Salvaguardia delle risorse di aria compressa

Andare oltre il compressore, oltre il sistema di aria compressa per un'analisi operativa completa al fine di ottimizzare l'efficienza e salvaguardare le risorse.
L'efficienza energetica è sempre più importante per tutti noi in quanto è direttamente correlata ai costi. Una crescente pressione normativa è all'orizzonte anche sotto forma della proposta di revisione della Commissione Europea sull'efficienza energetica (EED). L'EED rivisto renderà giuridicamente vincolante l'obiettivo di risparmio energetico dell'UE, obbligando i paesi dell'UE a ridurre collettivamente il proprio consumo di energia del 9% rispetto ai livelli del 2020 entro il 2030. Inoltre, i paesi dell'UE dovranno probabilmente ottenere nuovi risparmi annuali dell'1,5% del consumo totale di energia a partire dal 2024, rispetto all'attuale livello dello 0,8%.
Nei processi di produzione che utilizzano aria compressa, i miglioramenti dell'efficienza energetica sono fondamentali poiché i compressori d'aria consumano circa il 12% dell'energia elettrica. Inoltre, nel ciclo di vita di un compressore d'aria, l'80% del costo è costituito dal consumo di energia e il 20% è dal costo dell'unità . Ma gli utenti dei sistemi ad aria compressa hanno un'idea generale della natura di tali costi e di ciò che vi contribuisce?
Guardare oltre il sistema
Vi sono diverse questioni tecniche ed economiche da considerare nell'adozione del giusto approccio per ridurre l'impegno energetico dei sistemi di aria compressa. Non molto tempo fa, l'attenzione del settore guardava giustamente oltre l'efficienza dell'unità ed era rivolta al sistema e all'efficienza del sistema. La maggiore consapevolezza delle esigenze operative e la maggiore pressione per ridurre i consumi energetici e migliorare l'efficienza impongono un esame più approfondito del sistema. Più in dettaglio, come bilanciamo le esigenze operative, i costi capitale, la durata delle risorse critiche e il consumo di energia?
L'approccio tradizionale del costo totale di proprietà (TCO) considera il costo dell'energia in base alla potenza di un pacchetto di compressori o al consumo energetico specifico. Mentre un'analisi operativa completa esamina tutto, dal compressore all'ambiente in cui opera, oltre alle esigenze operative quali i livelli di picco e minimi nella domanda di aria e pianificazione dell'espansione operativa. Un'analisi finita del quadro più ampio, per comprendere come anche gli elementi più piccoli del sistema influiscano sul consumo di energia associato al compressore.
L'obiettivo consiste nel trovare il giusto equilibrio nelle scelte tecniche ed economiche: unità di compressione, capacità , parametri operativi, efficienza energetica, pianificazione di futuri cambiamenti della domanda d'aria e considerazione dei costi energetici legati a perdite, uso improprio dell'aria, domanda artificiale, ecc.
Gli utenti dei sistemi ad aria compressa devono esaminare la propria domanda operativa e vedere quanta aria compressa è necessaria per il funzionamento specifico durante tutto il ciclo di produzione. In seguito, dovrebbero studiare come ottimizzare la sala compressori e ridefinire l'hardware e le impostazioni dell'installazione dei sistemi ad aria compressa. Dopo questo studio, gli utenti dei sistemi ad aria compressa possono davvero salvaguardare le proprie risorse, investimenti e costi energetici e, infine, raggiungere un nuovo TCO basso per l'aria compressa.
In conclusione, diamo uno sguardo più ampio alla salvaguardia dei propri asset
Nel dettaglio, diamo un'occhiata a un ipotetico processo in cui un cliente pensa di espandere il proprio sito produttivo, aggiungere un'altra linea di produzione, aumentare la propria capacità produttiva, ecc. In tal caso, una tipica discussione tra l'utente di sistemi ad aria compressa e il fornitore del compressore d'aria in merito alle nuove richieste di aria compressa inizia con la richiesta del cliente di più aria presupponendo che la soluzione sia un compressore aggiuntivo o più grande. In realtà la semplice aggiunta di un altro compressore non è la risposta quando il sistema circostante rimane lo stesso. Ciò può comportare un eccessivo stress sulla struttura esistente del sistema e può portare a una riduzione dell'efficienza complessiva. Come mai?
