Making Screw Air Compressors Oil-free
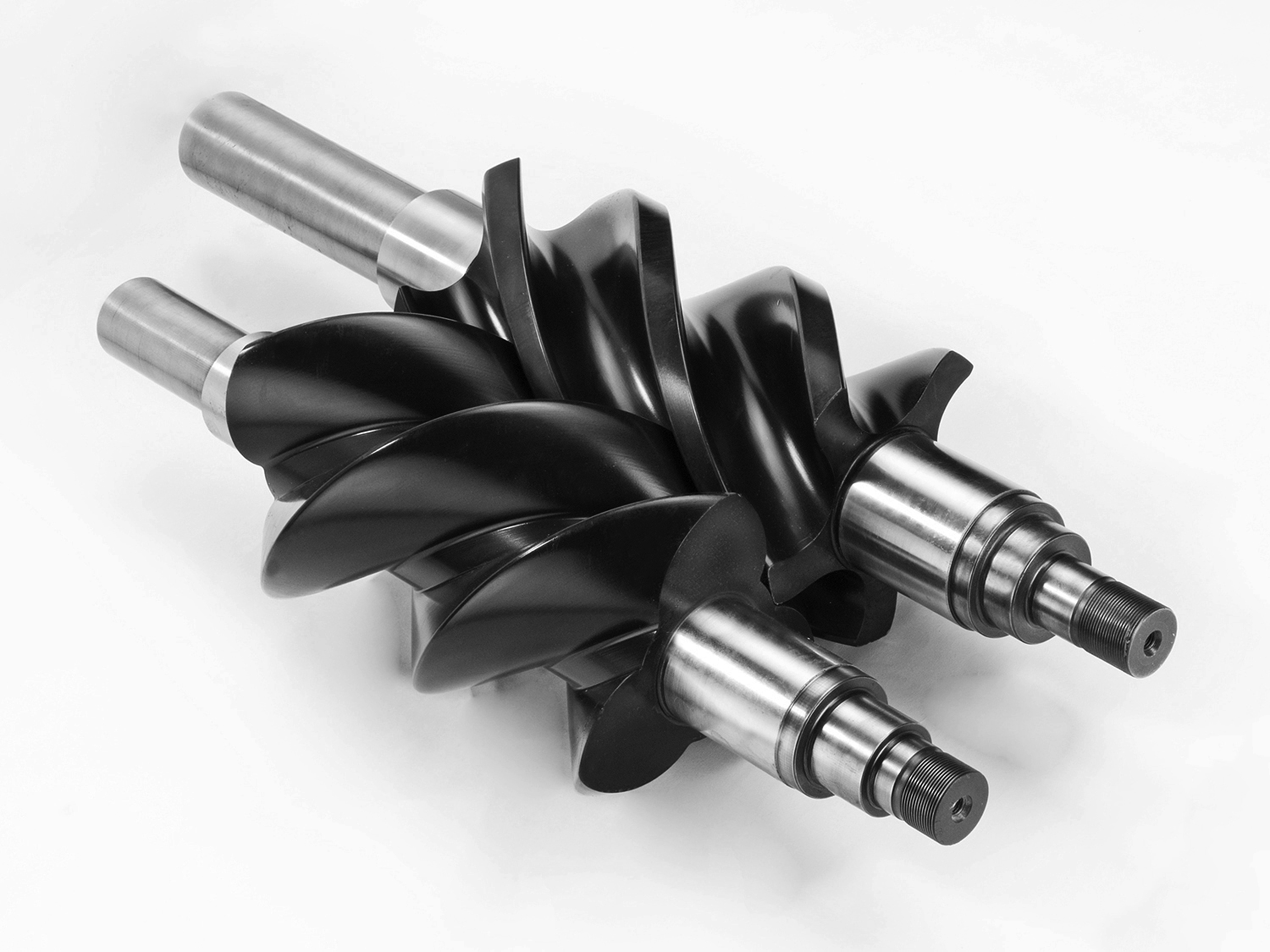
Oil-free compressors eliminate the need for lubricating oil in the compression process, offering several benefits over traditional oil-lubricated compressors.
Understanding Screw Air Compressors
Screw air compressors are positive displacement machines that utilize two intermeshing rotors to compress air. As air enters the compressor, it becomes trapped between the lobes of the rotating rotors, progressively compressing as they turn. Conventionally, these compressors rely on oil for lubrication and cooling, aiding in reducing friction, dissipating heat, and ensuring an airtight seal. However, the presence of oil in the compressed air can cause contamination issues in specific industries, compromising product quality and processes. To address this concern, oil-free screw compressors have been developed, operating without any lubricating oil in the compression chamber, guaranteeing clean and high-quality compressed air output.
