ELGi COMPRESSED AIR AUDIT REPORT
Our Audit Report includes recommendations on short, medium, and long-term measures for energy conservation, along with financial estimates and analysis for their implementation. These recommendations come to you with databases and factsheets generated by measurements and tests conducted in your plant as well as on the field. We also track the implementation and performance monitoring of our energy conservation proposals. This is done by our expert engineers who also train the operators from the user end.
With increasing energy costs, the performance and efficiency of your compressed air systems have never been more critical. Potential energy savings not only reduces the conservational impact of your business, but they also reduce the bottom line. Our compressed air audit helps customers reduce their power consumption and compressed air system load, and prevent wear and tear, which further extends the lifetime of the entire compressed air system.
HOW IS COMPRESSED AIR SYSTEM AUDIT DONE?
Conducting an air audit involves a systematic assessment of a compressed air system to evaluate its efficiency, identify areas of improvement, and optimize energy usage. Some of the compressed air audit equipment includes flow meters, pressure gauges, leak detection devices, dew point monitors, oil content analysers, data loggers and more.
Information: Relevant data about the compressed air system is collected, including equipment specifications, operating hours, maintenance records, and utility bills. This information provides insights into the system's performance and energy consumption.
Leak Detection: Compressed air leak audits use leak detection equipment such as ultrasonic leak detectors or soap bubbles to identify and locate compressed air leaks in the system. Leaks are a common source of energy waste and can significantly impact system efficiency.
Air Quality Assessment: The quality of compressed air is tested using instruments such as particle counters, dew point meters, and oil vapor analysers. Parameters such as particle concentration, moisture content, and oil contamination are measured to ensure compliance with quality standards.
Pressure Measurement: The operating pressure at various points in the compressed air system is measured to assess pressure drop and distribution. Evaluate pressure levels against recommended operating parameters and identify opportunities to optimise pressure settings.
Flow Measurement: Using flow meters, the actual airflow rates at different stages of the compressed air system is measured and compared to the equipment specifications and design requirements to identify inefficiencies or capacity issues.
Energy Consumption Analysis: Compressed air energy audit quantifies the energy consumption of the compressed air system using energy meters or utility bills. Calculate energy usage for compressors, air dryers, and other components to identify areas of high energy consumption and potential savings.
End-Use Assessment: Evaluation on how compressed air is used in various applications and processes within the facility. Identifying opportunities for demand-side management, air usage optimisation, and efficiency improvements in end-use equipment.
Data Analysis: Analysing the collected data to identify patterns, trends, and opportunities for improvement. Looking for inefficiencies, energy-saving opportunities, and areas where system performance can be optimised.
Report and Recommendations
Compiling audit findings into a report that outlines recommended actions for improving the efficiency and performance of the compressed air system. Providing cost estimates, payback periods, and prioritised recommendations for implementation.
Implementation
Developing an action plan based on audit recommendations and implementing energy-saving measures, system upgrades, and operational improvements as needed. Monitoring the performance of implemented measures to ensure effectiveness and tracking energy savings over time.
Compressed air audit's top 5 targets
- Energy Efficiency
- Detecting AirLeakage
- Compressed Air System and Demand
- Air Quality
- Operational Practices
Comprehensive Air Audit:
- Total systems scientific approach.
- Demand-side flow analysis [end use].
- Supply-side flow optimisation.
- Full measurement of power consumption including power factor.
- Actual flow, pressure & power requirements.
- Quality of the compressed air &dew point [where relevant].
Air Leakage Management Plan:
- Air leakage recognition, quantification and costing.
- Air leakage correction recommendations.
- Air leakage tracking [data management for repeat surveys].
- Targeting of maintenance up grades.
Detailed Measurement & Technical Analysis:
- Flow demand classification and optimisation
- Compressed air system distribution
- Possibility verification
- Cost savings analyses
- Recommendations and conclusions
- Continuing plan to reduce energy costs
Energy is a valuable resource, and compressed air is an expensive utility that finds application in a wide range of processes across various industries. The prudent, careful and energy-efficient use of compressed air is vital as it affects the viability of any processing activity. We, at ELGi, are involved in the manufacturing of air compressors and offering compressed air solutions, with over 60 years of experience in research and innovation of air compressors, instrumentation, and services. Our proven expertise in these fields has enabled us to understand compressed air operations accurately, thus allowing us to pioneer techniques and equipment for auditing energy consumption.
The audit of energy consumption is a specialised process; it takes through knowledge and expertise in multiple fields to estimate, design, and commission and undertake performance monitoring of projects for energy conservation. We have an expert team of mechanical, electrical and instrumentation engineers. They not only conduct the audit survey but also train end-users in key energy-oriented functional areas to ensure that energy is utilised most efficiently.
Targets & Benefits of Energy Audit at Compressed Air System:
- Accurate measurement of the compressed air system.
- Reduction in the amount of energy, and required for the generation and use of the utility.
- Trapping of any unused energy.
- Recycling and efficient use of energy.
We enable energy-intensive industries to utilise, consume and manage compressed air efficiently, thus helping to cut the electricity bills drastically, and turn the operations more competitive by increasing productivity and overall profitability.
The objective of the activities is to achieve a combination of the following benefits:
- Better and more accurate monitoring of compressed air utilities.
- Reduced specific energy consumption of air compressor generation.
- Elimination of total wastage.
- Reduction in operating & maintenance costs.
- Reduction in downtime of equipment.
- Increase in process output.
- Improvement in product quality and quantity.
- Massive savings in costs and an increase in revenue.
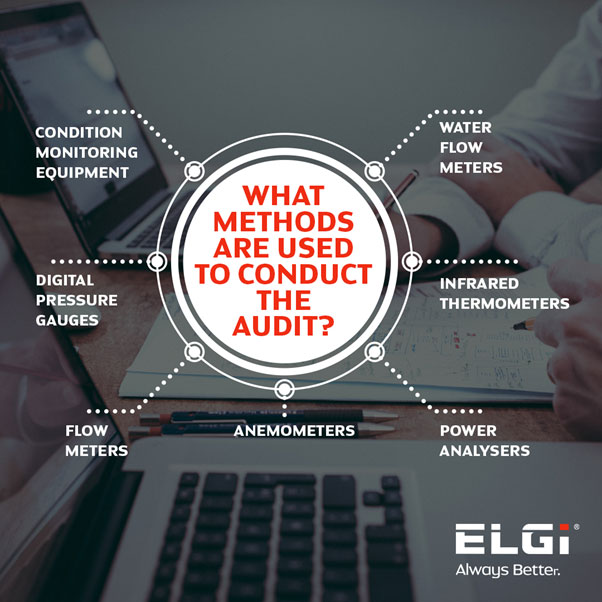
INTERESTED IN OUR
SERVICES & PARTS?
If you are interested in our extensive range of services and parts, click below.
SERVICE REQUEST