Quando viene costruito un impianto o una linea di produzione, viene pianificato e progettato un sistema di aria compressa per adattarsi al carico di un particolare processo di produzione. Tutto funziona come pianificato e raggiunge i risultati pianificati. Quando crescono le attività dell'azienda e l'impianto aumenta la produzione, cambiano le richieste di aria. E l'aggiunta di un altro compressore per soddisfare le crescenti esigenze non è la risposta. Prima ancora di considerarlo, gli utenti dei sistemi ad aria compressa dovrebbero collaborare con gli esperti per condurre un'analisi dettagliata delle prestazioni del sistema attuale in un dato momento e nell'ambito di determinate richieste. Prima di prendere qualsiasi decisione, è necessario eseguire un'analisi olistica dell'intero sistema di produzione, i requisiti storici e pianificati dell'aria, le tubazioni attuali e il controllo delle perdite.
Molto spesso, l'espansione di un sito di produzione o di una linea di produzione non richiede nemmeno l'aggiunta di un altro compressore. La messa a punto delle risorse esistenti in modo che funzionino con carichi adeguati e adattati, non alle pressioni più elevate o ai compiti estremi, può comportare una riduzione della pressione sull'intero sistema e ridurre il consumo di energia. È facile aggiungere un altro compressore, ma adottare un approccio olistico, analizzare e ottimizzare il sistema esistente e i suoi elementi, è la chiave per salvaguardare le tue risorse e ottenere i miglioramenti desiderati in termini di efficienza energetica.
Controlliamo, dimensioniamo correttamente e implementiamo
Prima di prendere una decisione su cosa fare, se sostituire un compressore, aggiungerne un altro o adeguare il sistema esistente, è necessario un audit delle operazioni. Un revisore dell'aria compressa può controllare l'intero sistema e stabilire l'ingresso, lo stato delle unità di compressione e come stanno funzionando e quali pressioni esatte sono richieste. Questo disegnerà un quadro del sistema con i suoi dintorni, elementi, tubazioni e consumi critici. Avendo queste informazioni, possiamo passare al passaggio successivo, che consiste nel prendere una decisione informata su come ottimizzare il sistema per soddisfare i nuovi requisiti. Molto spesso, le nuove esigenze di produzione ampliate possono essere soddisfatte mantenendo la stessa potenza ma regolando il flusso d'aria (ovviamente, a seconda delle dimensioni dell'espansione). Si tratta di dimensionare correttamente il fabbisogno d'aria.
Descriviamolo con un esempio concreto.
Un impianto con una domanda di aria compressa sta espandendo le sue operazioni e richiede un aumento fino al 35% di aria compressa. Il nostro compito consiste nel vedere come è possibile soddisfare questa richiesta aggiuntiva di aria compressa e se è necessario aggiungere un nuovo compressore. L'audit mostra lo stato attuale del sistema, comprese le tubazioni, le pressioni di esercizio durante il giorno e le variazioni cicliche delle richieste. Il passo successivo è vedere come il sistema esistente può essere ottimizzato per generare la domanda aggiuntiva con la stessa potenza. Questo si può ottenere analizzando e dimensionando correttamente il sistema e osservando più da vicino:
Impatto della perdita - La perdita si verifica in tutto il sistema nel tempo. Può essere causata da tubi invecchiati, giunti impropri, installazioni, parti sbagliate o corrosione. Stimiamo che anche dal 20 al 30% del flusso d'aria compressa possa andare perso a causa di perdite. La perdita attraverso un foro da 3 mm (~1/8") può consumare 4 kW/h di elettricità , con una perdita annuale di 19.200 kW (a 7 bar g. (100 psi g.) 16 ore/giorno per 300 giorni all'anno). Ciò consente enormi margini di miglioramento. Le perdite che si verificano nei giunti e nei collegamenti dei tubi possono essere prevenute mediante un semplice e appropriato serraggio e con guarnizioni e mezzi sigillanti adeguati. Raccordi, tubi e collegamenti di qualità adeguati durano più a lungo. Un audit può stabilire le aree di rischio mentre un programma di rilevamento e manutenzione delle perdite a intervalli regolari ridurrà le perdite future.
L'uso improprio dell'aria compressa può riguardare cose semplici e ordinarie quali soffiare su parti lavate o anche operatori che lavorano in un ambiente polveroso e utilizzano l'aria compressa per soffiare via la polvere dai vestiti. Sono cose che capitano. Il controllo e l'eliminazione dell'uso inappropriato dell'aria compressa in tutto l'impianto possono apportare vantaggi significativi.
