How to Measure and Improve Reciprocating Compressor Performance
Reciprocating air compressors are vital components in many industries, including manufacturing, oil and gas, and power generation. Their performance directly impacts the efficiency and reliability of operations in various industries and use cases. This article will delve into the best practices for measuring and improving the performance of reciprocating compressors.
Understanding Reciprocating Compressor Performance
A reciprocating air compressor, also known as a piston air compressor, is a type of air compressor that uses a piston and cylinder mechanism to compress gas. The performance of a reciprocating compressor is primarily determined by two factors: its capacity and its efficiency.
Capacity refers to the volume of gas that the compressor can handle during a given period. This is determined by the volume displaced by the pistons during their movement. The capacity of a reciprocating compressor can be influenced by several factors, including the size of the cylinder, the speed at which the piston moves, and the pressure of the gas being compressed.
Efficiency is the ratio of the useful work done by the multi-stage reciprocating air compressor to the energy it consumes. In other words, it’s a measure of how effectively the compressor converts input energy (usually in the form of electricity) into output energy (in the form of compressed gas). The efficiency of a reciprocating compressor can be influenced by factors such as the quality of the air intake, the accuracy of the compressor controls, the design of the system, the minimization of pressure drop, and the routine maintenance of the compressor.
Understanding these two aspects of reciprocating air compressor performance is crucial for anyone looking to optimize the operation of these machines. By regularly measuring and monitoring capacity and efficiency, air compressor operators can identify potential issues early. With this information, they can make necessary adjustments and ensure that their compressors are always operating at peak performance.
Measuring Performance
Measuring the performance of a reciprocating air compressor involves several key indicators:
Flow Measurement :
Comparison of measured airflow with predictions can provide insights into the compressor’s performance. This involves using flow meters to measure the amount of fluid that passes through the compressor over a given period.
Inter-stage Pressure Comparison :
Another method of comparing inter-stage pressures with software model predictions can help identify the two-stage reciprocating air compressor’s performance issues. This involves measuring the air pressure at various stages of the compression process and comparing them with the expected values.
Discharge Temperature Comparison :
Cylinders with higher discharge temperatures at the same stage may indicate performance issues. This involves measuring the temperature of the fluid as it exits the compressor.
Valve Cap Temperature Comparison :
Hot valves can be identified by comparing equivalent valve cap temperatures. This involves measuring the temperature of the valve caps and comparing them with the expected values.
Capacity Calculation :
The capacity of each stage can be calculated based on observed pressures and suction temperatures. This involves using the ideal gas law to calculate the volume of gas that the compressor can handle at a given pressure and temperature.
Improving Performance
Improving the performance of a reciprocating air compressor involves several strategies:
System Pressure :
System pressure is a critical indicator of compressor performance. Regular monitoring and adjustments can help maintain optimal performance. This involves using pressure gauges to measure the system pressure and adjusting the compressor settings as needed.
Holistic System View :
A holistic view of the system which may include aspects beyond the compressor itself, can boost its efficiency. By considering the entire compressed air system, including the air intake, piping, and end-use equipment save money, and reduce environmental impact as well.
Modified Mechanisms :
Incorporating modified mechanisms, such as a geared four-bar slider-crank mechanism, can produce favourable stroke characteristics and improve performance. Extra steps like redesigning the dual piston air compressor mechanism can optimize the piston stroke and reduce energy losses.
Optimized Suction Pressure :
In natural gas gathering applications, maintaining the lowest possible suction pressure can provide a significant production advantage. This involves adjusting the compressor settings to optimize the suction pressure and maximize throughput.
Routine Maintenance :
Regular maintenance can ensure the compressor's operation for peak efficiency. Regularly inspecting and servicing the compressor can prevent breakdowns and reduce overall maintenance costs.
Conclusion
Measuring and improving the performance of reciprocating air compressors is a complex but essential task. With the right practices and aftermarket support from our team at ELGi organizations can ensure their compressors operate at peak efficiency, saving money and reducing environmental impact.
