Guide to Select a Suitable Air Compressor for Your Business
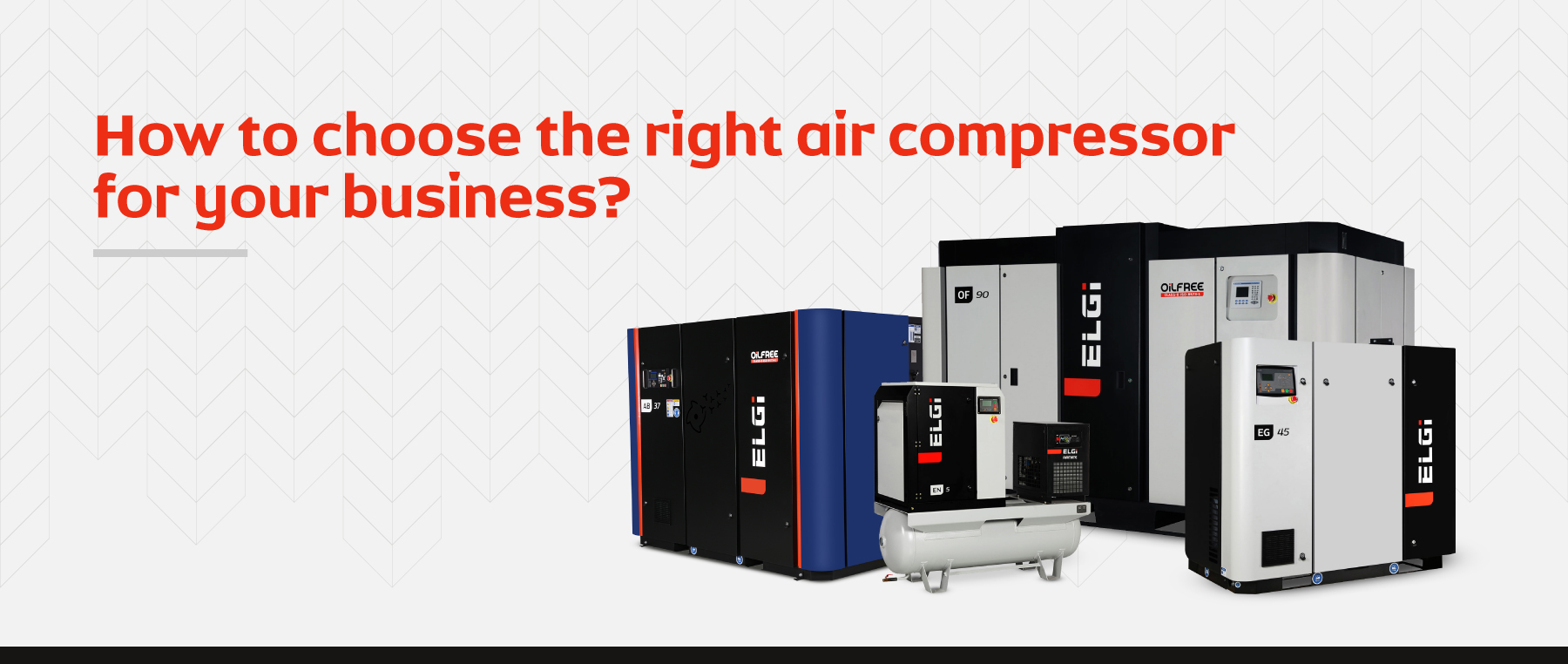
As automation expands across various industries, the demand for compressed air in the industrial sector is also rising. This reliance on compressed air is projected to escalate further in the future. Selecting a suitable compressor can be a daunting challenge with several technologies and available options. Here are some key factors to keep in mind before choosing the suitable compressor for your industrial requirements.
Key Factors to Consider When Choosing an Air Compressor
When choosing an air compressor, the key specifications that need to be considered include horsepower (HP), cubic feet per minute (CFM), pressure rating (PSI), and tank size. Horsepower determines the motor's power output, influencing the compressor's overall performance. CFM measures the volume of air the compressor can deliver, while PSI indicates the pressure at which the air is delivered. These specifications should match your tools' requirements and the desired airflow and pressure levels.