La domanda artificiale è il volume d'aria in eccesso richiesto da usi non regolamentati in conseguenza della fornitura di una pressione superiore a quella necessaria per le applicazioni. Ciò equivale a un consumo di energia non necessario. Una semplice strategia che esegua un'adeguata selezione e installazione e preveda l'uso corretto di regolatori di pressione oltre a prevenire perdite e un uso inappropriato può essere di grande aiuto in questo caso.
L'Ottimizzazione della fascia di pressione - L'impostazione delle pressioni corrette può essere effettuata stabilendo e comprendendo i requisiti, rilevando le perdite di pressione nel sistema di tubazioni tra il compressore e le apparecchiature di produzione, impostando correttamente la pressione di carico e scarico al livello più basso possibile ma comunque tale da soddisfare le esigenze dell'applicazione. Il risparmio derivante dalla riduzione di 1 bar (14,7 psi) della pressione impostata del compressore è addirittura del 7% del consumo energetico totale del compressore. Ogni anno, con 16 ore al giorno di funzionamento per 300 giorni all'anno, un risparmio del 7% in caso di consumo di potenza del compressore da 110 KW è pari a 36.960 kWh!
Ridurre al minimo la perdita di pressione - Sebbene nessun sistema possa essere privo di una perdita di pressione nel sistema di tubazioni e nelle apparecchiature a valle, la differenza di pressione tra il punto di scarico del compressore e il punto di consumo può essere ridotta al minimo e mantenuta il più bassa possibile. Si inizia con la progettazione delle tubazioni, avvicinando i punti di produzione e di applicazione l'uno all'altro e ottimizzando le dimensioni e la forma delle tubazioni. Le apparecchiature a valle devono essere selezionate alla caduta di pressione più bassa, mantenute secondo le raccomandazioni del fornitore del compressore d'aria e pulite periodicamente. Tutto questo tenendo presente che la perdita di 1 bar di pressione comporterà il 7% del consumo energetico totale di un compressore.
Un audit eseguito correttamente con il partner giusto mostrerà un modello di consumo completo di aria compressa nel tempo, aiutando con il rilevamento delle perdite, il dimensionamento del compressore e l'ottimizzazione dell'energia, utilizzando infine i dati per prendere la decisione giusta sulle operazioni in corso, futura espansione del sistema.
Che si tratti di utenti di sistemi ad aria compressa, fornitori di compressori d'aria, team di assistenza oppure operatori, tutti possiamo migliorare l'efficienza energetica, l'efficienza del sistema e i costi guardando oltre l'efficienza del sistema per ottimizzare la domanda e la fornitura di aria compressa. Il vantaggio aggiuntivo di questo approccio si ripaga salvaguardando le risorse, riducendo il rischio di tempi di inattività e mantenendo le operazioni efficienti.
BLOG CORRELATI
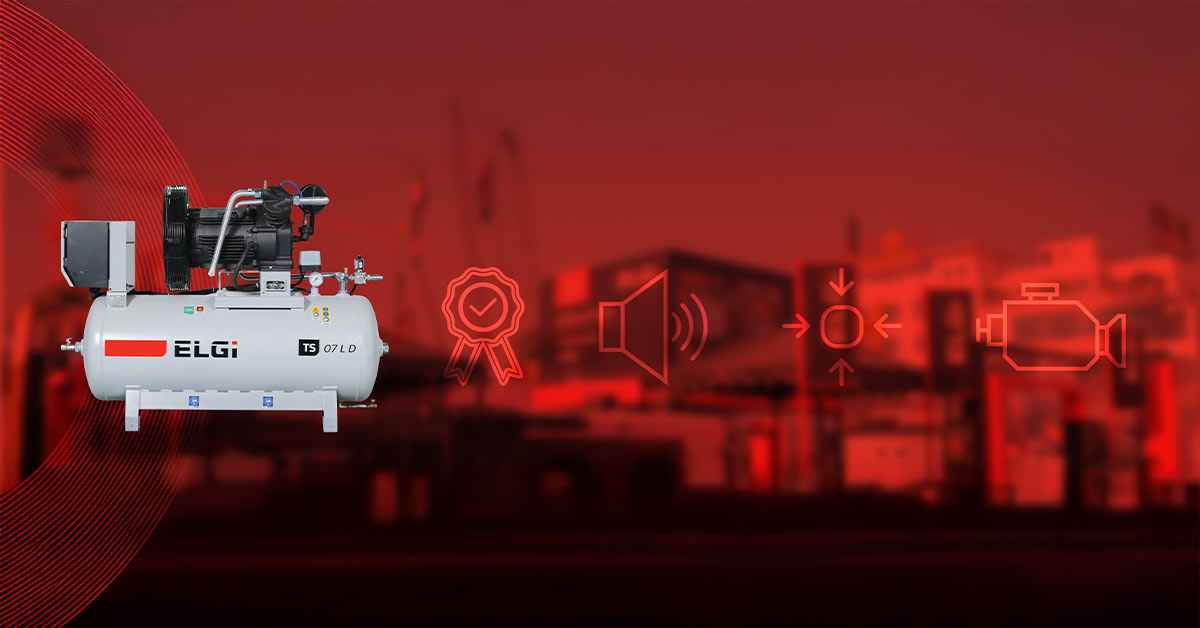
Compressed air is a critical element in many industrial operations, from powering tools to...
