What Makes Screw Air Compressors the Preferred Choice for Air Experts?
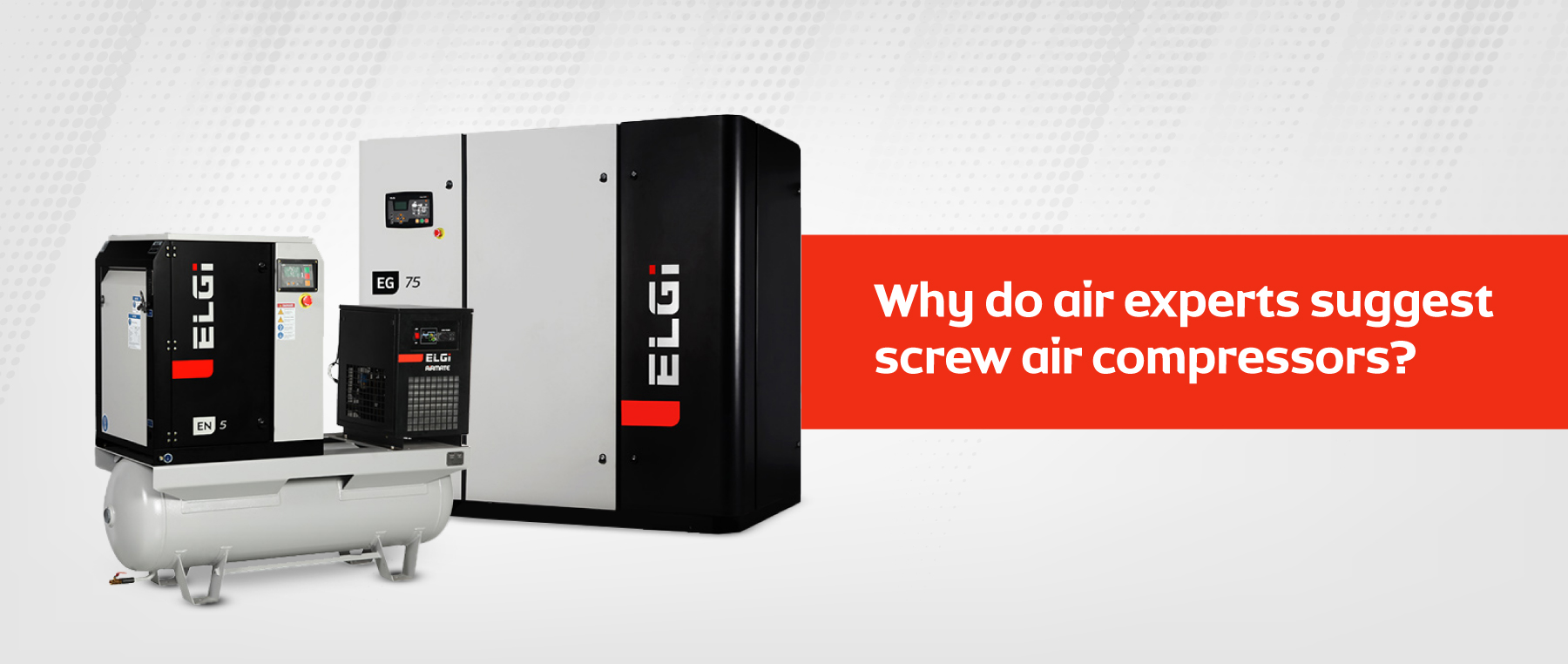
When seeking the optimal air compressor solution for your operations, it's essential to consider various parameters which extend far beyond the upfront cost. The productivity and effectiveness of your material handling systems, spray painting procedures, and diverse machine tools are heavily contingent upon the compressed air system. Consequently, industry experts often advocate for the adoption of screw air compressors for their exceptional efficiency, continuous operational capacity, reduced noise levels, space-saving design, and reliability.
Air compressors can be broadly categorized into two types: reciprocating and rotary screw compressors. Reciprocating compressors use pistons to compress air, while rotary screw compressors utilize rotating elements to generate compressed air. Among them, rotary screw compressors consist of interlocking helical rotors that compress the air as it moves through the compression chamber, allowing for continuous and efficient operation.
