Advancing Precision Milling for Enhanced Composite Tooling Solutions

One of Europe's leading composite tooling solutions providers raises the bar on precision milling of composites with ELGi EG Series air compressors, establishing new standards of excellence in production.
Denmark-based Dencam Composite elevates its automatic milling machines to new heights of productivity and precision by harnessing the power of ELGi's EG Series high-performance compressors with VFD (Variable Frequency Drive), boosting the efficiency of its composite tooling solutions in three production locations in Denmark.
Revolutionizing Manufacturing
Composite tools are produced using methods similar to tools used in manufacturing composites, including vacuum bagging and injection moulding. These tools are crucial in manufacturing high-quality composite parts that find applications across various industries. The Global Composite Tooling Market is projected to reach a substantial value of US$ 705.3 million by 2027, experiencing a steady compound annual growth rate (CAGR) of 5.5% from 2022 to 2027.
The market for lightweight and precise composites is driven by increasing demand from the renewable energy, aerospace, and defense sectors. The global aviation industry accounts for around 80% of the demand for lightweight composite materials. Additionally, the automotive industry has adopted composite tooling to reduce vehicle weight and improve fuel efficiency, contributing to further demand. Within Europe, Germany is forecasted to grow at approximately 3.2% CAGR. Europe's North Sea region is also emerging as a renewable energy hub, attracting industry and infrastructure development. With abundant wind potential, this area is promoting the installation of advanced wind turbines, further propelling the growth of wind turbine equipment manufacturers. The growing interest in composite tooling from these sectors is expected to impact the market positively.
Empowering Industries with Precision and Reliability
Dencam Composite is a leading provider of reliable and cutting-edge composite solutions, earning a well-deserved reputation as a prominent player in the composite industry. Their advanced technology, extensive knowledge, and impressive production capacity make them a go-to choice for various industries. The company's expertise lies in leveraging state-of-the-art technology to manufacture a diverse range of composite products, catering to sectors like wind energy, marine, and automobile. Backed by a team of industry experts with rich experience, Dencam Composite delivers top-quality products that meet even the most stringent specifications.
One of their standout strengths is their utilization of high-precision 5-axis milling machines. This cutting-edge technology allows them to create various shapes in different sizes, achieving remarkably tight tolerances as low as 0.1 mm. The company offers unlimited production possibilities by combining advanced milling capabilities with in-depth composites expertise. From intricate components to large-scale projects like wind turbine blades, Dencam Composite excels at meeting diverse project requirements.
Dencam Composites' primary focus is on providing uncompromising quality, a commitment that is championed by their team of skilled employees. Their quest for perfection is bolstered by an ISO 9001 certification, which serves as the cornerstone for their quality efforts. However, they transcend the conventional by consistently pushing boundaries to uncover and rectify quality intricacies across their supply chain. Dencam Composite's capabilities are underscored by an arsenal of cutting-edge tools that synergize to orchestrate unparalleled accuracy for all its products. Whether their products are for custom components, specialized parts, or complex structures, their meticulous selection of materials and suppliers and the use of modern milling machines backed by their composite knowledge ensure they are vested in delivering only the best.
The Role of Compressed Air in Composite Tooling
Compressed air is a versatile and critical utility in composite tooling that helps increase the productivity, quality, and consistency of composite material manufacturing processes. Compressed air serves as a driving force behind numerous automated processes within composite manufacturing facilities. Precision and consistency are paramount in composite manufacturing to ensure the integrity and reliability of finished products. Compressed air from EG Series air compressor plays a pivotal role in maintaining these standards by ELGi air compressor facilitating precise control over various production variables.
Here are some examples of compressed air in composite tooling:
- Release agent application: Compressed air is used to apply a release agent onto the surface of composite moulds or tools. The release agent keeps the composite material from clinging to the mould, making it easier to remove the finished object without damaging it.
- Cleaning and drying: The composite moulds are cleaned and dried using compressed air before the layup process. This ensures no impurities or moisture interfere with the composite components' adhesion during fabrication.
- Powering the milling process: Compressed air is used to power automatic milling machines. The milling machine's pneumatic system is powered by compressed air, allowing it to execute cutting operations on the composite material.
- Part demoulding: After curing, compressed air is utilized to aid the release and ejecting of the final composite component from the mould. This prevents the part from being damaged during the demoulding process.
- Automation and precision: Using compressed air with automatic milling machines allows precise and automated material removal. The milling process can be automated to produce correct forms and dimensions consistently, decreasing human error and enhancing total manufacturing consistency.