Tank size determines the storage capacity of compressed air, allowing the compressor to provide consistent airflow during peak demands. Calculating the required specifications based on your tools' airflow and pressure requirements will help you select an air compressor that can handle your business workload effectively.
Capacity Requirement
The capacity of an air compressor is determined by the amount of air it can deliver and the pressure it can achieve. This capacity is linked to the power rating of the compressor, measured in kilowatts (kW) or horsepower (HP).
To determine the required capacity for a plant, you can rely on the recommendations from the equipment manufacturer, previous equipment experience or conduct an air audit. Air audits provide valuable insights into a plant's compressed air usage.
ELGi offers customized air audits to create an energy management plan tailored to your needs. Reciprocating compressors work well for lower flow capacities (<
50 cfm), while screw compressors are better for higher flow capacities. Consider your plant's requirements when choosing the right compressor for your needs.
Duty Cycle & Utilization
The duty cycle of an air compressor is the duration it can operate at maximum capacity within an hour. Reciprocating compressors are typically designed to handle duty cycles ranging from 60% to 80%, while screw compressors are built to sustain a continuous 100% duty cycle.
Quality of Air
Industrial compressors use oil for cooling, lubricating, and sealing gaps between moving parts. Consequently, when air is compressed, it comes into contact with the oil, leading to a portion of it being carried over. In specific applications, the compressed air directly interacts with sensitive products like food and pharmaceuticals. In such cases, the preference is for oil-free air, ensuring no contamination. The quality of the compressed air, with regard to the presence of oil, is measured according to ISO 8573:2010 standards. Class 3 indicates that the oil carryover is less than 1 mg/m3, and even higher air quality can be achieved by implementing downstream filtration equipment. Hence, the choice of a suitable air compressor varies depending on your application's specific needs and requirements.
Assessing Power Sources and Energy Efficiency
Different sources, such as electricity, gas, or diesel, can power air compressors. Electric compressors are popular for their convenience, ease of use, and lower maintenance requirements. They are suitable for indoor use and businesses with access to reliable electrical power. Gas-powered compressors offer greater mobility and are suitable for outdoor or remote locations where electricity may not be available. Diesel compressors are commonly used in construction and mining sites due to their robustness and high portability. When choosing a power source, consider factors such as availability, cost, environmental impact, and the specific needs of your business.
Budget and Life-Cycle Costs
Investing in a reliable and efficient compressor upfront can save you money in the long run. Consider maintenance, repairs, energy consumption, and the compressor's lifecycle. When considering the cost of a compressor throughout its lifespan, it is essential to factor in the life cycle cost. This includes the initial purchase price, ongoing maintenance expenses, and energy consumption. Before finalizing the purchase decision, it is crucial to comprehensively understand the life cycle cost associated with the chosen compressor. Considering the initial cost, maintenance expenses, and energy consumption over the expected operational period, you can make a well-informed decision considering the total cost of owning and operating the compressor.
Maintenance and Support
Proper maintenance is crucial for the longevity and performance of your air compressor. Regular maintenance activities may include:
- Changing filters.
- Checking oil levels.
- Inspecting belts and hoses.
- Ensuring proper ventilation and airflow around the compressor.
Consult the manufacturer's guidelines and recommended maintenance schedules to keep your compressor in optimal condition. Additionally, consider the availability of technical support, spare parts, and service centers. Easy access to support and spare parts can minimize downtime and ensure prompt repairs if any issues arise. Selecting a suitable air compressor for your business is a critical decision that can significantly impact your operations and productivity. You can make a well-informed choice by understanding your business needs, evaluating different types of compressors, determining the required specifications, and considering factors like power sources, energy efficiency, and maintenance.
Our website offers a convenient product selector tool that can assist you in finding the perfect match for your specific requirements. By utilizing the product selector, you can easily identify and choose the most suitable products from our range. Visit the following link to access the product selector tool: https://www.elgi.com/product-selector/
RELATED BLOGS
When it comes to compressed air systems, rotary screw compressors have establishe...
Read MoreReciprocating air compressors are vital components in many industries, including m...
Read MoreOil-free air compressors are becoming increasingly popular due to their ability to ...
