Understanding the Differences Between Rotary Screw and Reciprocating Air Compressors
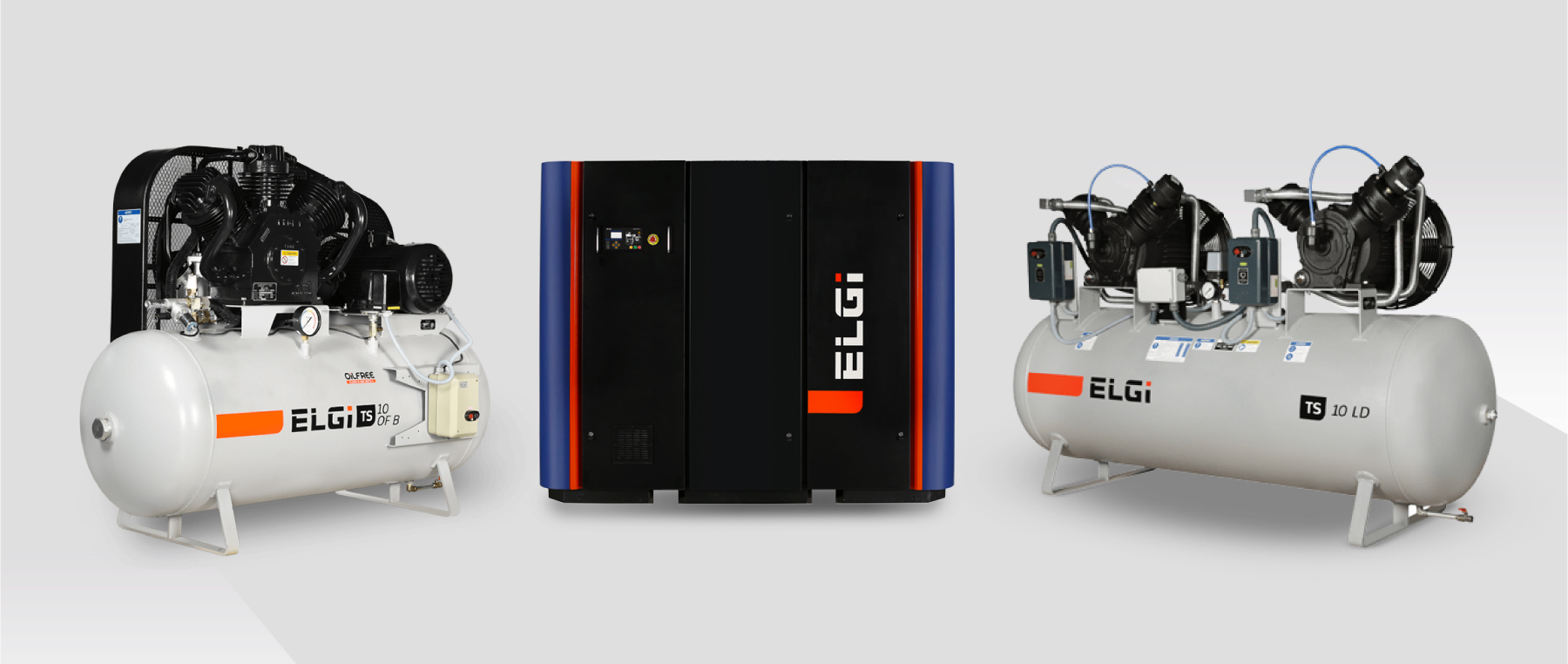
The two most commonly used types of air compressors are rotary screw compressors and reciprocating compressors. Understanding the differences between these two types is essential for selecting the right compressor for specific applications.
Overview of Air Compressors
Air compressors are categorized into different types based on their design, operation, and applications. Two prominent types are rotary screw compressors and reciprocating compressors.
Reciprocating Air Compressors
Reciprocating air compressors (or piston compressors), are one of the oldest and most common types of air compressors. They operate using a piston-cylinder mechanism, similar to the engine of an internal combustion vehicle.
Rotary Screw Air Compressors
Rotary screw air compressors are extensively used in commercial and industrial settings, offering higher air output and improved efficiency compared to reciprocating compressors. They operate on a positive displacement principle using two interlocking helical screws or rotors.