Screw Air Compressors
Screw air compressors are known for their efficiency, reliability, and ease of use. They typically use oil for cooling, sealing, and lubrication within the compressor. These compressors consist of two rotors, often referred to as male and female rotors, which have interlocking helical grooves that reduce the volume of air as it passes through the compression chamber. As the rotors rotate, air is drawn into the chamber, trapped between the lobes of the rotors, and compressed as the volume decreases. The injected oil provides cooling and lubrication, ensuring smooth operation and minimizing wear on the components. The compressed air and oil mixture are then separated, with the oil being cooled and recycled, while the compressed air is discharged.
Types of Rotary Screw Air Compressors
There are two main categories of rotary screw air compressors commonly used in businesses and manufacturing:
Oil-free Screw Air Compressors: These compressors operate without the need for oil lubrication. Instead, alternative lubricants such as PTFE, distilled water, or proprietary coatings are used for lubrication and heat dissipation. Oil-free compressors are essential for industries where even the tiniest trace of oil is unacceptable, such as food and beverage production, pharmaceuticals, packaging, and other sensitive sectors.
Oil-lubricated Screw Air Compressors: In oil-lubricated screw compressors, oil is introduced into the compression chamber to facilitate lubrication and efficient heat dissipation. The oil undergoes a separation process from the discharge stream, followed by cooling, filtration, and recycling. These compressors are commonly used in heavy drilling and mining operations, metallurgical processes, mobile tire services, and various other applications that can tolerate minimal traces of oil.
Advantages of Screw Air Compressors
Screw air compressors offer several advantages, making them highly recommended by air experts:
High Efficiency: Compared to reciprocating compressors, screw compressors are known for their high energy efficiency. The continuous compression process reduces energy waste.
Continuous Operation: Screw compressors provide a steady and uninterrupted supply of compressed air. They don't require frequent start-stop cycles, which can affect efficiency and equipment lifespan.
Low Noise and Vibration: Screw compressors produce less noise and vibration due to their helical rotor design. This makes them suitable for noise-sensitive environments.
Maintenance and Reliability: With fewer moving parts compared to reciprocating compressors, screw compressors are known for their reliability and require minimal maintenance. This results in reduced downtime and maintenance costs.
Applications of Screw Air Compressors
Screw air compressors find applications in various industries and sectors, including:
Industrial Manufacturing: Screw compressors are widely used in automotive assembly lines, metal fabrication, plastics production, and more. They power pneumatic tools, robotic systems, and machinery.
Construction and Building Sites: They are commonly used to power jackhammers, nail guns, sandblasting equipment, and painting systems on construction sites.
Automotive Industry: Screw compressors play a vital role in automotive manufacturing and repairs. They power air tools, assist in tire inflation, and enable pneumatic systems in car assembly lines.
Food and Beverage Production: Screw compressors provide clean and compressed air for various operations in the food and beverage processing industry. They control packaging systems, power pneumatic conveyors, and ensure product quality.
Pharmaceuticals and Healthcare: In pharmaceutical manufacturing, screw compressors supply clean compressed air for aseptic processes, packaging, and equipment operation. In healthcare, they power medical air systems for respiratory therapy and surgical equipment.
Pneumatic Tools and Machinery: Screw compressors are extensively used to power a wide range of pneumatic tools and machinery, ensuring efficient operation.
ELGi's Rotary Screw Air Compressors
ELGi offers a range of rotary screw air compressors that cater to different industrial needs, from lighter tasks to heavy-duty applications. With exclusive airend configurations, cutting-edge features, and innovative advancements, ELGi compressors deliver cost savings, improved uptime, and premium compressed air solutions.
AB Series: ELGi is among the few companies that design and manufacture airends for oil-free compressor technology. The AB series air compressors offer superior efficiency, reliability, and air quality. The Class-"0" certified compressed air is crucial for sensitive applications in industries like pharmaceuticals, food, and beverages.
EN Series: ELGi's EN series oil-lubricated screw air compressors are known for their reliability, low maintenance, compact design, and efficiency. They feature efficient air-oil separation technology and belt drive transmission for optimal power transmission. Optional variable frequency drives are available to match output with demand, saving energy. The EN series finds applications in various industries, including textile, automotive, paper, food processing, and small machining workshops.
EG Series: ELGi's EG series oil-lubricated screw air compressors offer a significant advancement in design and performance. Each component is crafted for reliability and easy maintenance. With energy-efficient eta-V profile rotors, these compressors provide optimal performance. They are compliant with international standards and come with a top-tier warranty program and low operating costs.