ELGi’s Support and Services: ELGi is a global reciprocating compressor manufacturer that offers a wide range of piston compressors for various pneumatic applications.ELGi offers a rapid response system and air restoration with minimal downtime. Our portfolio of over 400 products and accessories caters to a wide range of needs. ELGi’s team of professionals is just a call or email away to help you find exactly what you need.
RELATED BLOGS
When it comes to compressed air systems, rotary screw compressors have establishe...
Read MoreOil-free air compressors are becoming increasingly popular due to their ability to ...
Read More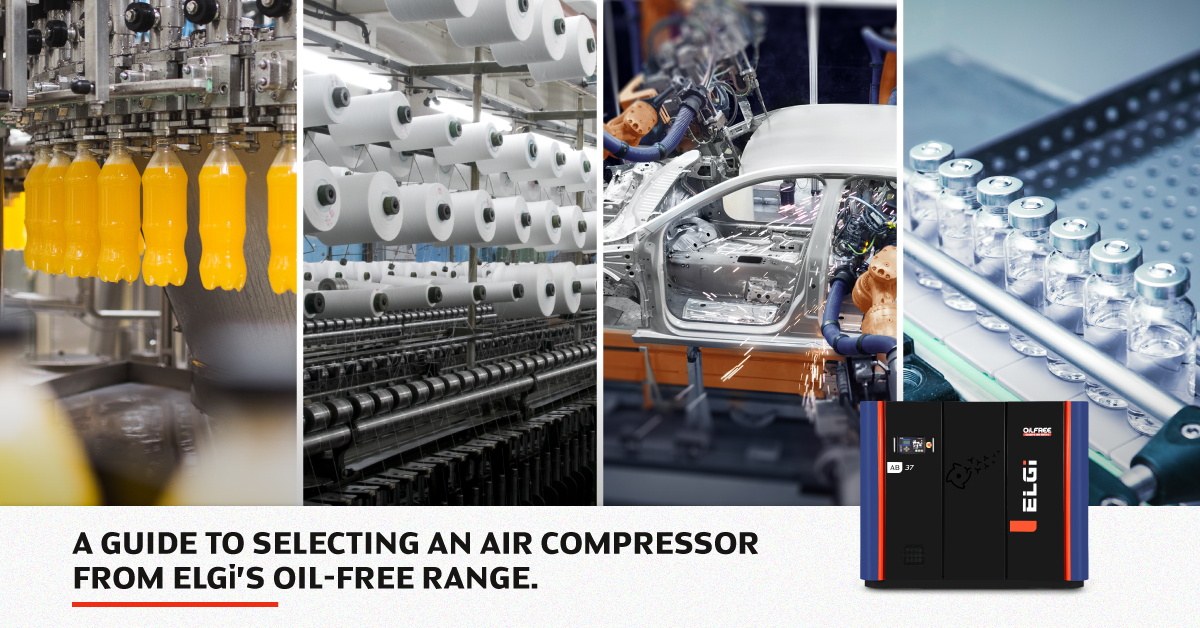
Oil-free air compressors are used in industries where clean air...