Key Differences Between Rotary Screw and Reciprocating Air Compressors
When considering the differences between rotary screw and reciprocating air compressors, several factors come into play, including design, operation, maintenance requirements, performance characteristics, and suitability for specific applications.
Design and Operation:
Reciprocating compressors have a piston-cylinder mechanism, with linear motion of the piston, while rotary screw compressors uses interlocking helical screws with rotary motion. Reciprocating compressors have a higher number of moving parts, including valves, piston rings, and connecting rods, whereas rotary screw compressors have fewer moving parts, resulting in reduced wear and tear.
Temperature:
While operating screw air compressors, the generated internal heat ranges from 80 to 99 degrees Celsius. This heat production is effectively controlled because there is no friction occurring between the screws. By using an oil or lubricant to form a non-wearing seal between the rotors and casing, the heat can be dissipated using a fluid circuit that is thermostatically managed.
In contrast, the piston temperature in reciprocating air compressors ranges from 150 to 200 degrees Celsius. These elevated temperatures are primarily because of the friction arising from the movement of piston rings against the cylinder walls.
Oil filtration:
The likelihood of finding any remaining traces of oil within an oil-lubricated screw air compressor is very low due to its highly efficient three-stage oil filtration mechanism. Typically, the concentration of oil particles in this unit remains below the threshold of three particles per million (PPM). In contrast, a reciprocating air compressor lacks an oil filtration system, resulting in more significant air contamination compared to a screw air compressor. Moreover, when the piston rings and oil rings degrade, permitting oil to ascend to the compression side, the oil content in the air increases.
Air-receiver tanks:
Selecting the right size for an air-receiver tank can be a complex task when using a rotary screw air compressor, given that most applications do not necessitate a tank. This particular apparatus is designed to provide a constant flow of compressed air without any interruptions or fluctuations. If the airflow requirement of your tool is lower than what the air compressor generates, a tank becomes unnecessary. Conversely, piston-based compressors incorporate air-receiver tanks to store air and eliminate pulsations before supplying it to connected applications. Once the tank reaches full capacity, the equipment can be operated.
Maintenance:
Reciprocating compressors require regular maintenance due to their complex design and higher number of components. This includes lubrication of moving parts, inspection and replacement of valves, and monitoring of piston rings. Rotary screw compressors also require maintenance, such as regular oil changes, filter replacements, and monitoring of the air-end temperature.
Performance:
Rotary screw compressors typically provide higher air output and can deliver a constant supply of compressed air. They are more efficient, consuming less energy compared to reciprocating compressors. Regarding pressure range, reciprocating compressors can achieve higher pressures, making them suitable for applications requiring greater pressure levels. Reciprocating compressors also have a quicker response time when the demand for compressed air changes, as they can start and stop more rapidly compared to rotary screw compressors.
Suitability for Applications:
Reciprocating compressors are suitable for small-scale applications that involve intermittent use of compressed air, such as automotive repair shops, small manufacturing operations, etc.
Rotary screw compressors are more suitable for continuous and heavy-duty applications that require a constant and high-demand air flow, such as large-scale manufacturing, construction sites, and industrial processes.
Applications and Industries
Reciprocating compressors find applications in industries where intermittent use of compressed air is common. They are often used in automotive repair shops for tire inflation, air-powered tools, painting applications and powering pneumatic machinery and equipments. Rotary screw compressors are extensively used in commercial and industrial setups due to their continuous operation capability and higher air output. They are commonly found in manufacturing industries, powering assembly lines, pneumatic machines, and automated processes. They are also used in the automotive industry for powering air tools, painting, and vehicle assembly lines. Construction sites often rely on them for tasks such as operating jackhammers, pneumatic drills, and powering heavy-duty machinery. Additionally, rotary screw compressors are utilized in pharmaceutical and food processing plants, where clean and oil-free compressed air is essential.
ELGi’s Reliable Reciprocating and Rotary Air Compressors.
ELGi offers a comprehensive range of air compressors, including rotary screw and piston-based reciprocating models. While reciprocating air compressors are suitable for low-capacity needs, your facility may require more energy-efficient units as the demand for associated applications grows. Our rotary screw air compressors are known for their compact size, quiet operation, and reliability, ensuring a consistent airflow. They are ideal for a wide range of applications across various industries, providing a stable air supply. To arrange a free consultation for selecting the right air compressor, kindly contact us at https://www.elgi.com/ae/contact-us/.