For expert assistance tailored to your business needs, reach out to our air experts at https://www.elgi.com/ae/contact-us/.
RELATED BLOGS
When it comes to compressed air systems, rotary screw compressors have establishe...
Read MoreReciprocating air compressors are vital components in many industries, including m...
Read MoreOil-free air compressors are becoming increasingly popular due to their ability to ...
Read More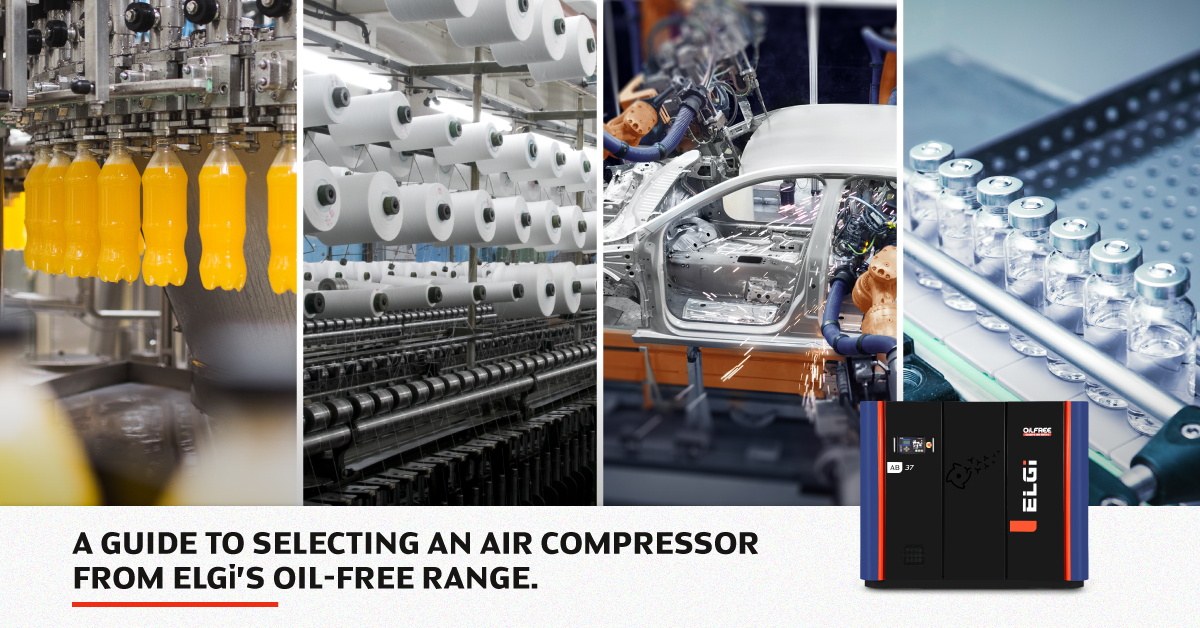
Oil-free air compressors are used in industries where clean air...
Read More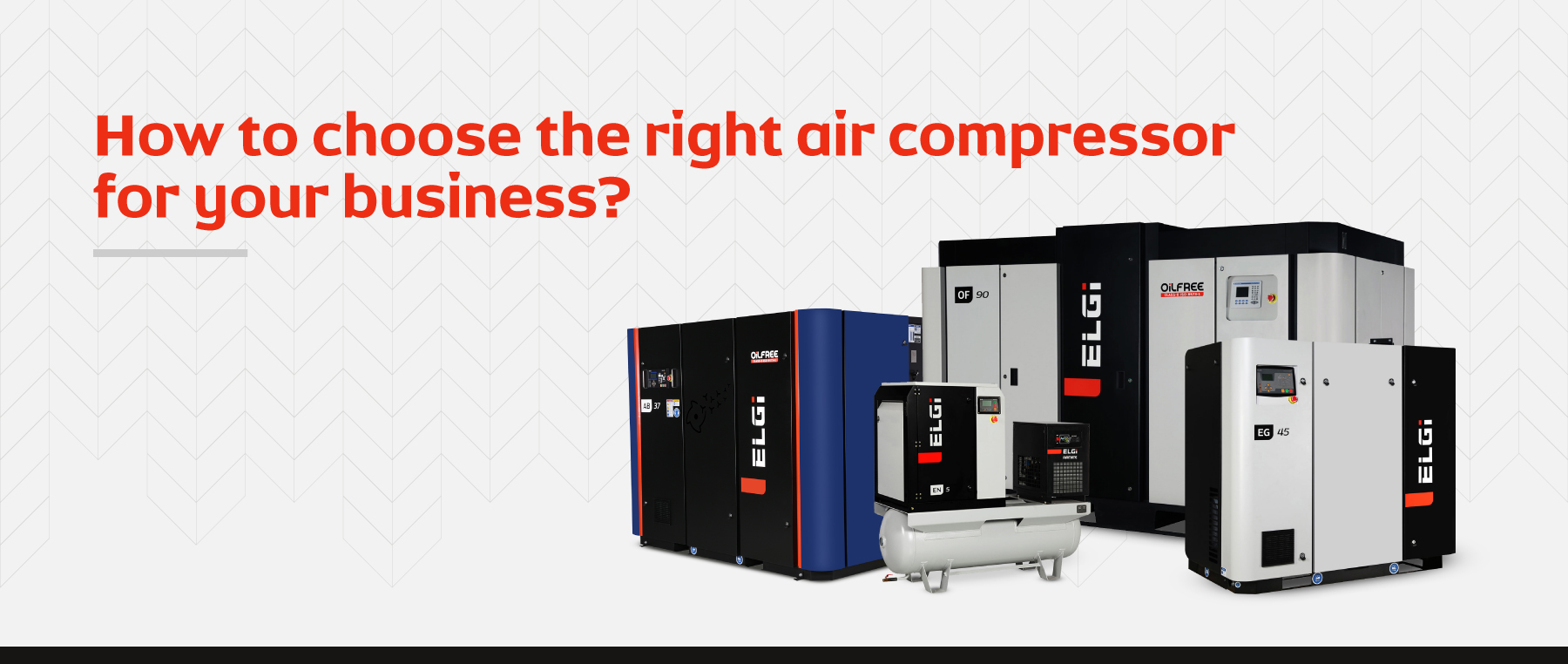
As automation expands across various industries, the demand for...
Read More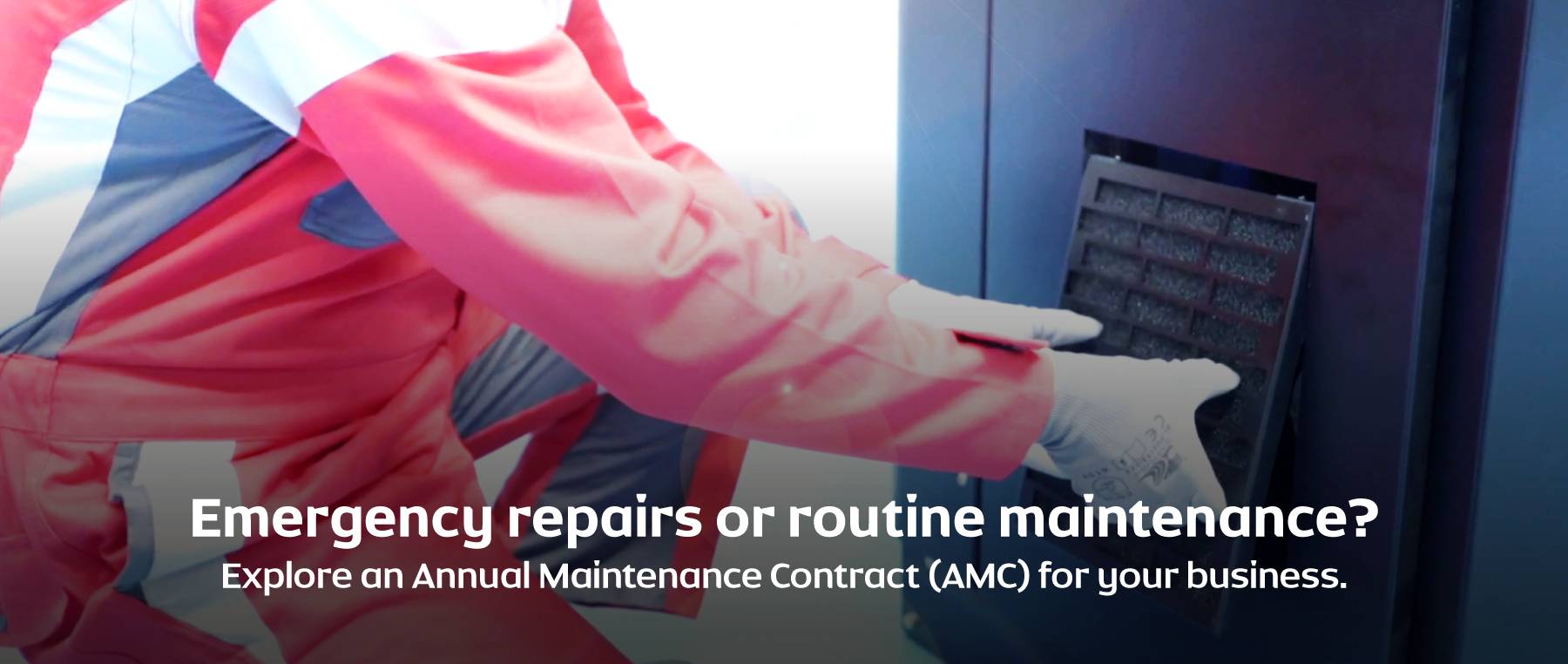
Air compressors require regular servicing and maintenance, a fa...