Read More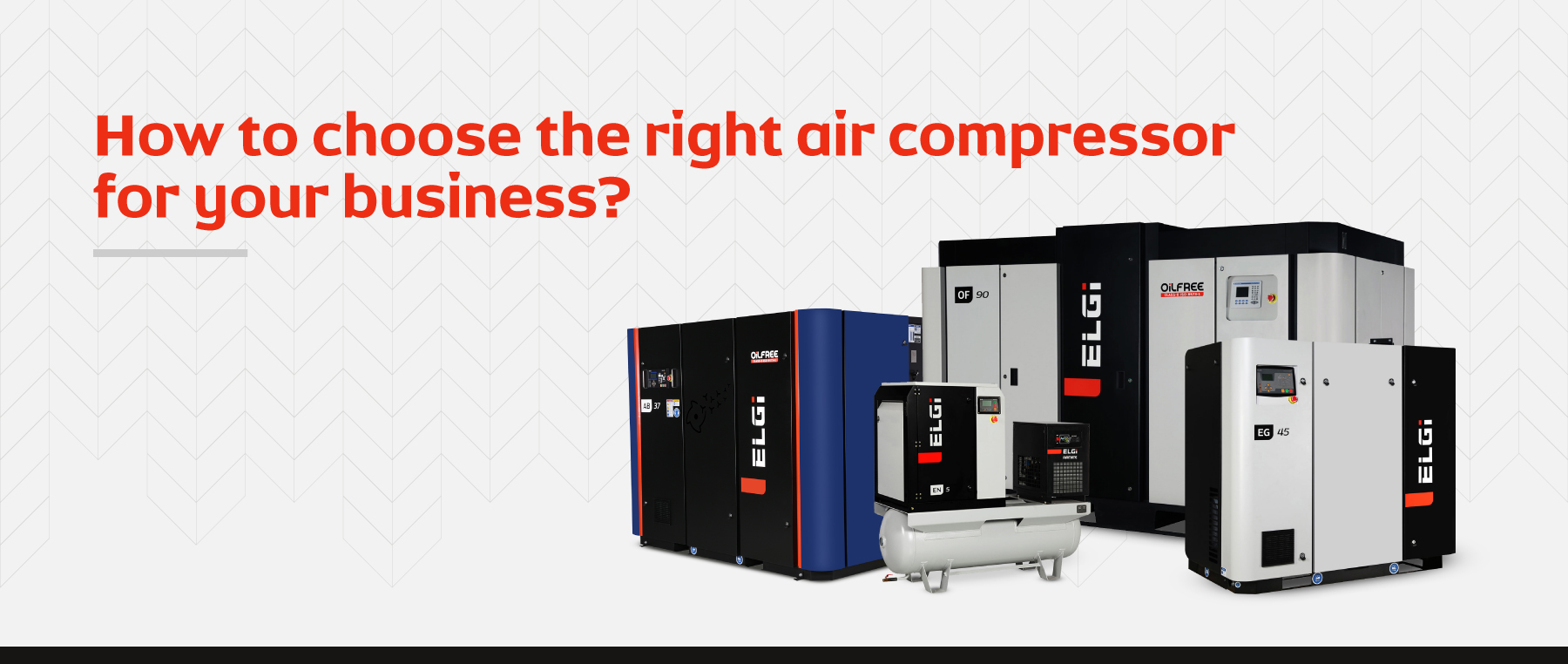
As automation expands across various industries, the demand for...
Read More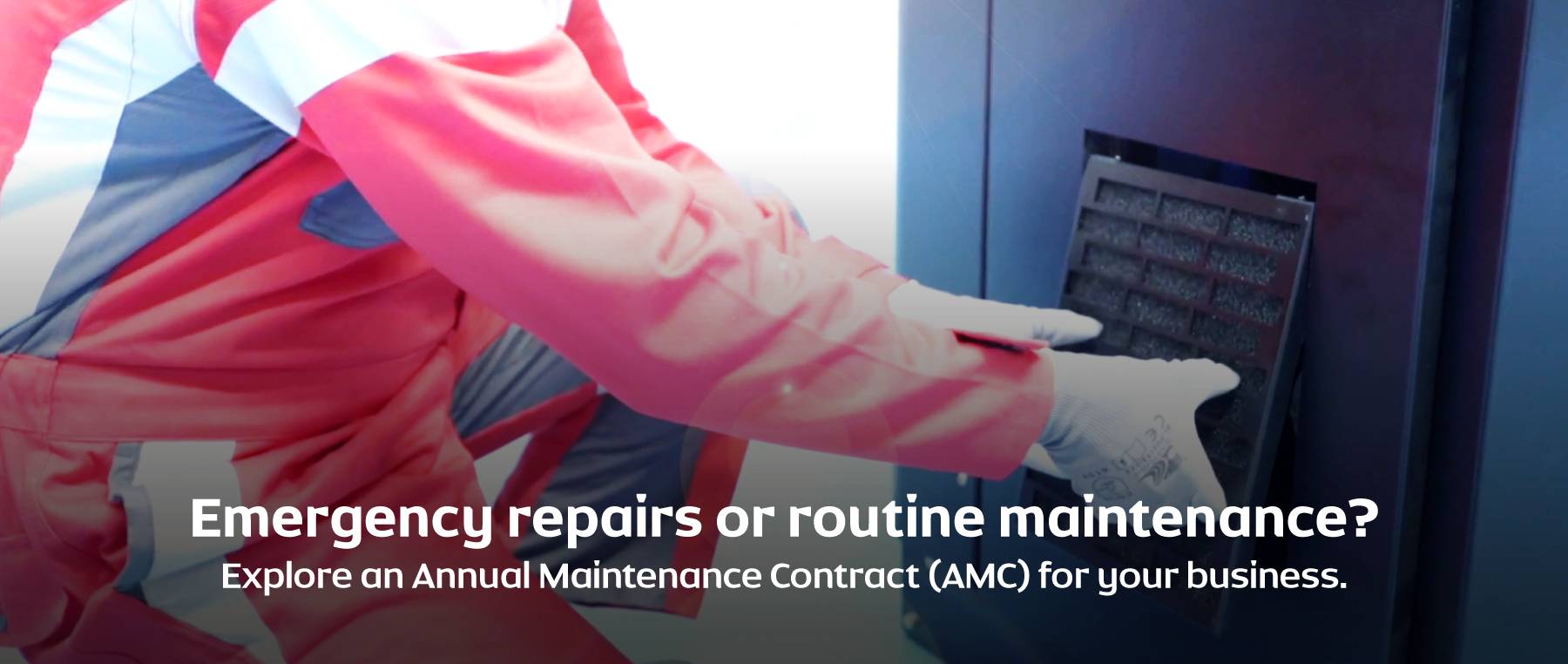