RELATED BLOGS
When it comes to compressed air systems, rotary screw compressors have establishe...
Read MoreReciprocating air compressors are vital components in many industries, including m...
Read MoreOil-free air compressors are becoming increasingly popular due to their ability to ...
Read More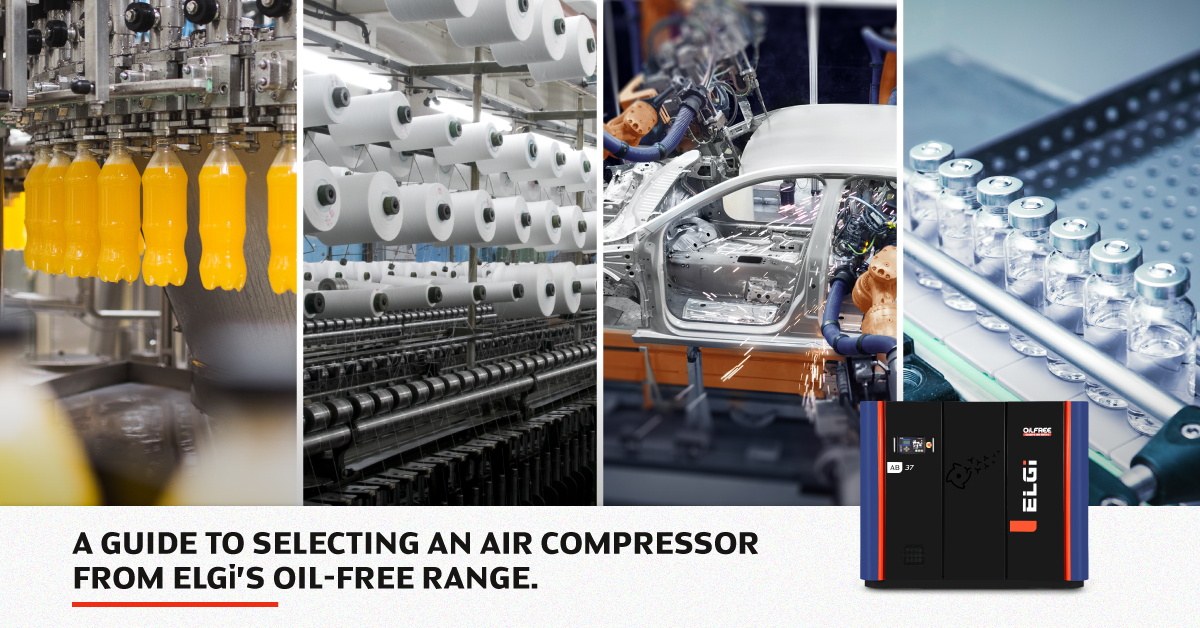
