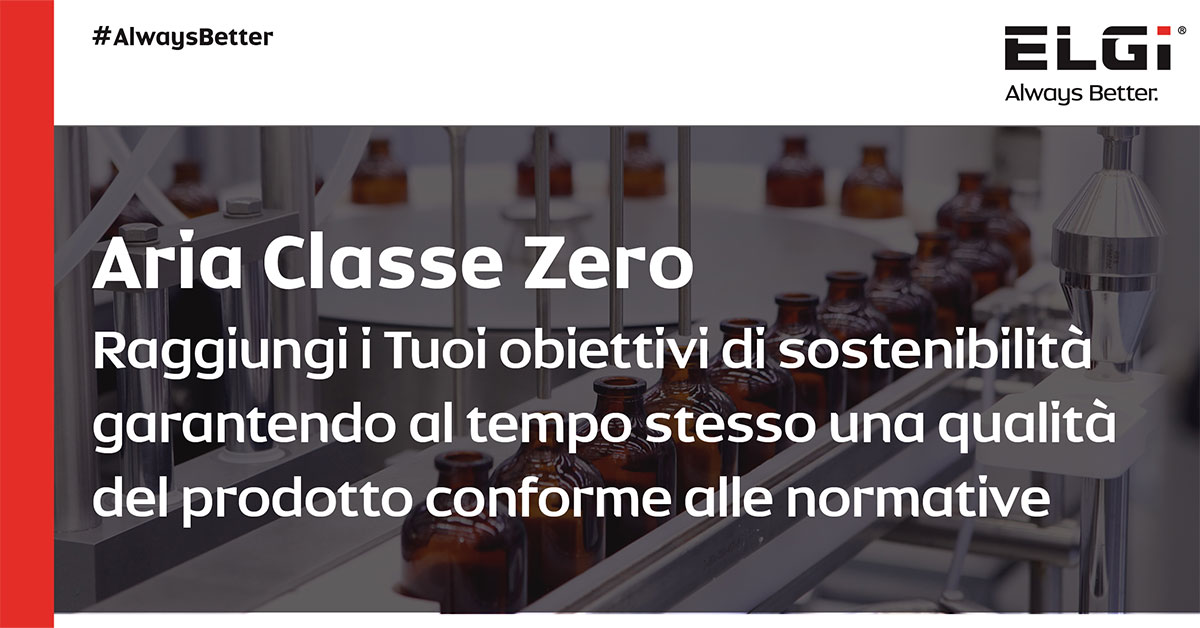
Affrontare la richiesta di aria compressa per il settore farmaceutico, offrendo al tempo stesso miglioramenti in termini di efficienza energetica, sostenibilità e crescita dei margini
Autore: David De Pril, Head of Product Management and Marketing, ELGi Europe
L'aria compressa ha sempre presentato diversi svantaggi, con ripercussioni sulla produzione e sulla movimentazione dei farmaci, tra cui elevati costi di manutenzione, elevato rischio di contaminazione e presenza di umidità. La qualità dell'aria compressa in un processo di produzione farmaceutica è direttamente correlata alla qualità del prodotto finale. Un tempo le aziende farmaceutiche potevano permettersi il lusso di pagare di più per avere questa qualità. Oggi però anche in questo settore si deve bilanciare l'aumento dei costi e le emissioni di energia dell'impianto mantenendo allo stesso tempo la qualità del prodotto e l'efficienza del processo. Questo significa mettere in discussione le norme esistenti e cercare soluzioni innovative per ottenere aria compressa di qualità.
Inoltre, anche la riduzione delle emissioni e del consumo di energia nell'ambito delle attività è oggetto di una maggiore attenzione da parte dei responsabili politici. In Europa, l'efficienza energetica e l'obiettivo più ampio della riduzione delle emissioni di carbonio si aggiungono alle pressioni delle industrie manifatturiere. Indipendentemente dall'attuale pandemia e dal previsto rallentamento globale, l'iniziativa faro della Commissione europea (il Green Deal europeo) rimane una priorità fondamentale che mira a "trasformare l'UE in una società equa e prospera, con un'economia moderna, competitiva ed efficiente sotto il profilo delle risorse". Le aziende di successo ed economicamente sostenibili sanno che devono prendere le decisioni di investimento ora per proteggere la loro sopravvivenza nel medio termine. L'industria ha la responsabilità di fare la sua parte per rendere l'UE a emissioni zero entro il 2050, il che include il raggiungimento dell'obiettivo intermedio di una riduzione del 55% delle emissioni di CO2 entro il 2030.