The Necessity for Oil-Free Screw Air Compressors
Oil-free compressors play a crucial role in industries where air quality is of utmost importance, such as pharmaceutical manufacturing, food processing, electronics, and clean air environments. In pharmaceutical manufacturing, for instance, compressed air directly interacts with sensitive drugs and equipment, making oil contamination completely unacceptable. Similarly, in the food industry, oil-free compressors prevent the risk of oil entering the production process, ensuring the integrity and safety of food products. In electronics manufacturing, where precision is paramount, oil-free compressors safeguard sensitive electronic components from potential damage caused by oil particles. Moreover, clean room environments like laboratories, research facilities, and hospitals necessitate compressed air free from any oil contamination to maintain the purity of experiments, tests, and medical procedures. Such critical applications made the need for oil free technology neccessary.
Oil-Free Screw Air Compressor Technology
Oil-free screw compressors employ advanced technologies to operate without the need for oil. One specific technology utilized is the dry screw compressor, which incorporates special coatings on the rotors, precise manufacturing techniques, and advanced sealing methods to eliminate the requirement for oil within the compression chamber. These compressors utilize rotors coated with a self-lubricating surface called PTFE (polytetrafluoroethylene), reducing friction and ensuring efficient compression without oil. As a result, these compressors require minimal maintenance, are energy-efficient, and deliver clean, oil-free compressed air.
Another technology employed is the water-injected screw compressor,where water acts as the lubricant and coolant, replacing oil. Injected water creates a hydrodynamic seal between the rotors, minimizing friction and heat generation. Furthermore, the water absorbs the compression heat and carries it away, ensuring that the compressor operates within safe temperature limits.
Both dry screw and water-injected screw compressors possess advantages and limitations. Dry screw compressors are employed in industries demanding the highest air quality, providing completely oil-free compressed air. However, their specialized design may result in higher initial costs. On the other hand, water-injected screw compressors offer excellent efficiency, lower upfront costs, and easier maintenance. Nonetheless, it is crucial to monitor water quality and filtration to ensure optimal performance and prevent any contamination risks.
Benefits of Oil-Free Screw Air Compressors
Oil-free screw air compressors deliver superior air quality by eliminating the risk of oil contamination. This ensures that the compressed air meets the most stringent air quality standards, safeguarding product integrity and preventing damage to sensitive equipment and processes. Oil-free compressors are invaluable in industries where compressed air directly interacts with end products, such as pharmaceutical manufacturing, where purity is an absolute requirement.
Furthermore, oil-free compressors reduce maintenance requirements and costs. Traditional oil-lubricated compressors necessitate regular oil changes, filter replacements, and other maintenance tasks to ensure optimal operation. By eliminating the need for these activities, oil-free compressors reduce downtime and maintenance costs, making them more cost-effective in the long run.
Moreover, oil-free compressors contribute to a cleaner and healthier working environment. The absence of oil in the compression process eradicates the risk of oil mist or vapour entering the ambient air, improving air quality for occupants and reducing potential health hazards associated with oil inhalation.
Lastly, oil-free screw compressors have positive environmental implications. By eliminating lubricating oil, these compressors minimize the potential risk for oil leaks, spills, and the release of oil-contaminated air into the atmosphere.
Considerations and Challenges
While oil-free screw compressors offer numerous benefits, there are several considerations and challenges to bear in mind when implementing this technology. One critical consideration is the upfront cost. Oil-free compressors, especially those utilizing advanced technologies, may entail higher initial investment costs compared to conventional oil-lubricated compressors. However, evaluating the long-term benefits and potential cost savings in terms of maintenance, energy efficiency, and improved product quality is crucial.
System design represents another vital aspect to consider. Proper sizing and layout of the compressor system is essential to ensure optimal performance and efficiency. Evaluating the compressed air demand, pressure requirements, and any specific conditions unique to the application or industry is imperative. Consulting with experts or original equipment manufacturers (OEMs) can aid in determining the most suitable oil-free compressed air system for your requirements.