Dencam Composite has years of experience creating and producing composite tooling solutions across the wind, marine, and automobile industries.When selecting a compressed air partner, their key considerations were enhancing existing manufacturing processes and identifying a reliable, energy-efficient compressed air solution to power their high-precision 5-axis milling machines.
The ELGi Advantage
ELGi and ALT Trykluft collaborated to conduct an air audit, identifying energy-saving opportunities by simulating the efficiency of three ELGi EG Series variable speed oil-lubricated screw air compressor units. ELGi's inherent comprehension of Dencam's energy needs helped optimize its energy usage and overall operational efficiency.
With the ELGi EG Series compressors, Dencam Composite gained the following business benefits:
- Reliable and Stable Air Supply: ELGi compressors provided Dencam Composite with a stable and reliable compressed air source, essential for their automated milling machines and other production processes. This ensured uninterrupted operations, reduced downtime, and increased overall efficiency.
- Cost Savings and Energy Efficiency: ELGi compressors are renowned for their energy-saving features and efficiency. Using ELGi compressors, Dencam Composite experienced reduced energy consumption, leading to cost savings in their manufacturing processes.
- High Quality and Performance: ELGi compressors are known for their quality and performance. By using ELGi compressors, Dencam Composite was able to maintain the high-end quality standards required for their composite tooling products, including those with small tolerances.
- Warranty and Service Support: ELGi compressors come with a great warranty, providing Dencam Composite with peace of mind and assurance of product reliability. Additionally, the professional service offered by ALT Trykluft, the ELGi Channel Partner, ensured prompt assistance and support whenever needed.
- Improved Productivity: With the reliable and uninterrupted supply of compressed air from ELGi air compressors, Dencam Composite experienced improved productivity in their manufacturing processes. The consistent performance of the compressors minimiszed downtime and allowed for smooth and efficient operation of equipment and machinery.
Potential Energy Savings:
- Incorporating ELGi compresed air systems into Dencam’s operations has proven to be a strategic move with substantial benefits for Dencam. One of the key advantages lies in the in-built ELGi Variable Frequency Drive (VFD), which intelligently matches compressor output with demand by dynamically adjusting the motor speed. This translates into significant energy savings, aligning perfectly with Dencam’s commitment to sustainability and cost-efficiency, resulting in an impressive 34% reduction in energy costs compared to traditional compressors without VFD.
Embracing Innovation and Efficiency
Dencam Composite has successfully harnessed the power of ELGi compressors to optimize their manufacturing processes and elevate their production capabilities. A spokesperson from Dencam Composite remarked, "We are delighted to share our experience with ELGi compressors and the remarkable partnership with ALT Trykluft. As a leading manufacturer of composite tooling for the wind, marine, and automobile industries, the quality of our production processes is paramount to our success. One of the most critical aspects for us is the quality of our products. ELGi compressors have proven to be top-notch in terms of performance and durability, enabling us to maintain the highest standards for our composite tooling. Consistent and precise outputs with small tolerances are crucial for the success of our projects.
The collaborative air audit conducted by ELGi and ALT Trykluft was a revelation. Identifying energy-saving opportunities within our compressed air system, we were able to optimize our energy consumption, which directly impacted our wind turbine production. The reliable compressed air solutions provided by ELGi compressors have been vital in ensuring the integrity and longevity of our products in this critical sector."
Tord Sandberg, Regional Manager, ELGi Nordics, said, "At ELGi, we understand the importance of energy efficiency for our customers. The in-built ELGi VFD (Variable Frequency Drive) matches compressor output with demand by varying the motor speed, which reduces the power consumption in line with the demand reduction. Compared to a compressor without a VFD, an EG Series with variable speed over a ten-year operating period can have a 34 percent reduction in energy costs."
Dencam Composite selected three ELGi EG Series compressors (EG55V, EG22V, and an EG15V) to support precision milling of composites, plugs, moulds and models across three production locations in Denmark. With the installation of ELGi compressors, Dencam Composite successfully established a stable and dependable air supply for their automated milling machines and various production processes. Incorporation of these advanced compressors resulted in a host of benefits, including increased operational efficiency, minimized downtime, and consistently high-quality outputs with precision tolerances. One of the standout advantages of ELGi compressors was their energy-saving features, which contributed to significant cost savings for Dencam Composite. This alignment with Dencam's commitment to innovation and top-notch production further solidified the value of choosing ELGi compressors for their manufacturing needs.