La direttiva Ecodesign è riconosciuta come la politica europea più efficace per promuovere il risparmio energetico. Questa politica (che include il LOTTO 31) stabilisce requisiti obbligatori di efficientamento energetico per una gamma di prodotti, tra cui i compressori. Il gruppo di prodotti "Compressori" è stato identificato come gruppo prioritario nella prima iterazione del piano di lavoro sulla progettazione ecocompatibile (periodo 2009-2011) e tutte le indicazioni fanno presupporre che i compressori (ENER Lotto 31) saranno inclusi nel rinnovo della Commissione europea per coprire il periodo 2020-2024.
Tutto ciò serve a focalizzare l'attenzione dell'industria (incluso il settore dell'aria compressa) sull'innovazione per soddisfare la richiesta del settore manifatturiero verso nuovi modi per fornire aria compressa di qualità e più sostenibile. Stanno ora giungendo sul mercato nuovi processi e tecnologie che consentono alle aziende di contenere i costi senza scendere a compromessi su altri fattori critici.
Purezza dell'aria
Per uno stabilimento farmaceutico l'aria compressa è una delle utenze di importanza assoluta. L'assenza di aria compressa porterebbe l'impianto all'arresto, proprio come la mancanza di energia elettrica. Tuttavia, la mancanza di aria di qualità, che non soddisfa i requisiti di conformità globali di ISO 8573, 1:2010 e ISO 8573-7, potrebbe causare un elevato rischio di contaminazione e umidità. Ne conseguirebbero richiami di farmaci e divieti di esportazione, danneggiando così la reputazione dell'azienda in questione.
In tutti questi processi gli stabilimenti devono mantenere una tolleranza zero per le impurità. I compressori a vite oil free sono la scelta preferita in quanto comprimono l'aria all'interno di una camera di compressione senza olio, per evitare che l'olio di lubrificazione contamini l'aria compressa.
Fino a pochi anni fa le aziende utilizzavano compressori a iniezione d'olio con filtrazione che permetteva di raggiungere standard di qualità dell'olio di "Classe 1", cioè aria con non oltre 0,01 mg/m3 di olio residuo. Per garantire che olio residuo, particelle trasportate dall'aria o vapore non potessero entrare nel sistema, sono stati utilizzati essiccatori d'aria a valle e filtri a doppia linea per purificare ulteriormente l'aria.
Oggi, i settori maggiormente sensibili alla qualità come quello farmaceutico, fanno uso di compressori d'aria oil free che erogano aria senza olio di "Classe 0" secondo ISO:8573 (P-2):2007, per garantire aria completamente priva di contaminanti per varie applicazioni nei rispettivi processi di produzione e confezionamento.
Tuttavia, fino a poco tempo fa, questi compressori erano costosi e venivano utilizzati principalmente da grandi aziende e da quelle che esportavano farmaci in mercati con standard rigorosi (ad es. la Food and Drug Administration statunitense). Grazie all'avanzata tecnologia oil free nei compressori certificati "Classe 0", ogni azienda può essere certa di avere aria senza olio che soddisfa gli standard più severi, ma anche di ottenere risparmi energetici e tempi di attività molto più elevati.
Niente olio. Acqua
La conformità e le norme a livello qualitativo definiscono chiaramente l'industria farmaceutica, spingendo così i produttori di compressori a evolversi e dimostrare il loro impegno per la purezza dell'aria compressa secondo gli standard più elevati. Molto spesso la ricerca di tale purezza porta i produttori farmaceutici agli estremi. Ad esempio, l'installazione di più filtri invece di uno solo, che aumenta il consumo di energia e incrementa la complessità con conseguente maggiorazione dei costi e della frequenza di manutenzione.
Da diversi anni l'industria farmaceutica considera i compressori oil free a iniezione d'acqua come un'alternativa altamente efficiente ai tradizionali compressori oil free a due stadi a vite a secco. Questo tipo di compressori eroga la stessa aria compressa di "Classe 0" con un design monostadio molto più semplice, in cui l'acqua (e non l'olio) viene iniettata nell'airend raffreddandolo e sigillando il sistema. Di conseguenza, il compressore e l'airend funzionano a una velocità molto inferiore rispetto a un compressore a vite a secco, il che si traduce in maggiore affidabilità, minore usura delle parti, minore manutenzione e migliore efficienza energetica.
C'è solo un "ma". La maggior parte dei compressori oil free a iniezione d'acqua sono dotati di componenti aggiuntivi come purificatori ad osmosi inversa (RO) sensibili nella linea di ingresso dell'acqua, materiali speciali per il rotore e complessi sistemi di cuscinetti. Questi sistemi hanno dimostrato di essere costosi e soggetti a guasti.
Oil free e a iniezione d'acqua. Il Cambiamento
Oggi c'è una risposta a questi problemi:
- un design con circuito idraulico ad anello chiuso di minore complessità
- nessun cuscinetto speciale o materiali particolari
- non occorrono sistemi di purificazione RO sensibili
Insomma, un design innovativo e molto più affidabile. Per la produzione farmaceutica, dove i guasti equivalgono a perdite significative e dove la riduzione dei costi energetici e di manutenzione è fondamentale, i vantaggi sono evidenti.
