Understanding servicing & maintenance of air compressors
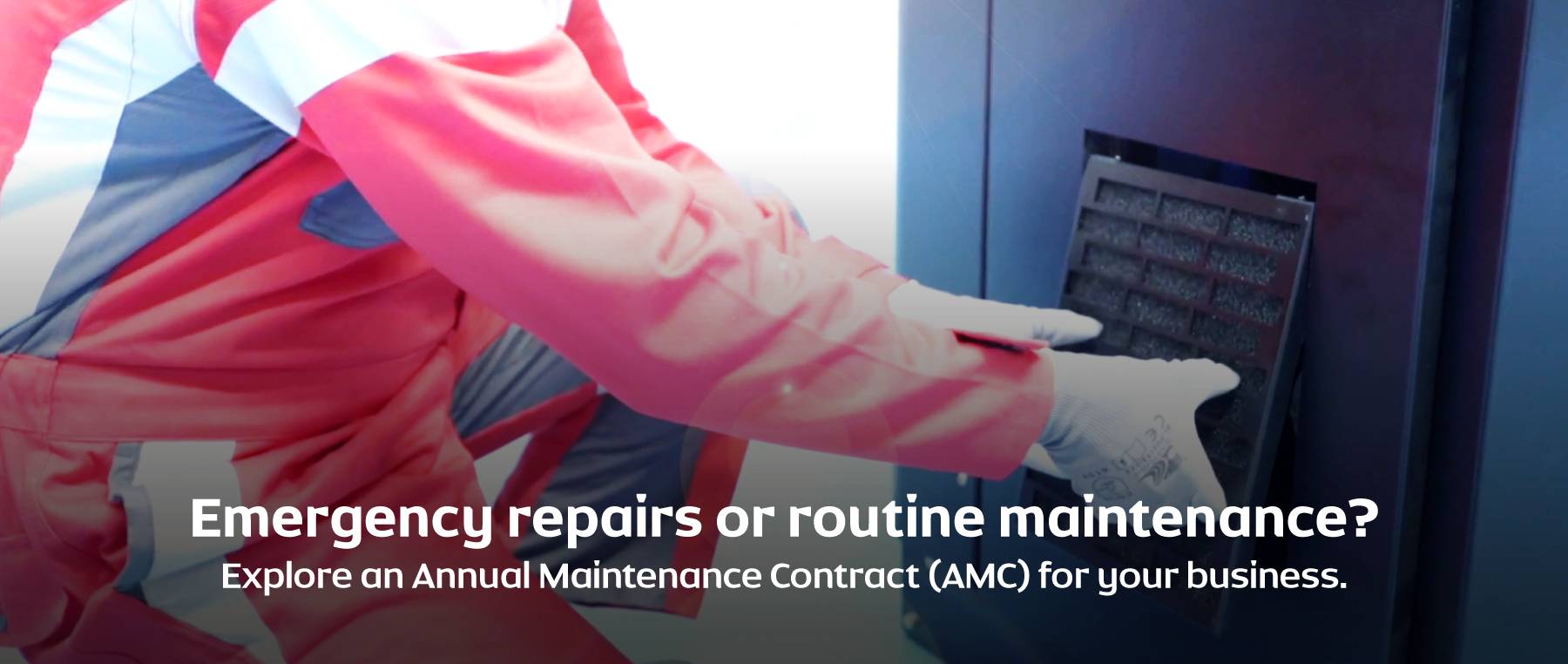
Air compressors require regular servicing and maintenance, a fact that many overlook. Taking preventive measures is more advantageous in the long run than dealing with problems later. By conducting essential inspections each time you use your air compressor, you can avoid potential troubles in the future, saving both time and money. The significance of properly maintaining your air compressor is often underestimated in today's fast-paced business world. However, dedicating time and effort to its upkeep yields advantages in both the immediate and distant future. These benefits include minimizing downtime, reducing energy costs, extending equipment life, and improving efficiency.
Why procure spares and consumables from certified suppliers?