Read More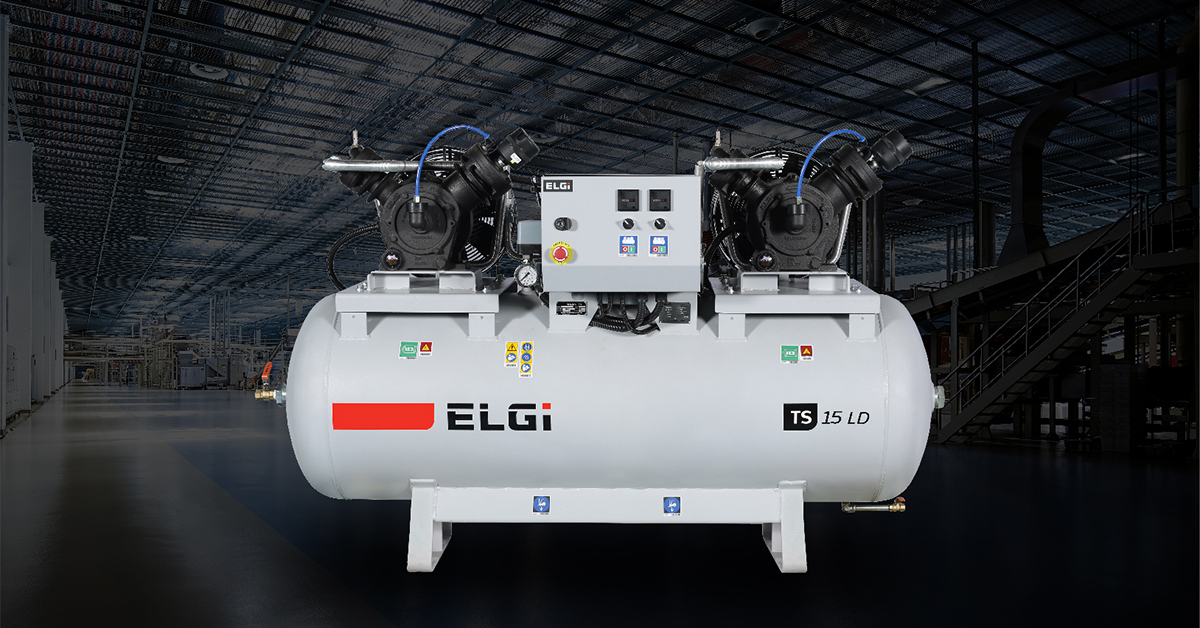
Come funzionano i compressori lubrificati a olio e il loro ruolo nell'efficienza energetic...