In questo sistema a circuito chiuso, il rischio di contaminazione è ulteriormente ridotto. L'acqua viene rabboccata e risciacqua e pulisce l'interno del compressore. Inoltre, il compressore scarica la condensa che non richiede alcun trattamento aggiuntivo (poiché è analoga all'acqua potabile).
Infine, oltre ad un'acqua più pulita e a un funzionamento più lento del compressore, il sistema ad anello chiuso si basa su cuscinetti standard più economici rispetto a quelli utilizzati nei tradizionali compressori lubrificati a olio, riducendo ulteriormente complessità e costi.
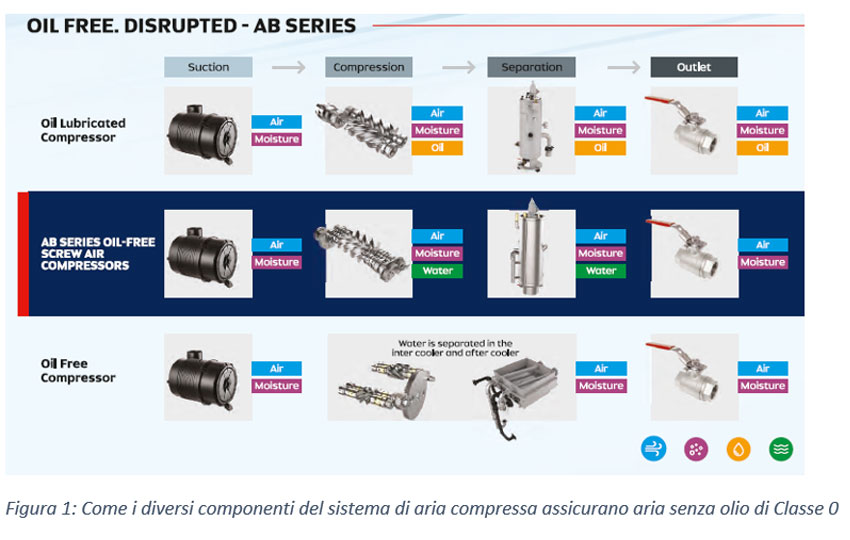
Il costo totale di proprietà di questo compressore a iniezione d'acqua è notevolmente inferiore (8% o più) rispetto ai tradizionali compressori oil free a vite a due stadi grazie al ridotto consumo energetico e alla semplicità del design, nonché alla facilità di manutenzione. Rispetto alle soluzioni a iniezione d'olio, questi sistemi sono ancora più interessanti in quanto la filtrazione a valle è meno sollecitata.
Semplicità, efficienza e requisiti di manutenzione meno complessi, le regole di progettazione avanzata di questi recentissimi compressori oil free a iniezione d'acqua ad anello chiuso possono aiutare le aziende a percorrere nuove strade verso aria compressa di qualità sempre migliore, migliorando al contempo la produttività delle apparecchiature nei momenti di picco. Tutto questo si traduce nel consumo energetico e nei costi di affidabilità di un compressore lubrificato a olio monostadio, fornendo al contempo una soluzione oil free. Si proteggono inoltre i processi di produzione farmaceutica da normative più rigorose in termini di efficienza energetica, rispettando al contempo gli standard di qualità dell'aria di Classe 0, il tutto per un costo totale inferiore sull'intero ciclo di vita.