Maintenance requirements for oil-free compressors should also be taken into account. While these compressors generally require less maintenance than their oil-lubricated counterparts, regular monitoring of water quality (for water-injected compressors) or rotor coating conditions (for dry screw compressors) is necessary to ensure continued efficient operation. Adhering to the manufacturer's recommended maintenance procedures maximizes the compressor's lifespan and reliability.
ELGi Oil-Free Compressor Technology
ELGi stands out as one of the few manufacturers of oil-free air compressors that develop and produce their own lubricant-free airends. These compressors are meticulously engineered to ensure maximum uptime and the delivery of clean compressed air. ELGi's unique eta-V rotor design effectively minimizes pressure losses while facilitating high airflow at the rated power.
For a comprehensive range of oil-free compressed air solutions, ELGi offers both the OF Series, designed to handle large capacities and the AB Series, suitable for low to medium capacities. The design of both the AB Series and the OF Series oil-free air compressors prioritizes easy serviceability, strategically placing all access points within convenient reach and optimizing the overall system structure. To provide complete peace of mind during machine operation, ELGi's flagship UPTIME Warranty programs cover all ELGi air compressors.
Connect with our team of compressed air experts to identify the best solution for your application https://www.elgi.com/ae/contact-us/.
RELATED BLOGS
When it comes to compressed air systems, rotary screw compressors have establishe...
Read MoreReciprocating air compressors are vital components in many industries, including m...
Read MoreOil-free air compressors are becoming increasingly popular due to their ability to ...
Read More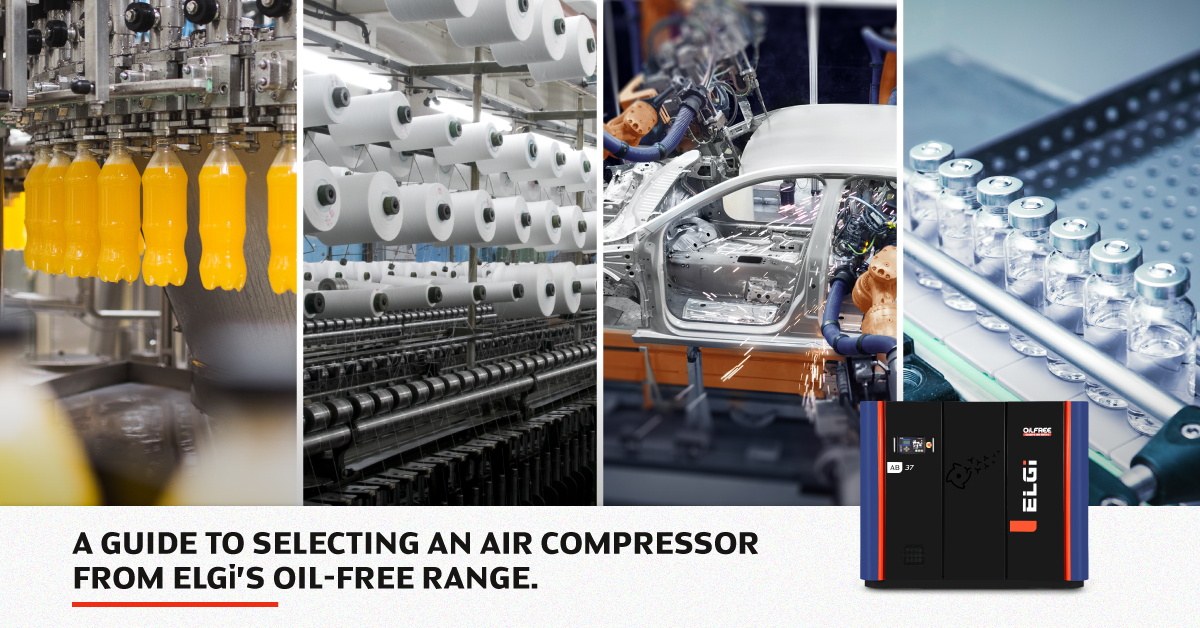
Oil-free air compressors are used in industries where clean air...