Read More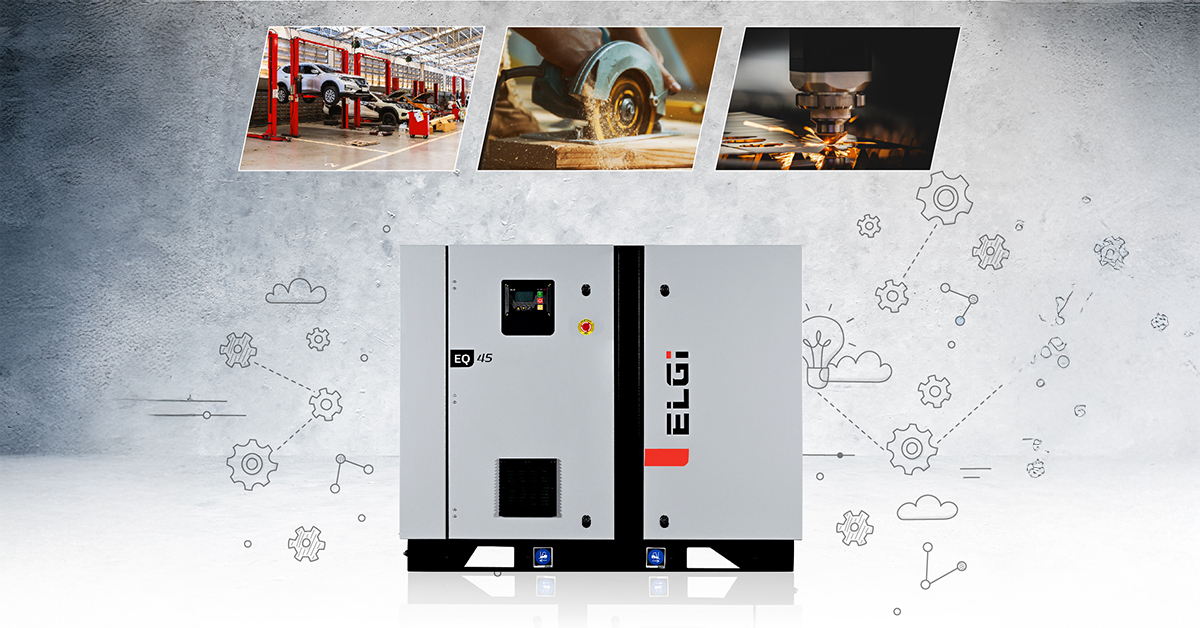
Perché la serie ELGi EN è ideale per soluzioni compatte di aria compressa industriale ...
Read More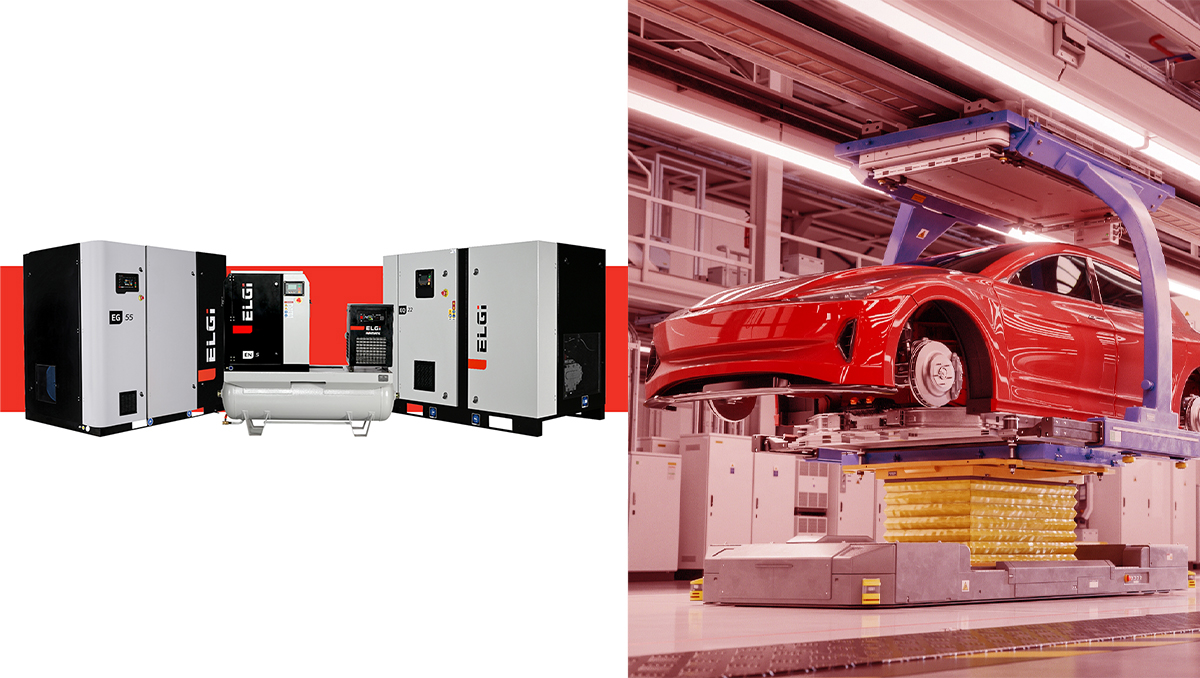
L'aria compressa è una risorsa inestimabile nel settore automobilistico: alimenta di tutt...