The successful integration of ELGi compressors into Dencam Composite's manufacturing operations underscores the value of choosing reliable and technologically advanced compressed air equipment to meet the demands of modern production processes in Europe. The partnership between Dencam Composite and ELGi reflects a shared commitment to excellence, innovation, and continuous improvement in manufacturing practices.
For further insights into ELGi's range of compressed air systems and authorized service options, we invite you to reach out to ELGi directly or download our comprehensive brochures. Discover how ELGi can elevate your manufacturing capabilities and drive sustainable growth in your operations.
In collaboration with ALT Trykluft, the ELGi Channel Partner, Dencam Composite, found a reliable partner that provided not only exceptional service but also conducted air audits to identify energy-saving opportunities. The entire experience underscored the importance of reliable compressed air solutions, particularly for critical applications like wind turbine production. By making strategic choices in their compressed air supply systems and partnering with ALT Trykluft and ELGi, Dencam Composite demonstrated their dedication to maintaining the highest efficiency, reliability, and quality standards in their manufacturing processes.
RELATED BLOGS
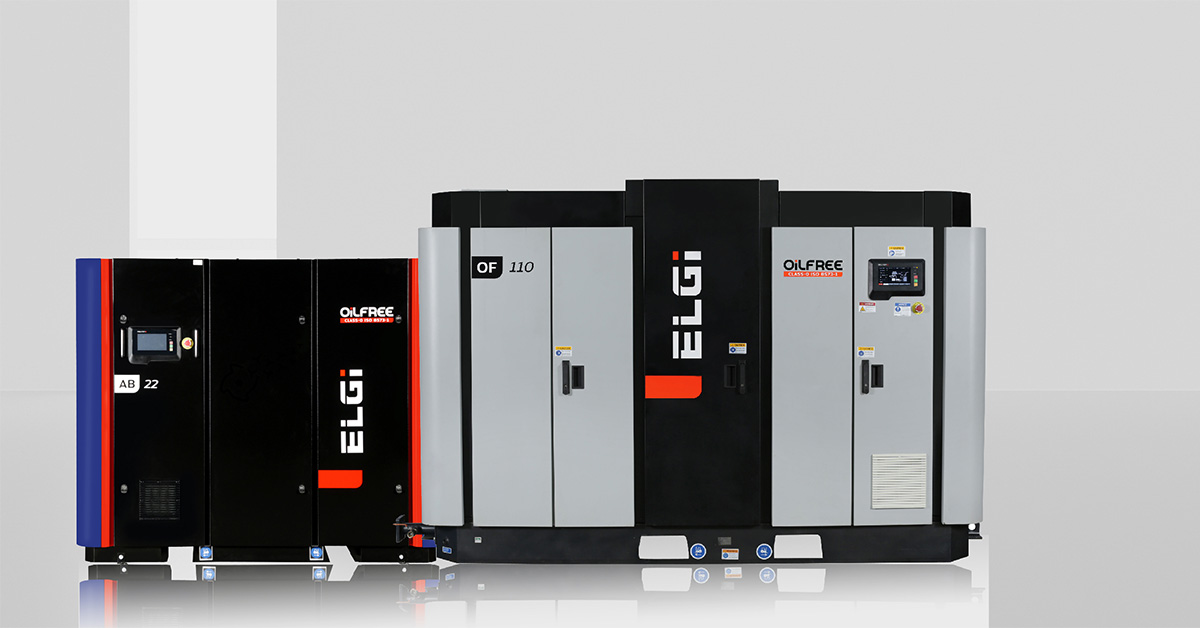
Clean compressed air is vital to the operations of various industries. Oil-free compressor...