Read More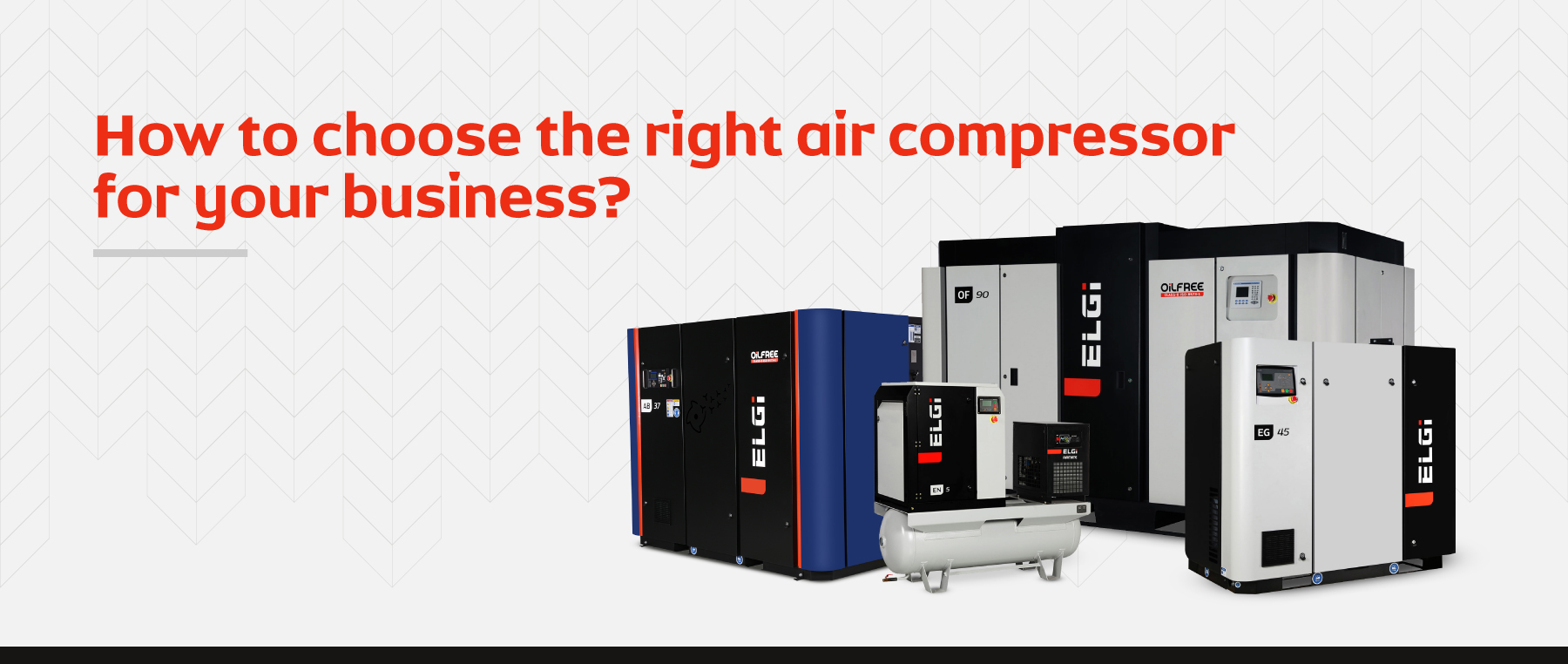
As automation expands across various industries, the demand for...
Read More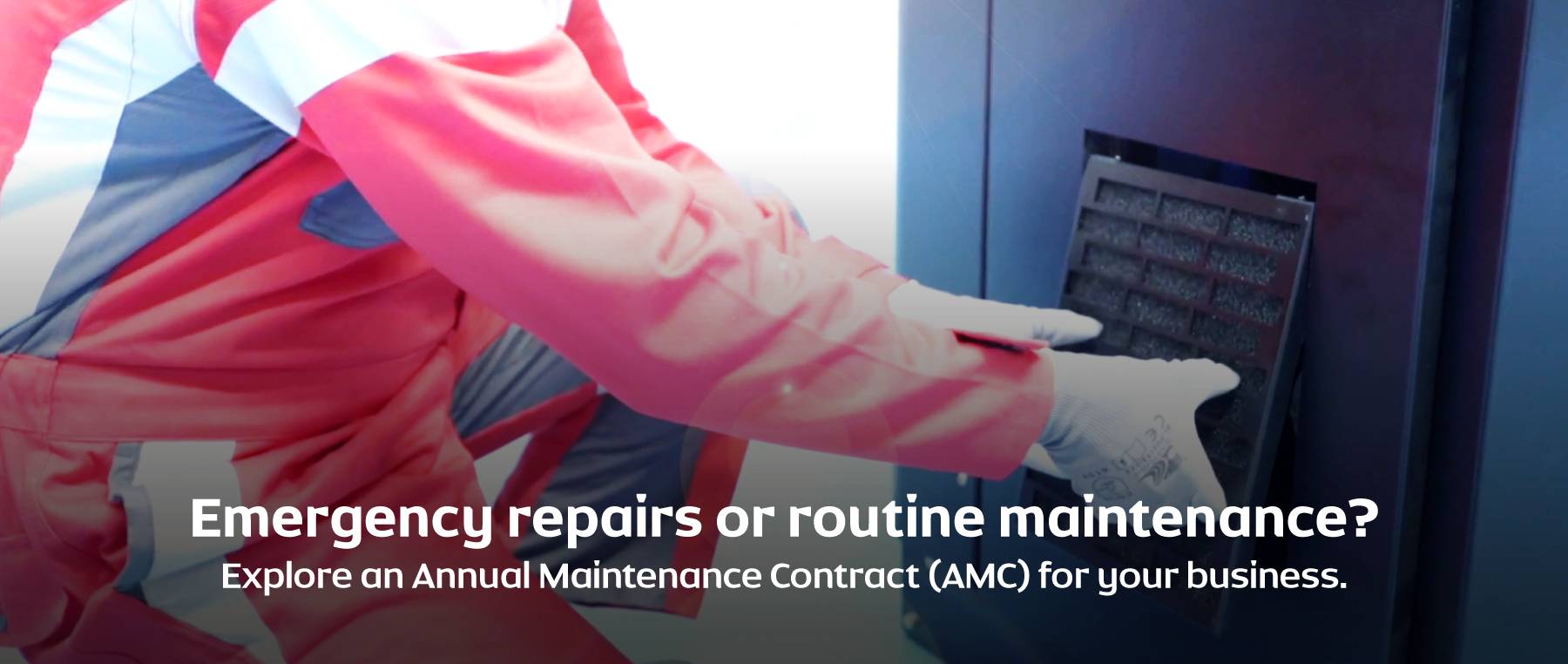