Read More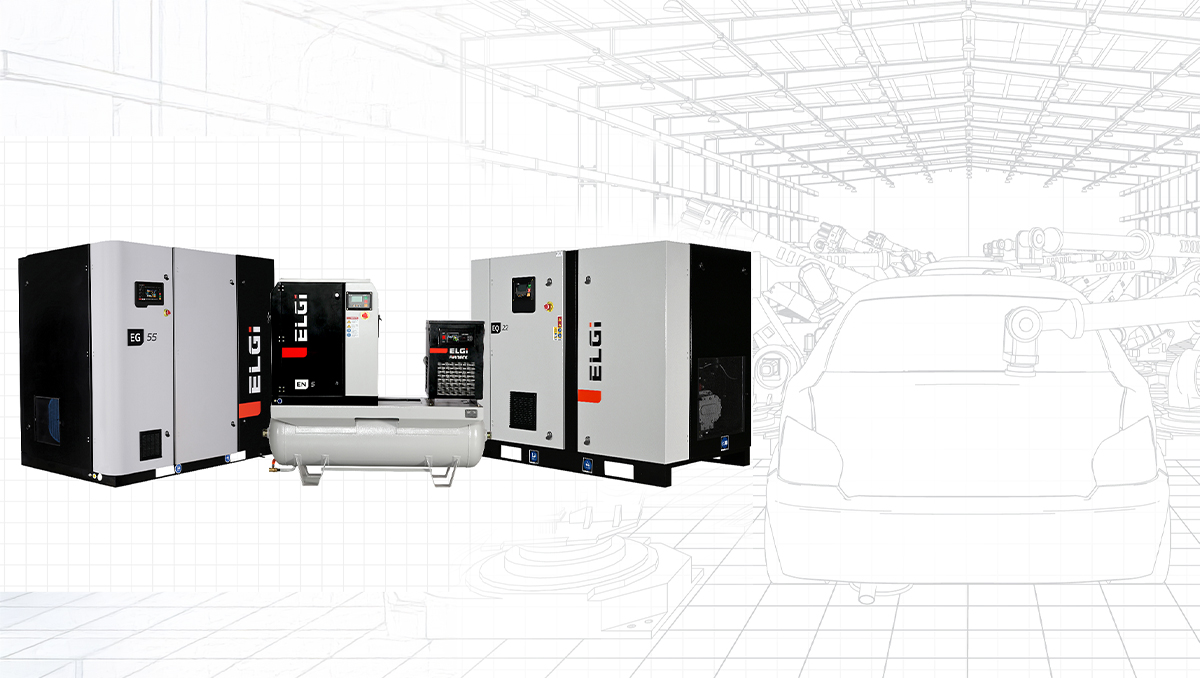
L'industria automobilistica è uno dei settori più dinamici e tecnologicamente orientati ...
Read More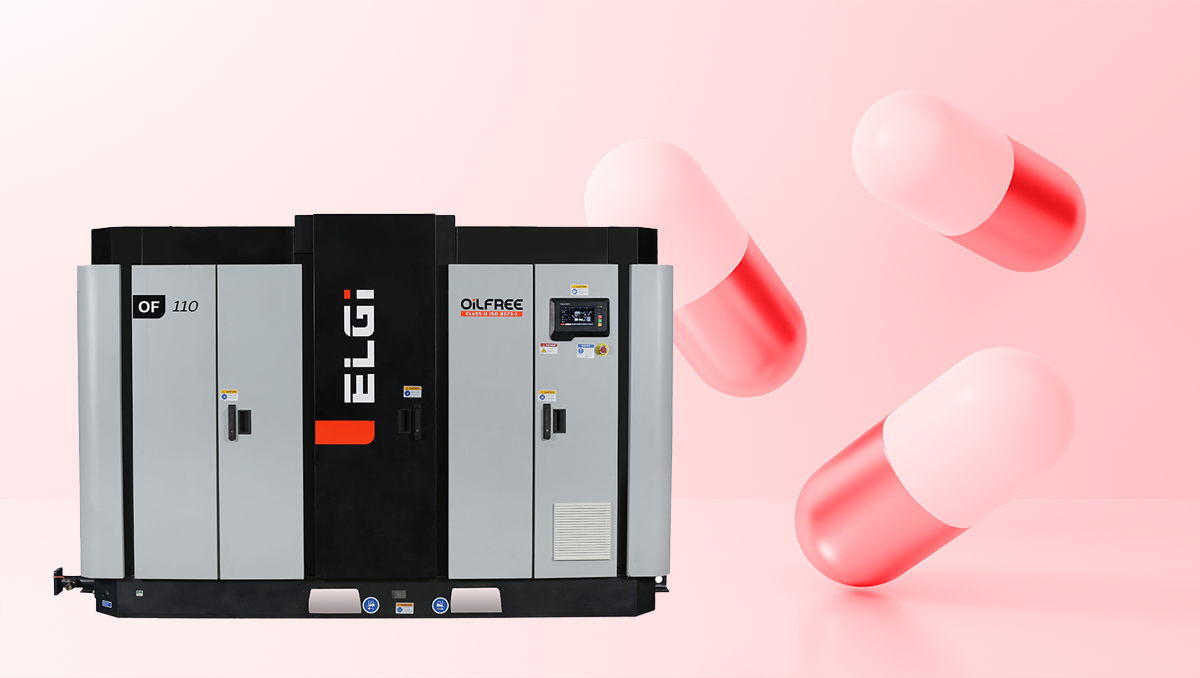
L'industria farmaceutica opera in un ambito in cui precisione, purezza e conformità sono ...