When it comes to sourcing spare parts and consumables, it's crucial to rely on certified suppliers and Original Equipment Manufacturers (OEMs). Genuine parts offer benefits such as warranty coverage, high product quality, longer lifespan, increased productivity, energy savings, high reliability, and ease of service and maintenance.
In addition to genuine parts, having a comprehensive service kit with the necessary hand tools is crucial for safe part replacements. Skilled repair personnel should be relied upon when servicing your compressed air system for optimal results.
ELGi provides a range of reliable industrial-grade air compressors and genuine spare parts that enhance the efficiency of your air compressor system while reducing operational expenses. ELGi’s Annual Maintenance Contract (AMC) to ensure consistent access to compatible parts and professional service.
Common Parts That Require Maintenance
Air Filters and Oil Separators
The role of air and oil filters, along with oil separators in air compressors, is paramount as they deter potential harm and performance degradation caused by system-internal contaminants. Dust particles from the intake air can inflict substantial damage on your air compressor's rotors, reducing the amount of compressed air delivered to the connected tools. Moreover, dust can considerably reduce the operational lifespan of the air compressor component and the oil separator. When dust intermixes with the oil that lubricates the rotary screw air compressor, the lubrication quality deteriorates, making the oil less effective. Furthermore, dust can damage the bearings and their housing, which can negatively affect the air compressor component and potentially lead to its seizure.
Airline filter cartridge
Utilizing a non-authentic line filter cartridge to replace your air compressor can compromise the filter's effectiveness, permitting the influx of dirt particles into the air network. This leads to unwanted pressure drops and high energy consumption within the compressed air system. Moreover, counterfeit filter cartridges often trigger the need for more frequent replacements or repairs, escalating the total lifecycle expenditure associated with the air compressor. Thus, choosing only authentic airline filters for your compressor is essential.
Lubricating Oil
Proper oil selection is vital for extending the lifespan of the air compressor. Inferior quality oil can compromise an air compressor's longevity. If the oil does not lubricate system components adequately, it may lead to sediment accumulation in oil circuits and over-moving parts. Such occurrences elevate the risk of oil oxidation and the potential for corrosion of metal components within the compressed air system. Regularly check the oil level, refill carefully to avoid damage from insufficient or excessive lubrication, and change the oil based on the manufacturer's recommendations. Monitor oil consumption for any abnormalities, and use oil analysis to detect contaminants. Oil filters should be replaced at recommended intervals to ensure clean and efficient lubrication.
Troubleshooting
Air compressors may encounter common issues that affect their performance. Inadequate pressure can result from leaks, improper adjustments, or worn components. Abnormal noise may indicate problems with bearings, pistons, or valves. Damaged seals, fittings, or hoses can cause air leaks. When troubleshooting, it's crucial to identify the root cause before attempting repairs. Simple solutions like tightening connections or replacing worn-out parts can often resolve these issues. However, seeking professional assistance is advisable for complex problems or uncertain diagnoses.
Extending the Lifespan of Your Air Compressor
To extend the lifespan of your air compressor, avoid overloading it, allow cool-down periods, and provide proper ventilation. Follow manufacturer-recommended maintenance schedules, including regular oil changes and inspection of key components. Proper storage, such as protecting the compressor from extreme temperatures and moisture, also contributes to its longevity. Regularly monitor and address any signs of wear, leaks, or abnormal operation to prevent further damage and costly repairs.
To learn more about ELGi's compressed air solutions and maintenance plans, visit https://www.elgi.com/in/services-parts/.
RELATED BLOGS
When it comes to compressed air systems, rotary screw compressors have establishe...
Read MoreReciprocating air compressors are vital components in many industries, including m...
Read MoreOil-free air compressors are becoming increasingly popular due to their ability to ...