Air compressors require regular servicing and maintenance, a fa...
Read More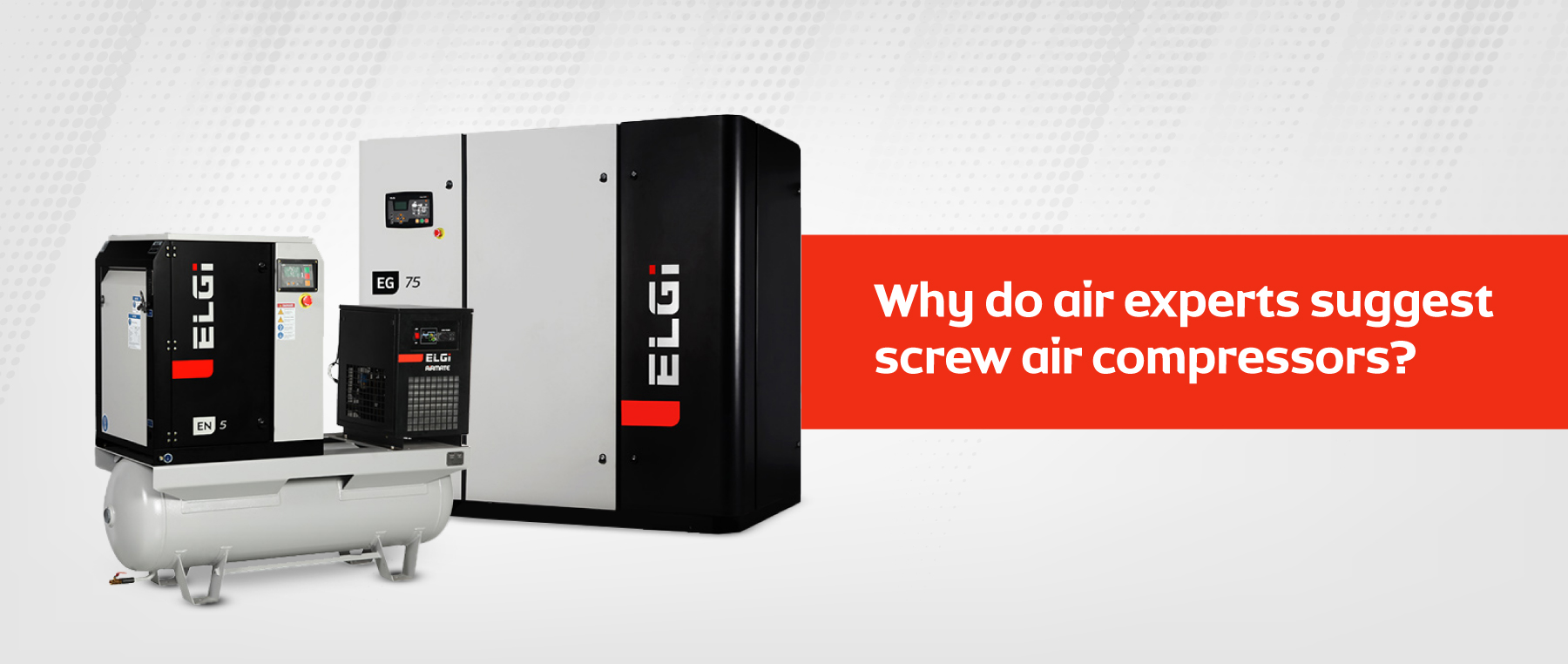
When seeking the optimal air compressor solution for your oper...