Read More
I compressori d'aria rotativi a vite sono macchine essenziali utilizzate in numerose appli...
Read More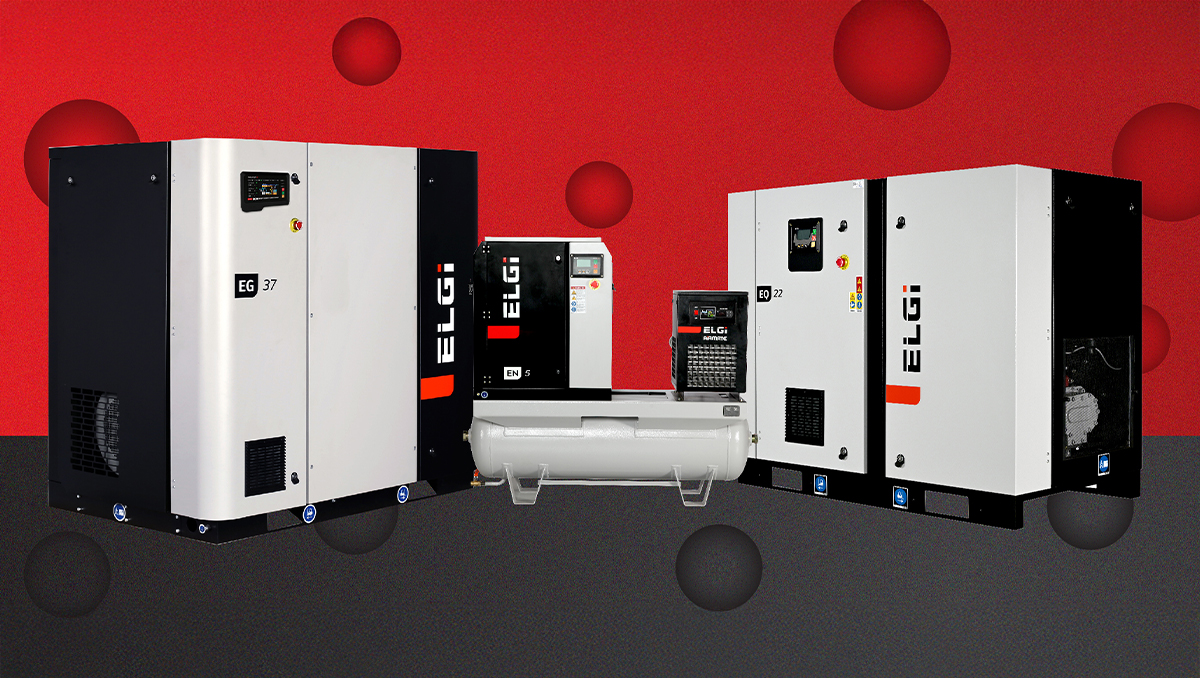
Introduzione Scegliere il giusto compressori rotativi a vite è fondamentale per le v...