Air compressors require regular servicing and maintenance, a fa...
Read More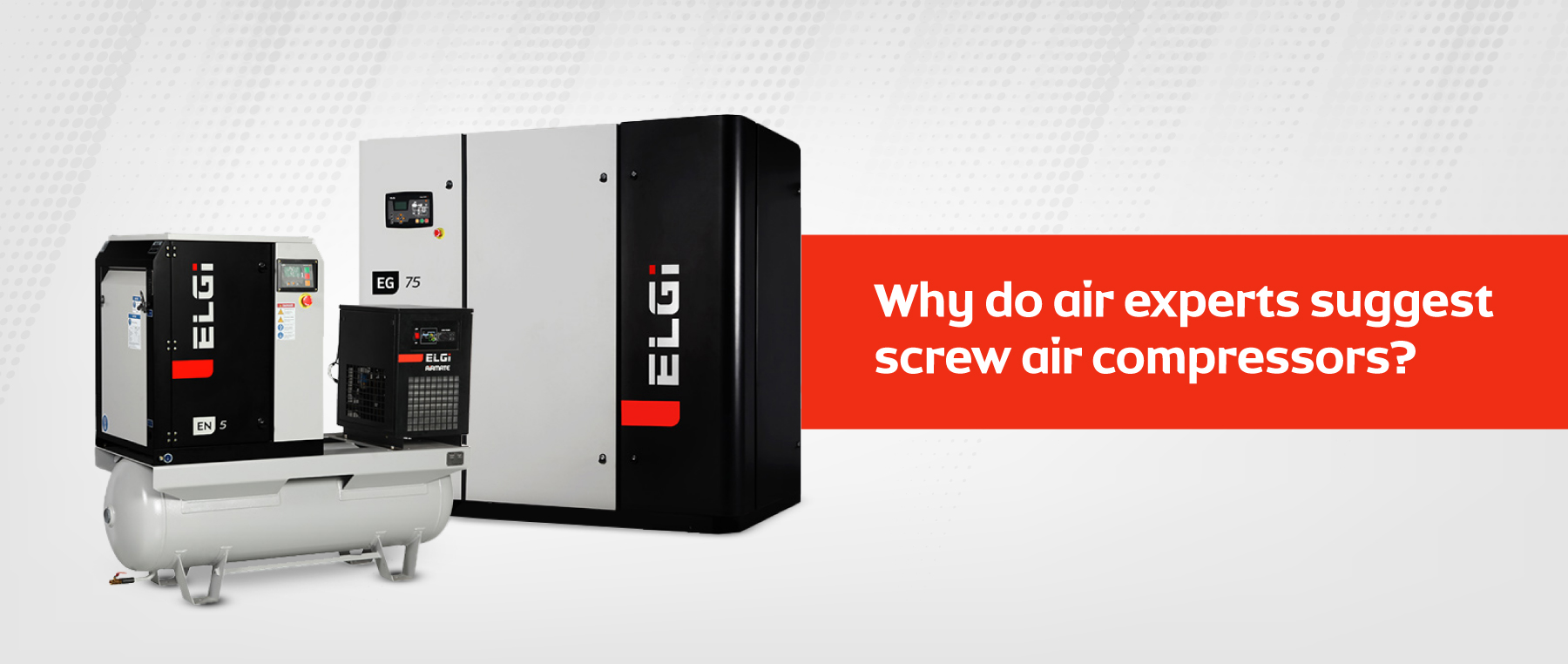
When seeking the optimal air compressor solution for your oper...