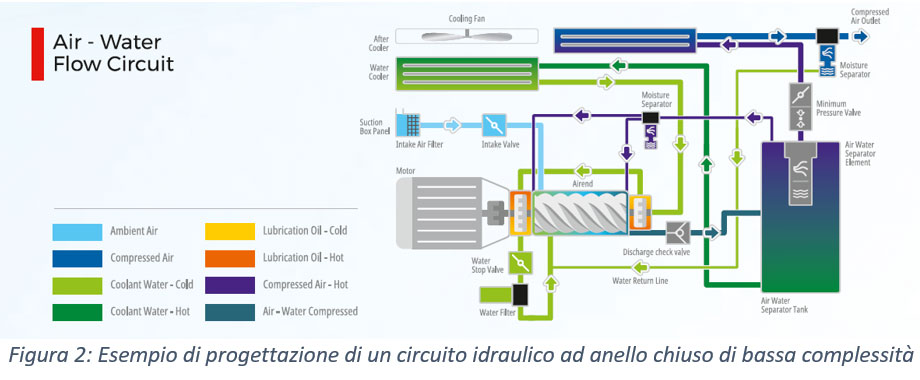
BLOG CORRELATI
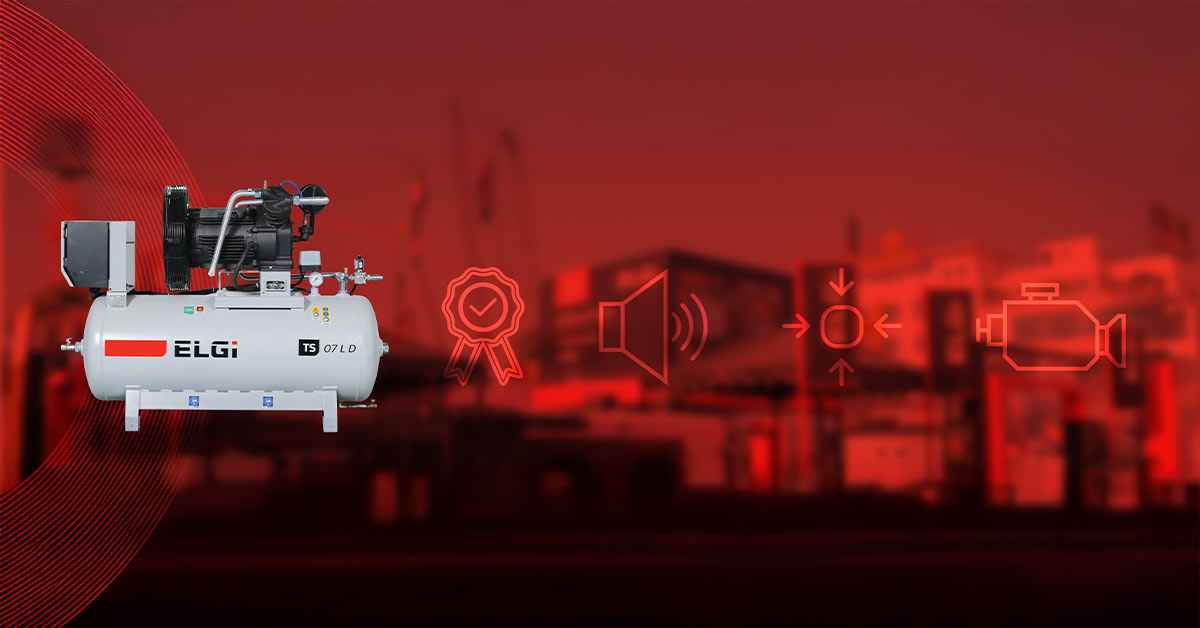
Compressed air is a critical element in many industrial operations, from powering tools to...
Read More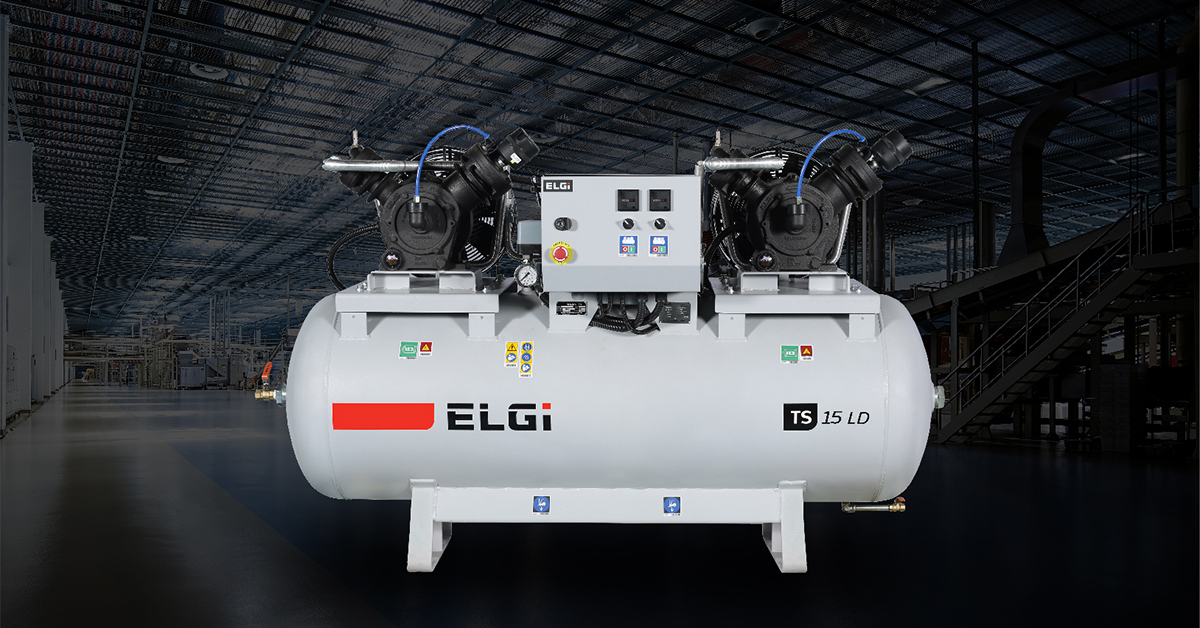
Come funzionano i compressori lubrificati a olio e il loro ruolo nell'efficienza energetic...