Read More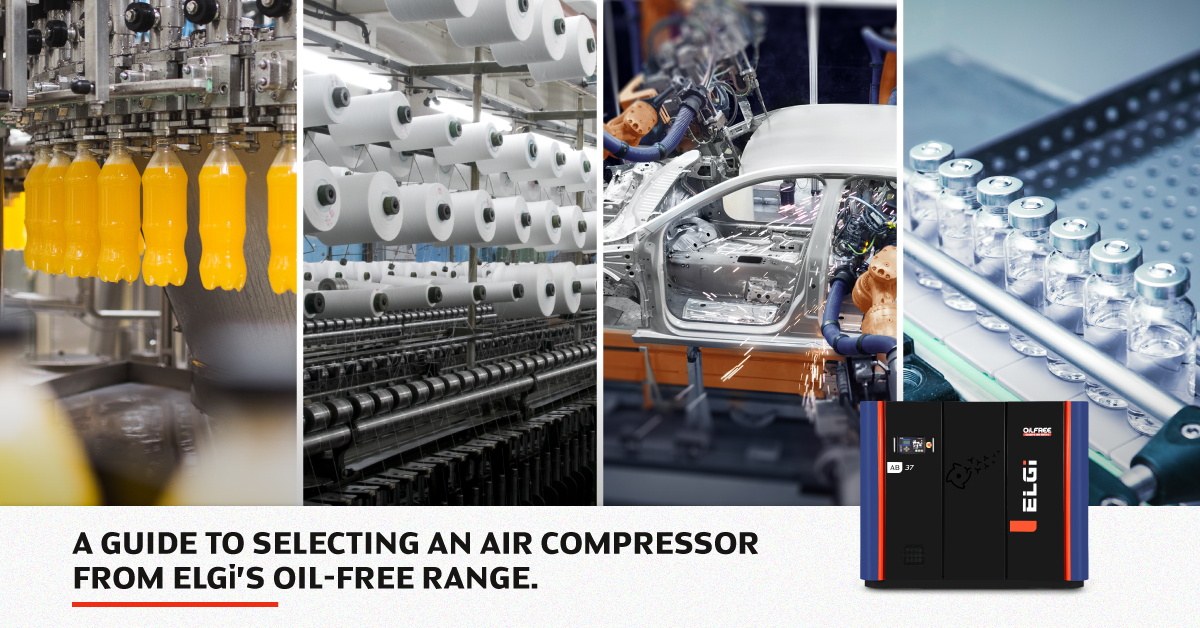
Oil-free air compressors are used in industries where clean air...
Read More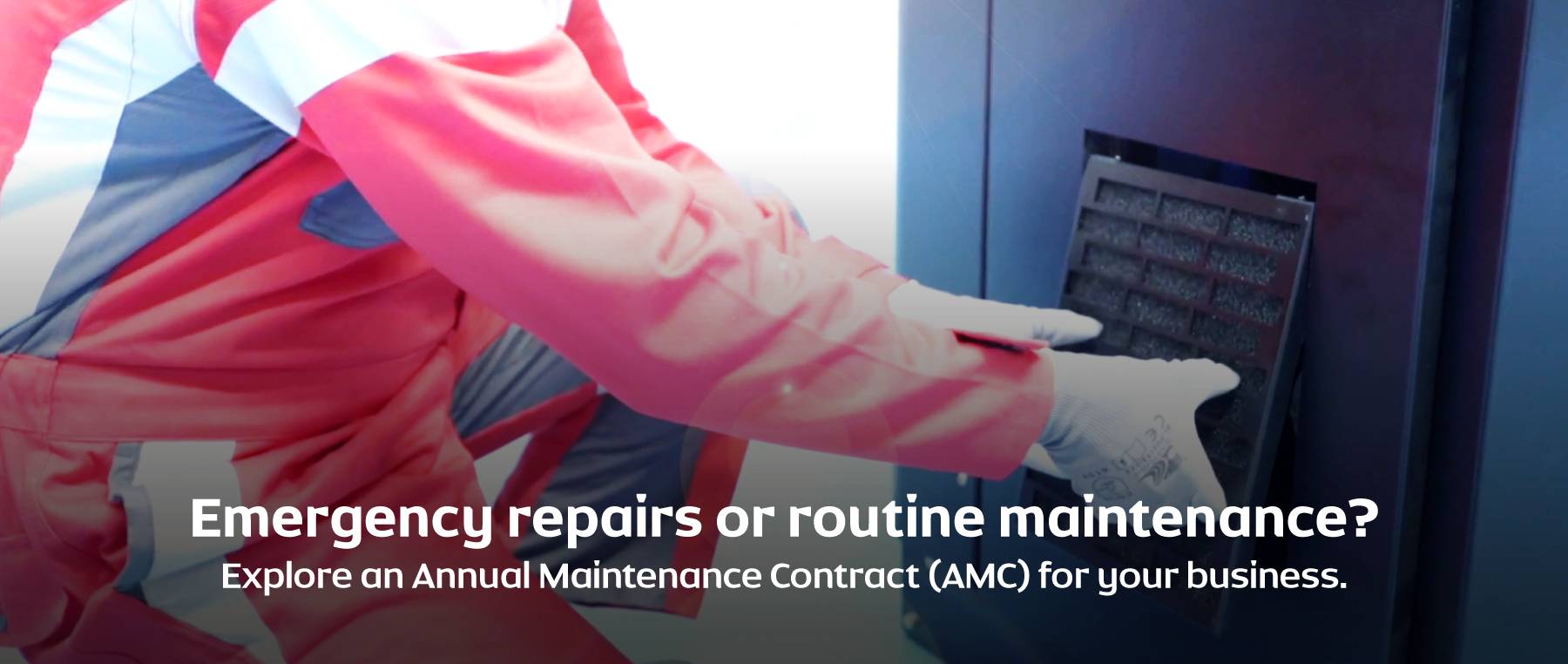