Read More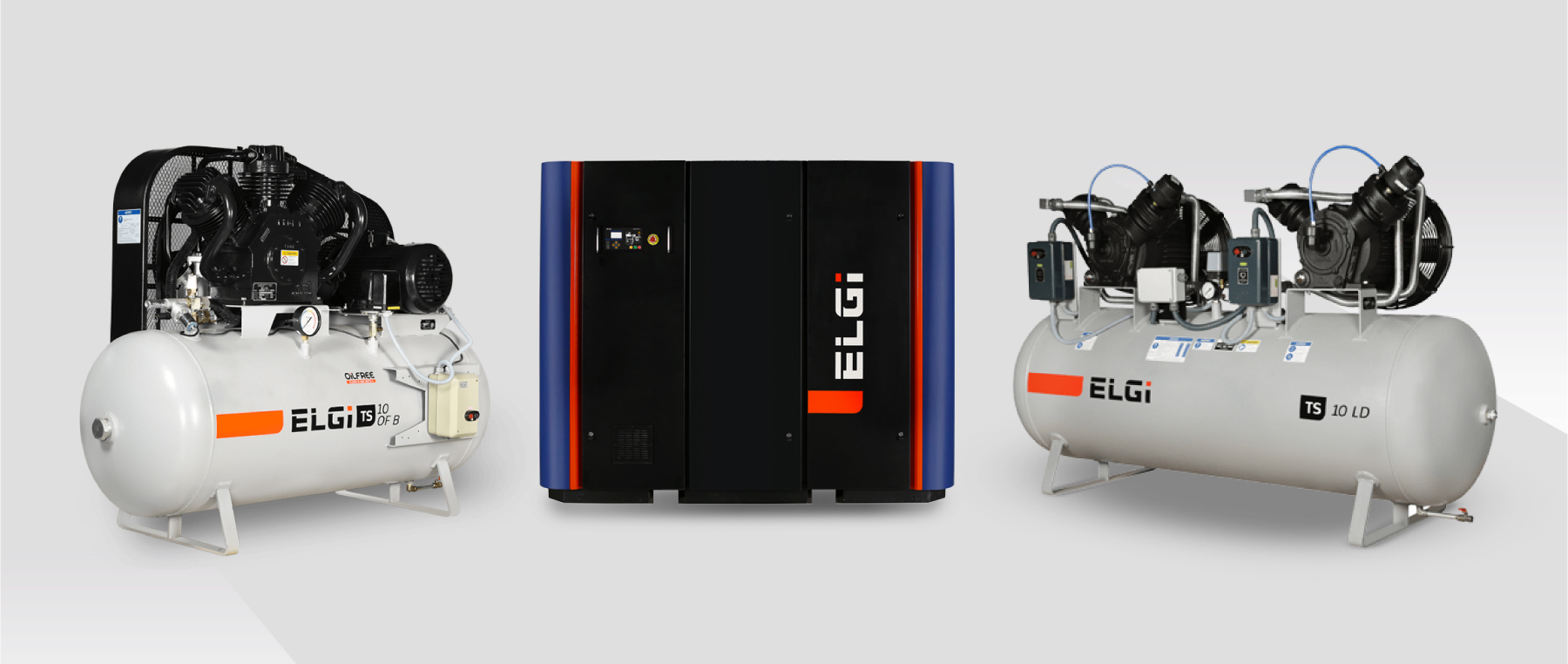
The two most commonly used types of air compressors are rotary ...