Oil-free air compressors are used in industries where clean air...
Read More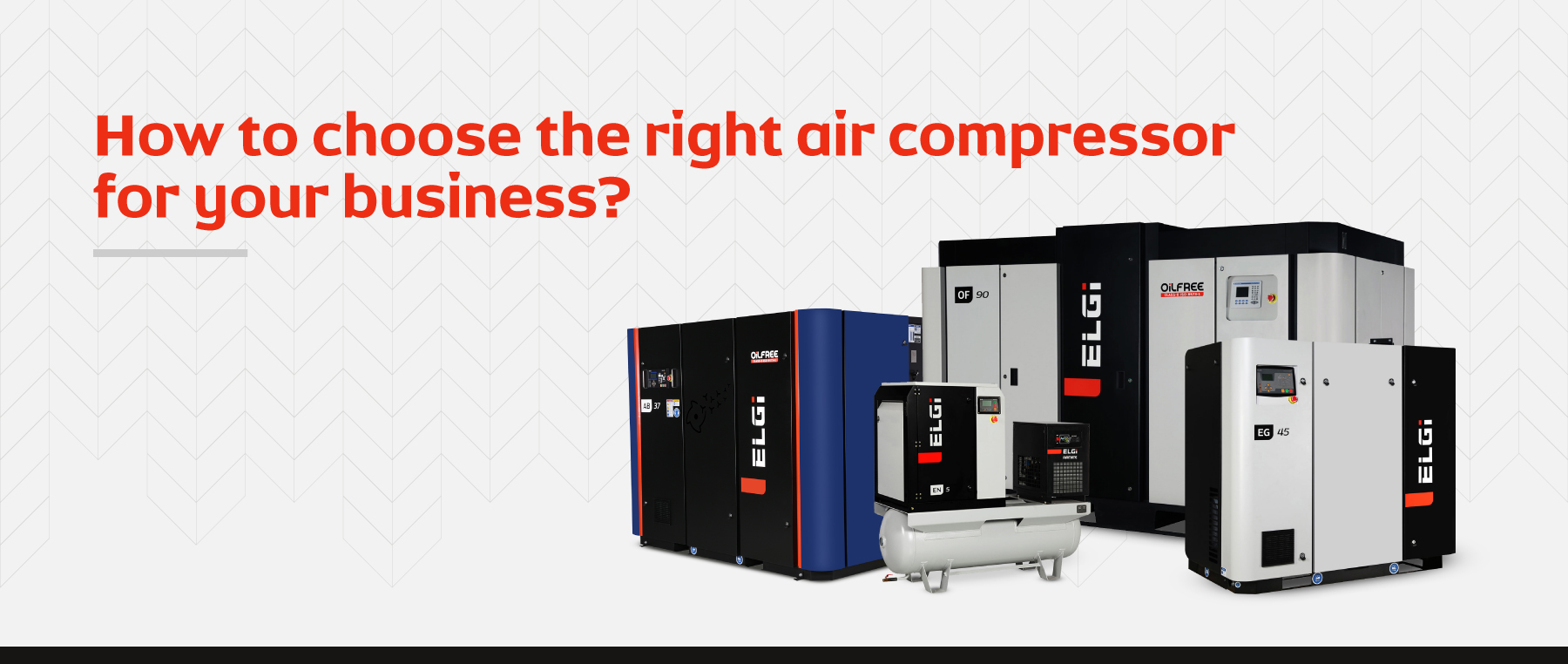
As automation expands across various industries, the demand for...
Read More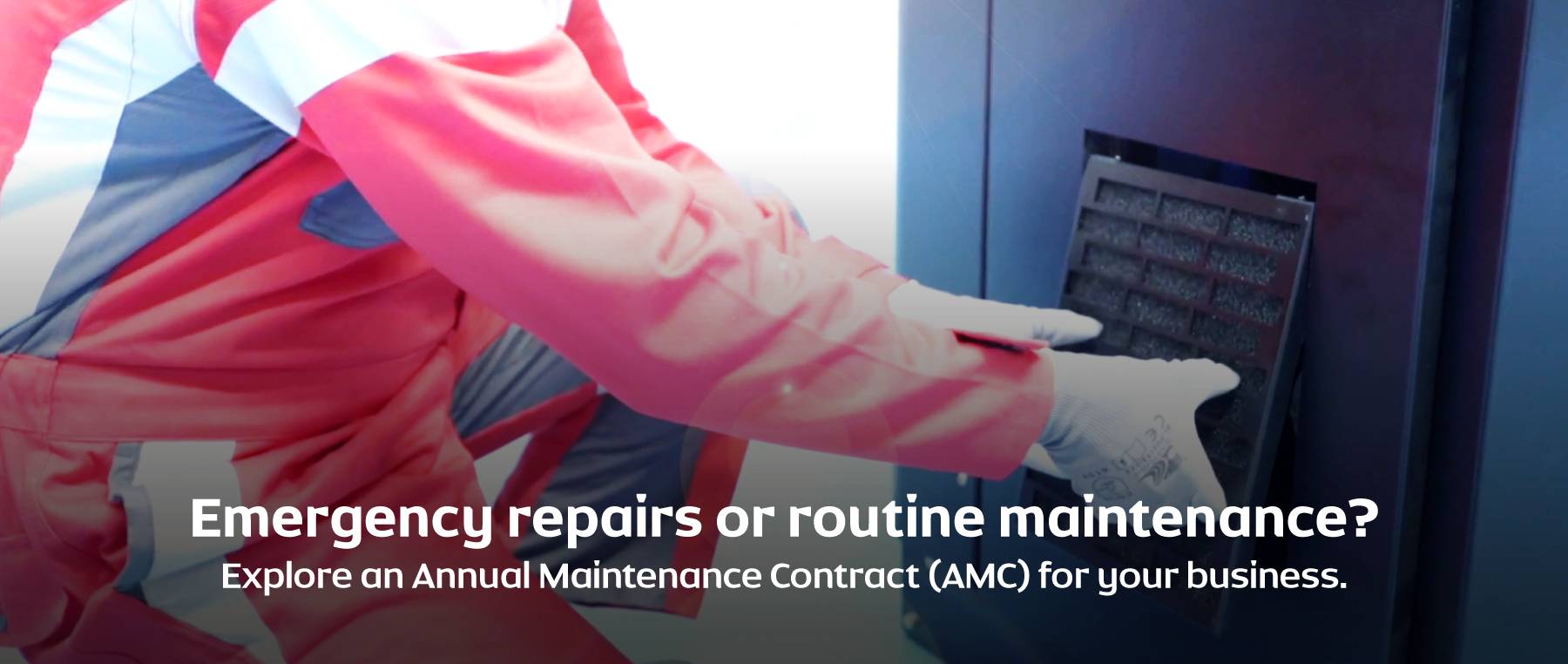
Air compressors require regular servicing and maintenance, a fa...