Read More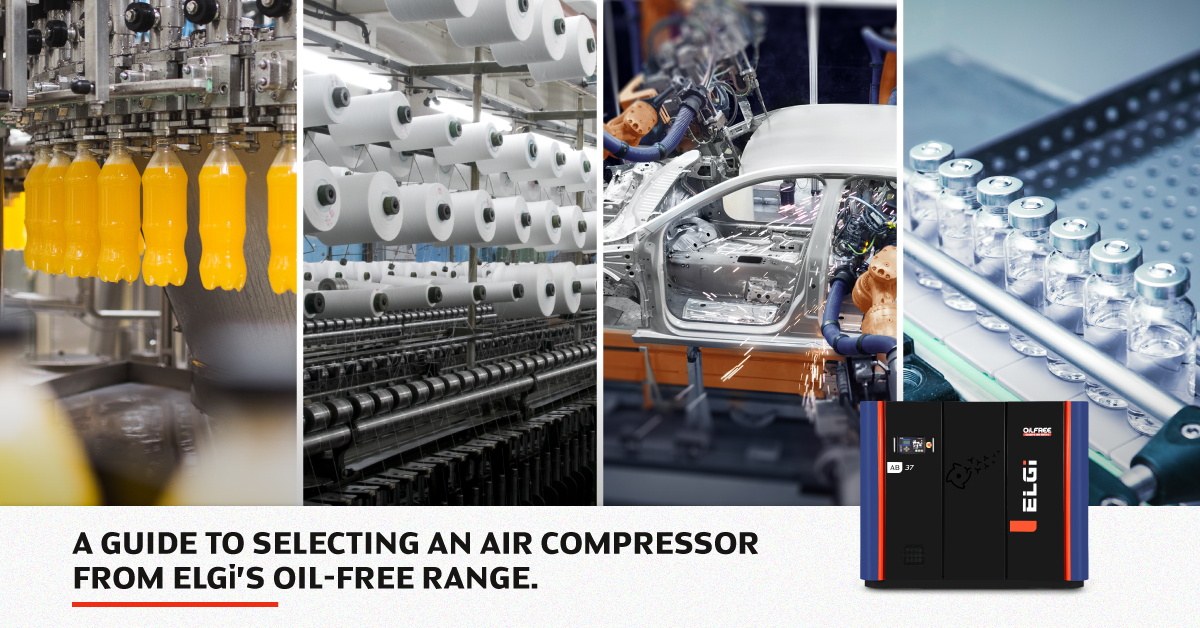
Oil-free air compressors are used in industries where clean air...
Read More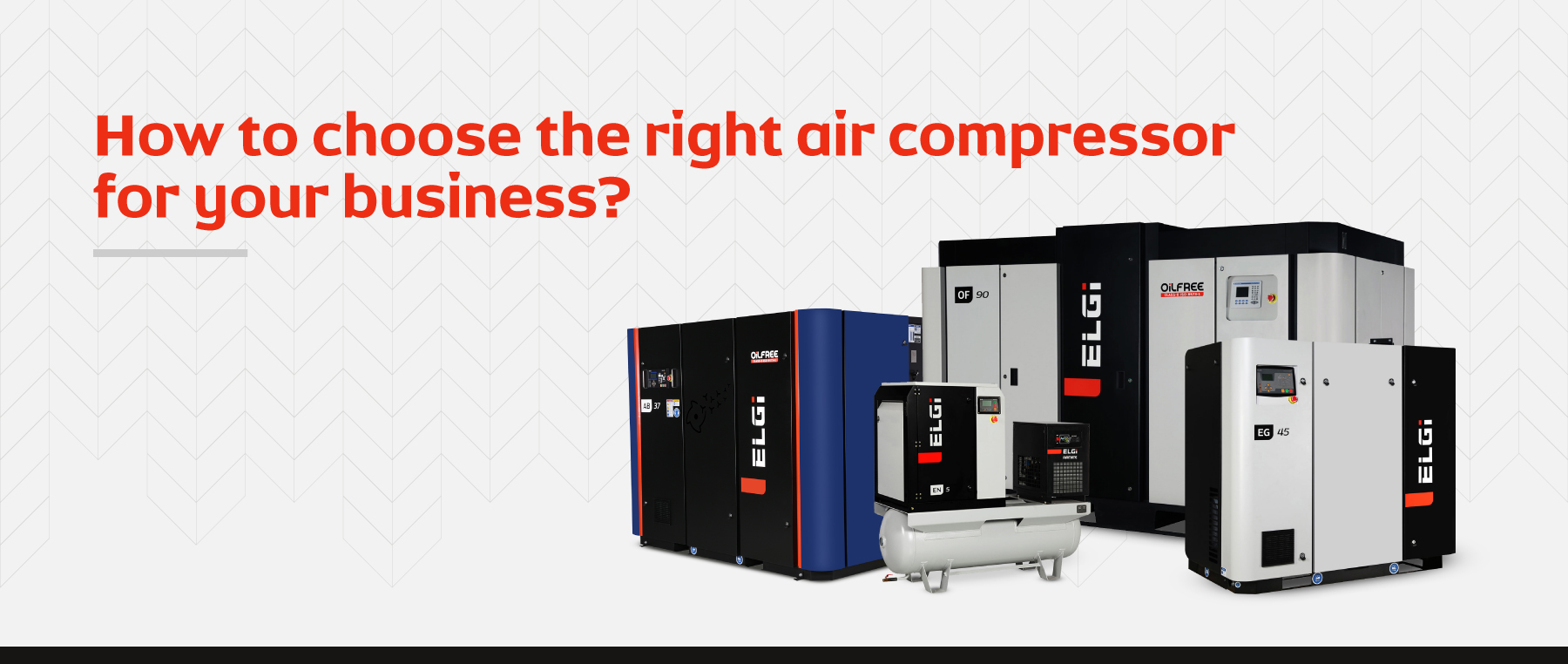