Read More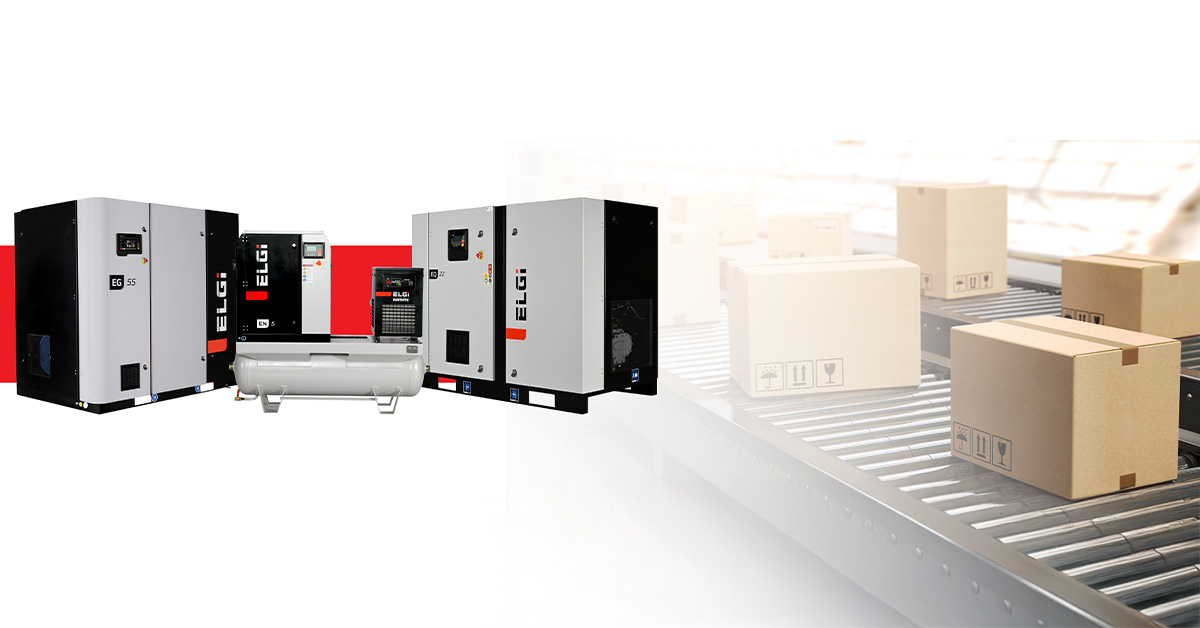
The packaging industry plays a vital role in the global economy, helping to protect and de...
Read More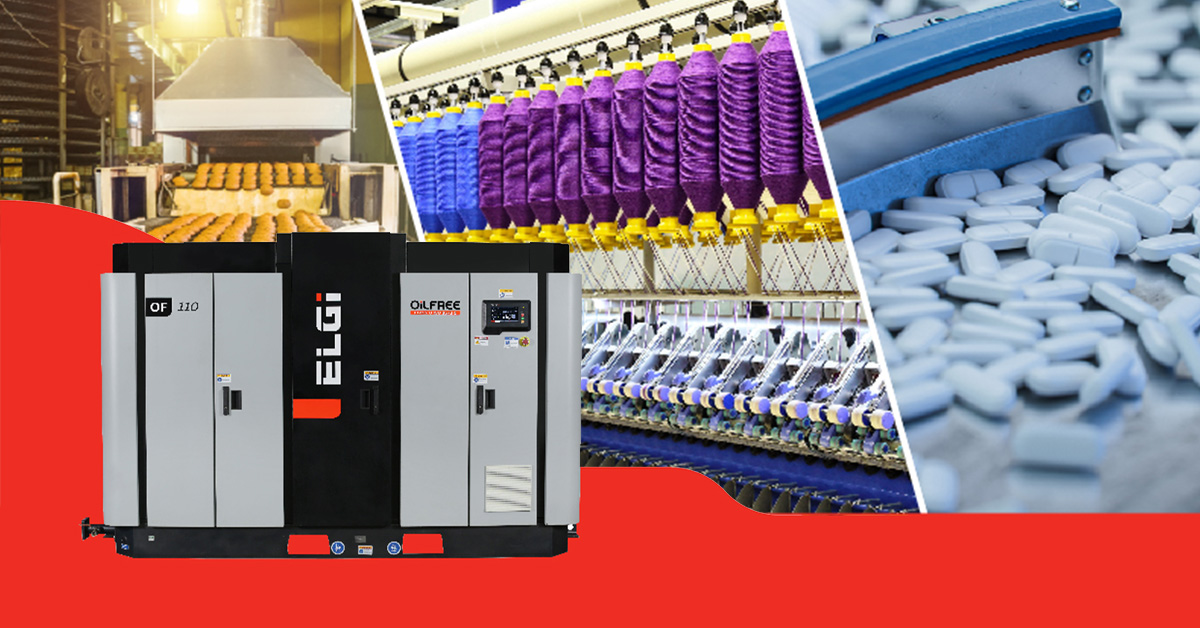
Have you ever wondered how air compressors achieve the highest levels of compressed air pu...