Read More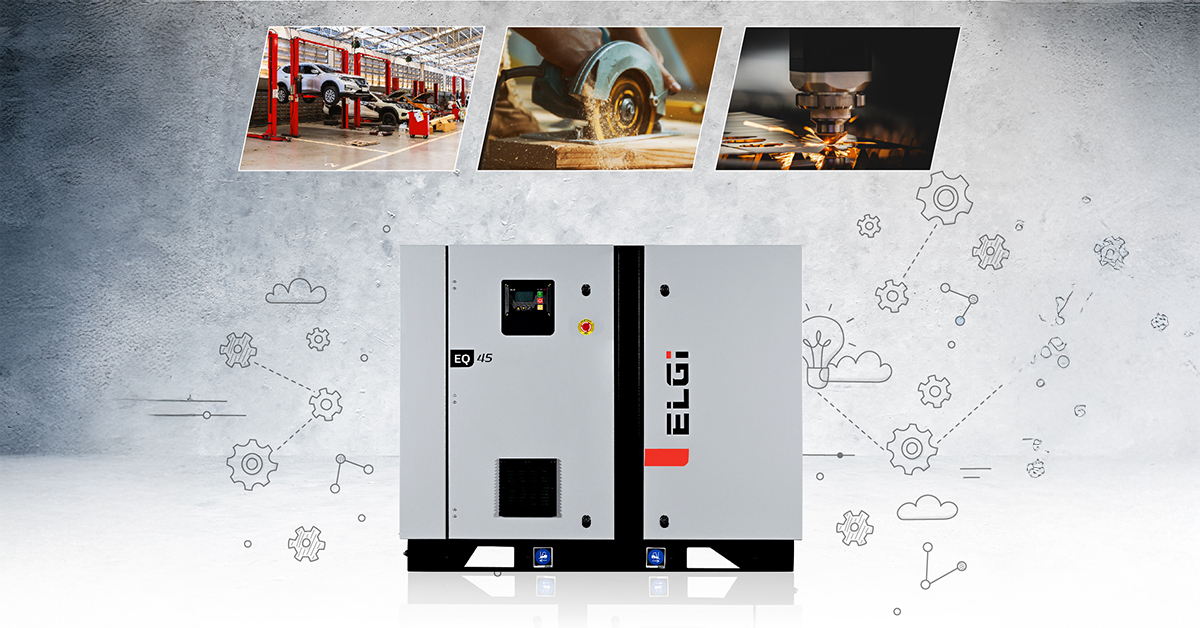
Perché la serie ELGi EN è ideale per soluzioni compatte di aria compressa industriale ...
Read More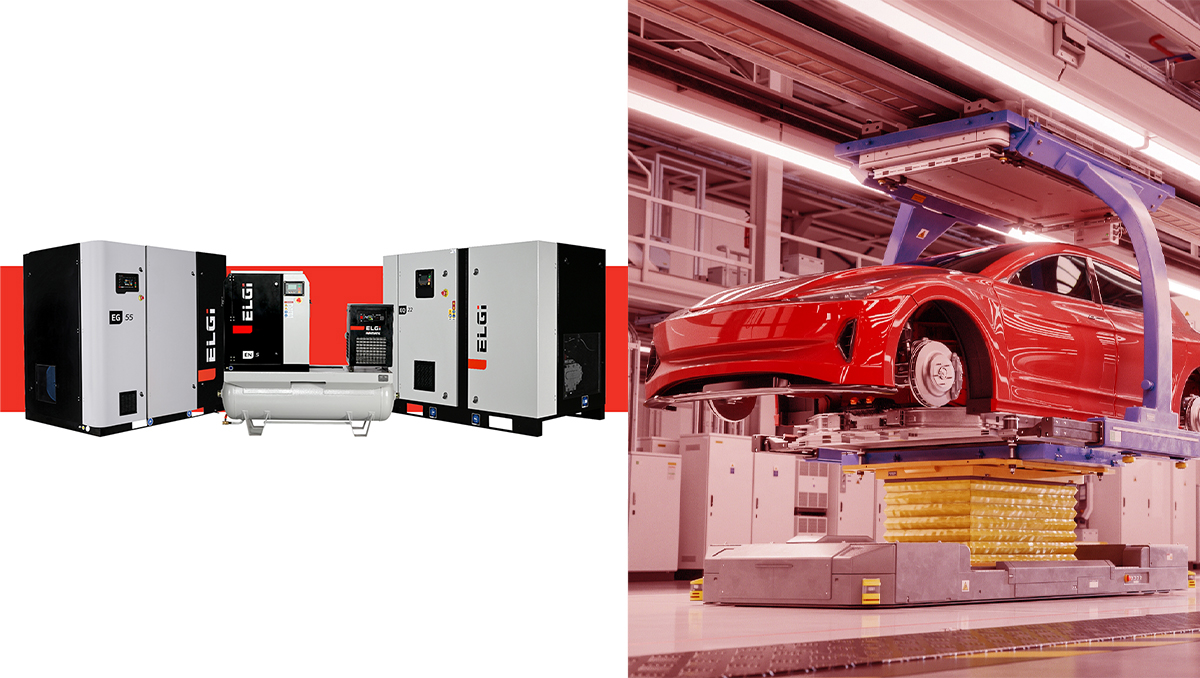
L'aria compressa è una risorsa inestimabile nel settore automobilistico: alimenta di tutt...