Air compressors require regular servicing and maintenance, a fa...
Read More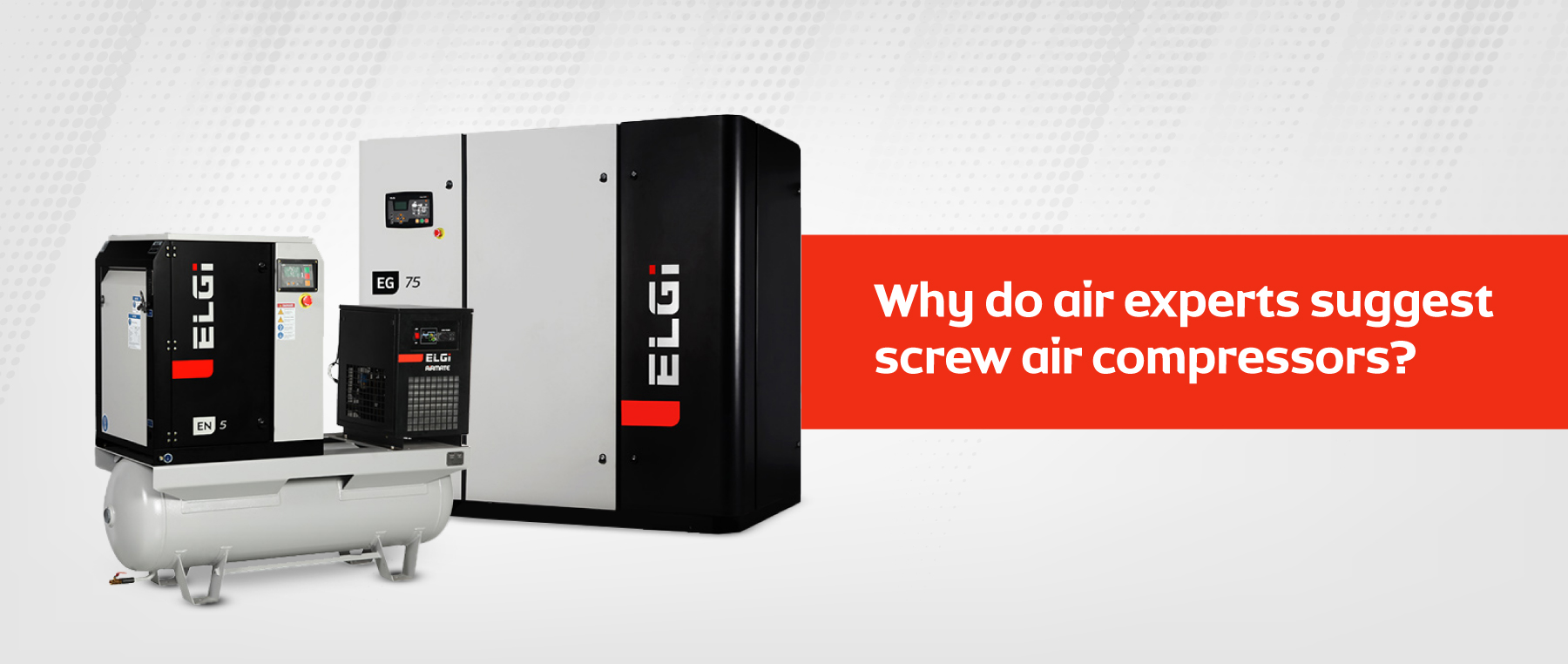
When seeking the optimal air compressor solution for your oper...