Read More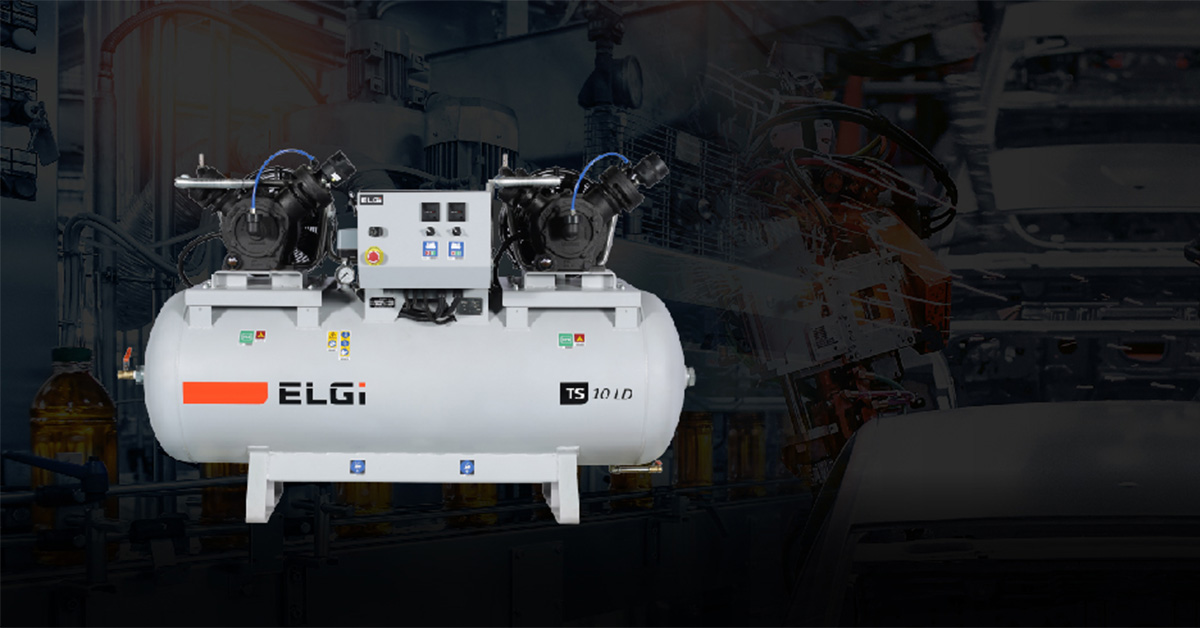
In the industrial sector, selecting the right air compressor is crucial for maintaining pr...
Read More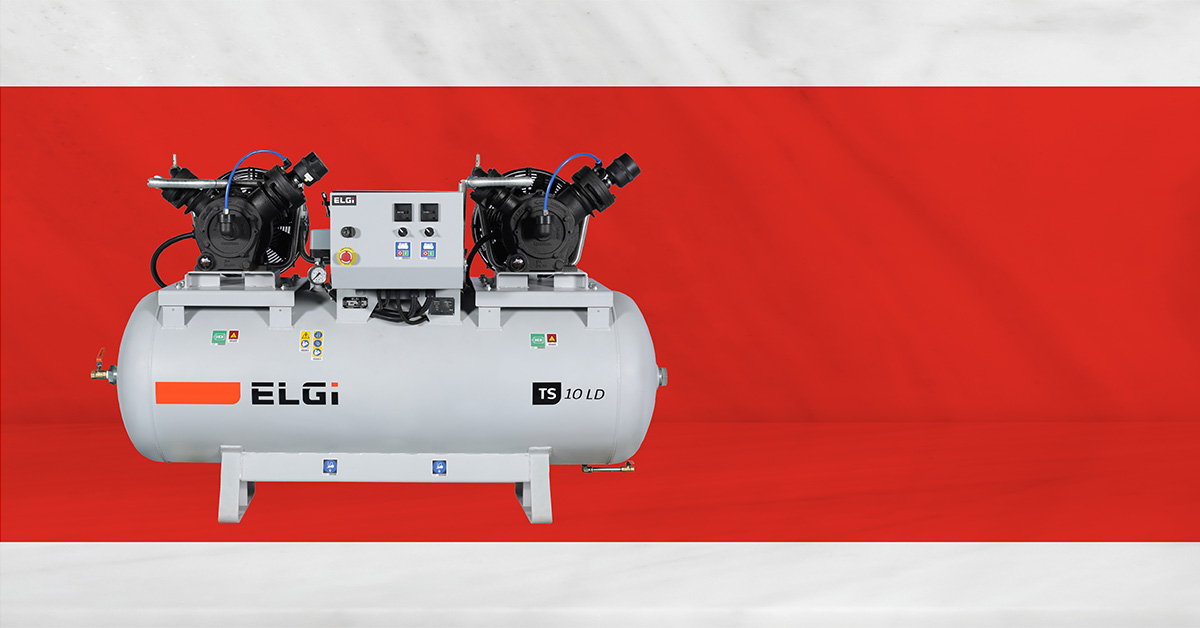
Selecting the right air compressor for your business is a crucial decision that can signif...