Read More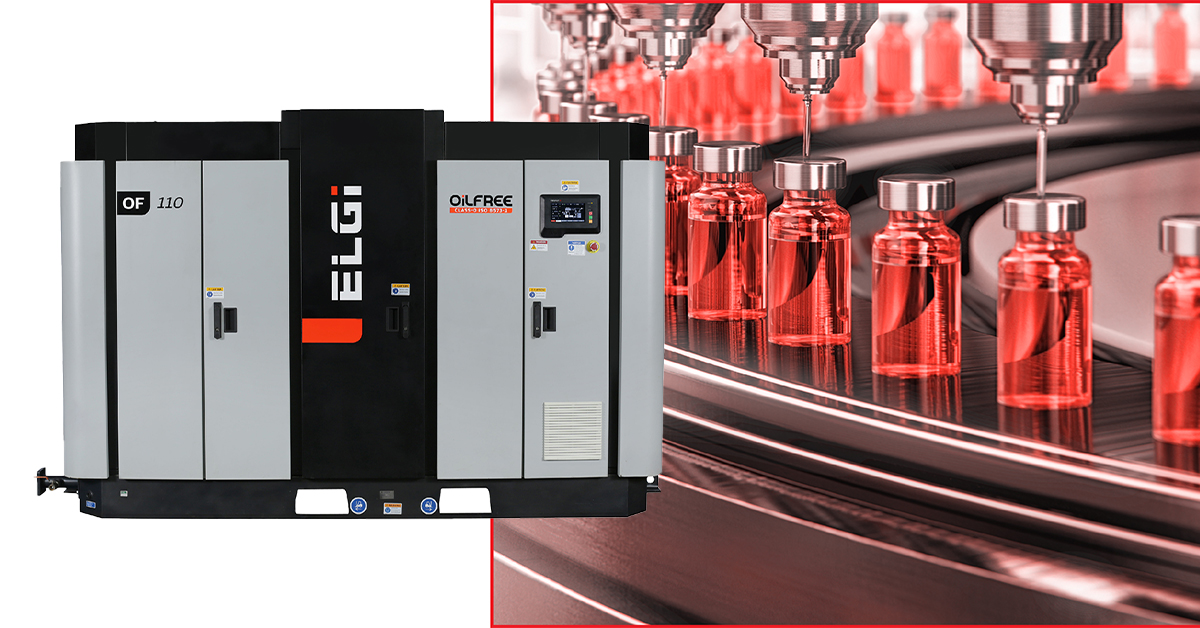
L'industria farmaceutica fa molto affidamento sulla precisione, sulla sterilità e sull'ef...
Read More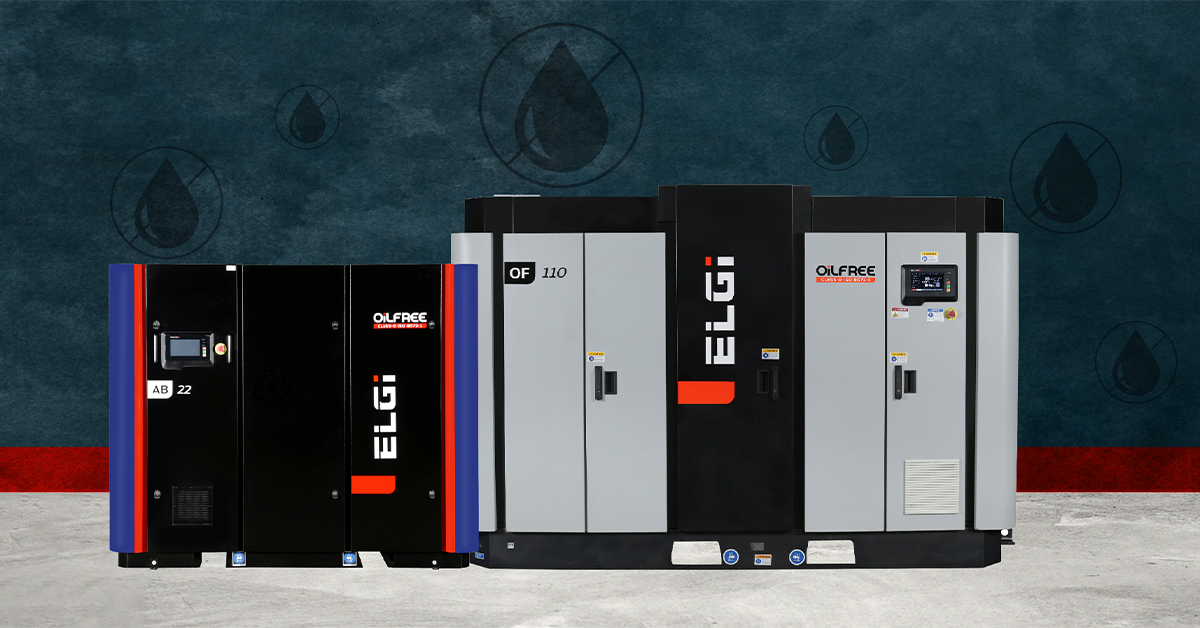
Immagina di gestire una linea di produzione nel settore alimentare e delle bevande, di pro...
Read MoreSii il primo a ricevere aggiornamenti, imparare di più e unirti al nostro mondo esplorativo iscrivendoti al nostro ufficiale giornale dell'aria compressa.
ISCRIVITI