Read More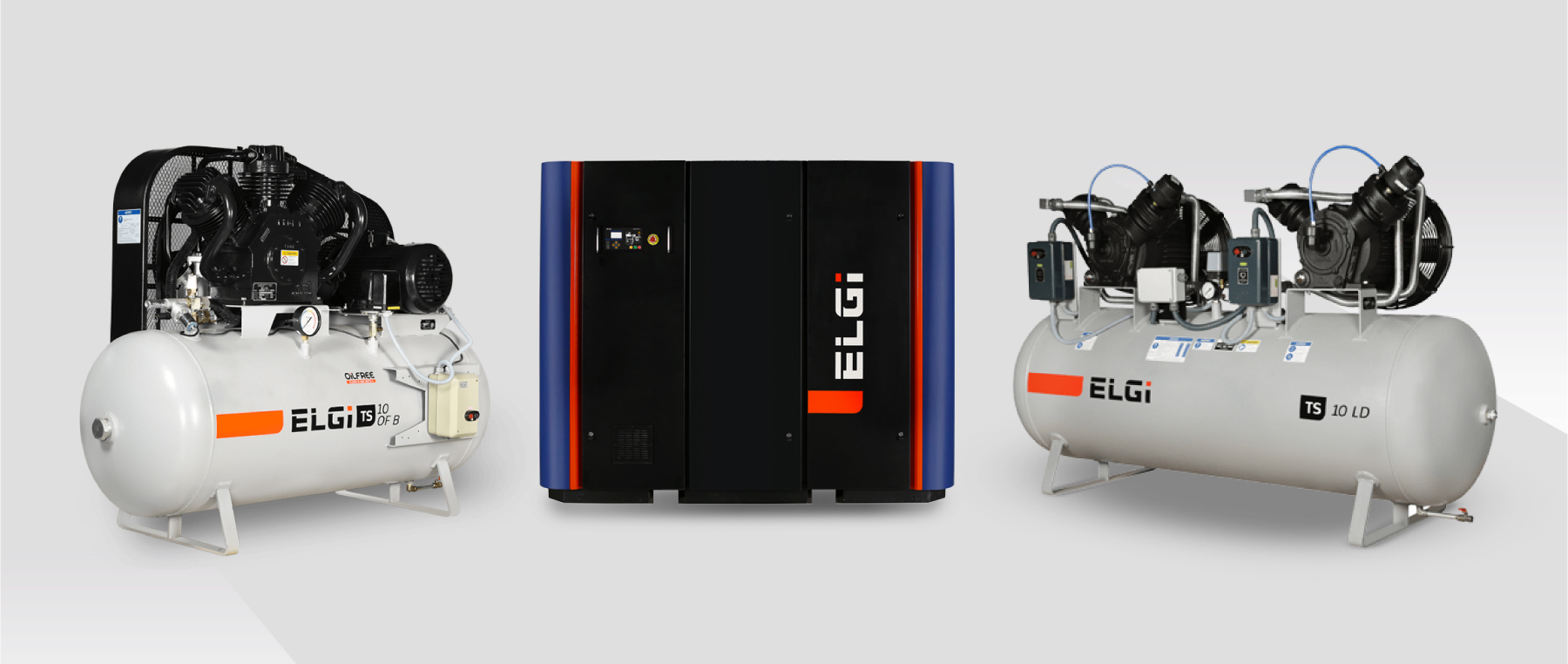
The two most commonly used types of air compressors are rotary ...