Read More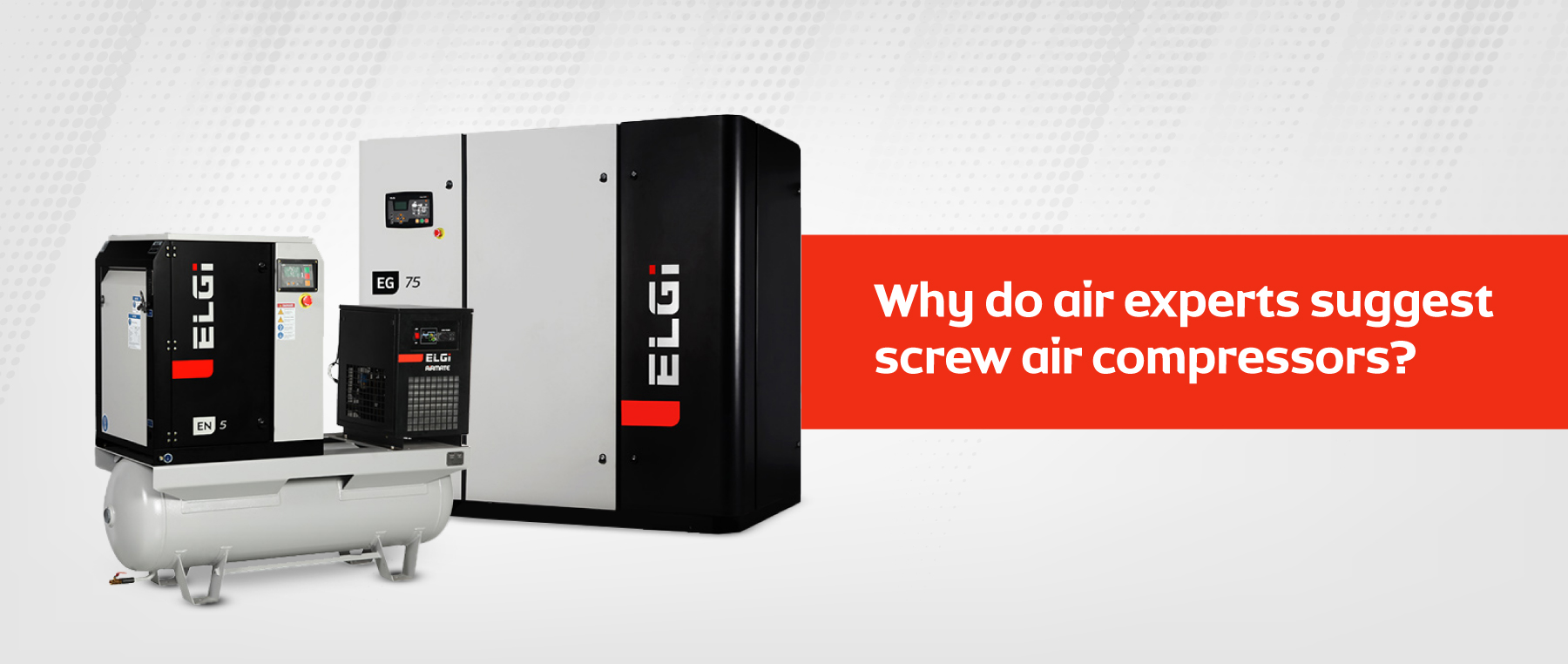
When seeking the optimal air compressor solution for your oper...