As automation expands across various industries, the demand for...
Read More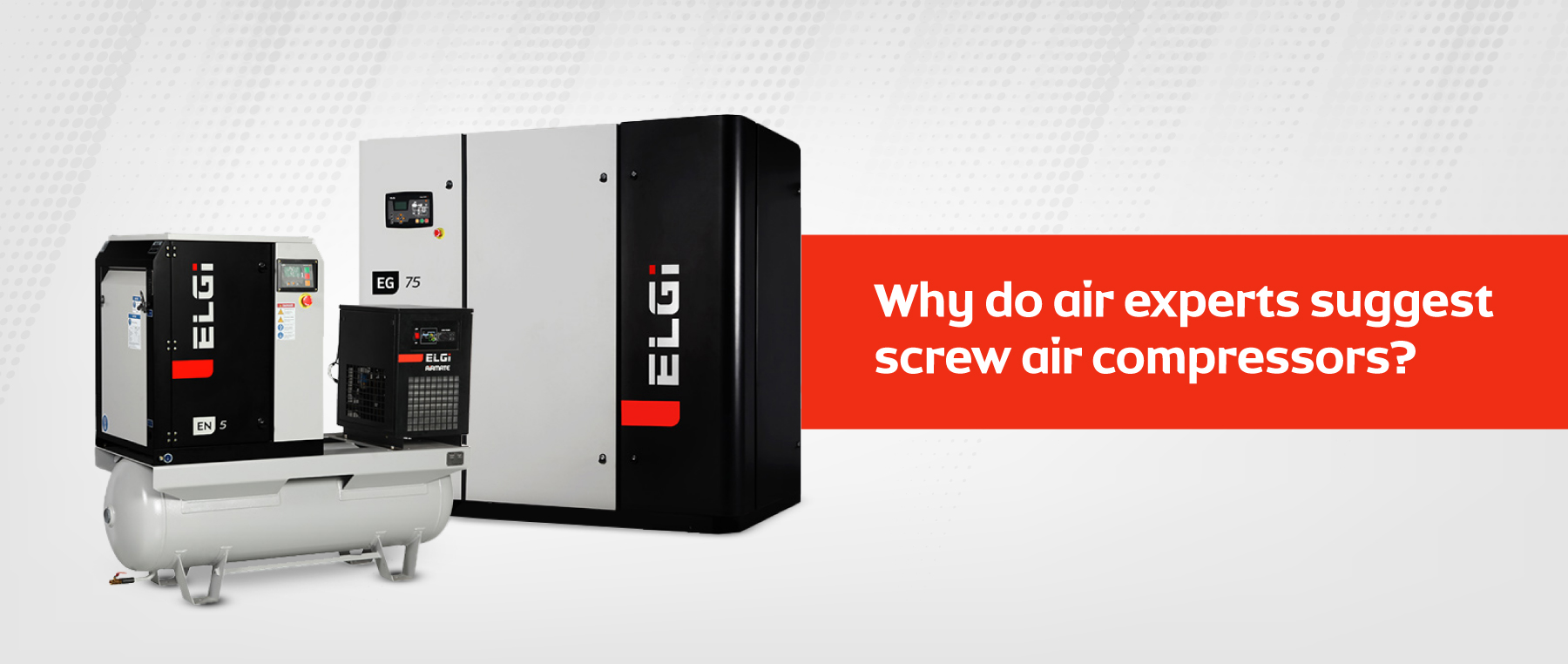
When seeking the optimal air compressor solution for your oper...