Read More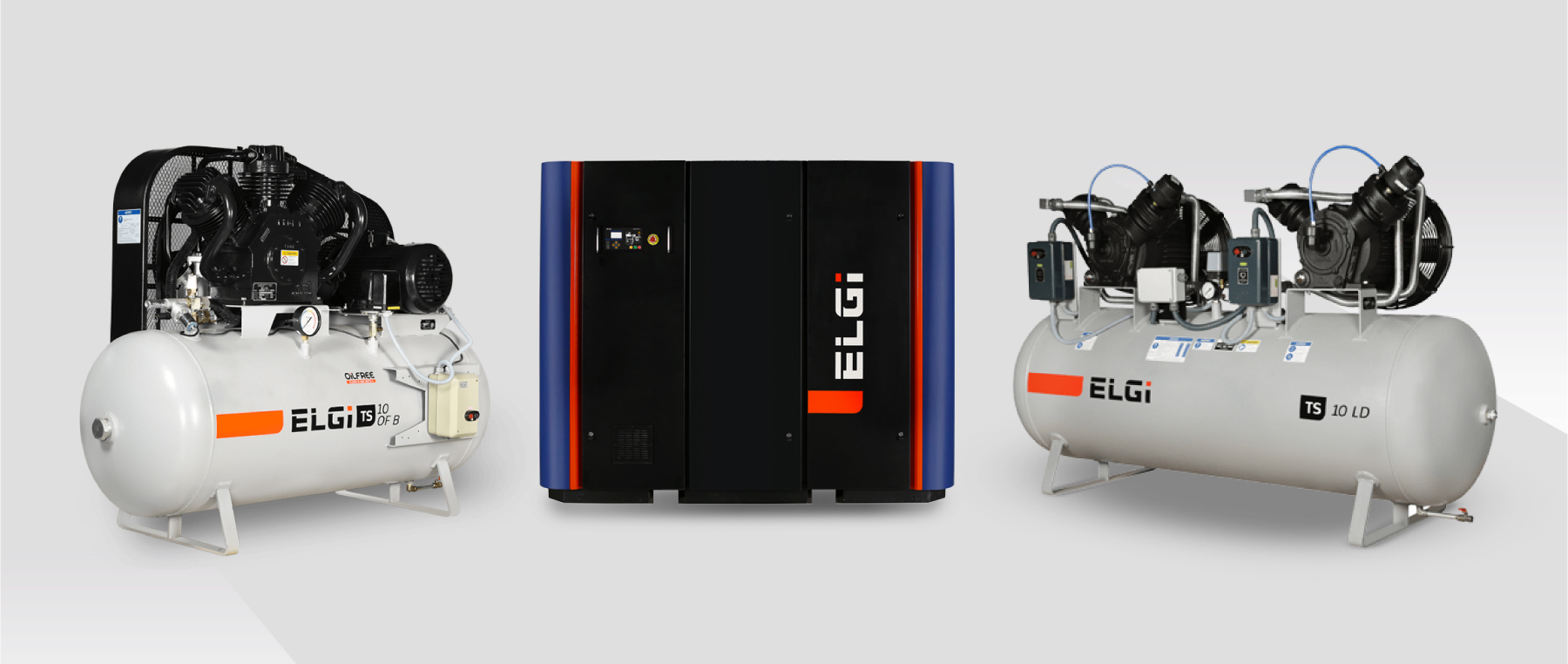
The two most commonly used types of air compressors are rotary ...