Read More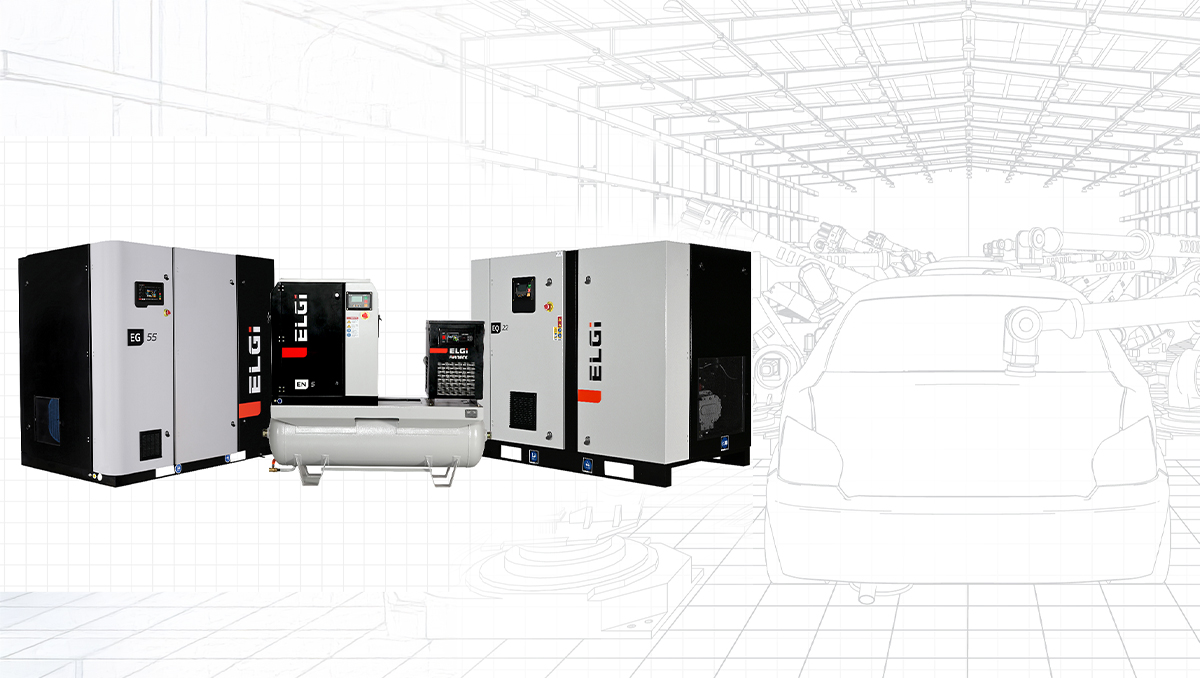
L'industria automobilistica è uno dei settori più dinamici e tecnologicamente orientati ...
Read More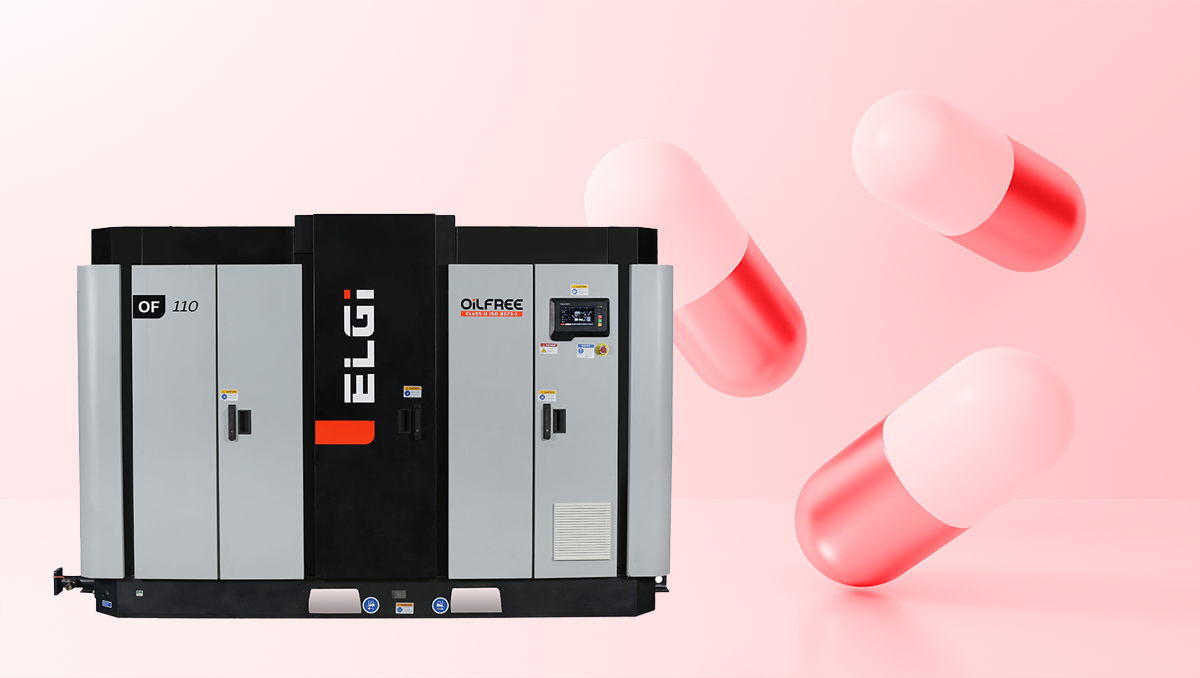
L'industria farmaceutica opera in un ambito in cui precisione, purezza e conformità sono ...