Read More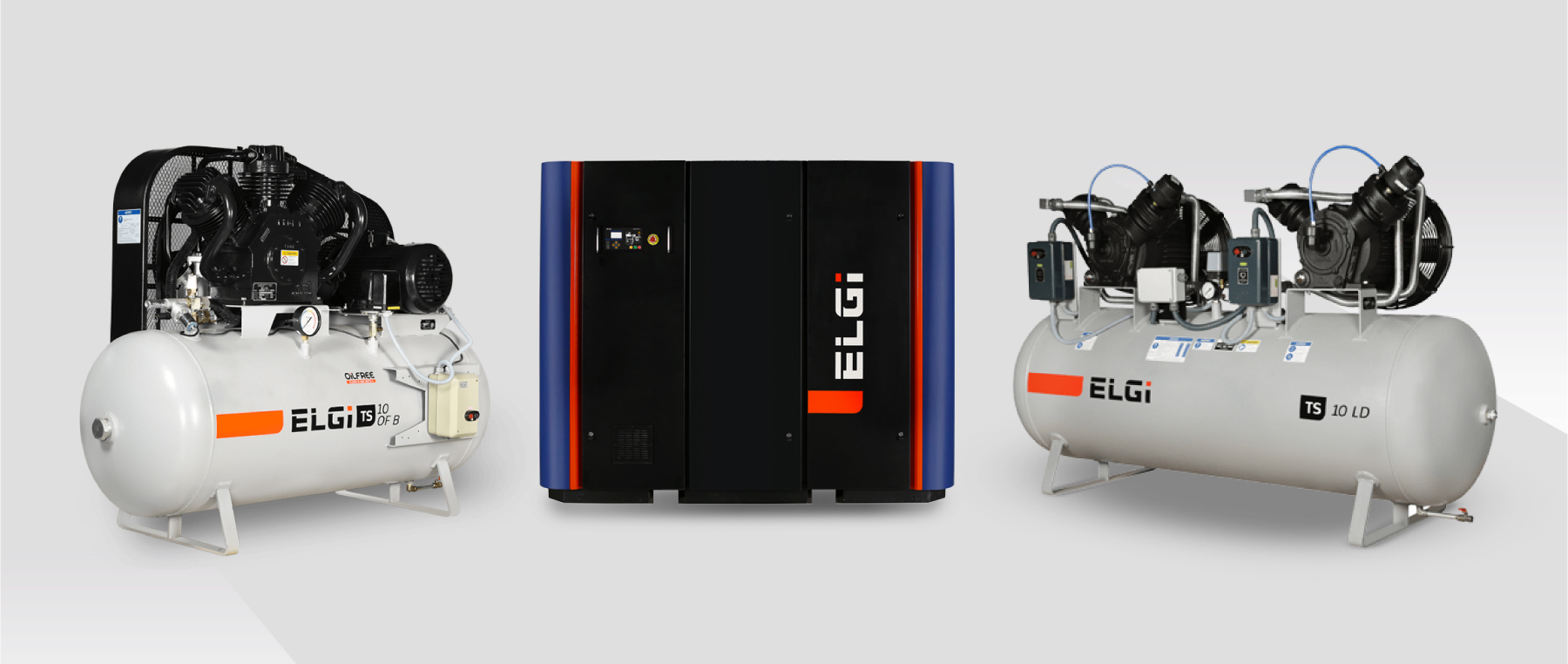
The two most commonly used types of air compressors are rotary ...