Read More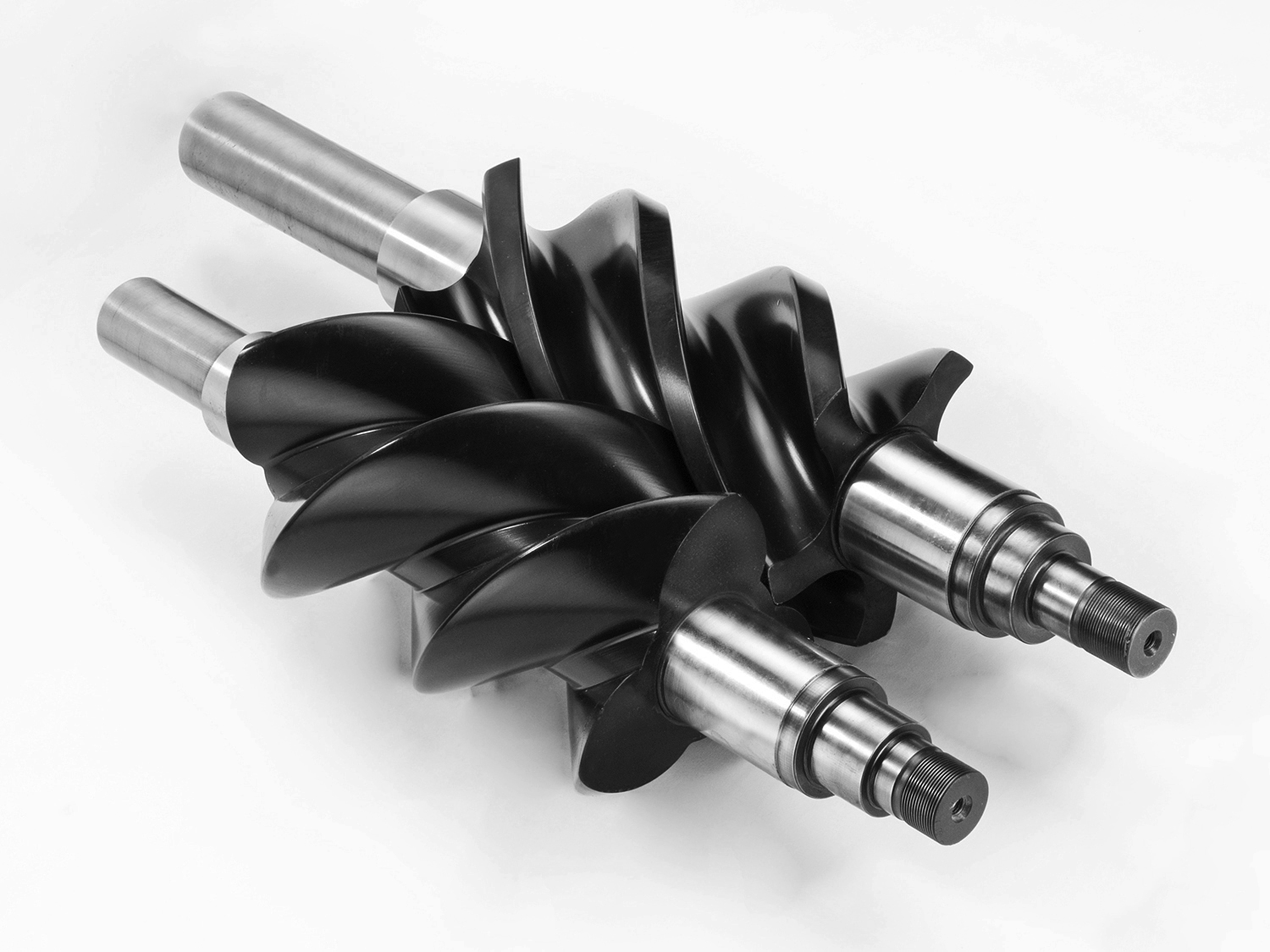
Oil-free compressors eliminate the need for lubricating oil in ...
Read More