Read More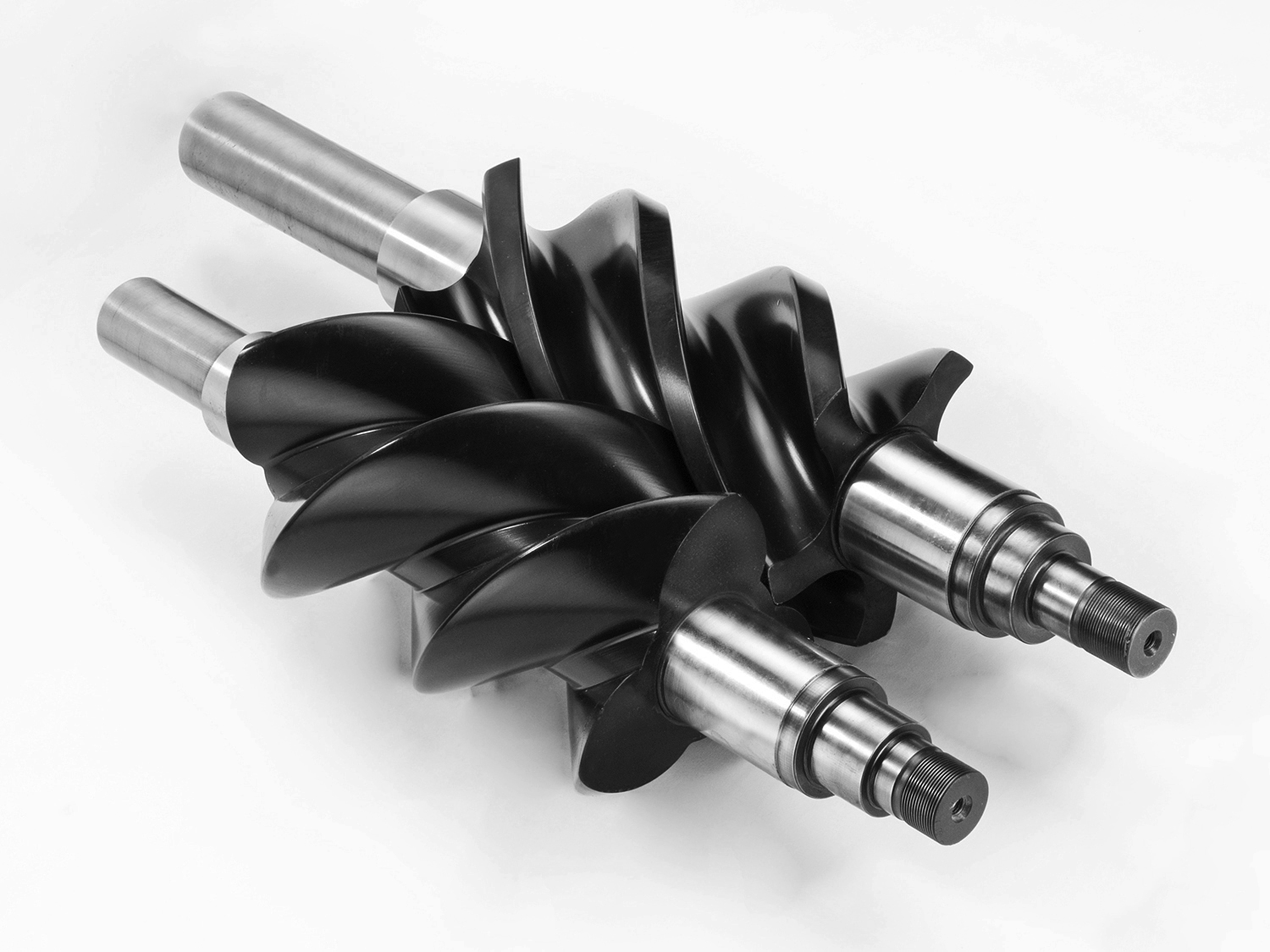
Oil-free compressors eliminate the need for lubricating oil in ...
Read More