Read More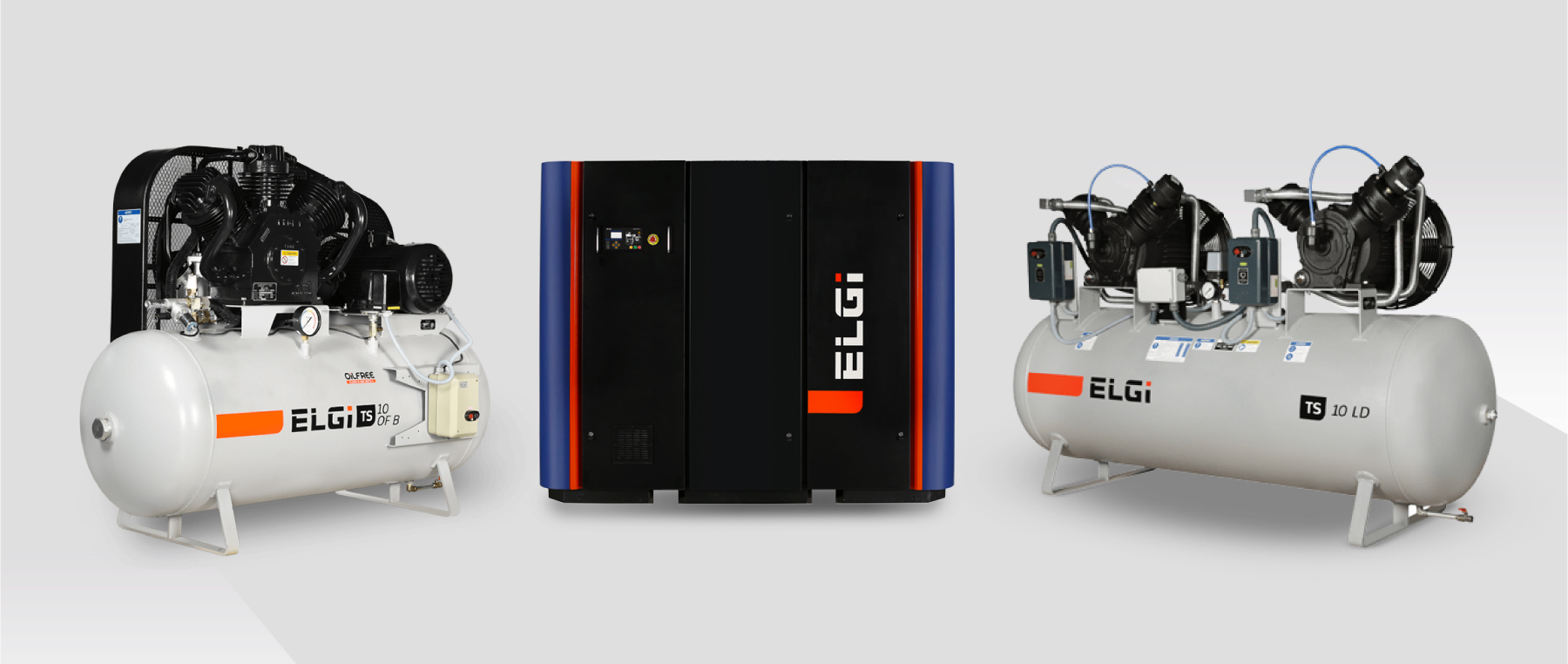
The two most commonly used types of air compressors are rotary ...
Read More