Read More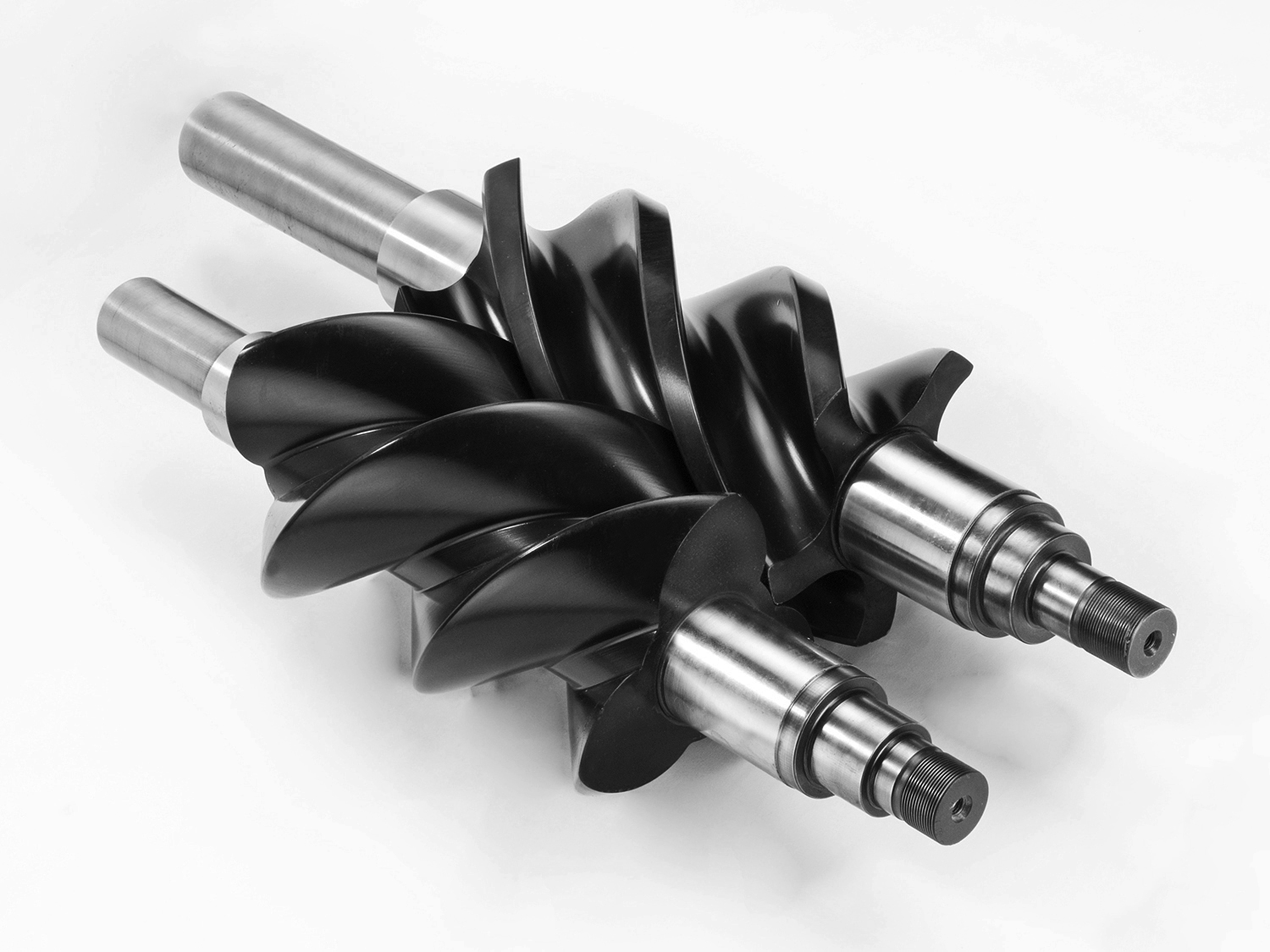
Oil-free compressors eliminate the need for lubricating oil in ...
Read More