Read More
I compressori d'aria rotativi a vite sono macchine essenziali utilizzate in numerose appli...
Read More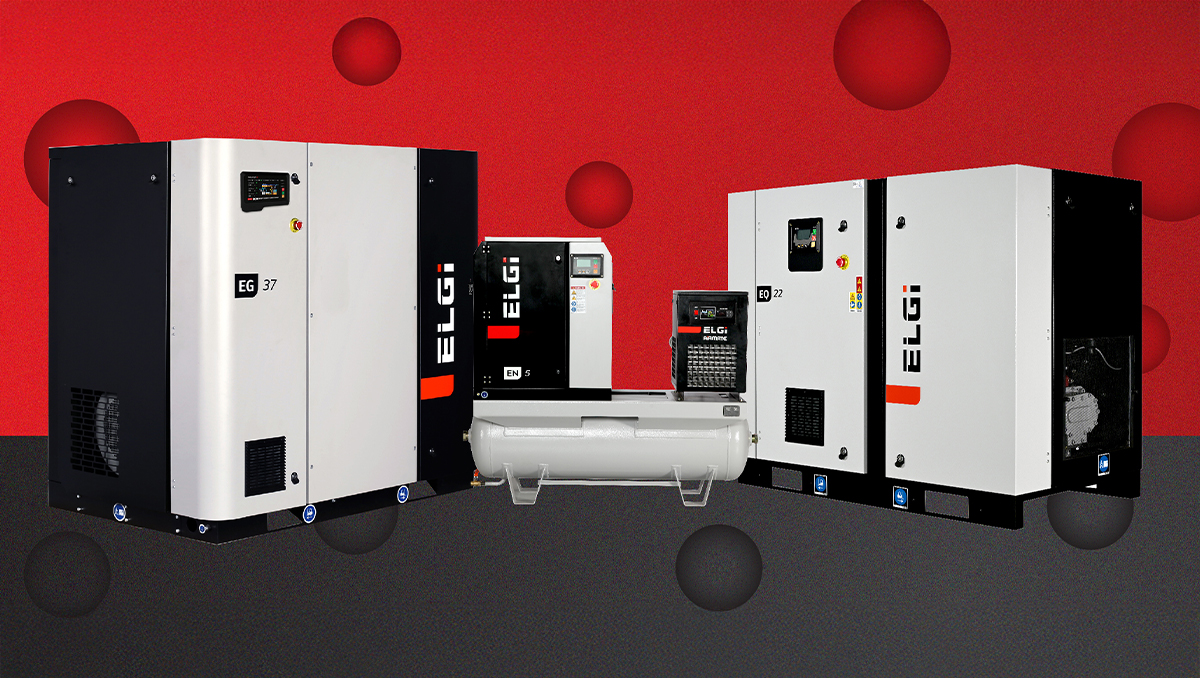
Introduzione Scegliere il giusto compressori rotativi a vite è fondamentale per le v...