Read More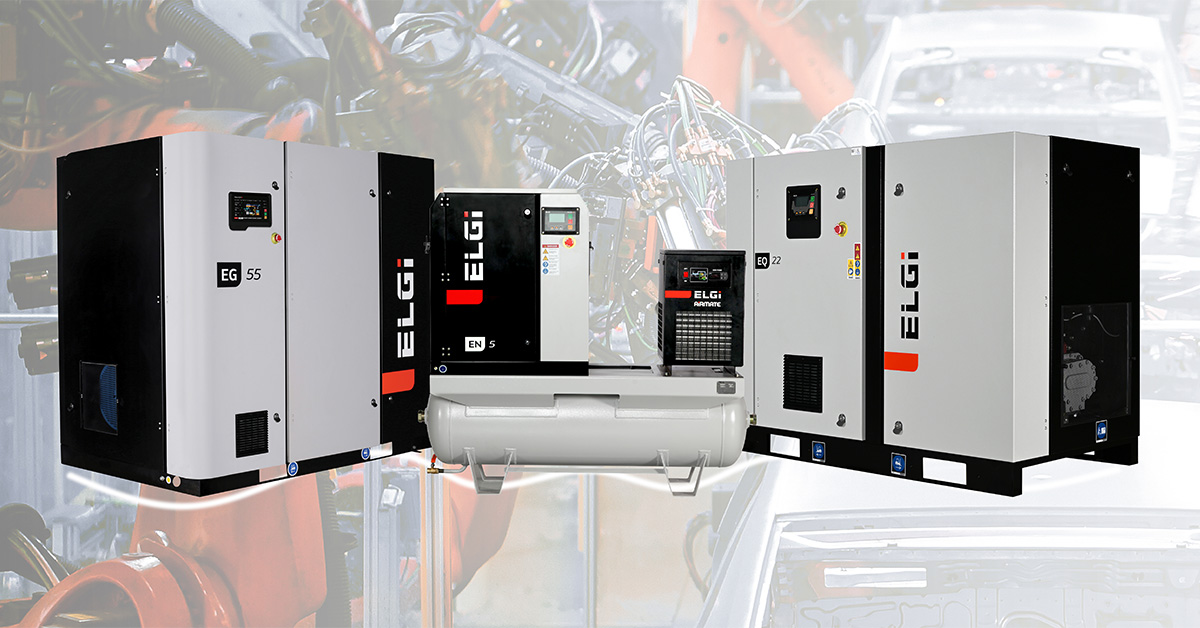
Adopting electric oil-lubricated rotary screw air compressors can significantly enhance th...
Read More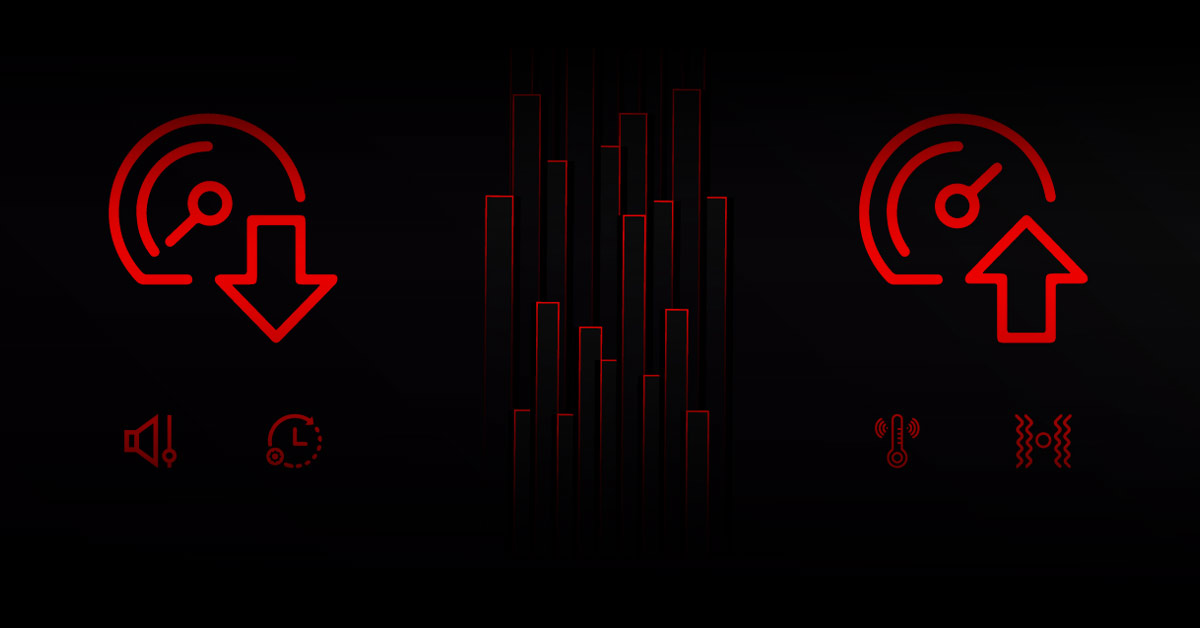
The speed at which a screw air compressor rotates is a critical factor that significantly ...