Read More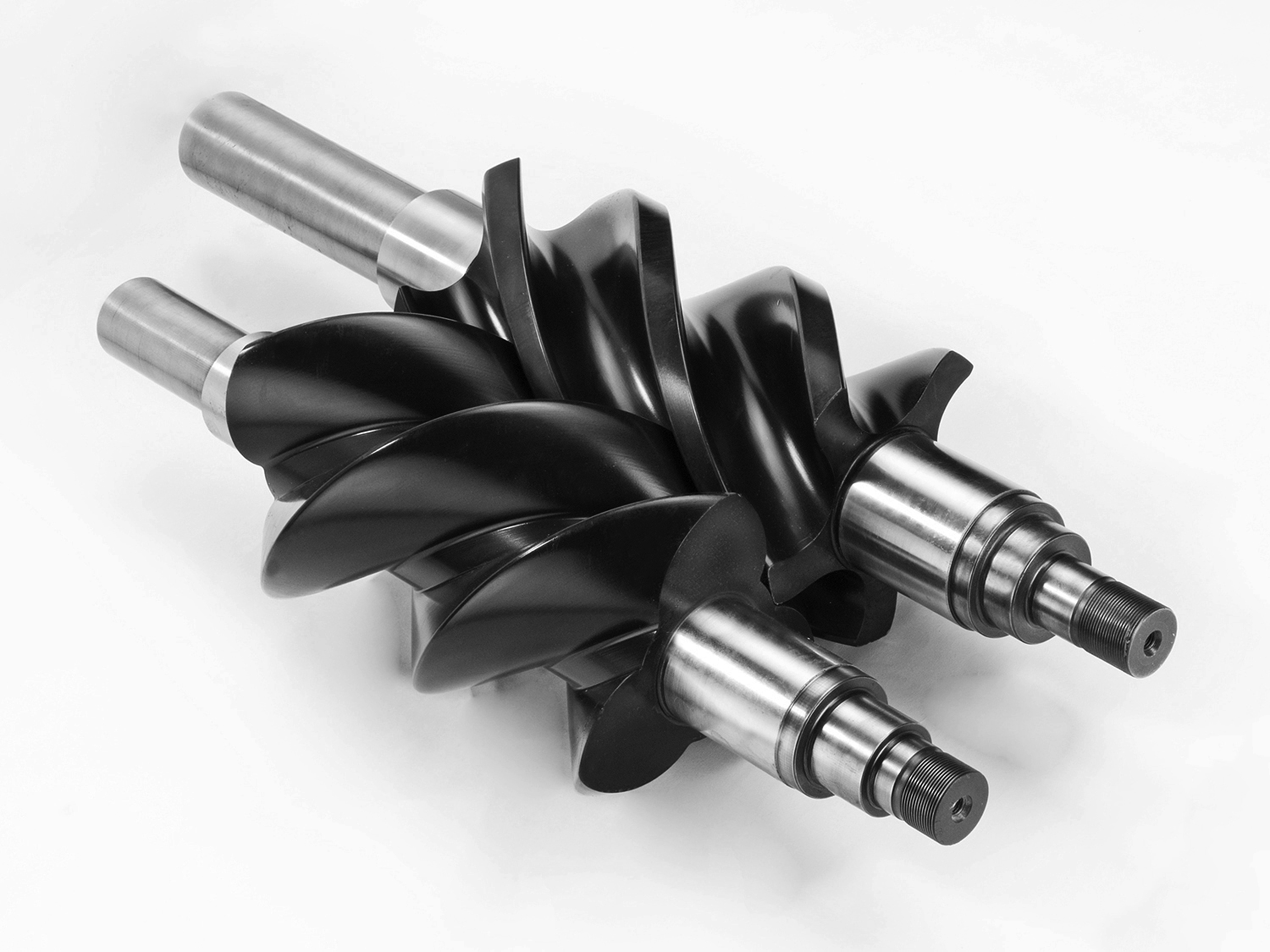
Oil-free compressors eliminate the need for lubricating oil in ...
Read More