Read More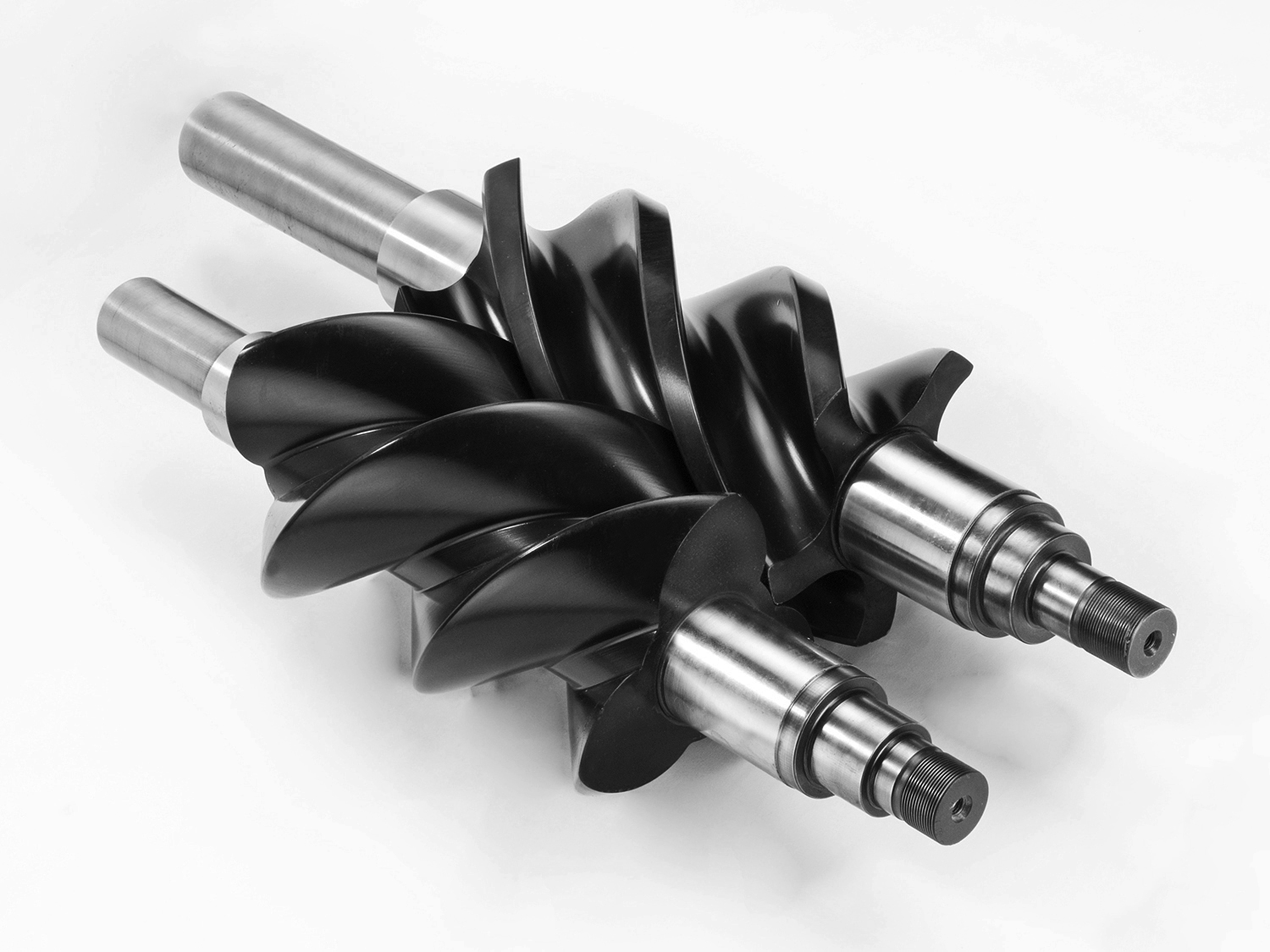
Oil-free compressors eliminate the need for lubricating oil in ...
Read More