Read More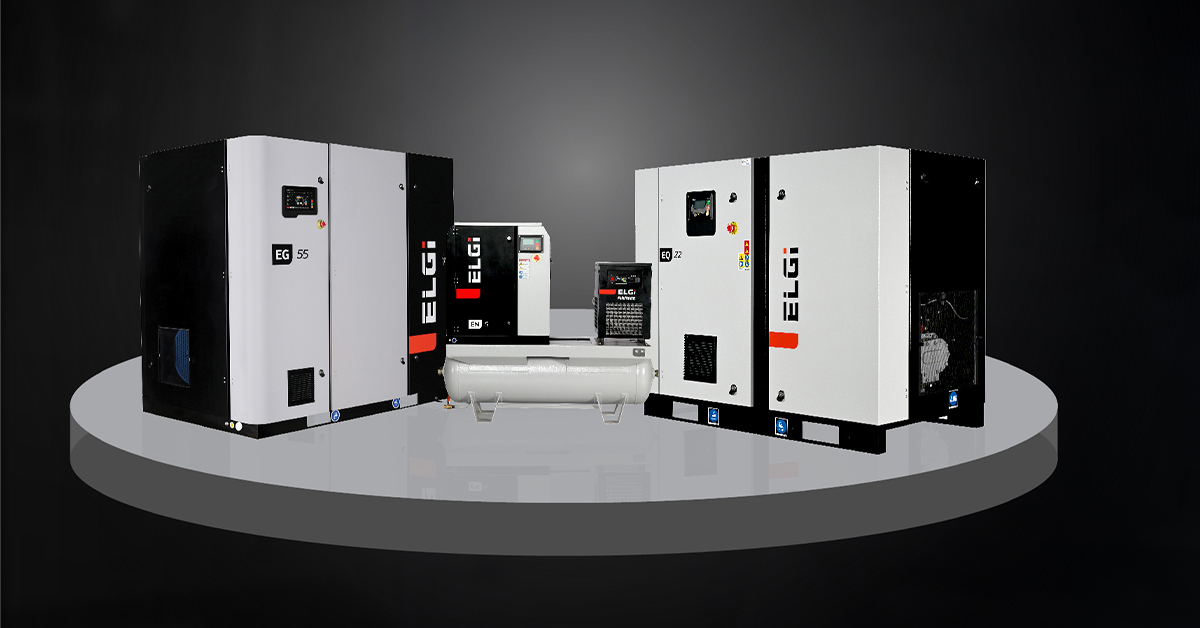
In the metal fabrication industry, the right air compressor can make all the difference. F...