Read More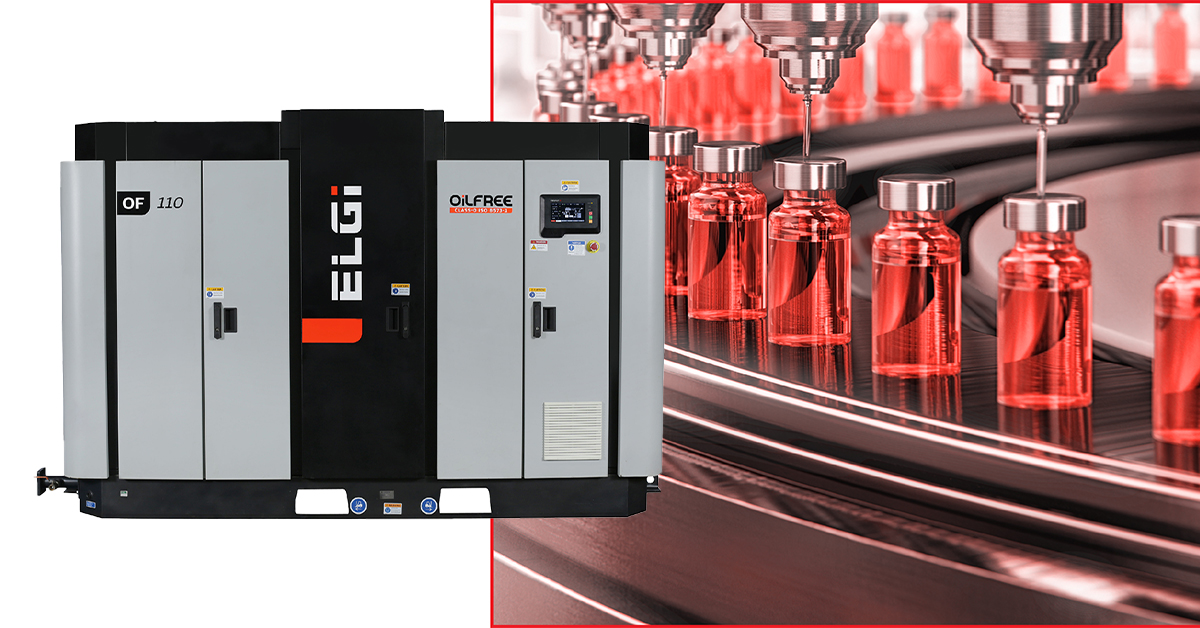
L'industria farmaceutica fa molto affidamento sulla precisione, sulla sterilità e sull'ef...
Read More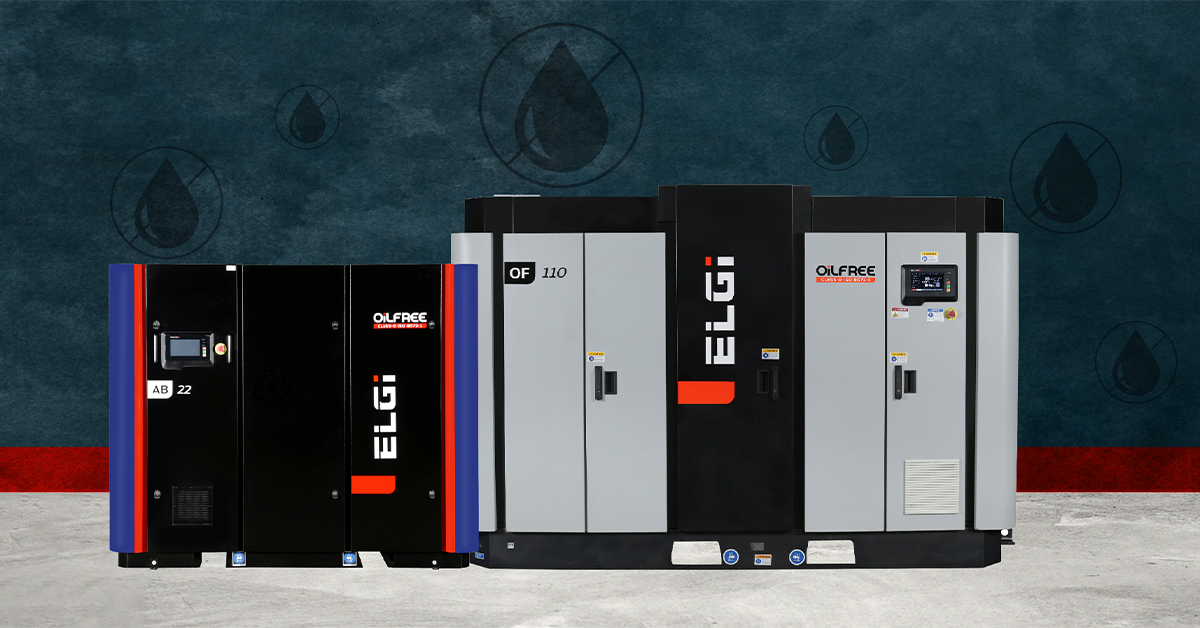
Immagina di gestire una linea di produzione nel settore alimentare e delle bevande, di pro...
Read MoreSii il primo a ricevere aggiornamenti, imparare di più e unirti al nostro mondo esplorativo iscrivendoti al nostro ufficiale giornale dell'aria compressa.
ISCRIVITI