Read More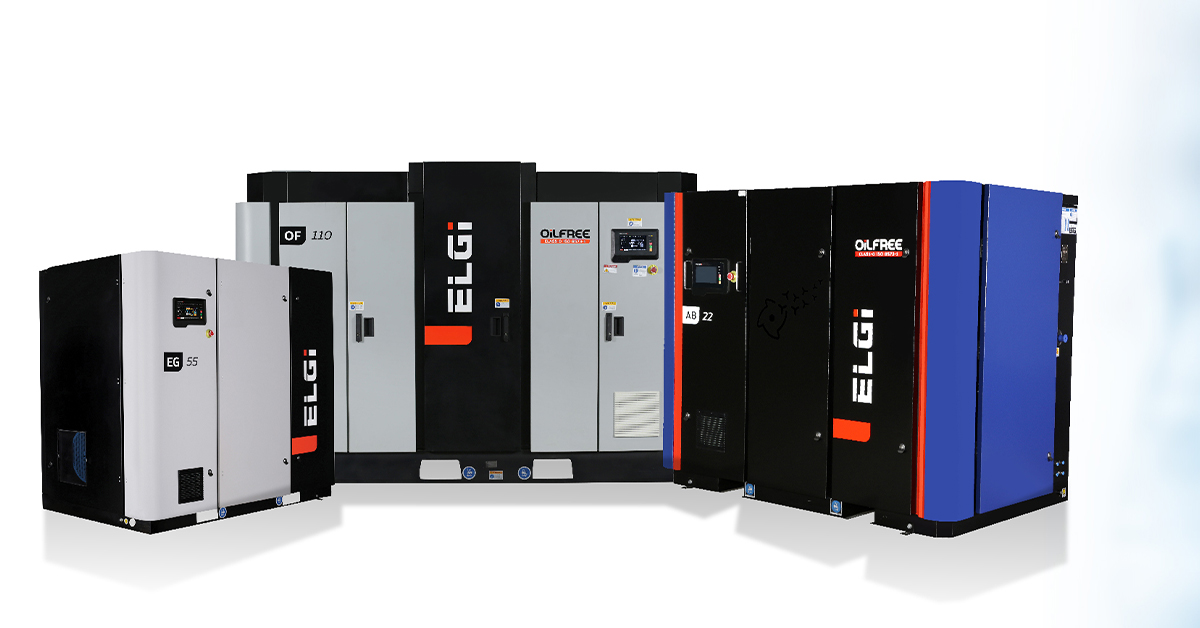
Air compressors are the unsung heroes of the chemical manufacturing industry. They power v...
Read More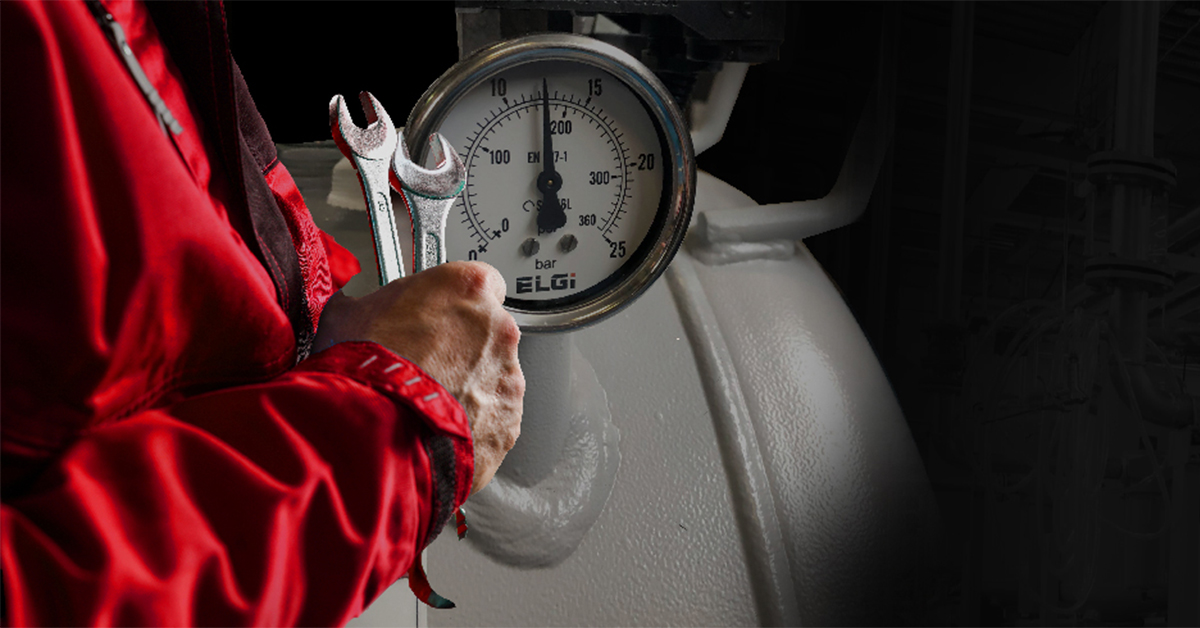
At the core of various industrial activities stands the industrial air compressor, an indi...
Read More